

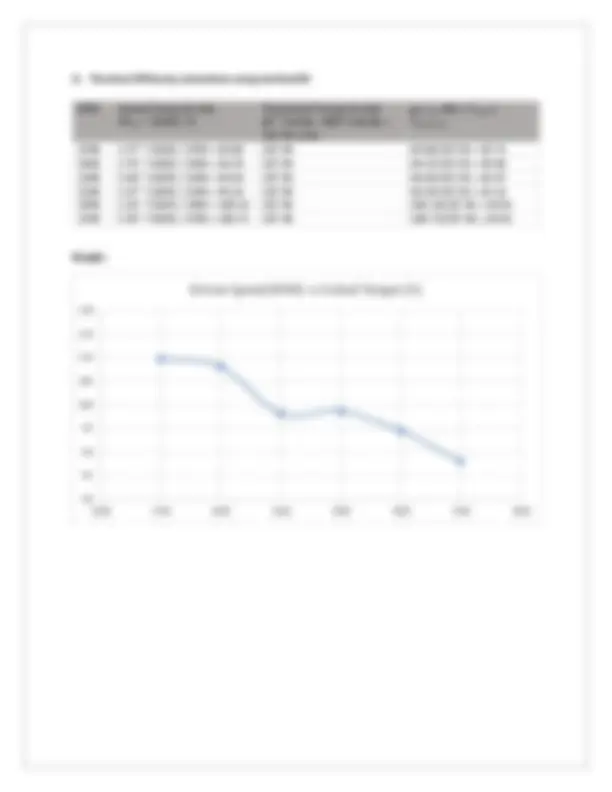
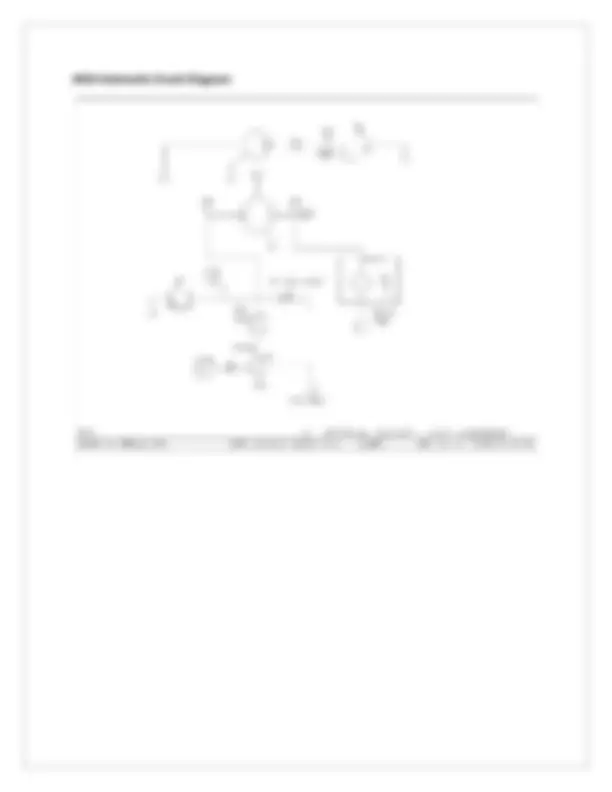
Study with the several resources on Docsity
Earn points by helping other students or get them with a premium plan
Prepare for your exams
Study with the several resources on Docsity
Earn points to download
Earn points by helping other students or get them with a premium plan
Community
Ask the community for help and clear up your study doubts
Discover the best universities in your country according to Docsity users
Free resources
Download our free guides on studying techniques, anxiety management strategies, and thesis advice from Docsity tutors
To learn more about the torsional, global, and volumetric effectiveness of the Piston Motor Torque Test.
Typology: Lab Reports
1 / 7
This page cannot be seen from the preview
Don't miss anything!
Lab report must be handed in at the beginning of your next lab class. Any late submission will be deducted 10% each business day.
(Last name) (First Name)
th
This practical assist with the following tasks: setting up the hydraulic circuit and the motor torque test apparatus; calculating the actual torque for each speed setting; creating a line graph to depict the relationship between the actual output torque and the drive speed; comprehending "part separation" as it relates to both volumetric and torsional efficiency; and, if necessary, troubleshooting the test's operational sequence.
To learn more about the torsional, global, and volumetric effectiveness of the Piston Motor Torque Test.
Hydraulic power unit Piston motor Hydraulic hoses Pressure, return and drain hoses Test Stand Flange coupling Flow meter Pressure gauges Pressure Relief Valve Tachometer Pump
b) Torsional Efficiency calculation using method #2: RPM Actual Torque (in-lbs) HPout * 63025 / N Theoretical Torque (in-lbs) ΔP * Vd/2π = 800*1.24/2π = 157.96 in-lbs ηtorsional (%) = Tactual / Ttheoretical 2700 3.77 * 63025 / 2700 = 88.00 157.96 88.00/157.96 = 55. 2500 3.7 5 * 63025 / 2 5 00 = 94.25 157.96 94.53/157.96 = 58. 2300 3. 60 * 63025 / 2 3 00 = 98.64 157.96 98.64/157.96 = 62. 2100 3. 2 7 * 63025 / 2 1 00 = 98.14 157.96 98.14/157.96 = 62. 1900 3. 26 * 63025 / 19 00 = 108. 14 157.96 108.14/157.96 = 68. 1700 2.96 * 63025 / 1 700 = 109.73 157.96 109.73/157.96 = 69.
80 85 90 95 100 105 110 115 120 1500 1700 1900 2100 2300 2500 2700 2900 Driven Speed (RPM) vs Actual Torque (%)
a) Create a table to include all incremental setting for motor speed. Include the following column headings: Motor Speed, Overall Efficiency, Volumetric Efficiency, Torsional Efficiency. Nmeasured (RPM) For Δ800 PSI ηoverall ηvolumetic ηtorsional 2700 53.34% 95.73% 55.81% 2500 57.25% 95.58% 59.89% 2300 59.50% 95.19% 62.50% 2100 59.45% 95. 53 % 62.23% 1900 65.20% 95.05% 68.59% 1700 66.66% 95.85% 69.54% b) What are the two major factors that affect the torque of a hydraulic motor? Pressure drop (ΔP) & Volumetric Displacement (in^3 /rev) c) Tradespeople and engineers in the fluid power industry describe what happens to the internal clearances of the piston motor’s components as pressure increase using the term “part-separation”. Describe why this condition increases torsional efficiency. By pulling internal components apart, part separation increases torsional efficiency and increases system pressure. As a result, internal leakage increases. However, actual torque increases along with volumetric displacement, enhancing torsional efficiency.
In general, this lab gave us the opportunity to learn how to carry out and assess a torque test on a piston motor. We had a better grasp of the many components and functions of the hydraulic unit because of the lab. Other topics covered in this lab included taking readings of flow, pressure, and speed, identifying the components of the power unit, and computing several variables pertinent to the unit, including output/input horsepower, actual/theoretical torque, and volumetric efficiency. It also became evident that the variables that affect the torque value for a hydraulic motor are the pressure drop and motor speed.