
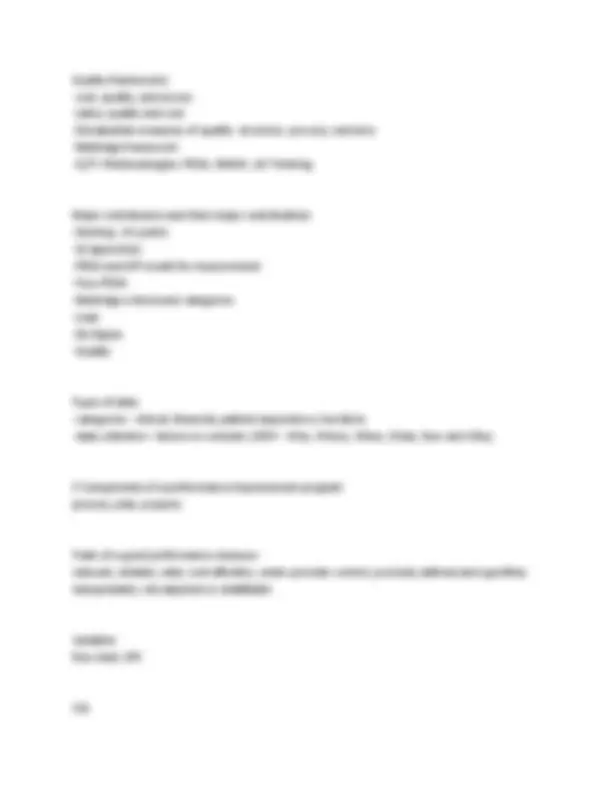
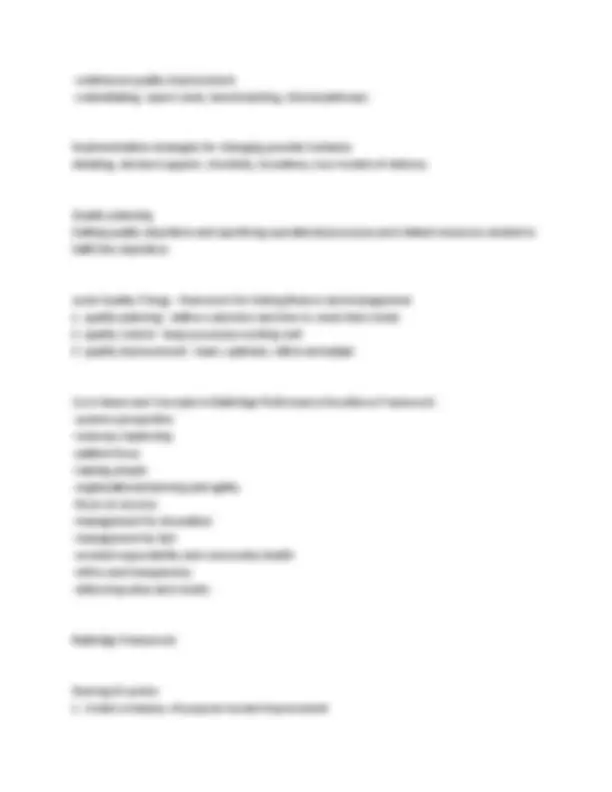
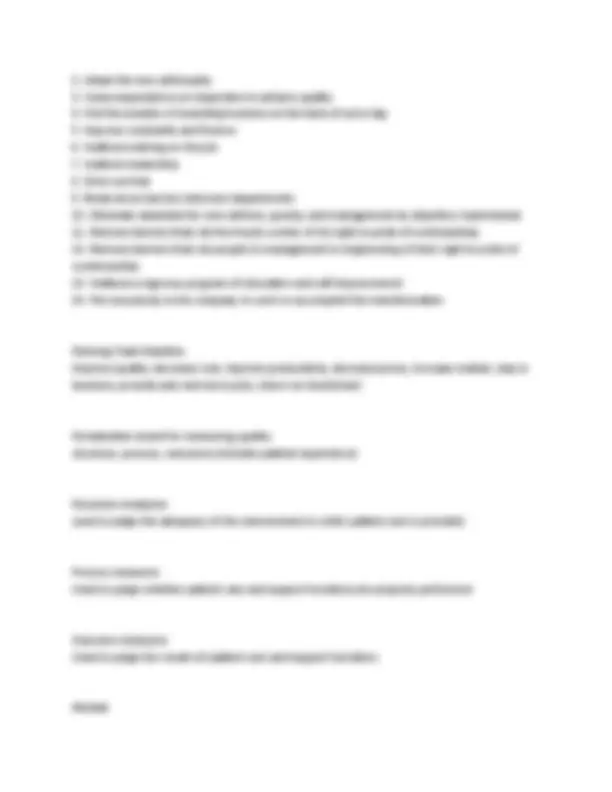
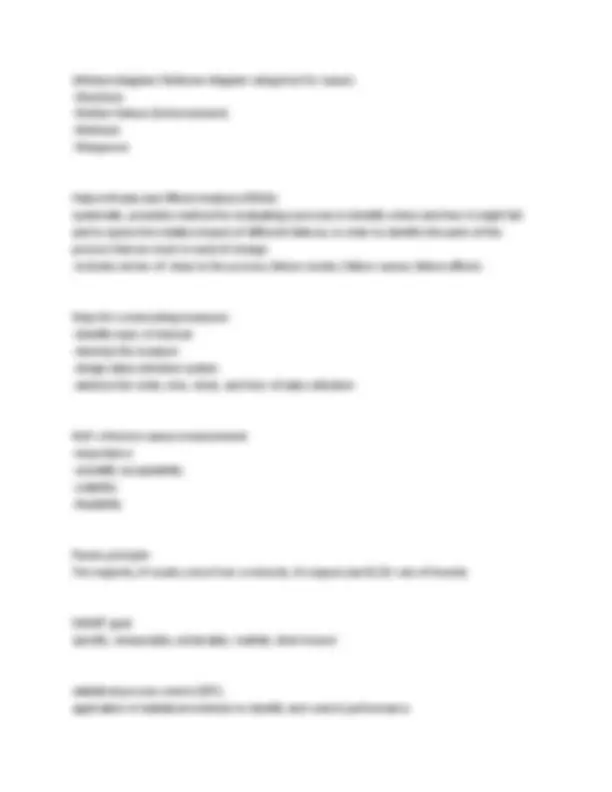
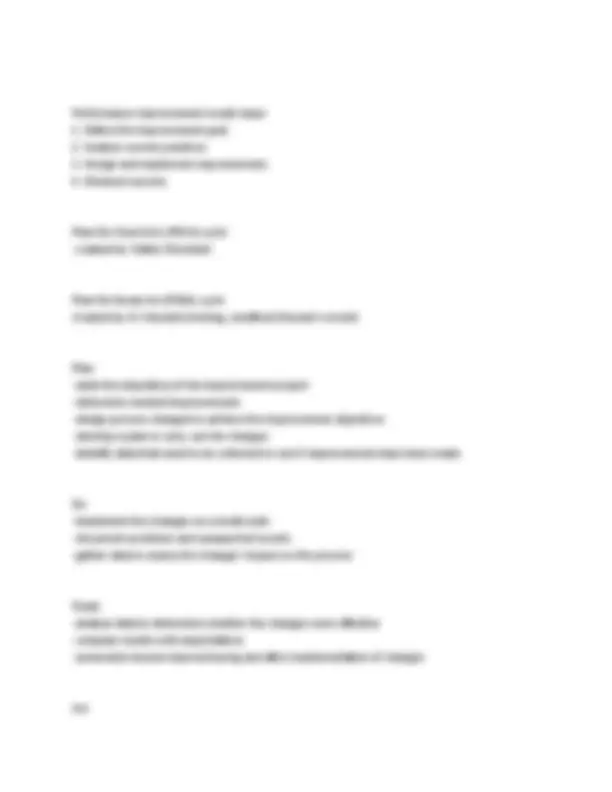
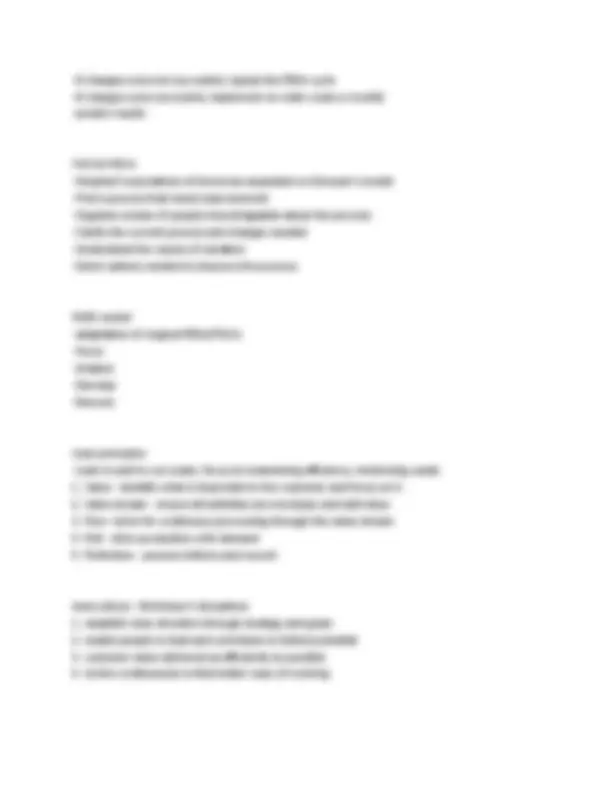
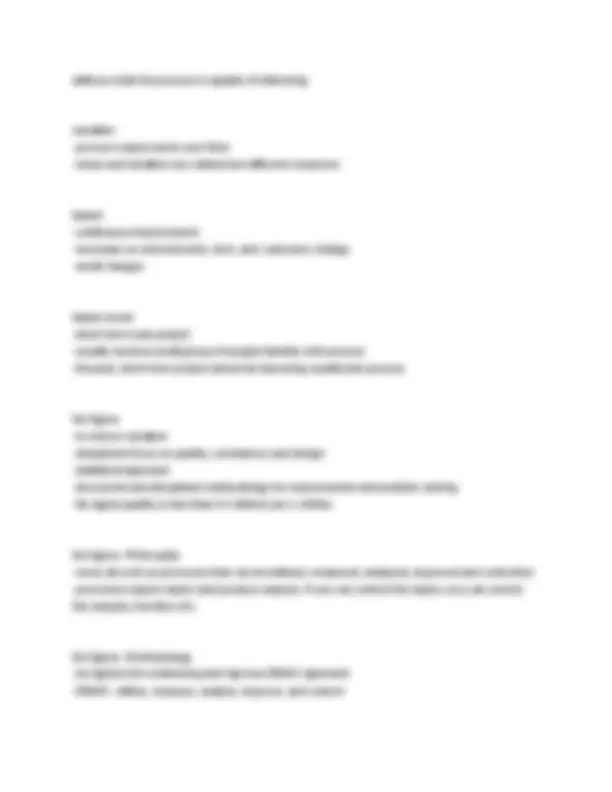
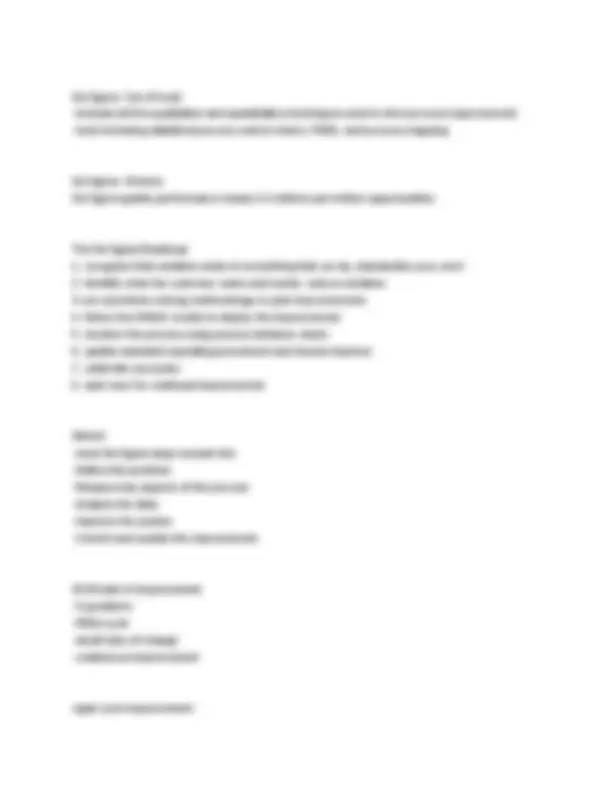
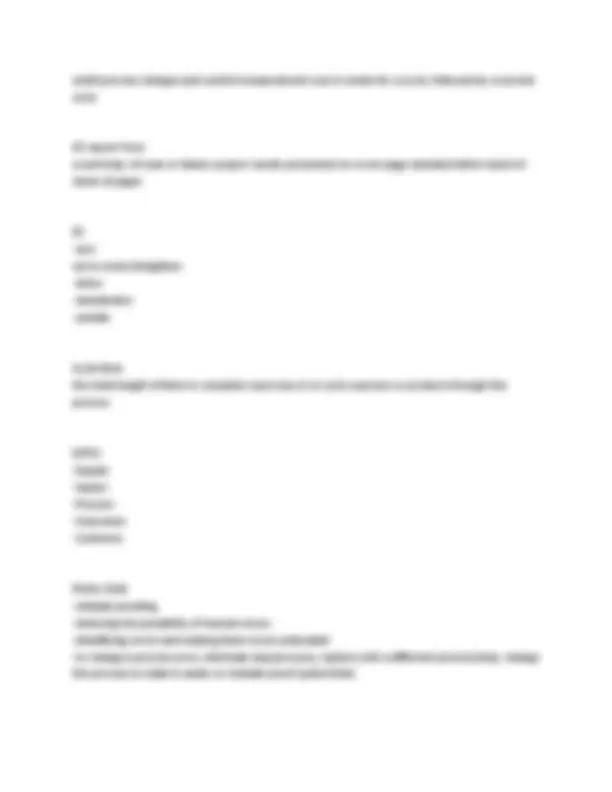
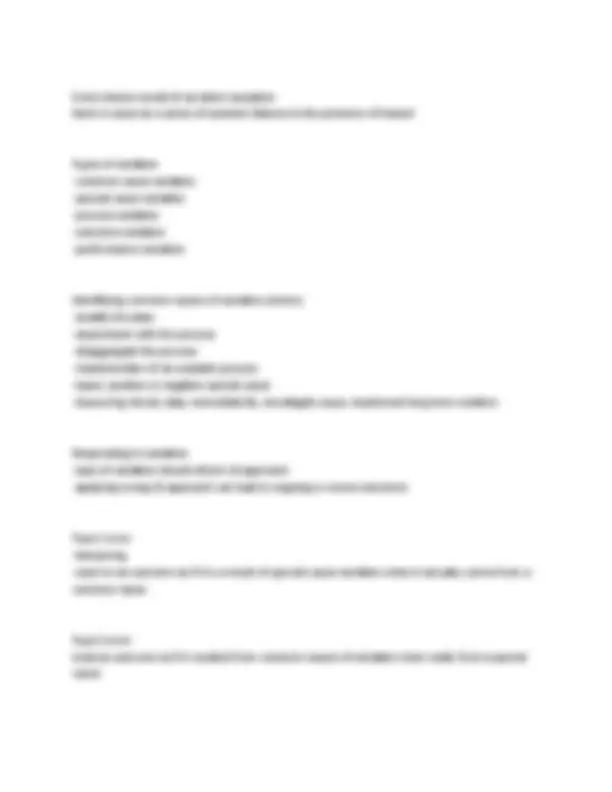
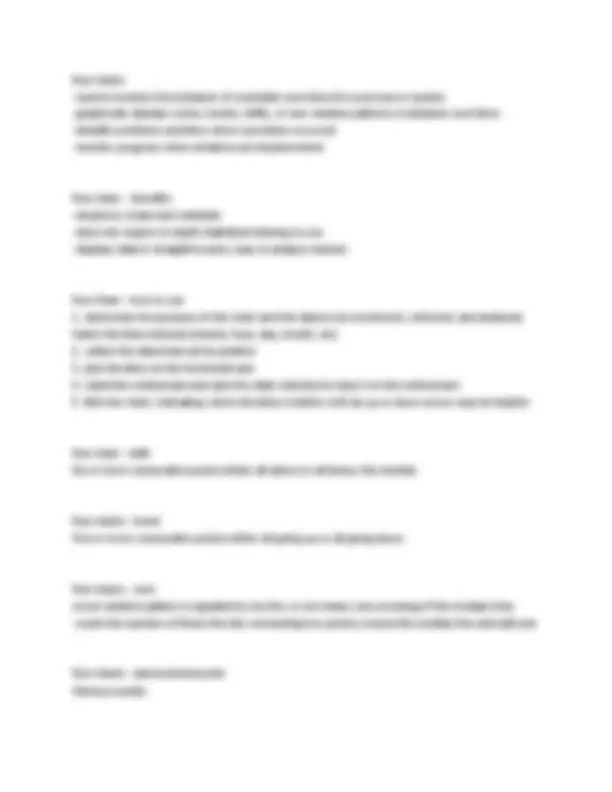
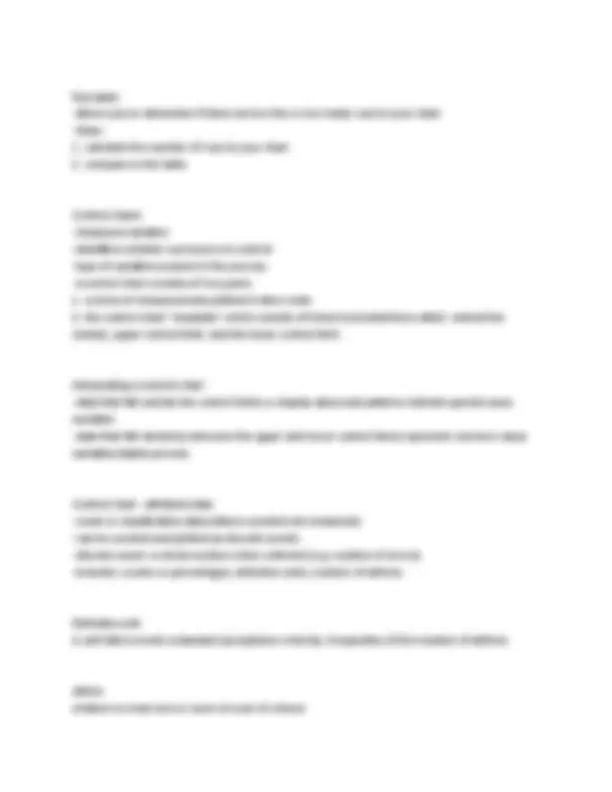
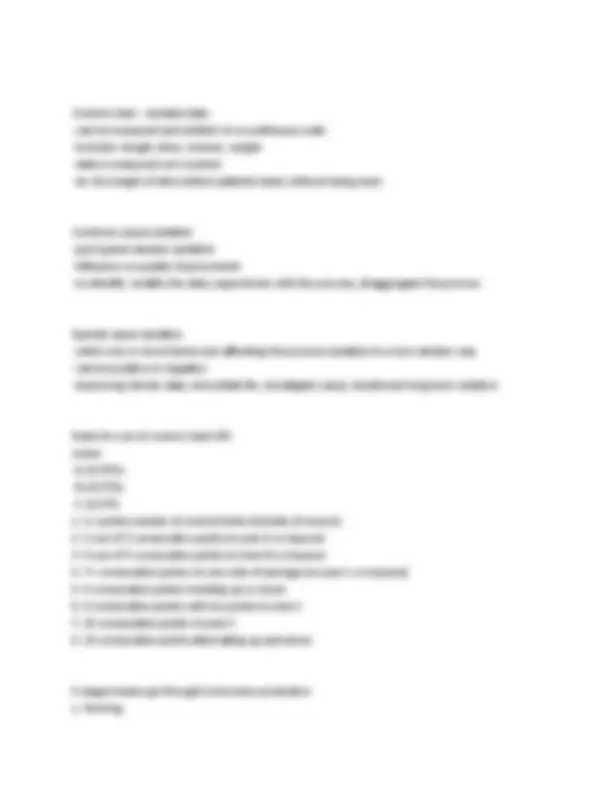
