
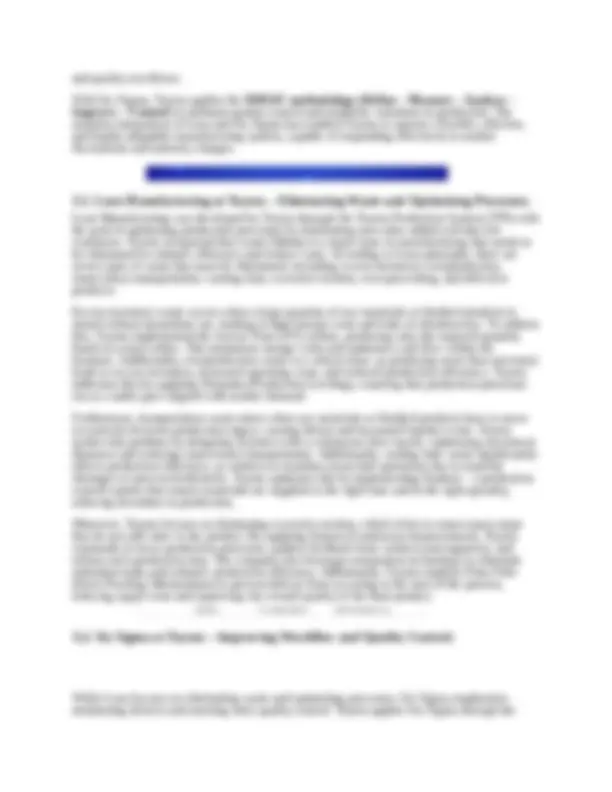
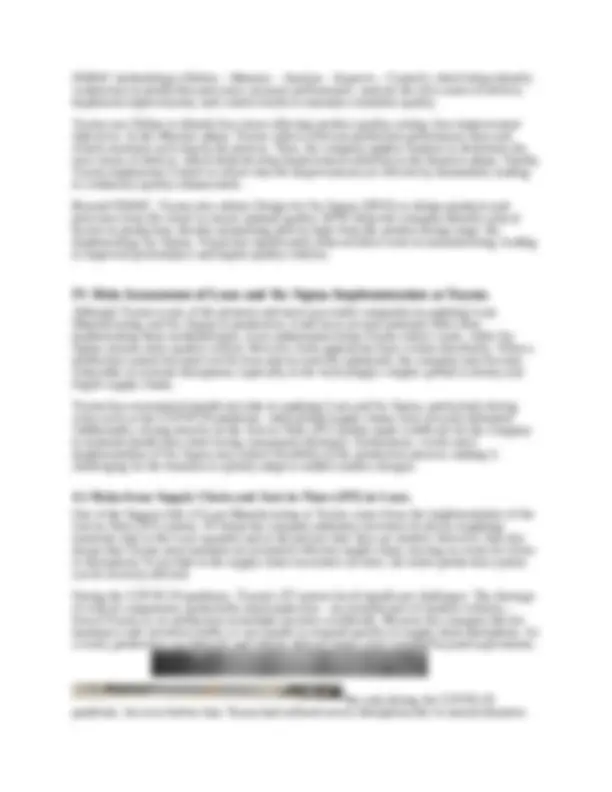
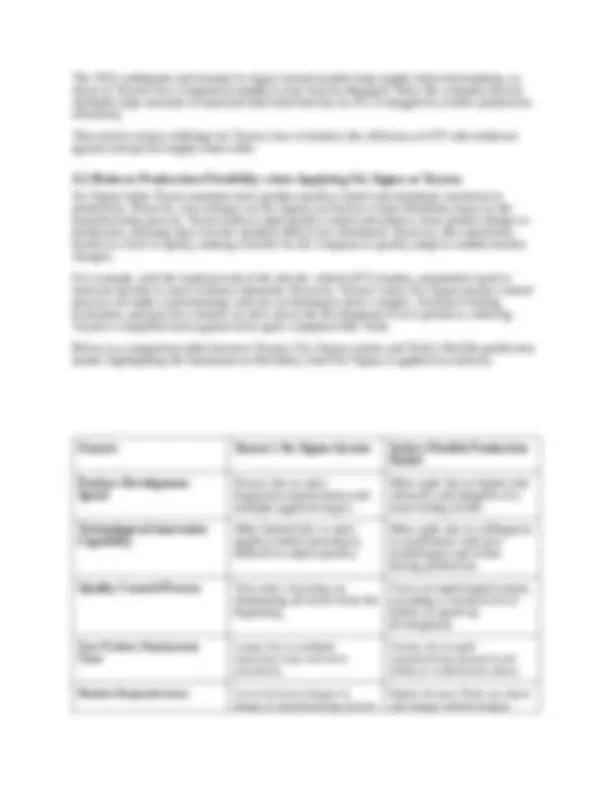
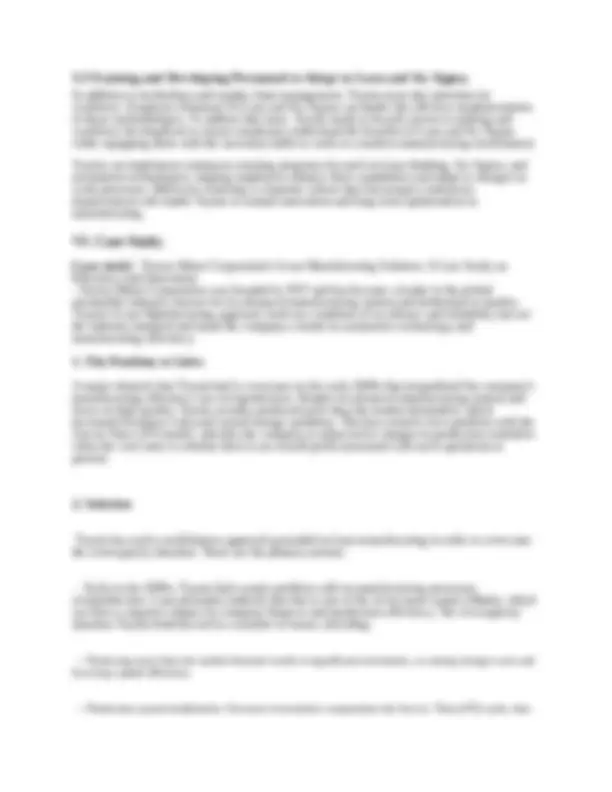
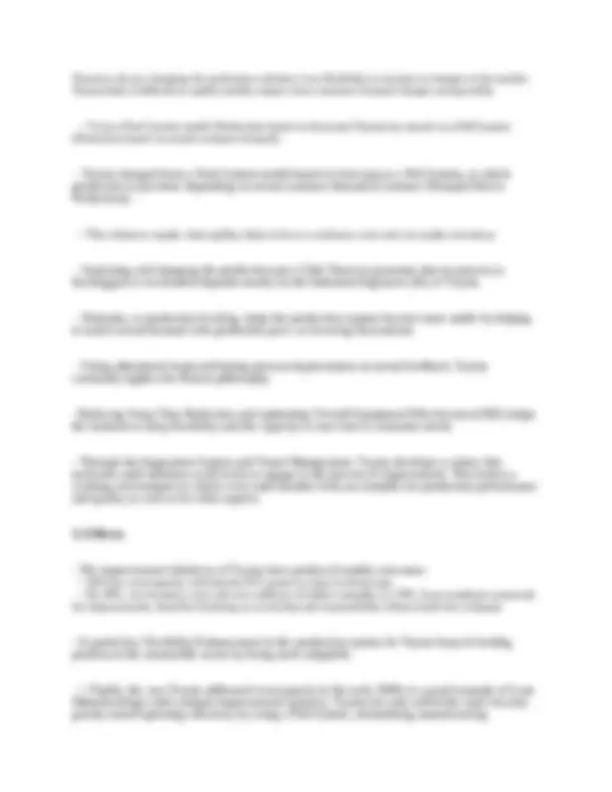
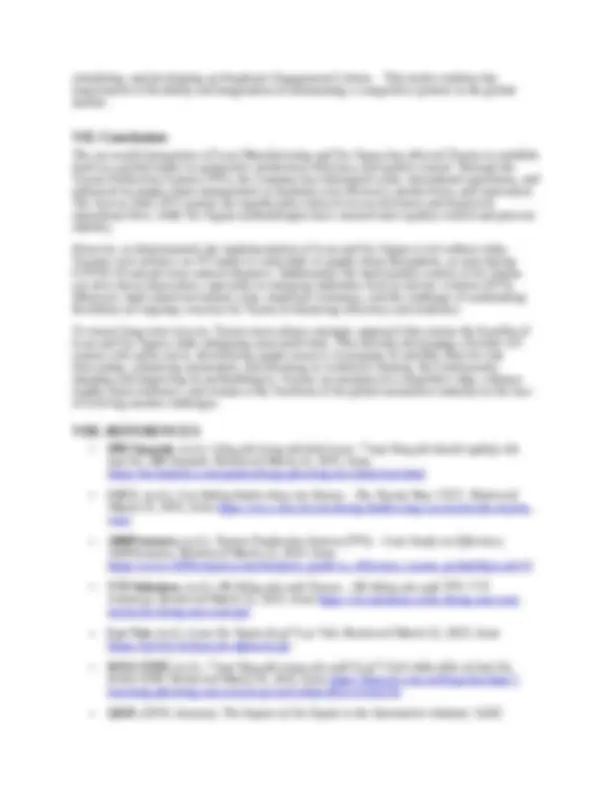
Study with the several resources on Docsity
Earn points by helping other students or get them with a premium plan
Prepare for your exams
Study with the several resources on Docsity
Earn points to download
Earn points by helping other students or get them with a premium plan
Community
Ask the community for help and clear up your study doubts
Discover the best universities in your country according to Docsity users
Free resources
Download our free guides on studying techniques, anxiety management strategies, and thesis advice from Docsity tutors
This small project/assignment was made by our group in March 3,2025. It is a course about Supply Chain Management. This project will help you overview about Toyota
Typology: Study Guides, Projects, Research
1 / 12
This page cannot be seen from the preview
Don't miss anything!
Group Presentation TOYOTA MOTOR CORPORATION ACKNOWLEDGEMENT
In the context of globalization and the rapid advancement of technology, manufacturing enterprises face increasing pressure to optimize processes, reduce costs, and enhance product quality. Fierce competition requires companies not only to increase productivity but also to ensure flexibility and responsiveness to market demands. To achieve these goals, two crucial manufacturing management methodologies have emerged and become industry standards in modern industrial production: Lean Manufacturing and Six Sigma. Lean Manufacturing is