
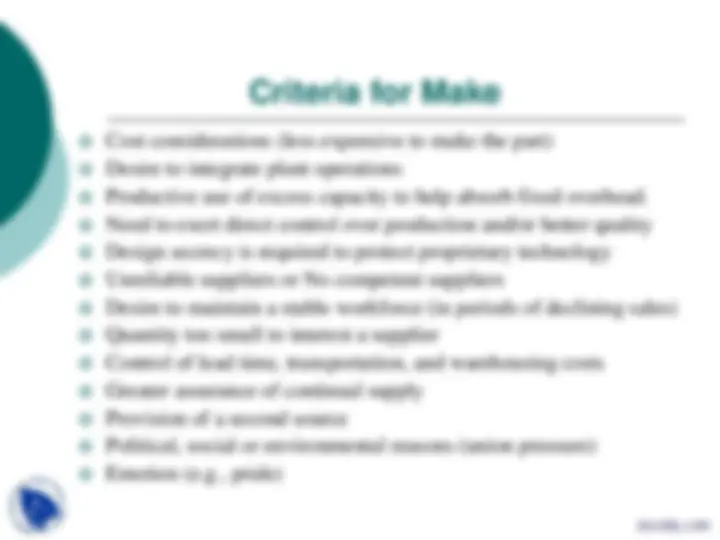
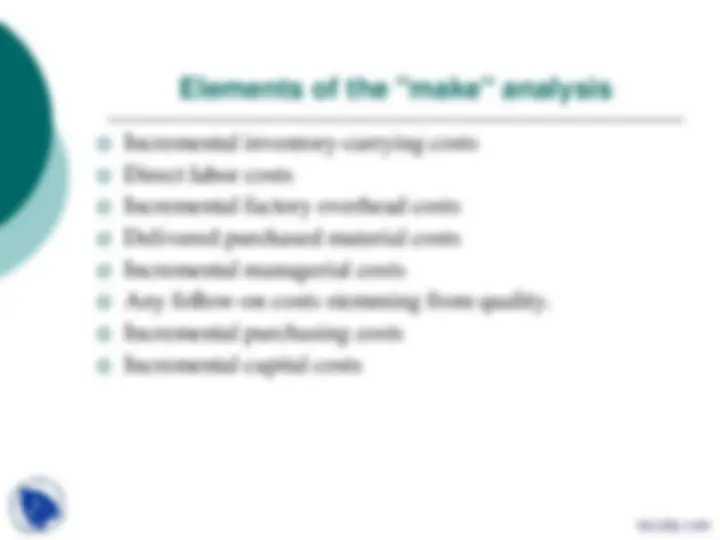
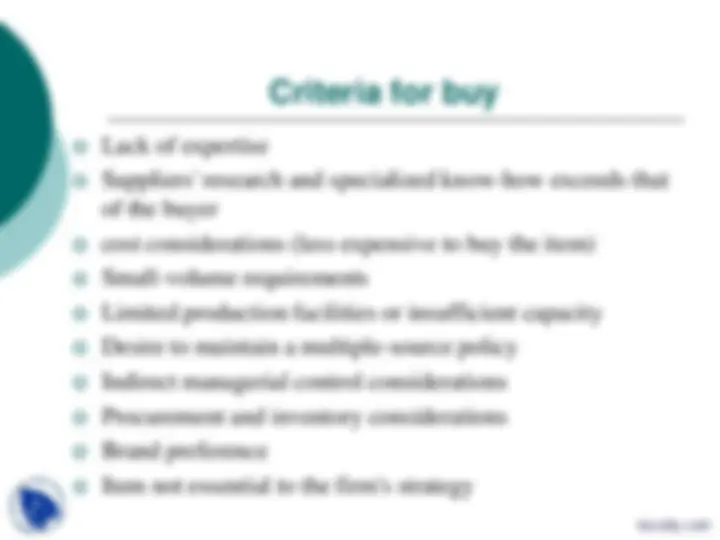
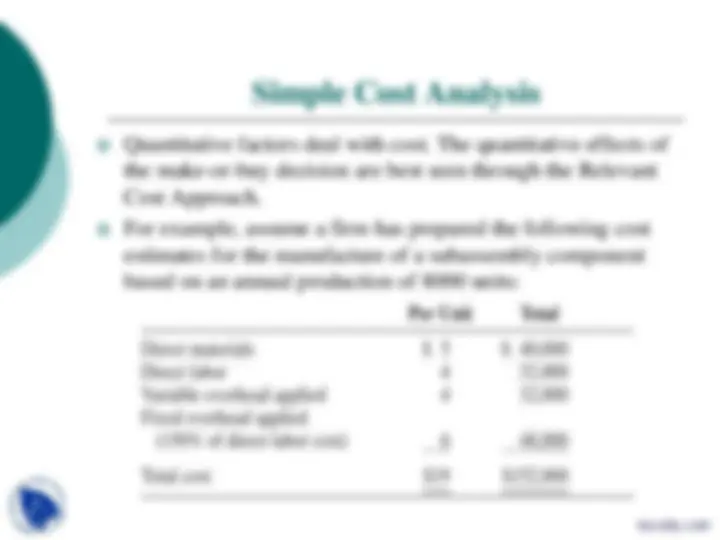
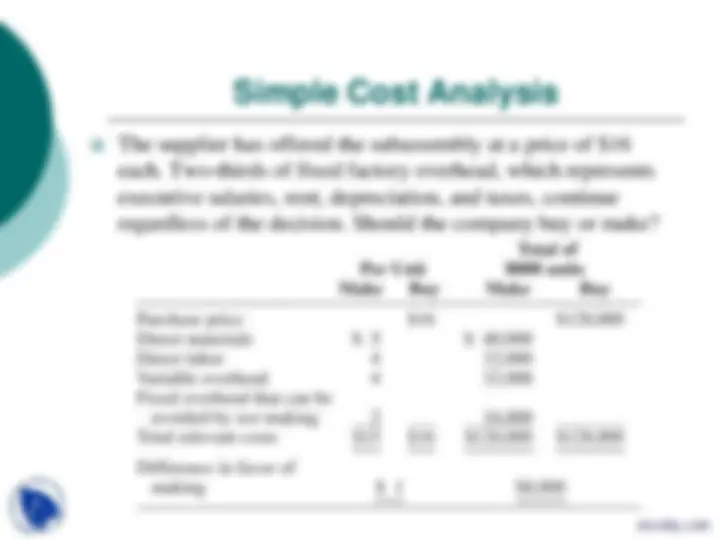
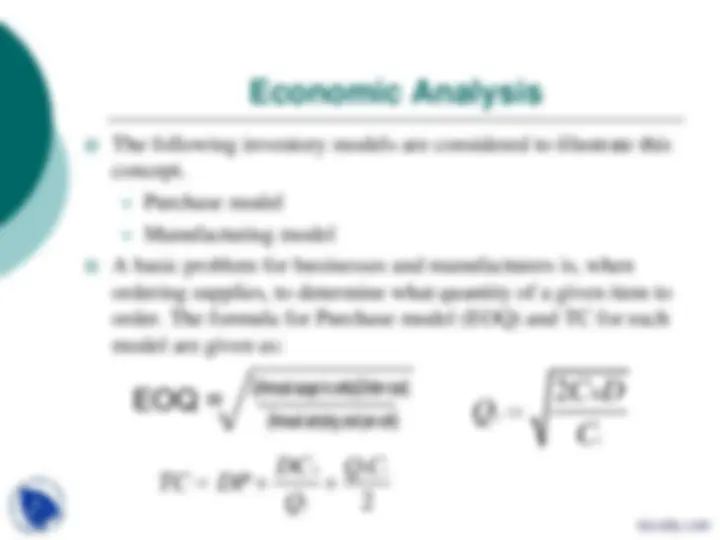
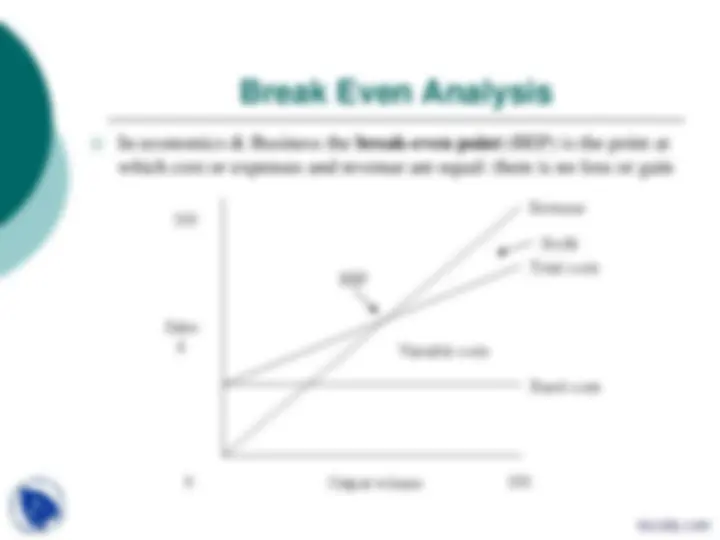
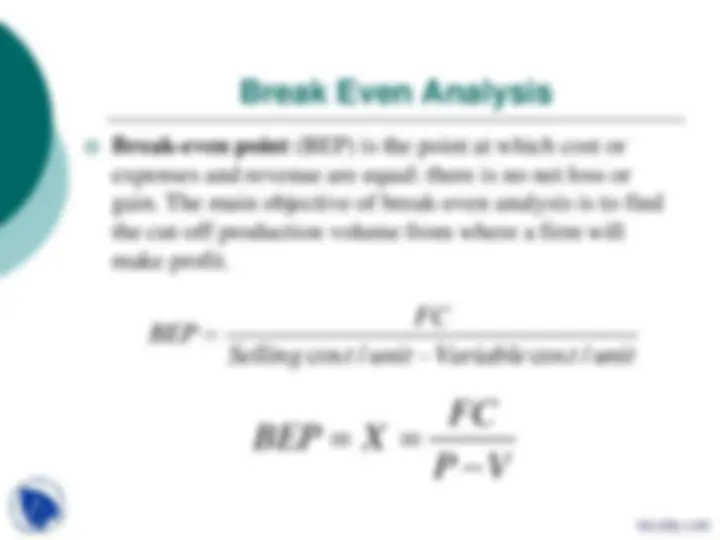
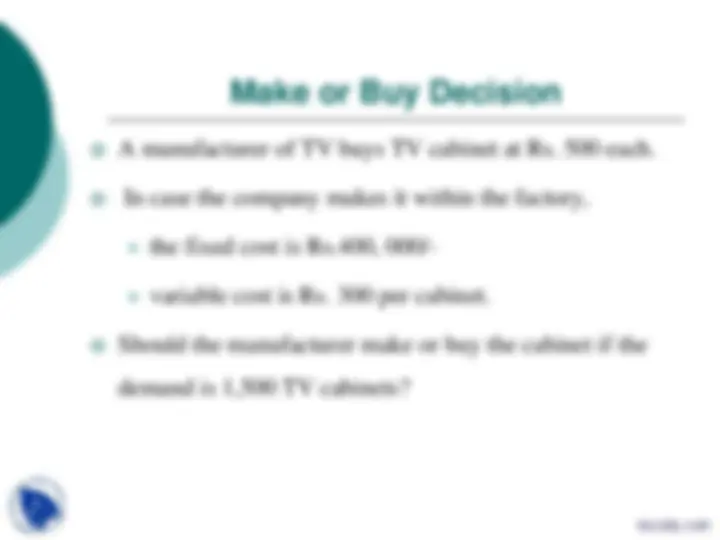
Study with the several resources on Docsity
Earn points by helping other students or get them with a premium plan
Prepare for your exams
Study with the several resources on Docsity
Earn points to download
Earn points by helping other students or get them with a premium plan
Community
Ask the community for help and clear up your study doubts
Discover the best universities in your country according to Docsity users
Free resources
Download our free guides on studying techniques, anxiety management strategies, and thesis advice from Docsity tutors
This lecture is part of lecture series for Engineering Economics course at M. J. P. Rohilkhand University. It was delivered by Dr. Badrinath Singh to cover following points: Supply, Demand, Market, Welfare, Consumers, Producers, Efficiency, Equilibrium, Consumer, Surplus
Typology: Slides
1 / 16
This page cannot be seen from the preview
Don't miss anything!
Introduction
Determination of whether it is more advantageous to make a particular item in house or to buy it from a supplier.