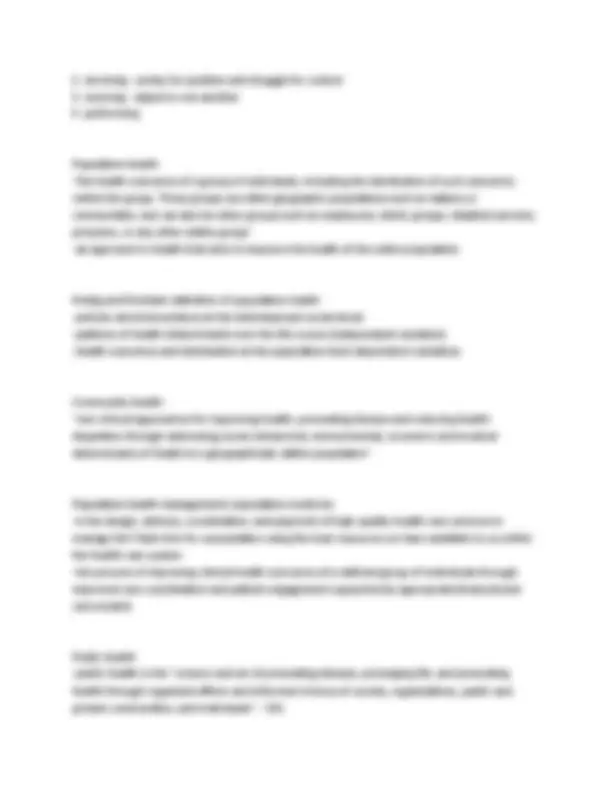
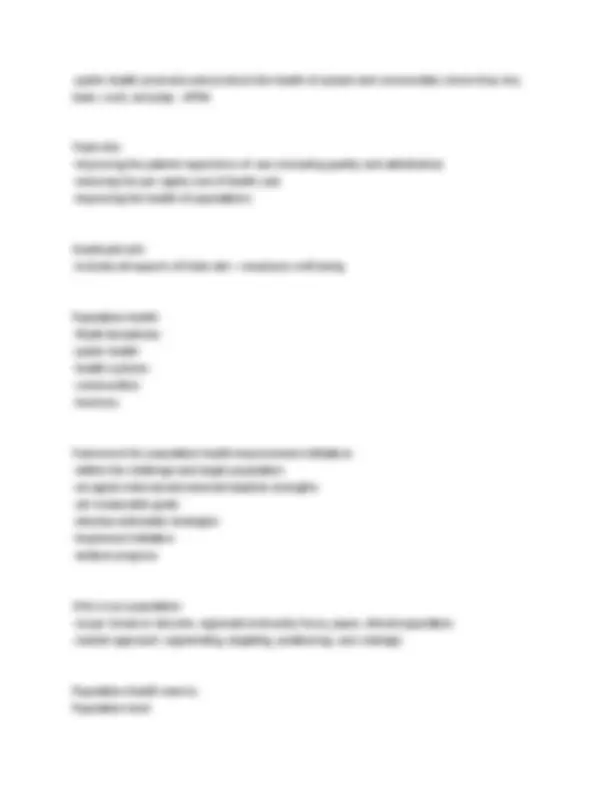
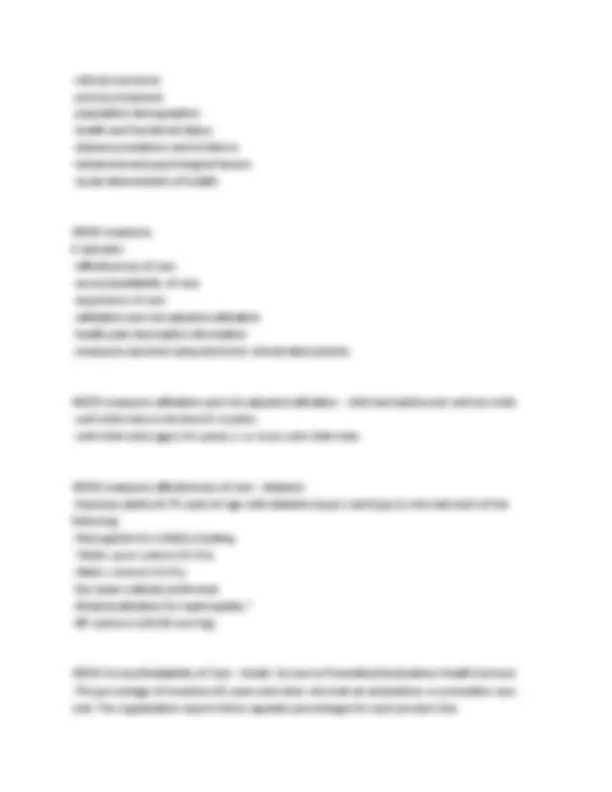
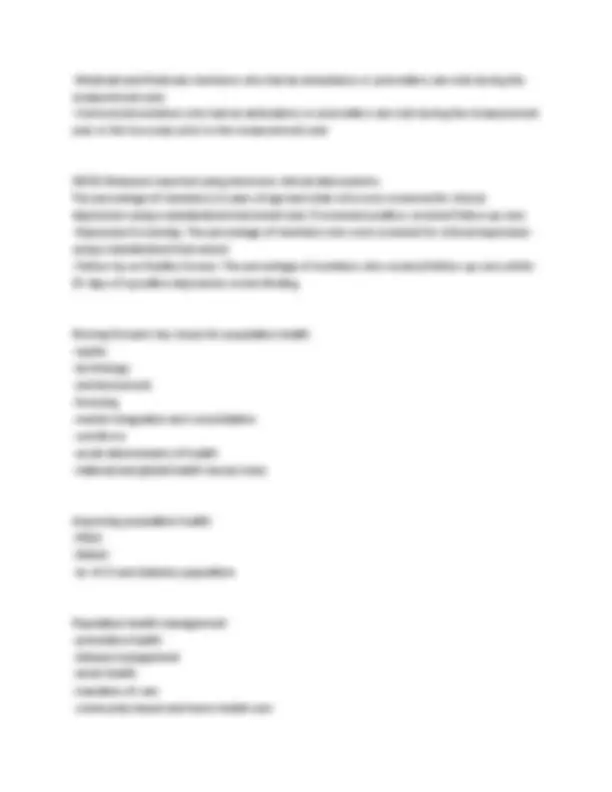
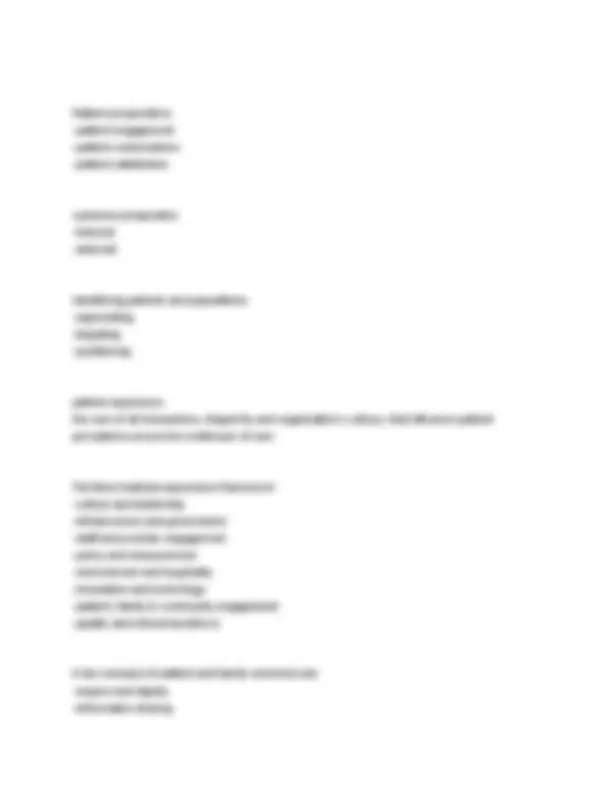
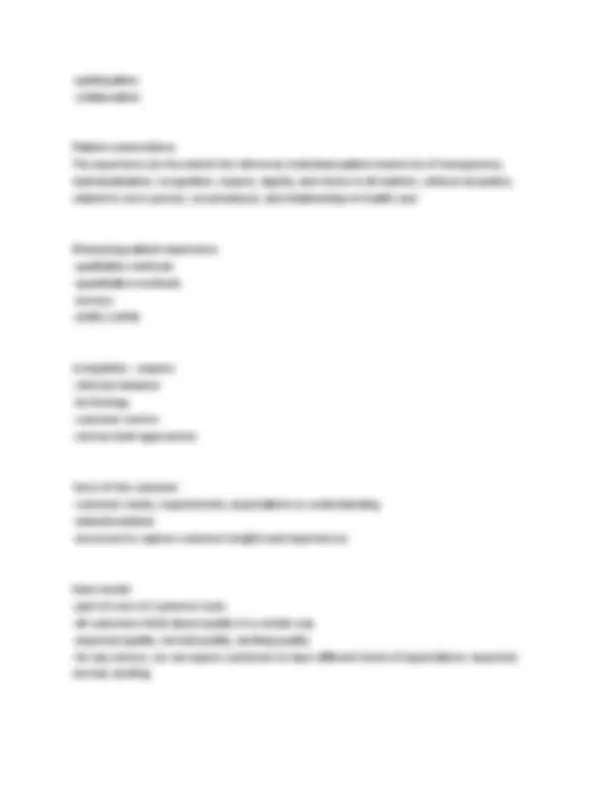
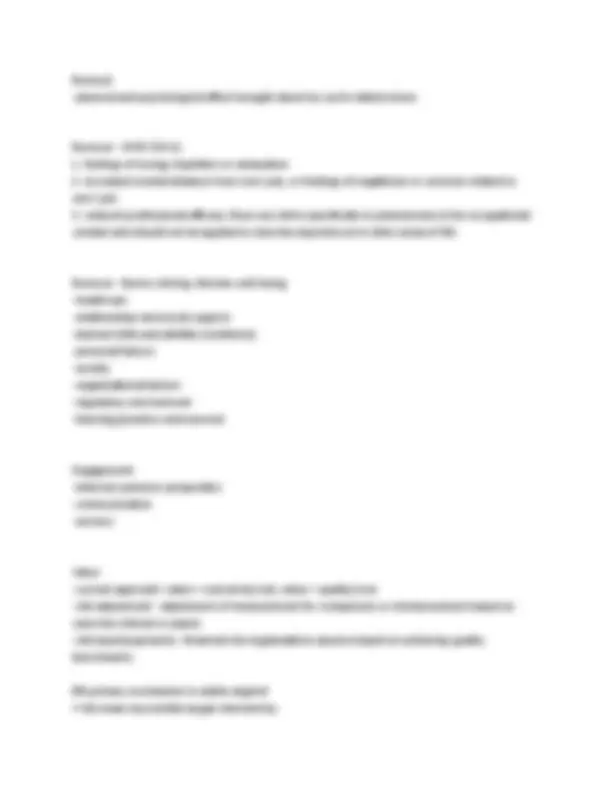
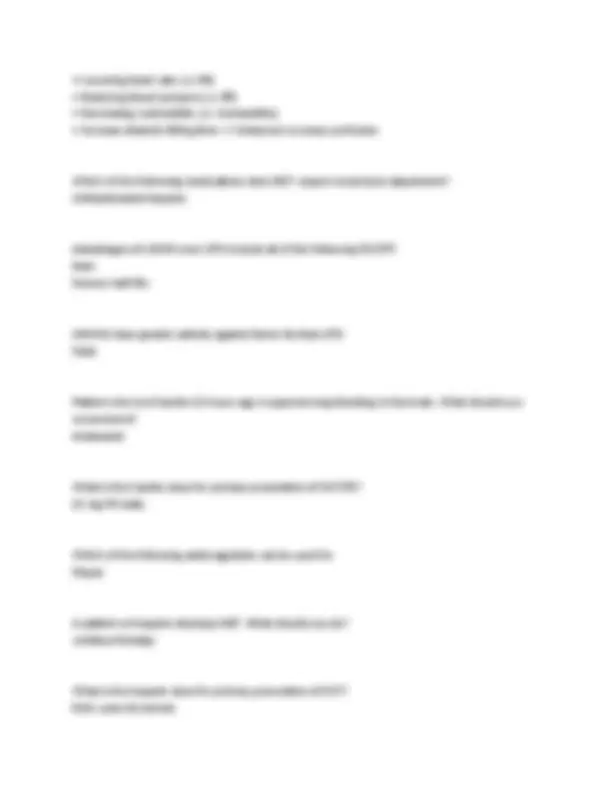
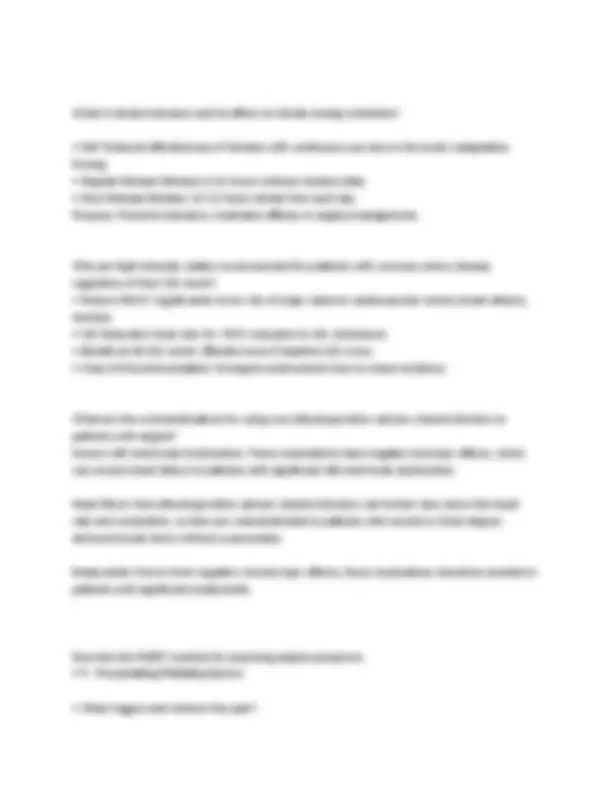
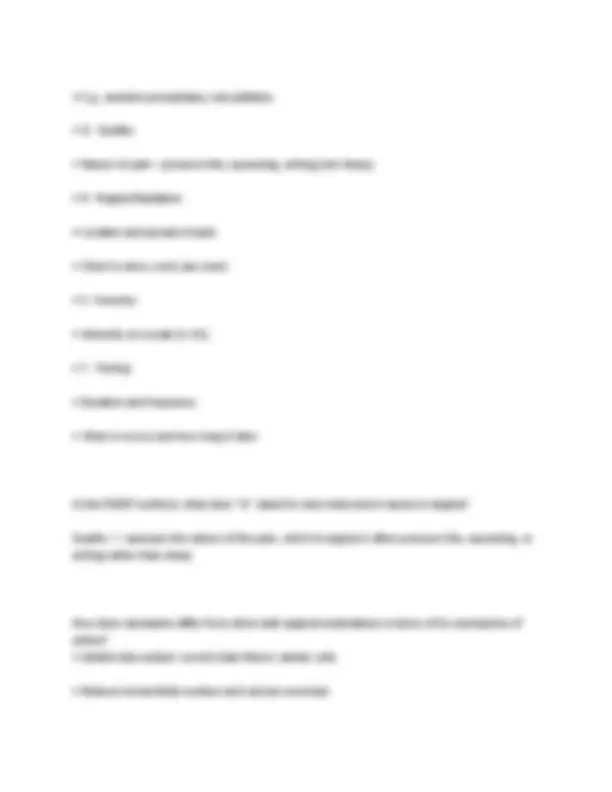
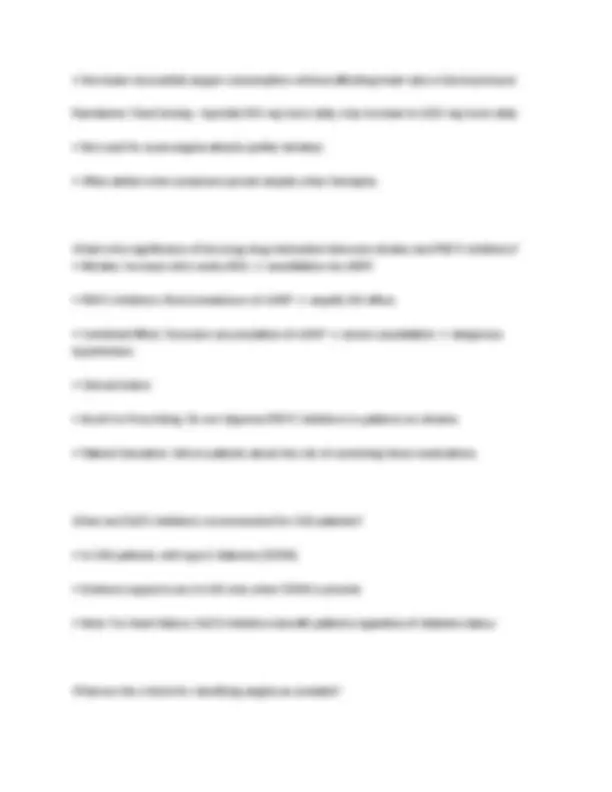
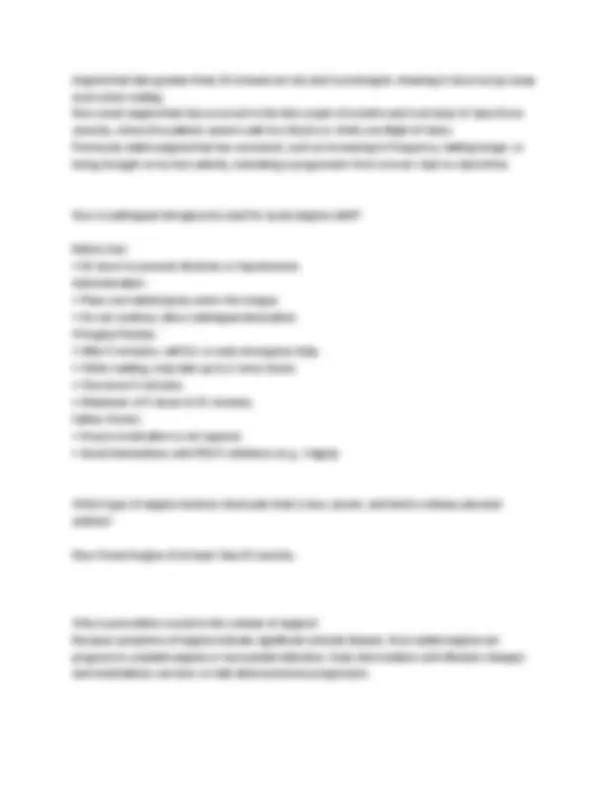