a production management philosophy developed from the Toyota Production System (TPS), focusing on waste elimination, optimizing value streams, and creating an efficient production system. Lean helps businesses not only reduce costs but also improve production speed and enhance product quality. One of the core principles of Lean is eliminating the seven types of waste (Muda) in manufacturing, which include excess inventory, overproduction, unnecessary transportation, waiting time in processes, inefficient movement, excessive processing, and defective products. Eliminating these factors helps businesses cut costs, improve production flow, and increase the value delivered to customers. In addition to Lean, Six Sigma is a quality management methodology developed by Motorola in the 1980s to minimize defects and variability in production processes. Six Sigma focuses on using data and statistical analysis to identify the root causes of problems and implement improvement measures. One of the most important tools in Six Sigma is the DMAIC process (Define - Measure - Analyze - Improve - Control), which consists of five key steps: defining the problem, measuring relevant data, analyzing root causes, implementing improvement solutions, and maintaining control to sustain effectiveness. By leveraging a data-driven approach, Six Sigma helps businesses reduce defect r below 3.4 defects per million opportunities (DPMO - Defects Per Million Opportunities), thereby enhancing production accuracy and improving customer experience
Company’s Name: Toyota Motor Corporation Established: 1937
Director-General (President & CEO): Koji Sato (as of 2023) Headquarters: 1 Toyota-Cho, Toyota City, Aichi Prefecture, Japan In the context of rapid global economic development and increasingly fierce competition, optimizing the supply chain has become a key factor in helping businesses improve productivity, reduce costs, and maintain a competitive advantage. This is especially true in the automotive manufacturing industry, where production processes are becoming more complex, and supply chains extend across the globe. The application of advanced management methodologies such as Lean Manufacturing and Six Sigma has enabled companies not only to optimize their processes but also to minimize waste and enhance product quality. Lean Manufacturing is a production philosophy focused on eliminating waste within the value chain, ensuring that manufacturing activities are centered on creating maximum value for customers. Meanwhile, Six Sigma is a quality management approach aimed at reducing variations in production processes and ensuring that products meet the highest quality standards. When Lean and Six Sigma are integrated into supply chain management, companies can significantly enhance operational efficiency, leading to a more agile, stable, and effective supply chain. One of the pioneering and most successful companies in implementing Lean and Six Sigma in its supply chain is Toyota. Through the Toyota Production System (TPS), the company has set the gold standard in the automotive industry for process optimization and quality control. This system has not only enabled Toyota to maintain its leadership position in the automotive sector but has also become a benchmark model for many other businesses to learn from and adopt.
