
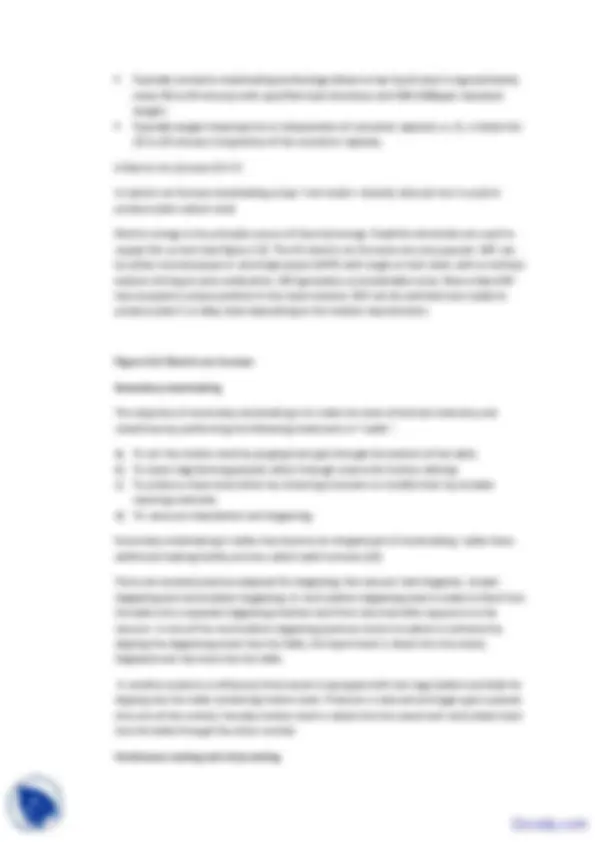
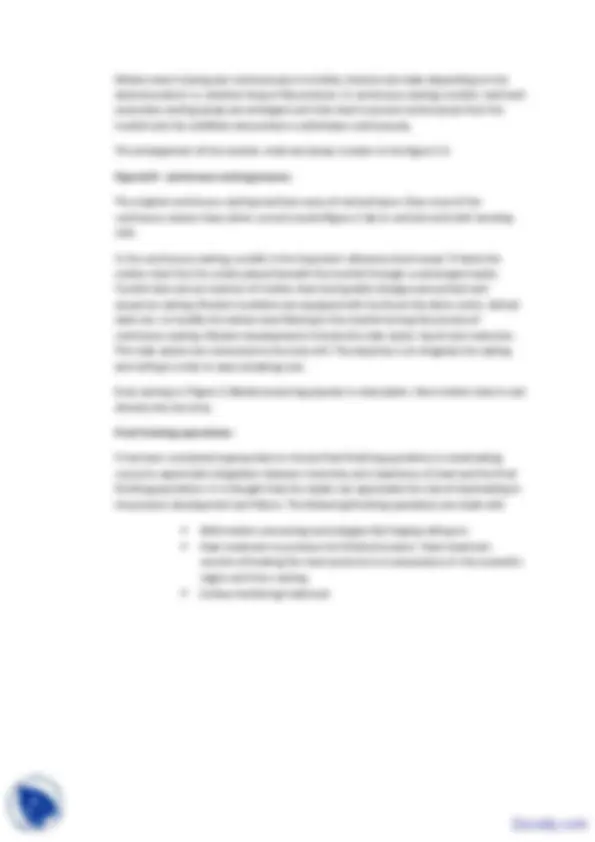
Study with the several resources on Docsity
Earn points by helping other students or get them with a premium plan
Prepare for your exams
Study with the several resources on Docsity
Earn points to download
Earn points by helping other students or get them with a premium plan
Community
Ask the community for help and clear up your study doubts
Discover the best universities in your country according to Docsity users
Free resources
Download our free guides on studying techniques, anxiety management strategies, and thesis advice from Docsity tutors
The major points which I found very informative are:Modeling of Steelmaking Processes, Physical Model, Fluid Flow in Steel Melt, Water Modeling, Tundish Metallurgic, Scale Factor, Model and Prototype, Inertia and Gravity Force, Froude Number, Reynold’s Number
Typology: Study notes
1 / 4
This page cannot be seen from the preview
Don't miss anything!