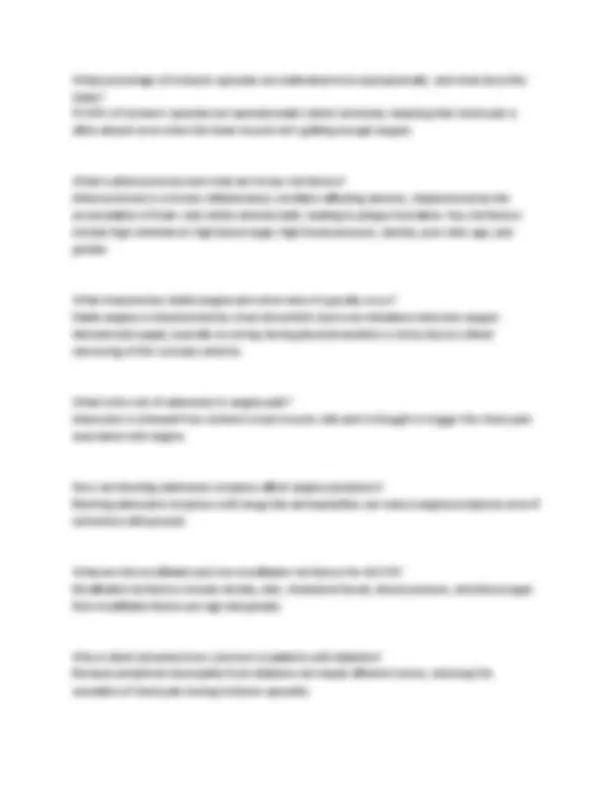
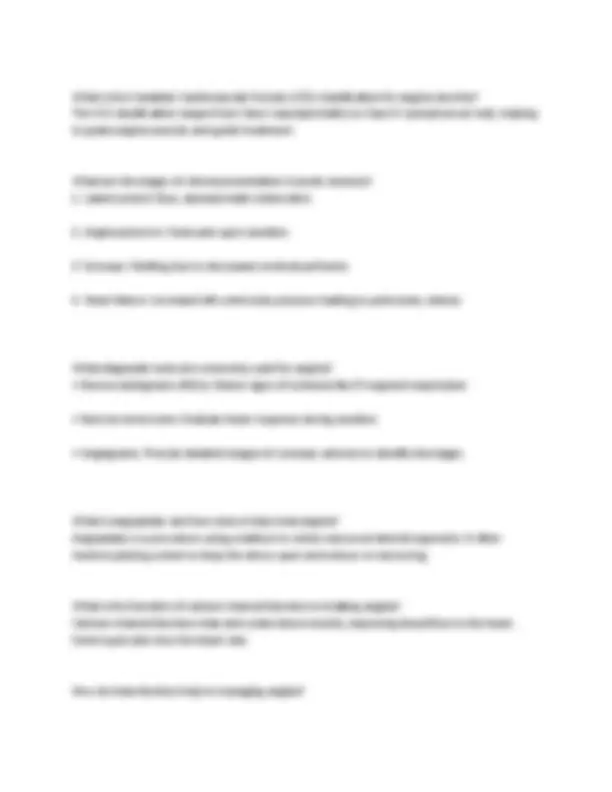
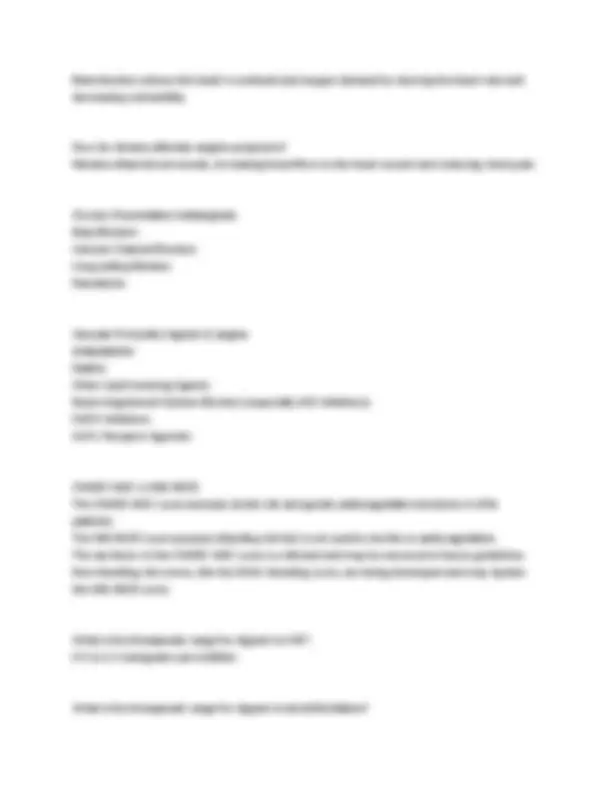
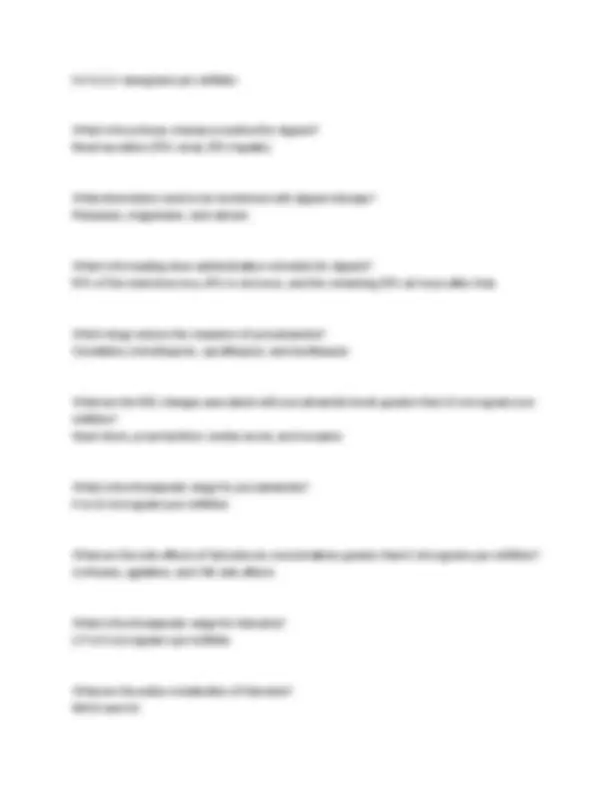
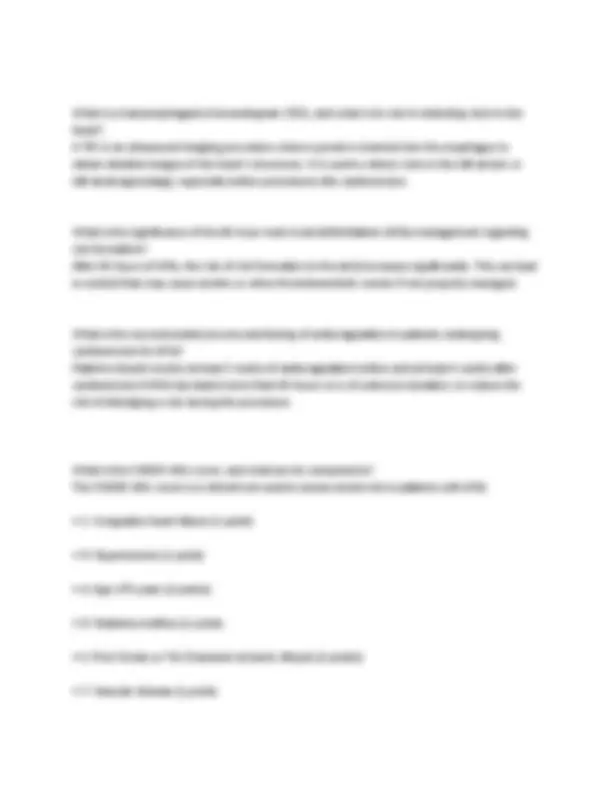
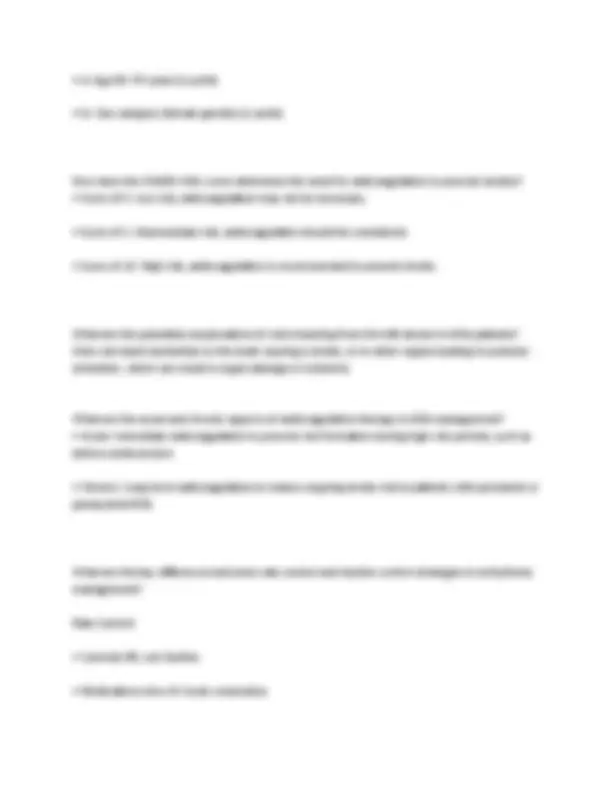
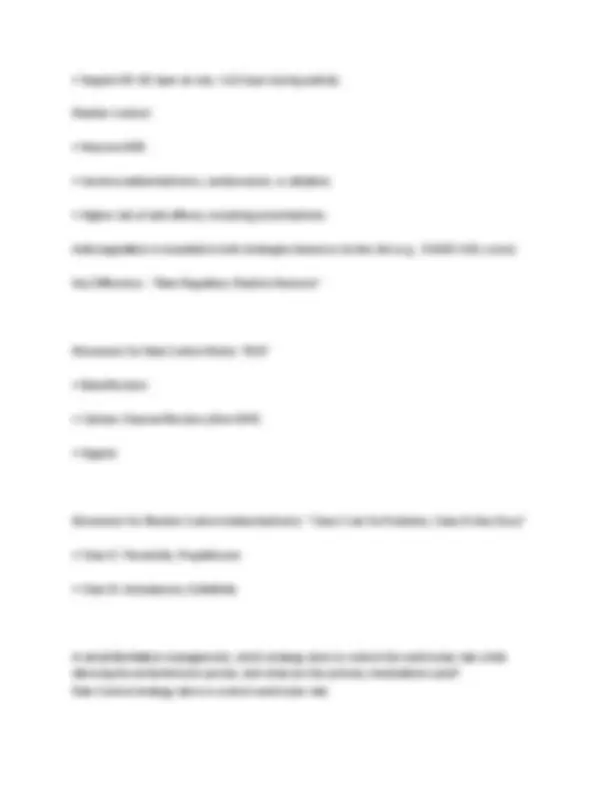
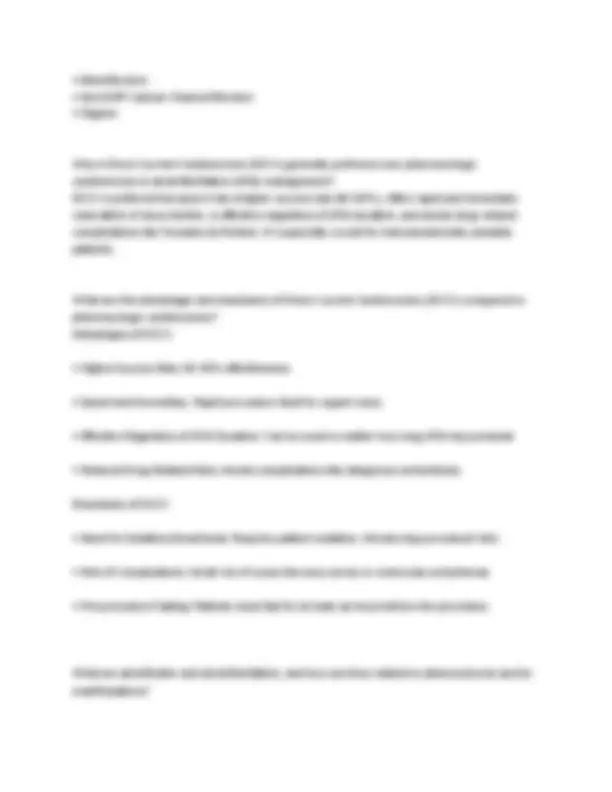
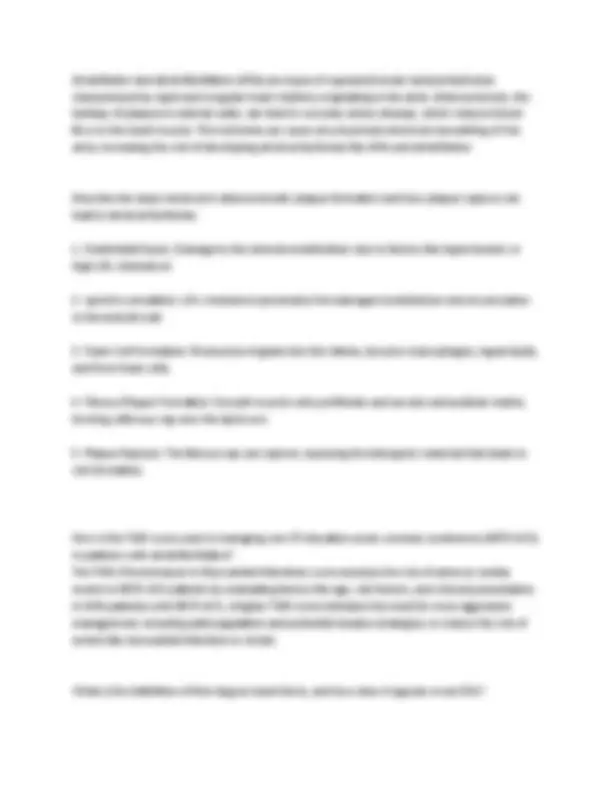
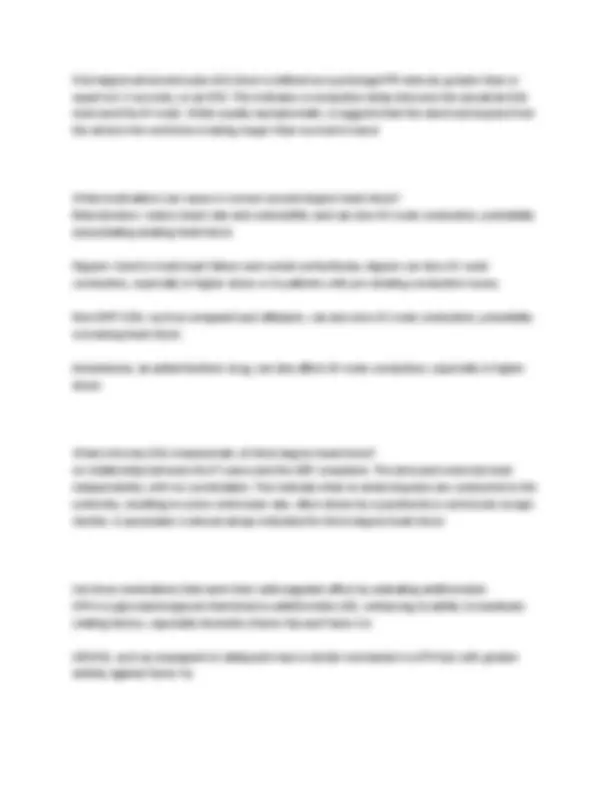
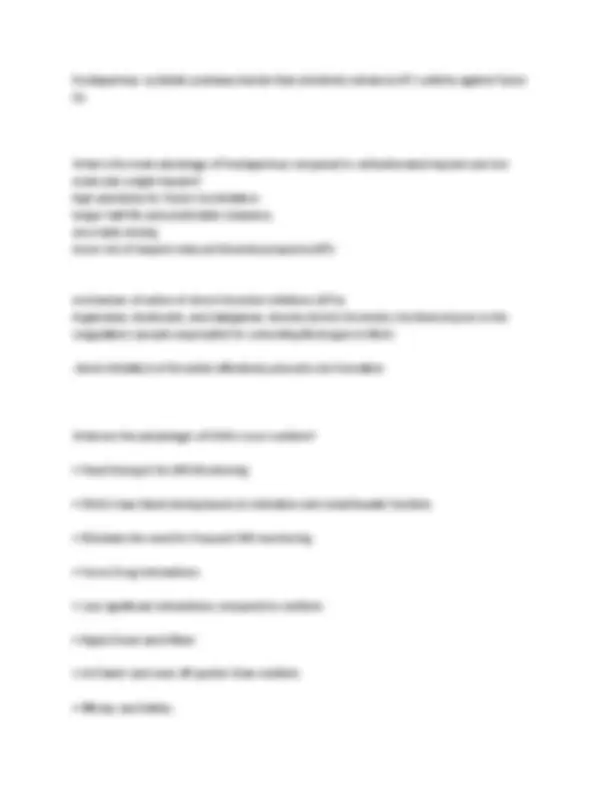
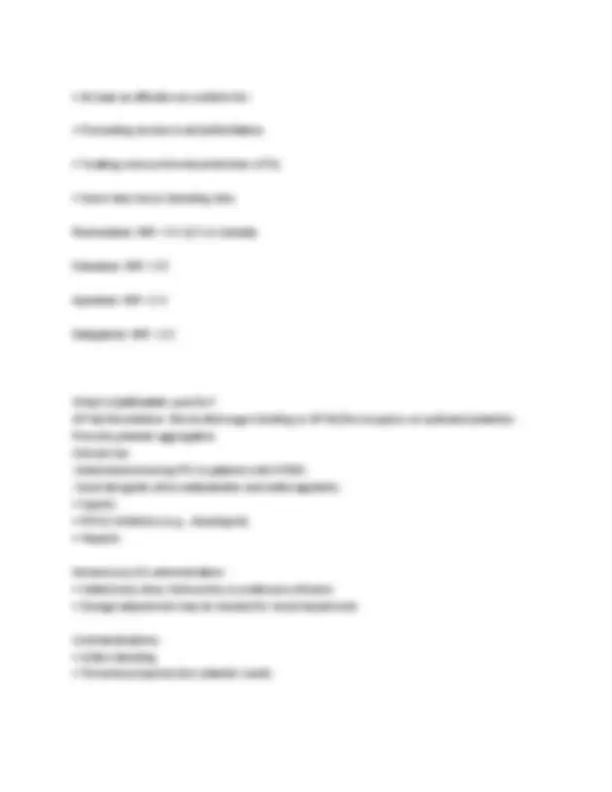
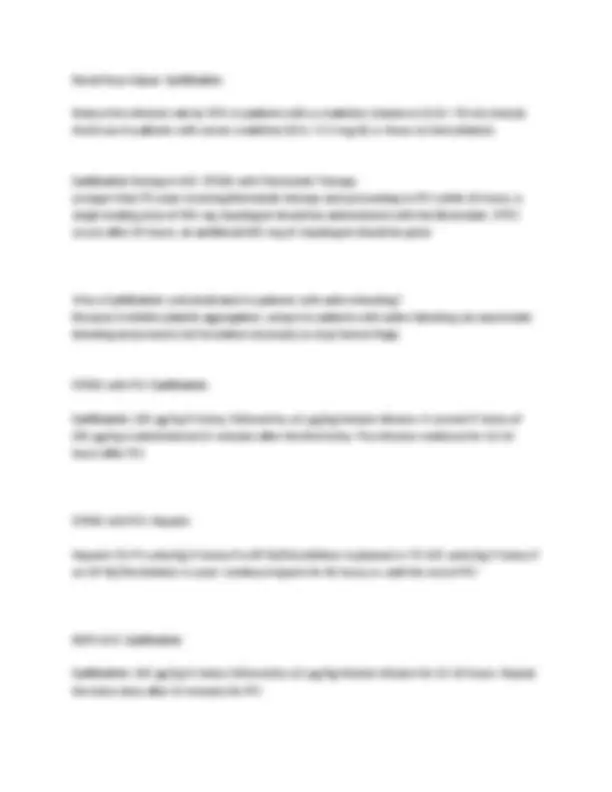