Toyota is known as a pioneer in applying Lean Manufacturing and Six Sigma to its production processes and supply chain management. By integrating these two philosophies, Toyota has developed a streamlined and highly efficient manufacturing system, enhancing productivity, ensuring strict quality control, and optimizing costs. Lean Manufacturing helps Toyota eliminate waste at every stage of production, while Six Sigma improves quality by minimizing defects and controlling process variations. The successful implementation of these methodologies has not only enabled Toyota to maintain its leadership in the automotive industry but has also established modern manufacturing standards that many other companies strive to follow. The Toyota Production System (TPS) serves as the core foundation of Toyota's Lean philosophy. TPS is built on two fundamental principles:
DMAIC methodology (Define – Measure – Analyze – Improve – Control), which helps identify weaknesses in production processes, measure performance, analyze the root causes of defects, implement improvements, and control results to maintain consistent quality. Toyota uses Define to identify key issues affecting product quality, setting clear improvement objectives. In the Measure phase, Toyota collects relevant production performance data and closely monitors each step in the process. Then, the company applies Analyze to determine the root causes of defects, which helps develop improvement solutions in the Improve phase. Finally, Toyota implements Control to ensure that the improvements are effectively maintained, leading to continuous quality enhancement. Beyond DMAIC, Toyota also utilizes Design for Six Sigma (DFSS) to design products and processes from the outset to ensure optimal quality. DFSS helps the company identify critical factors in production, thereby minimizing defects right from the product design stage. By implementing Six Sigma, Toyota has significantly reduced defect rates in manufacturing, leading to improved performance and higher-quality vehicles.
Although Toyota is one of the pioneers and most successful companies in applying Lean Manufacturing and Six Sigma in production, it still faces several potential risks when implementing these methodologies. Lean optimization helps Toyota reduce waste, while Six Sigma ensures strict quality control. However, both approaches have certain drawbacks. When a production system becomes overly lean and excessively optimized, the company may become vulnerable to external disruptions, especially in the increasingly complex global economy and fragile supply chains. Toyota has encountered significant risks in applying Lean and Six Sigma, particularly during crises such as the COVID-19 pandemic, when global supply chains were severely disrupted. Additionally, relying heavily on the Just-in-Time (JIT) system made it difficult for the company to maintain production when facing component shortages. Furthermore, overly strict implementation of Six Sigma may reduce flexibility in the production process, making it challenging for the business to quickly adapt to sudden market changes.
One of the biggest risks of Lean Manufacturing at Toyota comes from the implementation of the Just-in-Time (JIT) system. JIT helps the company minimize inventory levels by supplying materials only in the exact quantity and at the precise time they are needed. However, this also means that Toyota must maintain an extremely efficient supply chain, leaving no room for errors or disruptions. If any link in the supply chain encounters an issue, the entire production system can be severely affected. During the COVID-19 pandemic, Toyota's JIT system faced significant challenges. The shortage of critical components, particularly semiconductors—an essential part of modern vehicles— forced Toyota to cut production at multiple factories worldwide. Because the company did not maintain a safe inventory buffer, it was unable to respond quickly to supply chain disruptions. As a result, production was delayed, and vehicle delivery times were extended beyond expectations. Not only during the COVID- pandemic, but even before that, Toyota had suffered severe disruptions due to natural disasters.
The 2011 earthquake and tsunami in Japan caused months-long supply chain interruptions, as many of Toyota's key component suppliers were heavily damaged. Since the company did not stockpile large amounts of materials and relied heavily on JIT, it struggled to restore production efficiently. This raised a major challenge for Toyota: how to balance the efficiency of JIT with resilience against unexpected supply chain risks.