The choice involves both qualitative (such as quality control) and quantitative (such as the relative cost) factors.
The buy side of the decision also is referred to as outsourcing.
Make-or-buy decisions usually arise when a firm that has developed a product or part—or significantly modified a product or part—is having trouble with current suppliers, or has diminishing capacity or changing demand.
Issues like government regulation, competing firms, and market trends all have a strategic impact on the make-or- buy decision.
Incremental inventory-carrying costs
Direct labor costs
Incremental factory overhead costs
Delivered purchased material costs
Incremental managerial costs
Any follow-on costs stemming from quality.
Incremental purchasing costs
Incremental capital costs
Lack of expertise
Suppliers' research and specialized know-how exceeds that
of the buyer
cost considerations (less expensive to buy the item)
Small-volume requirements
Limited production facilities or insufficient capacity
Desire to maintain a multiple-source policy
Indirect managerial control considerations
Procurement and inventory considerations
Brand preference
Item not essential to the firm's strategy
Criteria for buy
Types of analysis followed in make or buy decision are as
follows: Simple cost analysis Economic cost analysis Break even analysis
Simple Cost Analysis
Quantitative factors deal with cost. The quantitative effects of the make-or-buy decision are best seen through the Relevant Cost Approach.
For example, assume a firm has prepared the following cost estimates for the manufacture of a subassembly component based on an annual production of 8000 units:
Economic Analysis
The following inventory models are considered to illustrate this concept. Purchase model Manufacturing model
A basic problem for businesses and manufacturers is, when ordering supplies, to determine what quantity of a given item to order. The formula for Purchase model (EOQ) and TC for each model are given as:
1
2 0
c
C D Q C
0 1
Manufacturing model
Economic Analysis
2
2 0 c (1 / )
C D Q C r k
0 2 2
( ) 2
c
DC Q TC DP C k r Q k
Break Even Analysis
In economics & Business the break-even point (BEP) is the point at which cost or expenses and revenue are equal: there is no loss or gain
Break Even Analysis
Break-even point (BEP) is the point at which cost or
expenses and revenue are equal: there is no net loss or gain. The main objective of break-even analysis is to find the cut-off production volume from where a firm will make profit.
cos / cos /
FC BEP Selling t unit Variable t unit
FC BEP X P V
There are three alternatives available to meet the demand
of a particular product. The details are as follows:
Make or Buy Decision
Cost Manufacturing by using process A
Manufacturing by using process A
Buy
FC/yr 5,00,000 6,00,
VC/unit 175 150
Pur. price 125
The annual demand of a product is 8,000. should the company make the product using process A or process B or buy it?