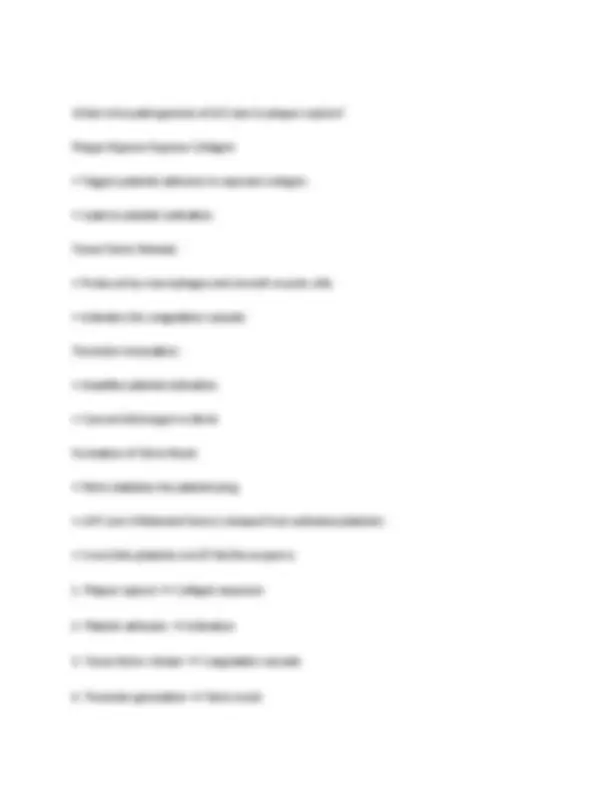
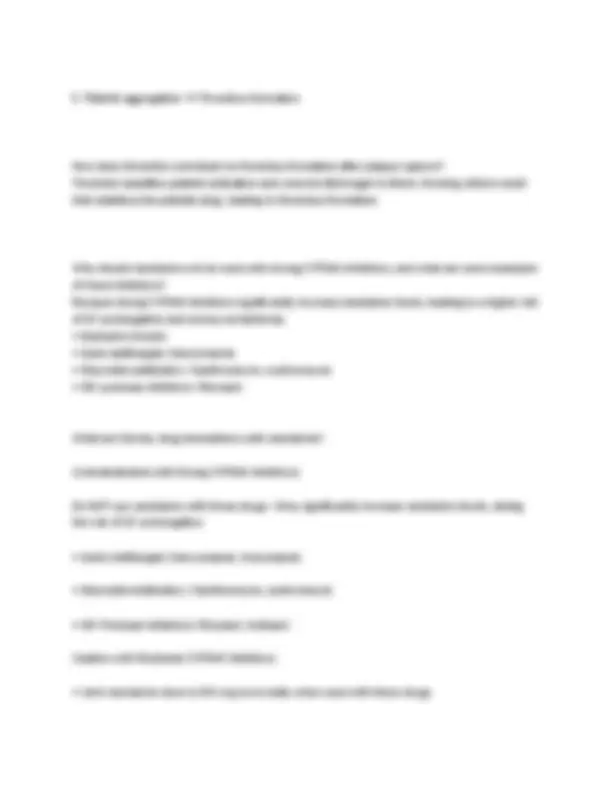
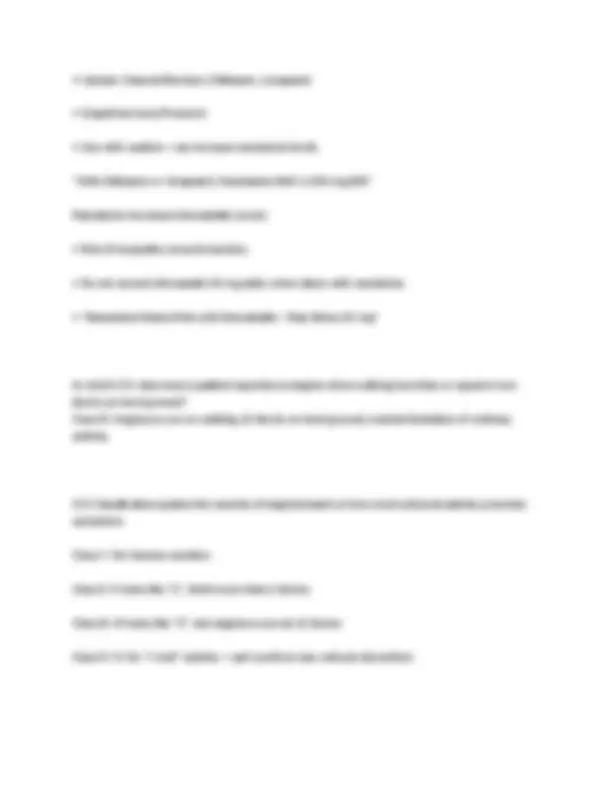
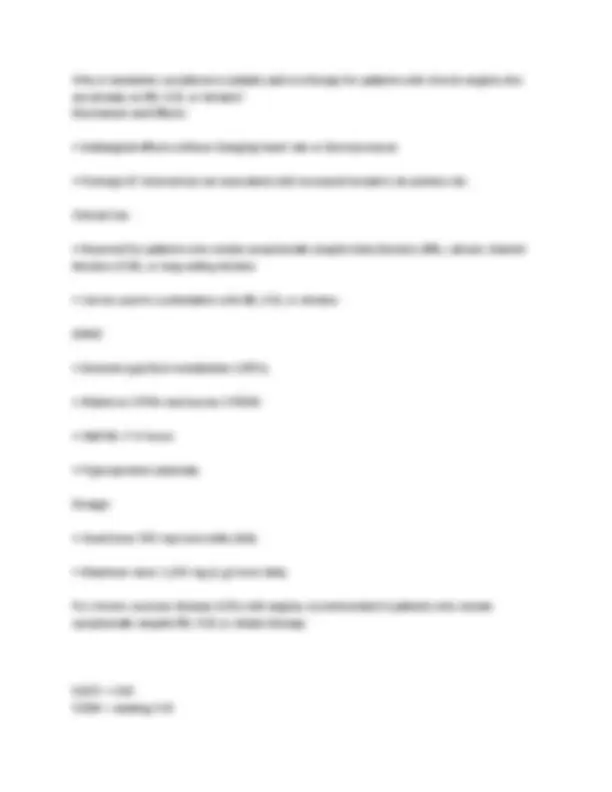
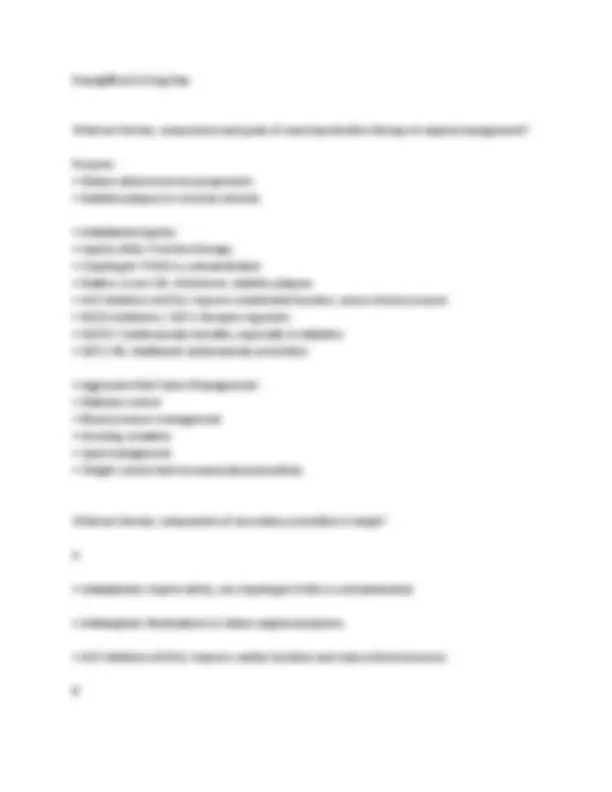
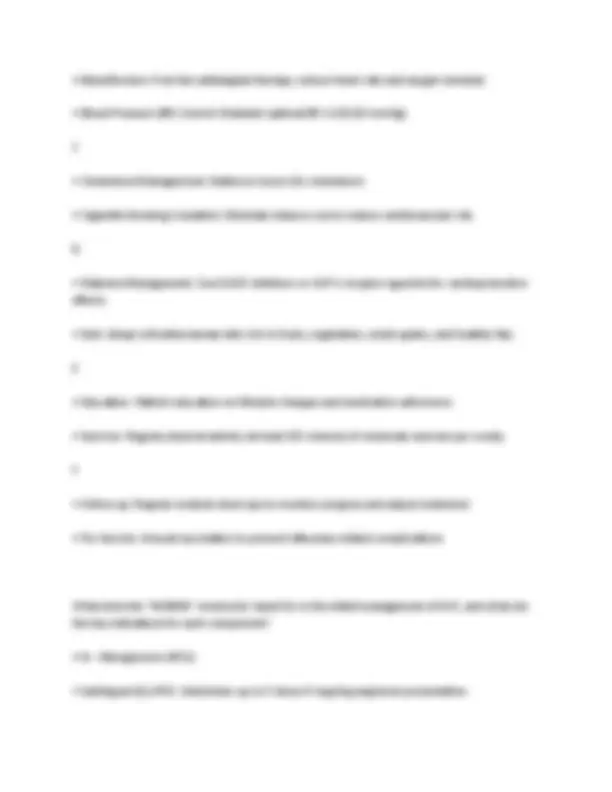
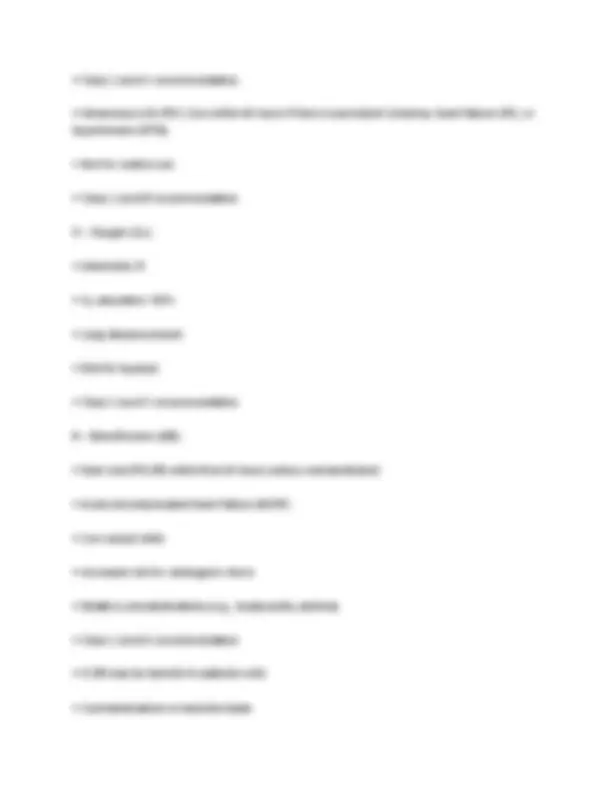
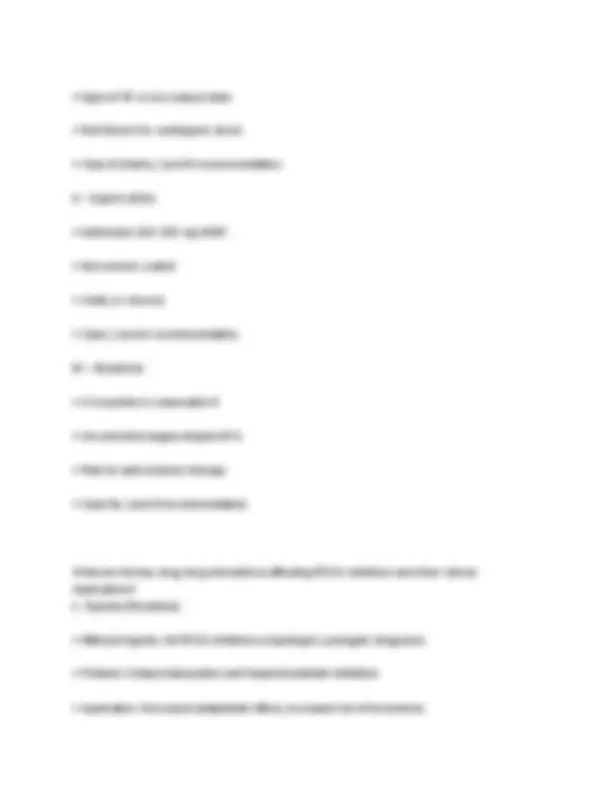
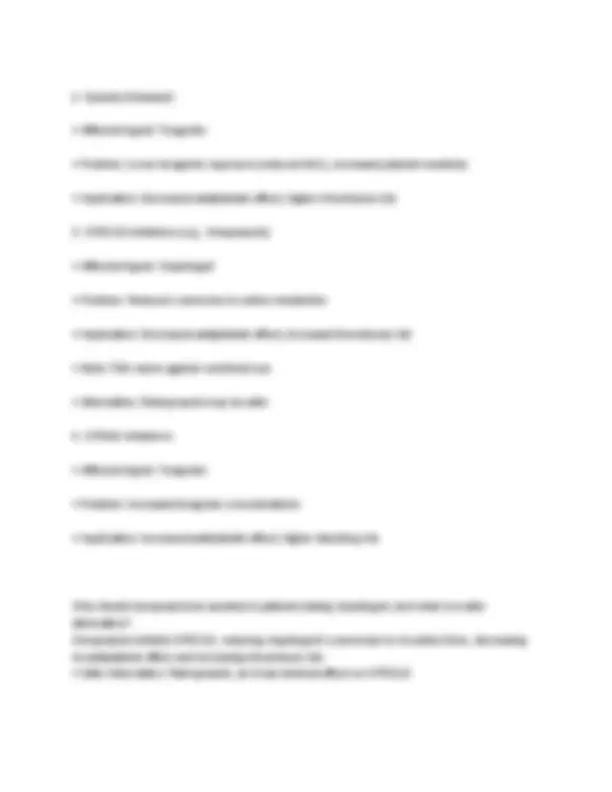
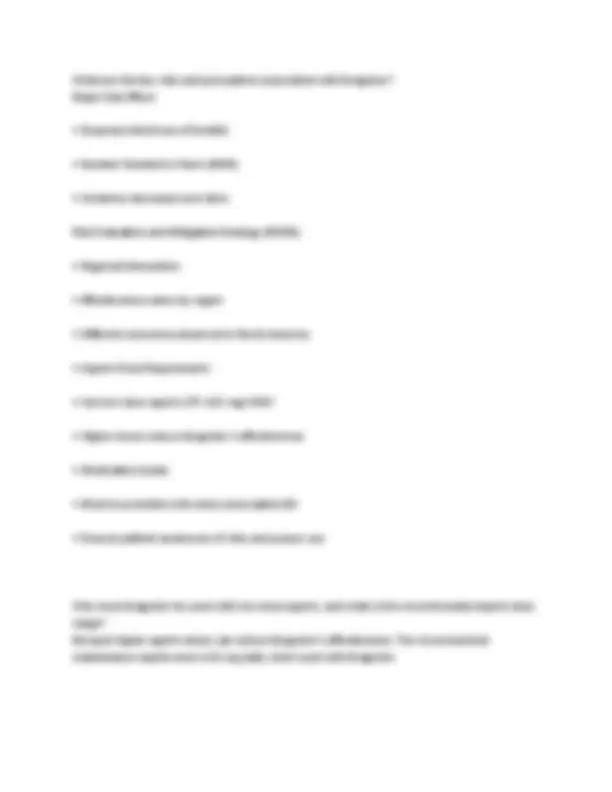
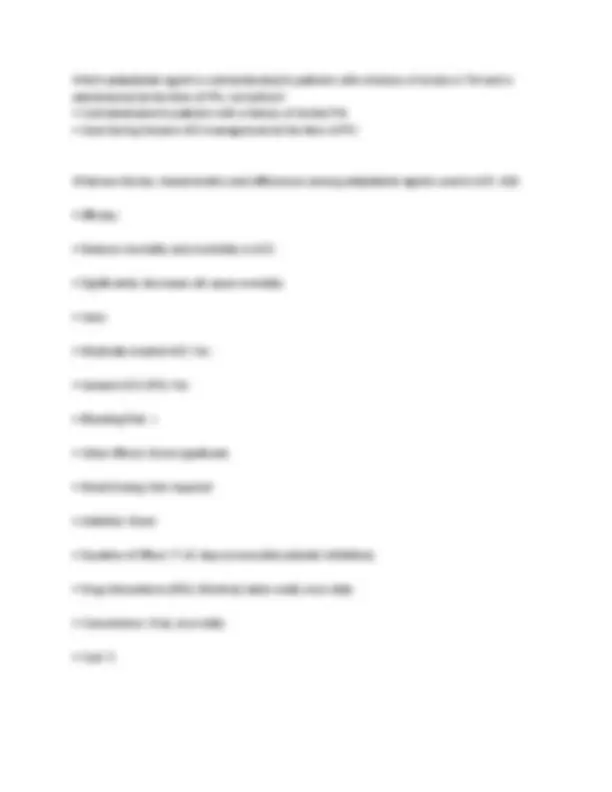
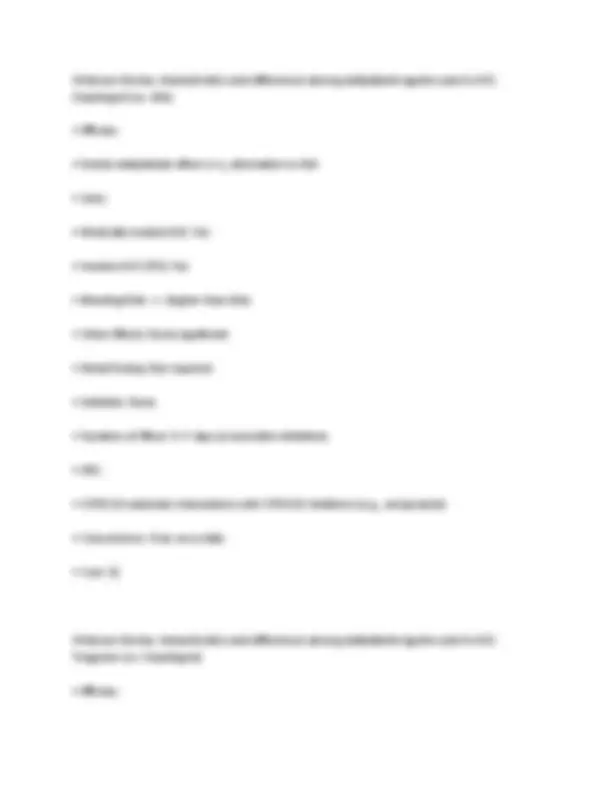
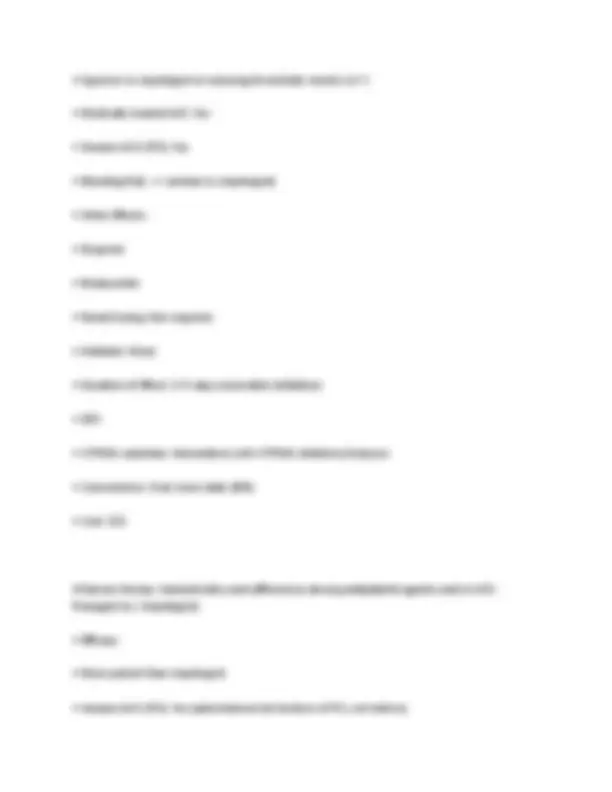