L 2 Modern steelmaking
Contents:
Concept
Primary steelmaking
Secondary steelmaking
Continuous casting and thin strip casting
Final finishing operations
Key words: Primary steelmaking, ladle metallurgy, ingot casting, continuous casting
Concept
The concept of modern steelmaking is to make use of the steelmaking vessels like converter, ladle
and tundish of a continuous caster. In all these vessels molten steel is handled for one or the other
purpose. For examples ladles are used to transfer the molten steel either to ingot casting or
continuous casting. Tundish of a continuous caster is used to transfer molten steel to the continuous
casting mould. In all these vessels the residence time of molten steel is sufficiently long so as to carry
out some refining operations like composition adjustment, removal of gases, control of S, removal of
inclusions etc. in ladle and tundish. This has led into the development of ladles, tundishes for some
refining operations like deoxidation, inclusion modification, desulphurization etc. and other
operations like composition adjustment, inclusion removal etc. The basic idea of employing ladles
and tundishes for either refining or composition adjustment or for producing clean steels is to use
the steelmaking units like converter and electric furnace for producing steels without much
bothering for final chemistry. Modern steelmaking comprises of hot metal / scrap to finished
products through the following
a) Primary steelmaking
b) Secondary steelmaking
c) Continuous casting
d) Finishing operations
Primary steelmaking
Primary steelmaking consists of refining of hot metal or scrap +hot metal to steel in a) converter and
b) Electric furnace. The objective is to refine hot metal to the nearly desired chemistry.
a) Types of converter steelmaking
with multi-hole nozzles. This technology of refining of hot metal is called top blown
steelmaking.
through the bottom. These are called combined top blowing and bottom stirred processes.
2
is blown from top and bottom and these processes are called top
and bottom blowing, Duplex blowing or hybrid blowing.
converter. This variant is not popular amongst steelmakers
Fig. 2.1 Types of converter steelmaking (a)Top blown steelmaking (b) Combined top and
bottom blowing, and (c) Bottom blowing
It is important to note that in all different types of converter steelmaking practices, a pear
shaped vessel is used and blast furnace hot metal is refined to plain carbon steel. Some amount
of scrap is also used.
Principle chemical reactions
Hot metal contains C ~ 3. 5 to 4 %, Si ~ 0. 6 to 1 %, Mn~ 0. 6 to 0. 8 % and P ~ 0. 1 to 0. 2 %.
Oxygen is blown from top and the following reactions occur:
[Fe] + [O] = (FeO) 1
[Si] + 2 [O] = (SiO
2
Mn
MnO
2
5
FeO
Fe
Fe
MnO
FeO
Mn
Note the following:
sufficient enough to raise the temperature of hot metal from around
1250 ℃ to 1300 ℃ to molten steel tapping temperature of 1600 ℃ to 1650 ℃.
Slag formation of desired chemistry and physico-chemical properties is vital for the
successful operation of converter steelmaking technology.
Molten steel is being cast continuously in to billets, blooms and slabs depending on the
desired product i.e. whether long or flat products. In continuous casting, tundish, mold and
secondary cooling sprays are arranged such that steel is poured continuously from the
tundish and the solidified cast product is withdrawn continuously.
The arrangement of the tundish, mold and spray is shown in the figure 2.3.
Figure2.3: continuous casting process.
The original continuous casting machines were of vertical types. Now most of the
continuous casters have either curved mould (Figure 2.3a) or vertical mold with bending
rolls.
In the continuous casting, tundish is the important refractory lined vessel. It feeds the
molten steel into the molds placed beneath the tundish through a submerged nozzle.
Tundish also acts as reservoir of molten steel during ladle change-over periods and
sequence casting. Modern tundishes are equipped with furniture like dams, weirs, slotted
dams etc. to modify the molten steel flowing in the tundish during the process of
continuous casting. Modern developments include thin slab caster, liquid core reduction.
Thin slab casters are connected to the strip mill. The objective is to integrate the casting
and rolling in order to save reheating cost.
Strip casting is ( Figure 2.3b)also becoming popular in steel plants. Here molten steel is cast
directly into the strip.
Final finishing operations:
It has been considered appropriate to include final finishing operations in steelmaking
course to appreciate integration between chemistry and cleanliness of steel and the final
finishing operations. It is thought that the reader can appreciate the role of steelmaking in
the product development and failure. The following finishing operations are dealt with
consists of heating the steel products to a temperature in the austenitic
region and then cooling.