Six Sigma helps Toyota maintain strict product quality control and minimize variations in production. However, over-reliance on Six Sigma can lead to certain flexibility issues in the manufacturing process. Toyota follows rigid quality control procedures, from product design to production, ensuring that even the smallest defects are eliminated. However, this sometimes results in a lack of agility, making it harder for the company to quickly adapt to sudden market changes. For example, with the rapid growth of the electric vehicle (EV) market, automakers need to innovate quickly to meet customer demands. However, Toyota’s strict Six Sigma quality control process can make experimenting with new technologies more complex. Extensive testing, evaluation, and process controls can slow down the development of new products, reducing Toyota’s competitiveness against more agile companies like Tesla. Below is a comparison table between Toyota’s Six Sigma system and Tesla’s flexible production model, highlighting the limitations in flexibility when Six Sigma is applied excessively: Feature Toyota’s Six Sigma System Tesla’s Flexible Production Model Product Development Speed Slower due to strict inspection requirements and multiple approval stages. More agile due to higher risk tolerance and adoption of a mass testing model. Technological Innovation Capability More limited due to strict quality control procedures, difficult to adjust quickly. More agile due to willingness to experiment with new technologies and refine during production. Quality Control Process Very strict, focusing on eliminating all errors from the beginning. Focus on rapid improvement, accepting a certain level of failure to speed up development. New Product Deployment Time Longer due to multiple inspection steps and strict procedures. Shorter due to agile manufacturing approach and ability to continuously adjust. Market Responsiveness Lower because changes in design or manufacturing process Higher because Tesla can adjust and change vehicle designs
Instead of relying solely on a “just enough, just in time” supply approach, Toyota can implement a "Flexible JIT" model, where high-risk components such as semiconductors, electronic sensors, and lithium-ion batteries are stored in optimized quantities. This does not mean abandoning JIT, but rather modifying it to better align with reality and prevent material shortages.
One of the major weaknesses of Lean is that it makes Toyota overly dependent on a few key suppliers, particularly those located in Asia. When disruptions such as the COVID-19 pandemic or trade tensions occur, Toyota is highly vulnerable to supply shortages. To address this issue, Toyota needs to implement a supply chain diversification strategy by collaborating with multiple suppliers from different regions. For example, instead of relying solely on semiconductor manufacturers in Japan and Taiwan, Toyota could seek partnerships in the U.S., Europe, or even develop an internal supply chain to ensure access to critical components. Additionally, Toyota could adopt a "Regionalized Supply Chain" model, where factories in each region prioritize local suppliers, helping minimize risks in the event of global disruptions.
Technology plays a crucial role in helping Toyota enhance its forecasting capabilities and manage the supply chain more efficiently. With advancements in Artificial Intelligence (AI) and Big Data, Toyota can utilize advanced analytical models to predict material demand, detect early supply chain disruption risks, and proactively develop contingency plans. By analyzing historical data from thousands of suppliers worldwide, Toyota can identify irregular patterns in deliveries, detect warning signs of delays or disruptions, and make rapid decisions before issues escalate. Additionally, Toyota can implement a real-time supply chain monitoring system, utilizing Internet of Things (IoT) sensors to track transportation status, material quality, and supplier performance. This enables Toyota to maintain complete control over the supply chain, ensuring greater flexibility and minimizing risks of disruptions.
One way for Toyota to minimize the impact of supply chain disruptions is by enhancing its production autonomy. To achieve this, Toyota must continue investing in automation and in- house manufacturing of critical components. Currently, Toyota has developed Smart Factories with high levels of automation, utilizing robots and artificial intelligence to improve production efficiency and reduce dependence on manual labor. However, the company needs to further expand its in-house manufacturing initiatives, such as producing semiconductors, electric vehicle battery systems, and other essential components, instead of relying entirely on external suppliers. This approach not only allows Toyota to maintain better control over product quality but also reduces the risk of supply chain disruptions caused by external suppliers' issues. Additionally, Toyota should invest in flexible manufacturing plants capable of switching between different product lines, ensuring quick adaptation to market changes and fluctuations in demand.