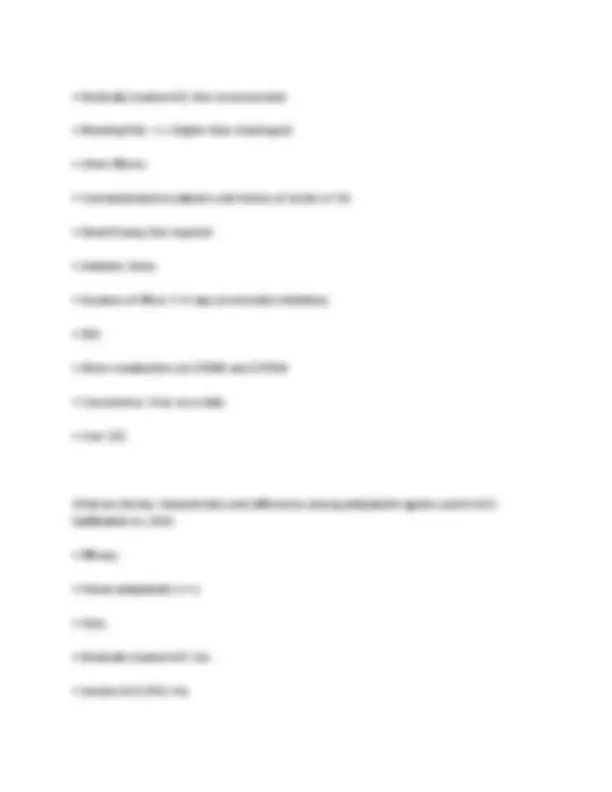
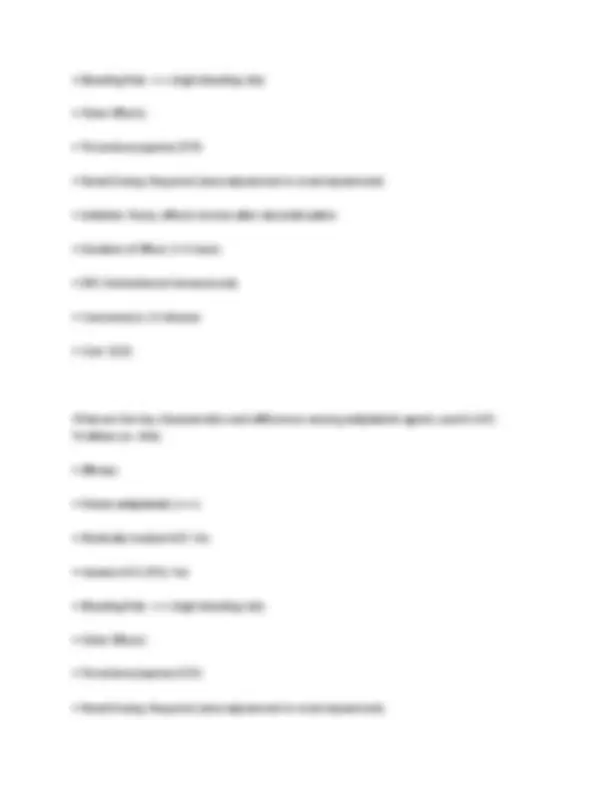
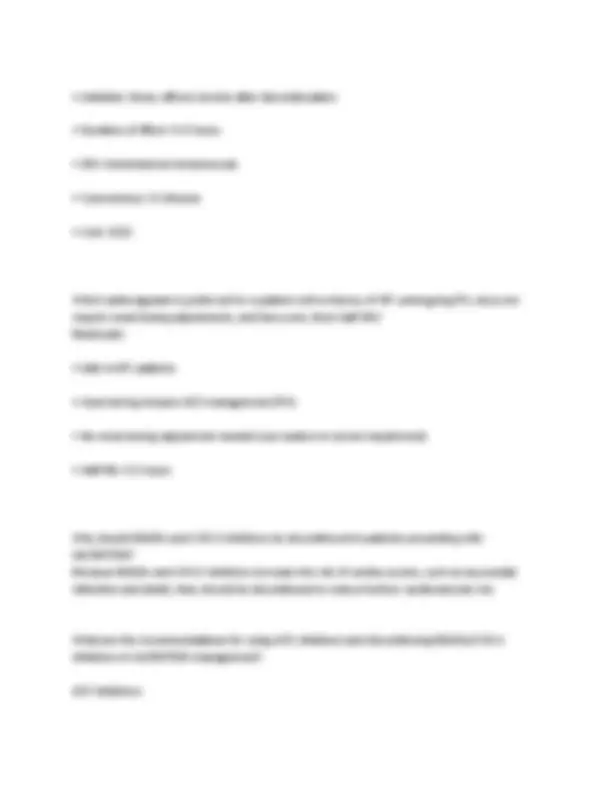
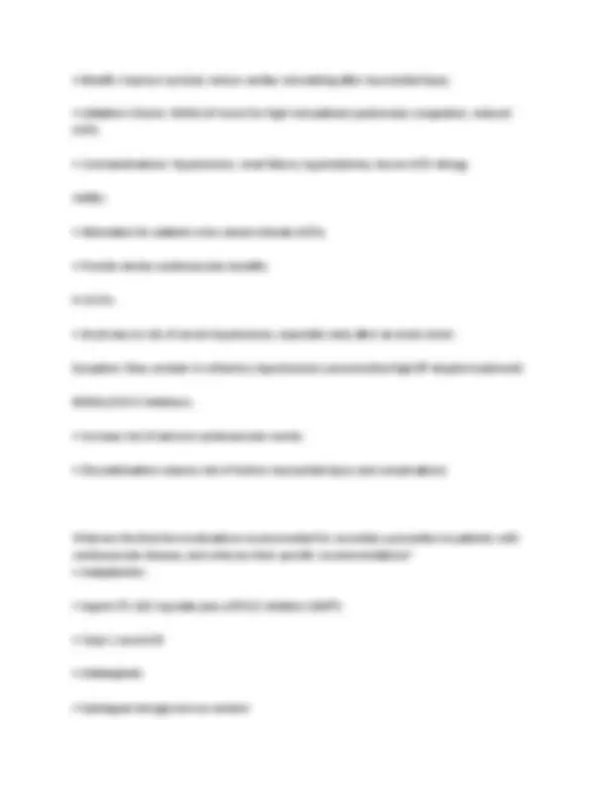
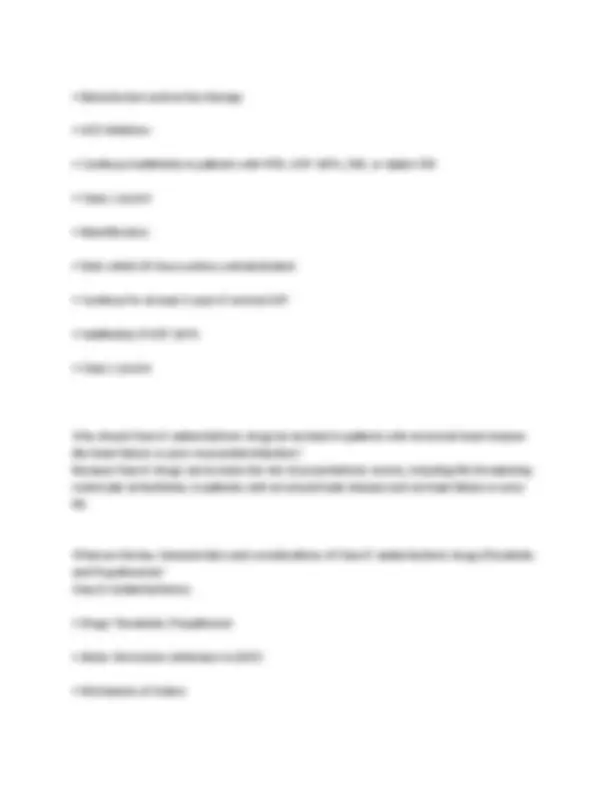
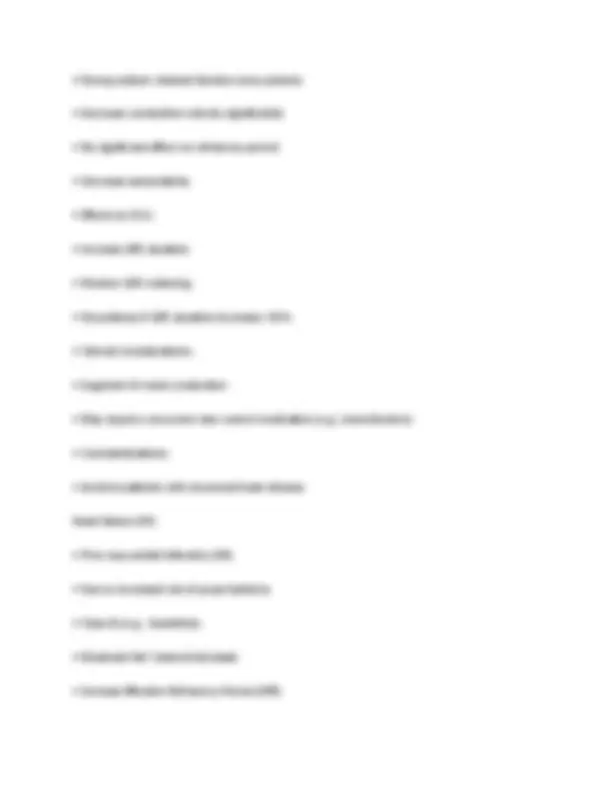

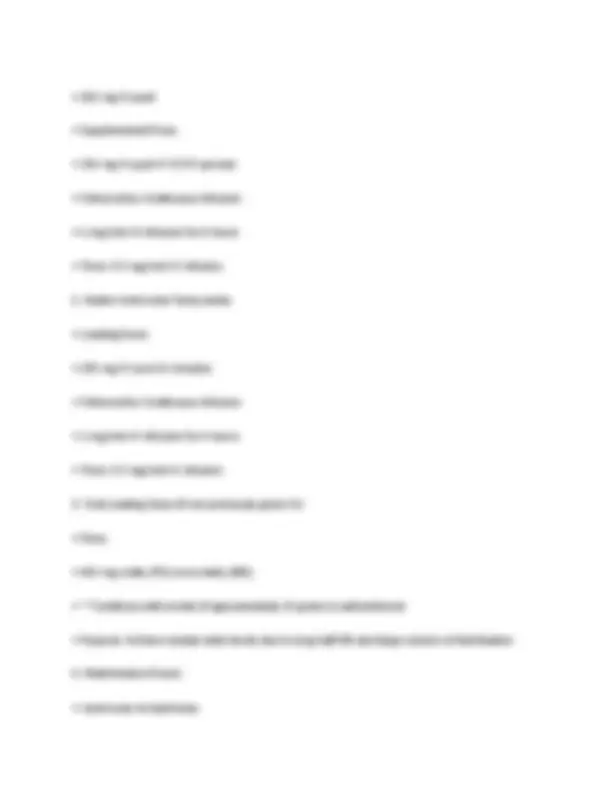
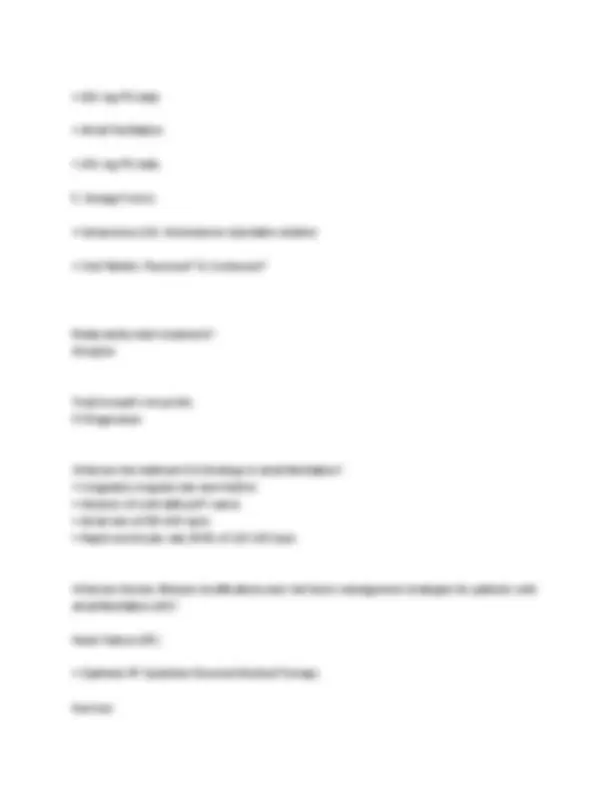
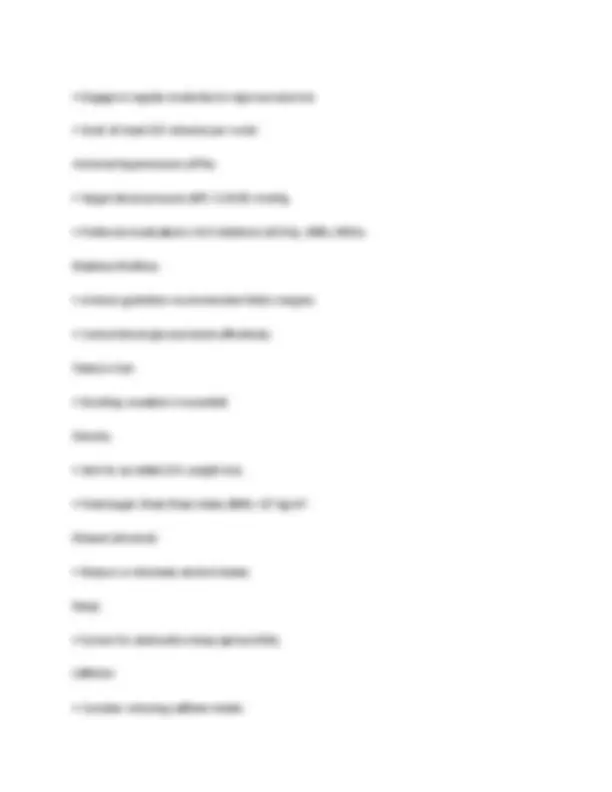
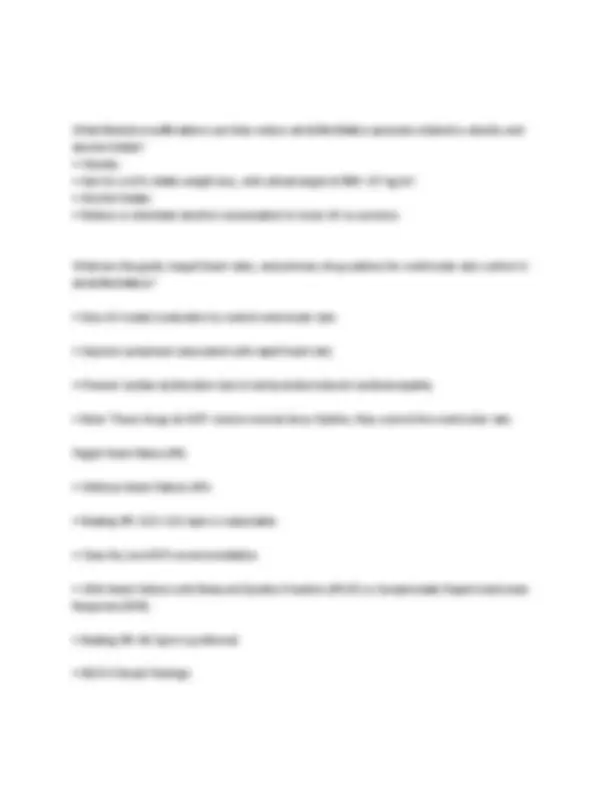

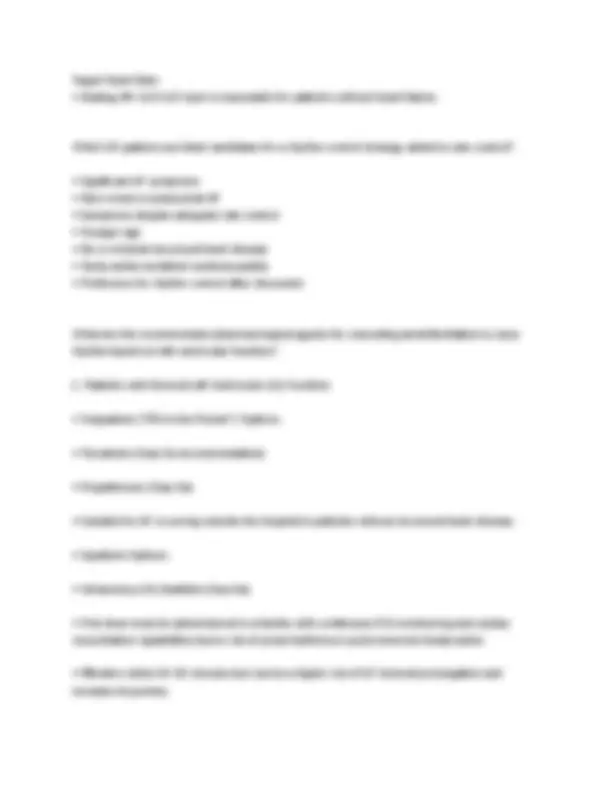
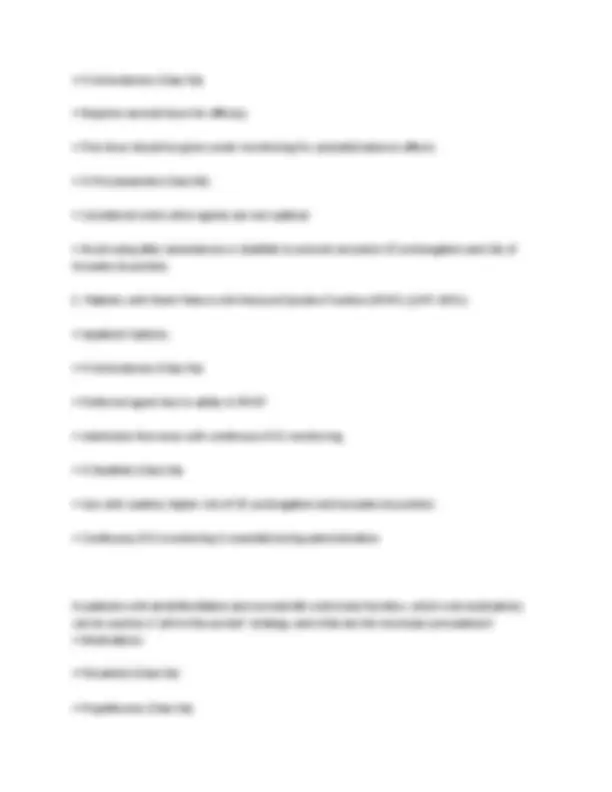
