
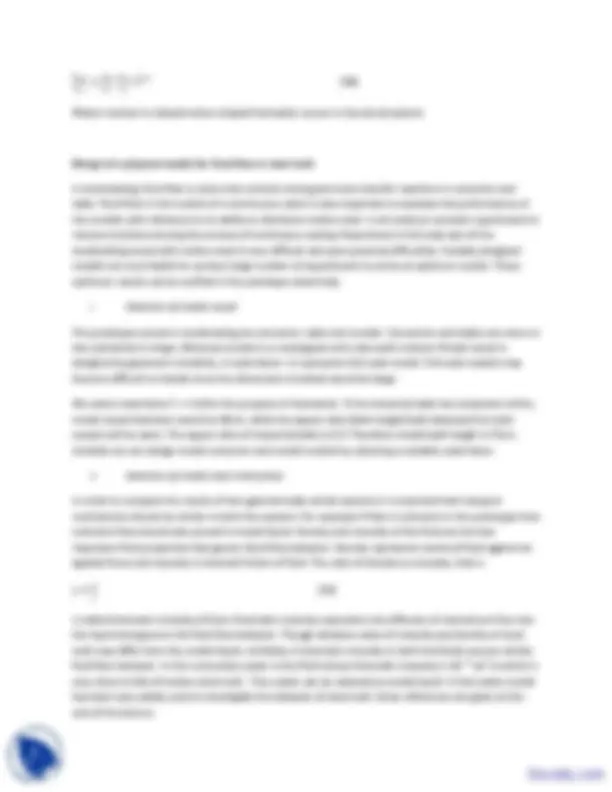
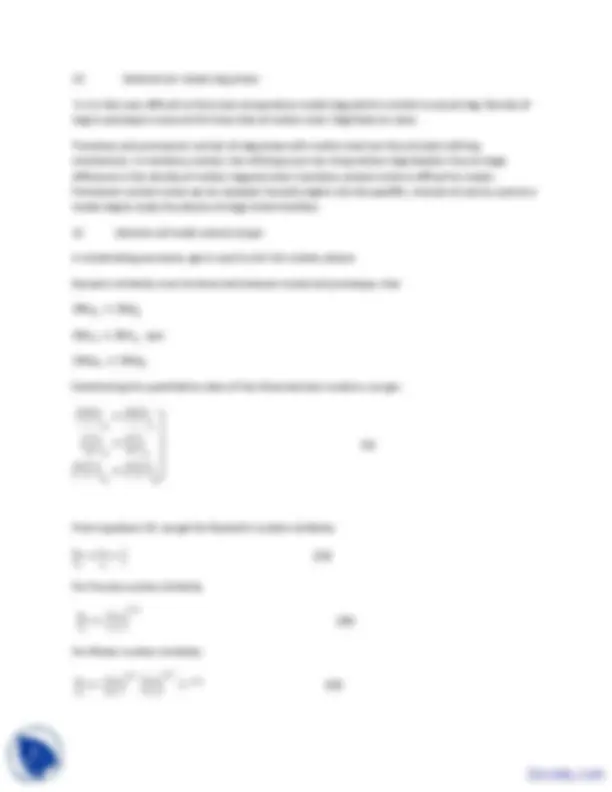
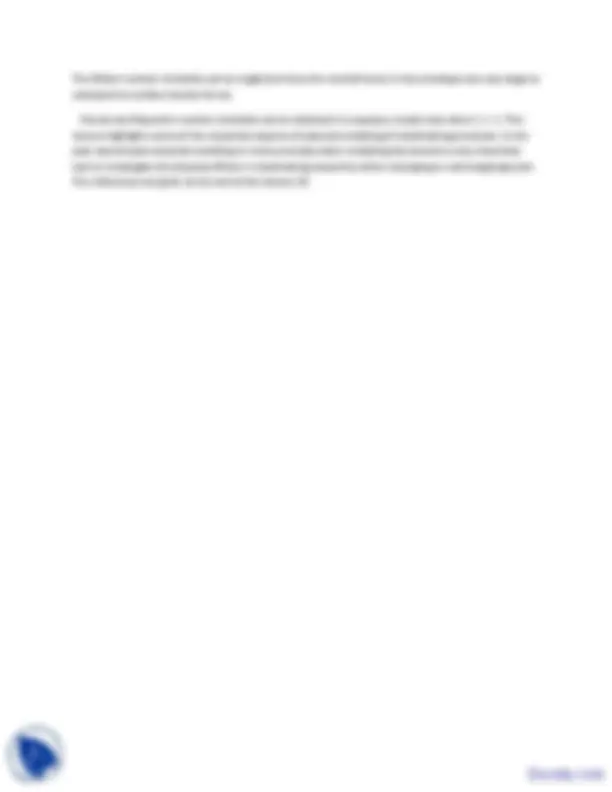
Study with the several resources on Docsity
Earn points by helping other students or get them with a premium plan
Prepare for your exams
Study with the several resources on Docsity
Earn points to download
Earn points by helping other students or get them with a premium plan
Community
Ask the community for help and clear up your study doubts
Discover the best universities in your country according to Docsity users
Free resources
Download our free guides on studying techniques, anxiety management strategies, and thesis advice from Docsity tutors
The major points which I found very informative are:Modeling of Steelmaking Processes, Physical Model, Fluid Flow in Steel Melt, Water Modeling, Tundish Metallurgic, Scale Factor, Model and Prototype, Inertia and Gravity Force, Froude Number, Reynold’s Number
Typology: Study notes
1 / 5
This page cannot be seen from the preview
Don't miss anything!