In addition to technology and supply chain management, Toyota must also prioritize its workforce. Employee resistance to Lean and Six Sigma can hinder the effective implementation of these methodologies. To address this issue, Toyota needs to heavily invest in training and workforce development to ensure employees understand the benefits of Lean and Six Sigma while equipping them with the necessary skills to work in a modern manufacturing environment. Toyota can implement continuous training programs focused on Lean thinking, Six Sigma, and automation technologies, helping employees enhance their capabilities and adapt to changes in work processes. Moreover, fostering a corporate culture that encourages continuous improvement will enable Toyota to sustain innovation and long-term optimization in manufacturing.
Efficiency and Innovation
A major obstacle that Toyota had to overcome in the early 2000s that jeopardized the company’s manufacturing efficiency was overproduction. Despite its advanced manufacturing system and focus on high quality, Toyota actually produced more than the market demanded, which increased inventory costs and caused storage problems. This has created a new problem with the Just-in-Time (JIT) model, whereby the company is subjected to changes in production schedules when the core issue is whether there is an overall profit associated with such operations at present.
Toyota has used a multifarious approach grounded on lean manufacturing in order to overcome the overcapacity situation. These are the primary actions:
scheduling, and developing an Employee Engagement Culture. This study confirms the requirement of flexibility and imagination in maintaining a competitive posture in the global market.
The successful integration of Lean Manufacturing and Six Sigma has allowed Toyota to establish itself as a global leader in automotive production efficiency and quality control. Through the Toyota Production System (TPS), the company has eliminated waste, streamlined operations, and enhanced its supply chain management to maintain cost efficiency, productivity, and innovation. The Just-in-Time (JIT) system has significantly reduced excess inventory and improved operational flow, while Six Sigma methodologies have ensured strict quality control and process stability. However, as demonstrated, the implementation of Lean and Six Sigma is not without risks. Toyota's over-reliance on JIT makes it vulnerable to supply chain disruptions, as seen during COVID-19 and previous natural disasters. Additionally, the rigid quality control of Six Sigma can slow down innovation, especially in emerging industries such as electric vehicles (EVs). Moreover, high initial investment costs, employee resistance, and the challenge of maintaining flexibility are ongoing concerns for Toyota in balancing efficiency and resilience. To ensure long-term success, Toyota must adopt a strategic approach that retains the benefits of Lean and Six Sigma while mitigating associated risks. This includes developing a flexible JIT system with safety stock, diversifying supply sources, leveraging AI and Big Data for risk forecasting, enhancing automation, and investing in workforce training. By continuously adapting and improving its methodologies, Toyota can maintain its competitive edge, enhance supply chain resilience, and remain at the forefront of the global automotive industry in the face of evolving market challenges.
Retrieved March 22, 2025, from https://www.qad.com/blog/2019/01/the-impact-of-six- sigma-in-the-automotive
- John & Partners. (n.d.). Thách thức trong triển khai Lean Six Sigma cho doanh nghiệp sản xuất. Retrieved March 22, 2025, from https://john-partners.com/thach-thuc-trong- trien-khai-lean-six-sigma-cho-doanh-nghiep-san-xuat - Toyota Vietnam. (n.d.). Toyota Việt Nam thực hiện hành trình “Toyota - Hành trình triệu nụ cười”. Retrieved March 22, 2025, from https://www.toyota.com.vn/tin-tuc/xa-hoi/toyota-viet-nam-thuc-hien-hanh-trinh-toyota- hanh-trinh-trieu-nu-cuoi- - PMS Education. (n.d.). Ứng dụng Kaizen tại Toyota. Retrieved March 22, 2025, from https://pms.edu.vn/ung-dung-kaizen-tai-toyota/ - GoBranding. (n.d.). Kaizen và thành công của Toyota. Retrieved March 22, 2025, from https://gobranding.com.vn/kaizen-va-thanh-cong-cua-toyota - Unknown Author. (n.d.). Toyota Motor Corporation’s lean manufacturing solution: A case study. LinkedIn. Retrieved March 22, 2025, from https://www.linkedin.com/pulse/toyota-motor-corporations-lean-manufacturing-solution- case-study-qqisc/ - Shih, W. (2022, January 30). From just-in-time to just-in-case: Is excess and obsolete next? Forbes. Retrieved March 22, 2025, from https://www.forbes.com/sites/willyshih/2022/01/30/from-just-in-time-to-just-in-case-is- excess-and-obsolete-next/