


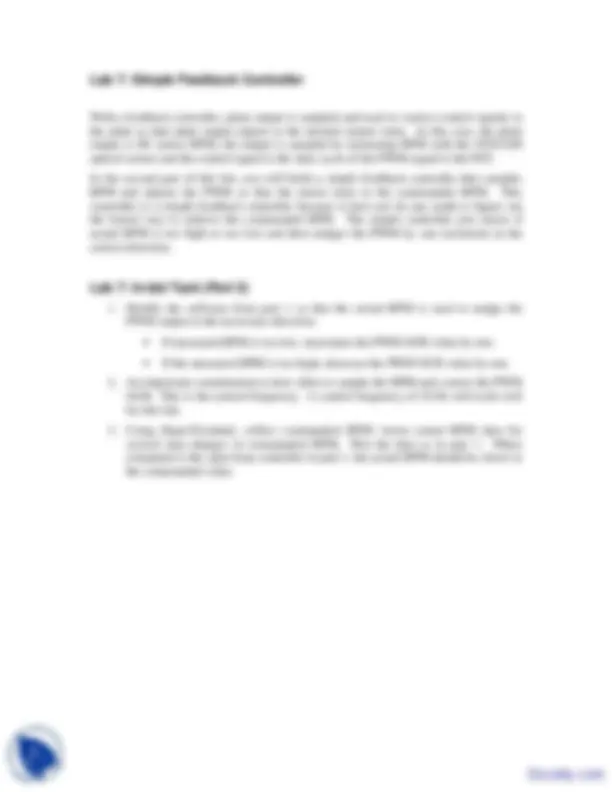
Study with the several resources on Docsity
Earn points by helping other students or get them with a premium plan
Prepare for your exams
Study with the several resources on Docsity
Earn points to download
Earn points by helping other students or get them with a premium plan
Community
Ask the community for help and clear up your study doubts
Discover the best universities in your country according to Docsity users
Free resources
Download our free guides on studying techniques, anxiety management strategies, and thesis advice from Docsity tutors
These are the Lecture Notes of Embedded System Design which includes Exceeded, Limit, Drive Slower, Larger Ticket, System Functions, Similar Principles, Basic Types Of Control Systems, Signals, Closed Loop etc. Key important points are: Motor Controller, Open Loop Control, Simple Feedback Loop Contorl, Proportional Feedback Control, Feedback Controller, Microprocessor, Output, Motor Spins, Disk or Paddle, Connected
Typology: Study notes
1 / 7
This page cannot be seen from the preview
Don't miss anything!
In most engineering applications, electric motors are controlled with some kind of feedback controller. In this lab, you will demonstrate why a feedback controller is better than an open loop controller. You will also build two kinds of feedback controllers to demonstrate why the PID variety is superior.
As you learned in lab 5, there are two kinds of control systems: open loop and closed loop. Your task in part 1 of this lab is to build an open loop DC motor controller.
The ‘plant’ to be controlled in this lab is a DC motor. The speed of the motor is controlled by a power FET. The signal to the gate of the FET is the PWM output of the microprocessor (μP). The greater the duty cycle of the PWM output, the faster the motor turns. The circuit is shown in figure 1 below.
A
VCC
5V
Q
PWM_Output
Figure 1 - DC Motor Speed Control with Power FET
The RPM of the DC motor is sensed with the NTE3100 optical sensor that was used in lab 3. The DC motor spins a disk or paddle that interrupts the IR beam between the LED and the sensor in the NTE3100. The NTE3100 is then connected as the clock source of a counter in the μP. Each rotation of the DC motor thus registers as a count. By reading the count periodically, the RPM of the motor is determined. The circuit for the RPM sensor is shown in figure 2. Note that the circuit uses the CD4050 buffer as discussed in lab 3.
ATMEGA
PA VTG 2.2K
NTE3100 20K
3 2 T (PB1)
CD
RXD To Computer Serial Port TXD
2
14 15
PA PA PA PA PA PA PA
40 39 38 37 36 35 34 33
SW SW SW SW SW SW SW SW
PC PC PC PC PC PC PC PC
22 23 24 25 26 27 28 29
LED LED LED LED LED LED LED LED OCR (PD7)
VTG
IRF
MotorDC
Figure 2 - DC Motor RPM Sensor
RPM Response - Open Loop Controller
0
2000
4000
6000
8000
10000
12000
14000
16000
18000
0 10 20 30 40 50 60 70 Time (s)
RPM
Commanded RPM Actual RPM
Figure 3 - Example Graph of Commanded RPM versus Actual RPM for an Open Loop Controller
With a feedback controller, plant output is sampled and used to correct control signals to the plant so that plant output adjusts to the desired output value. In this case, the plant output is DC motor RPM, the output is sampled by measuring RPM with the NTE optical sensor and the control signal is the duty cycle of the PWM signal to the FET.
In the second part of this lab, you will build a simple feedback controller that samples RPM and adjusts the PWM so that the motor turns at the commanded RPM. This controller is a simple feedback controller because it does not do any math to figure out the fastest way to achieve the commanded RPM. The simple controller just senses if actual RPM is too high or too low and then nudges the PWM by one increment in the correct direction.
Pre-Lab Questions Name: ______________________________
10 points total, 4 points for question 1 and 6 points for question 2.