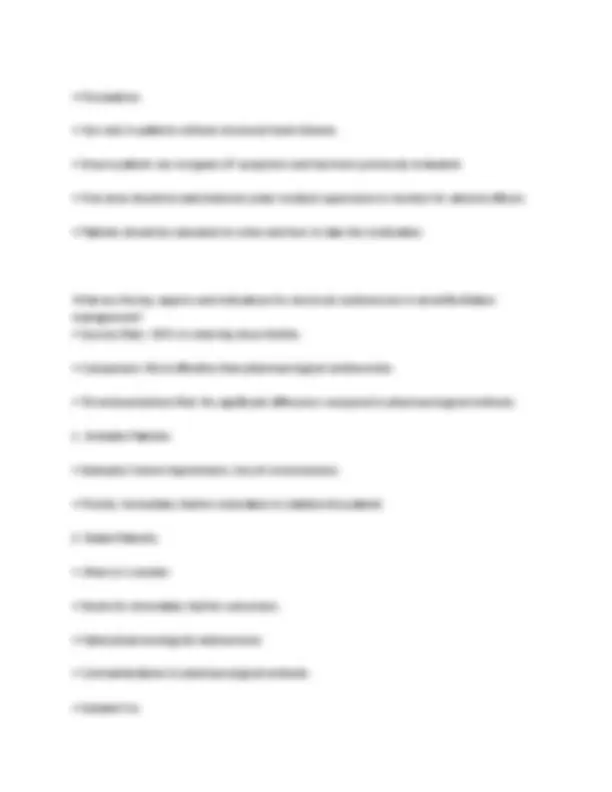
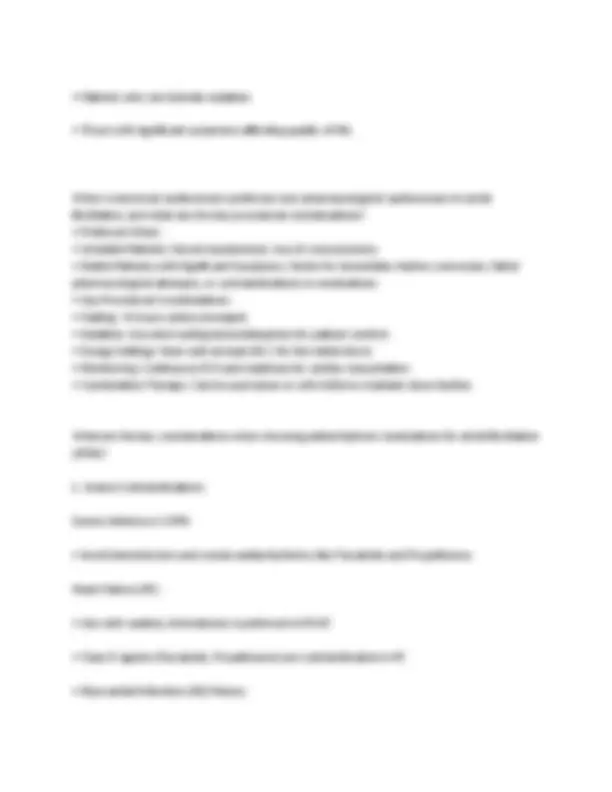
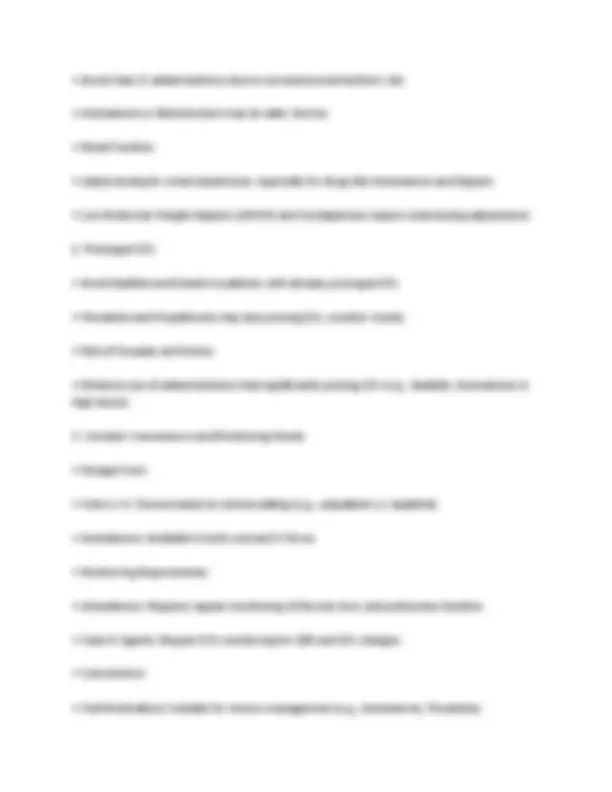
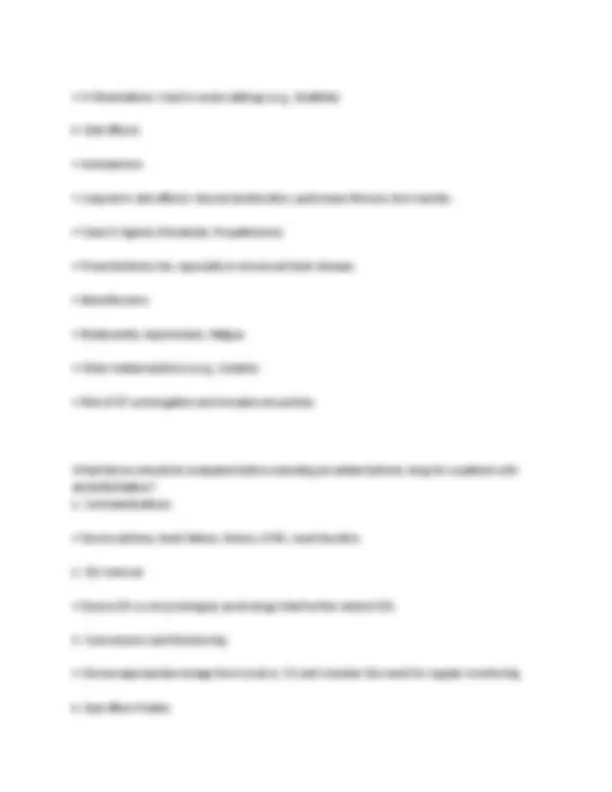
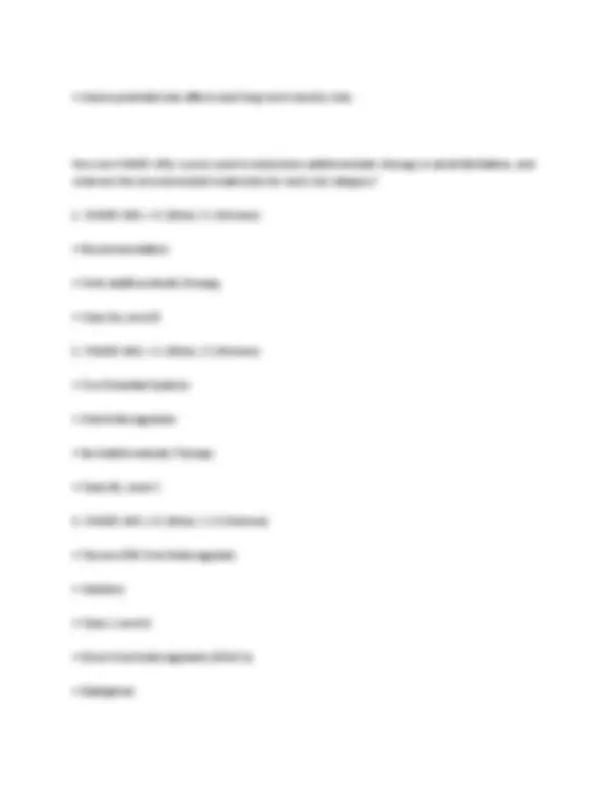
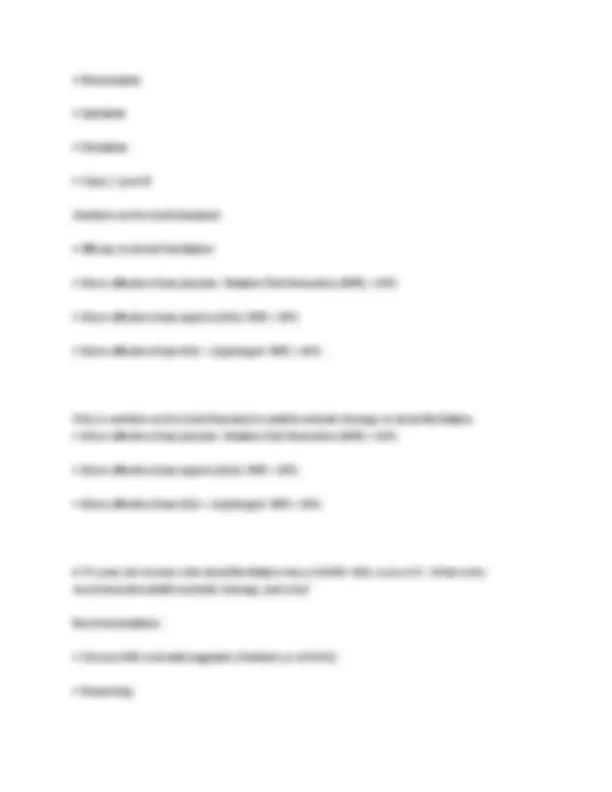
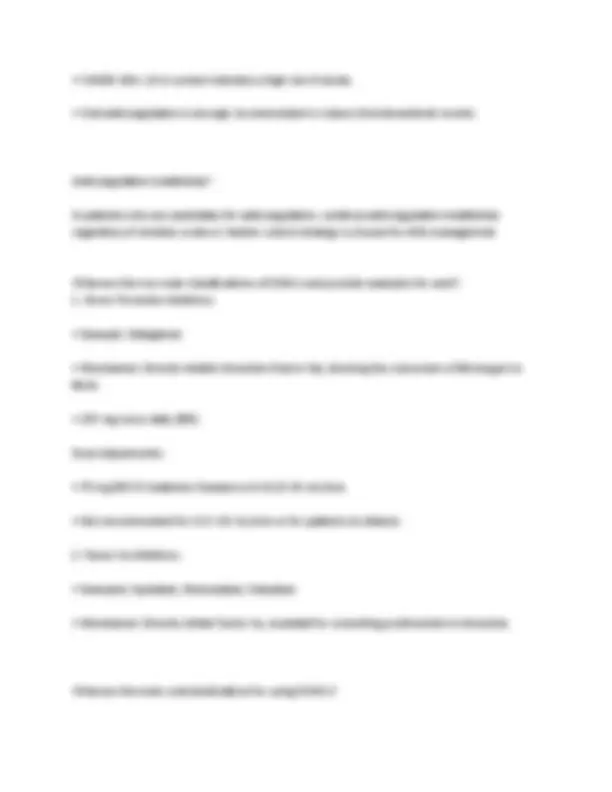
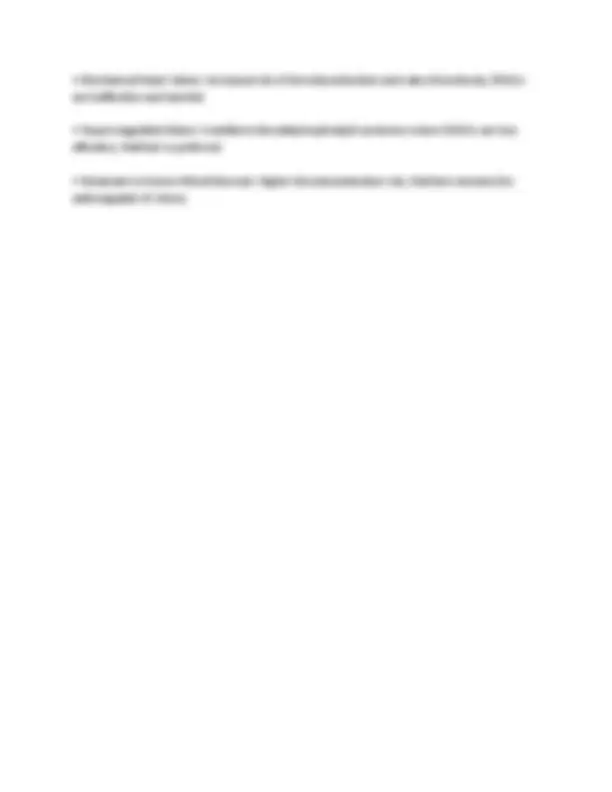
Study with the several resources on Docsity
Earn points by helping other students or get them with a premium plan
Prepare for your exams
Study with the several resources on Docsity
Earn points to download
Earn points by helping other students or get them with a premium plan
Community
Ask the community for help and clear up your study doubts
Discover the best universities in your country according to Docsity users
Free resources
Download our free guides on studying techniques, anxiety management strategies, and thesis advice from Docsity tutors
NURS6204 MIDTERM EXAM 2024 LATEST EXAM WITH RATIONALE CAPELLA UNIVERSITY ADVANCED HEALTH ASSESSMENT Quality -Perceived degree of excellence -meeting or exceeding customer expectations -dynamic - expectations can change -can be improved Reliability The measurable capability of a process, procedure, or health service to perform its intended function in the required time under commonly occurring conditions
Typology: Exams
1 / 81
This page cannot be seen from the preview
Don't miss anything!
Quality
ishikawa diagram/ fishbone diagram categories for causes
Value Stream
defines what the process is capable of delivering variation
Six Sigma - Set of tools
Types of errors
Run charts
Run table