Lecture 38 Modeling of steelmaking processes
Contents
Introduction
Physical model
Design of a physical model for fluid flow in steel melt
Key words: Physical modeling, water modeling, tundish metallurgic
Introduction
With the globalization, steel market has become competitive both with respect to quality and cost of
steel. Steel industry is required to produce quality steel at a reasonable cost so that it remains
competitive with the world market. For this purpose constant and continuous efforts are required to
introduce either new steelmaking technology or to improve the process technologies in the existing
steel processing vessels like converter, ladle, continuous casting tundish and mold. In order to meet
these objectives, a sustainable research and development activities must be carried out in the plant to
address the quality issues in the steel product and then to introduce changes in the steel processing line,
that is product- process integration approach. One of the research tools is to design the model of the
actual process (here after we call proto type) so that specific studies can be made. The results of these
studies can then be implemented for the desired objectives. A model of the process can either be
physical or mathematical. The present lecture deals with some issue related to design of physical models
of steelmaking processes.
Physical model
In physical modeling, the model reactor and experiments are designed based on the similarity criteria
between the prototype and model. Both, model and prototype, must be similar geometrically,
dynamically, chemically and thermally.
Two systems are said to be geometrically similar when for every point in the model, there exists a
corresponding point in the prototype. This can be achieved by maintaining a constant ratio between the
linear dimensions of the systems. This is called scale factor λ.
λ =
D m
D p
L m
L p
The above relation suggests that two systems following the geometrical similarly should have the same
aspect ratio of the vessel. The value of scale factor indicates how big or small model would be. For
example, a scale factor of 0.2 means that diameter of the model cylindrical vessel is 1 ⁄ 5 of the diameter
of the actual vessel, if the actual vessel is cylindrical in shape. For a rectangular vessel all the linear
dimensions of the model vessel are 1/5 of the actual ones.
Dynamic similarity requires that the corresponding forces acting at corresponding time and location
must bear the same ratio between the model and the prototype. In steelmaking the inertial, viscous and
surface tension forces are of relevance. The ratio between inertial and viscous force is called Reynold’s
number
Re =
inertial force
viscous force
ρ uL
μ
uL
γ
Where u is velocity, L is characteristic linear dimension and γ is kinematic viscosity. Reynold’s number
characterize the type of flow, that is whether laminar or turbulent.
The ratio between inertia and gravity force is Froude number (Fr)
Fr
u
2
gL
Modified Froude number 𝐹𝐹𝐹𝐹
1
is more relevant than simple Froude number
Fr
1
ρ
g
u
2
�ρ l
−ρ g
�gL
aerodynamic force
gravitational force
ρ
g
is the density of gas and 𝜌𝜌
𝑙𝑙
is density of liquid. Froude number determines the importance of
aerodynamics force and gravitational force when gas jet either impinges the bath or submerged into the
bath. Froude number similarity is very important to model the chemically active or inert gas injection in
steelmaking processes.
Weber number (We) is the ratio of aerodynamic to surface tension force
We =
ρu
2
L
σ
σ is surface tension of liquid. The dynamic similarity requires
Re m
= Re
p
Fr
m
= Fr
p
or Fr
m
1
= Fr
p
1
and (6)
We m
= We
p
The similarity in Reynold’s number requires that,
u om
u op
γ m
γ p
1
λ
The subscript m denotes model and p denotes prototype. The similarity in Froude number requires that.
u om
u op
= λ
And Weber number requires that,
iii) Selection for model slag phase
It is in fact very difficult to find a low temperature model slag which is similar to actual slag. Density of
slag in prototype is around 0.4 times that of molten steel. Slag floats on steel.
Transitory and permanent contact of slag phase with molten steel are the principle refining
mechanisms. In transitory contact, the refining occurs by rising molten slag droplets. Due to large
difference in the density of molten slag and steel, transitory contact mode is difficult to model.
Permanent contact mode can be modeled. Several organic oils like paraffin, mineral oil can be used as a
model slag to study the physics of slag/ metal interface.
iv) Selection of model velocity of gas
In steelmaking processes, gas is used to stirr the molten phases
Dynamic similarity must be observed between model and prototype, that
(Re)
m
= (Re)
p
Fr
m
Fr
m
and
(We) m
= (We)
p
Substituting the quantitative value of the dimensionless numbers, we get.
ρuL
μ
m
ρuL
μ
p
u
2
gL
m
u
2
gL
p
ρu
2
L
σ
m
ρu
2
L
σ
p ⎭
From equations 12 we get for Reynold’s number similarity
u m
u p
γ m
γ p
1
λ
For Froude number similarity
u
m
u
p
σ
m
σ
p
For Weber number similarity
u m
u p
ρ p
ρ m
σ m
σ p
λ
− 0. 5
The Weber number similarity can be neglected since the inertial forces in the prototype are very large as
compared to surface tension forces.
Froude and Reynold’s number similarity can be obtained in a aqueous model only when λ = 1. This
lecture highlights some of the important aspects of physical modeling of steelmaking processes. In the
past several years physical modeling or more precisely water modeling has become a very important
tool to investigate the physical effects in steelmaking caused by either impinging or submerged gas jets.
The references are given at the end of the lecture 39.