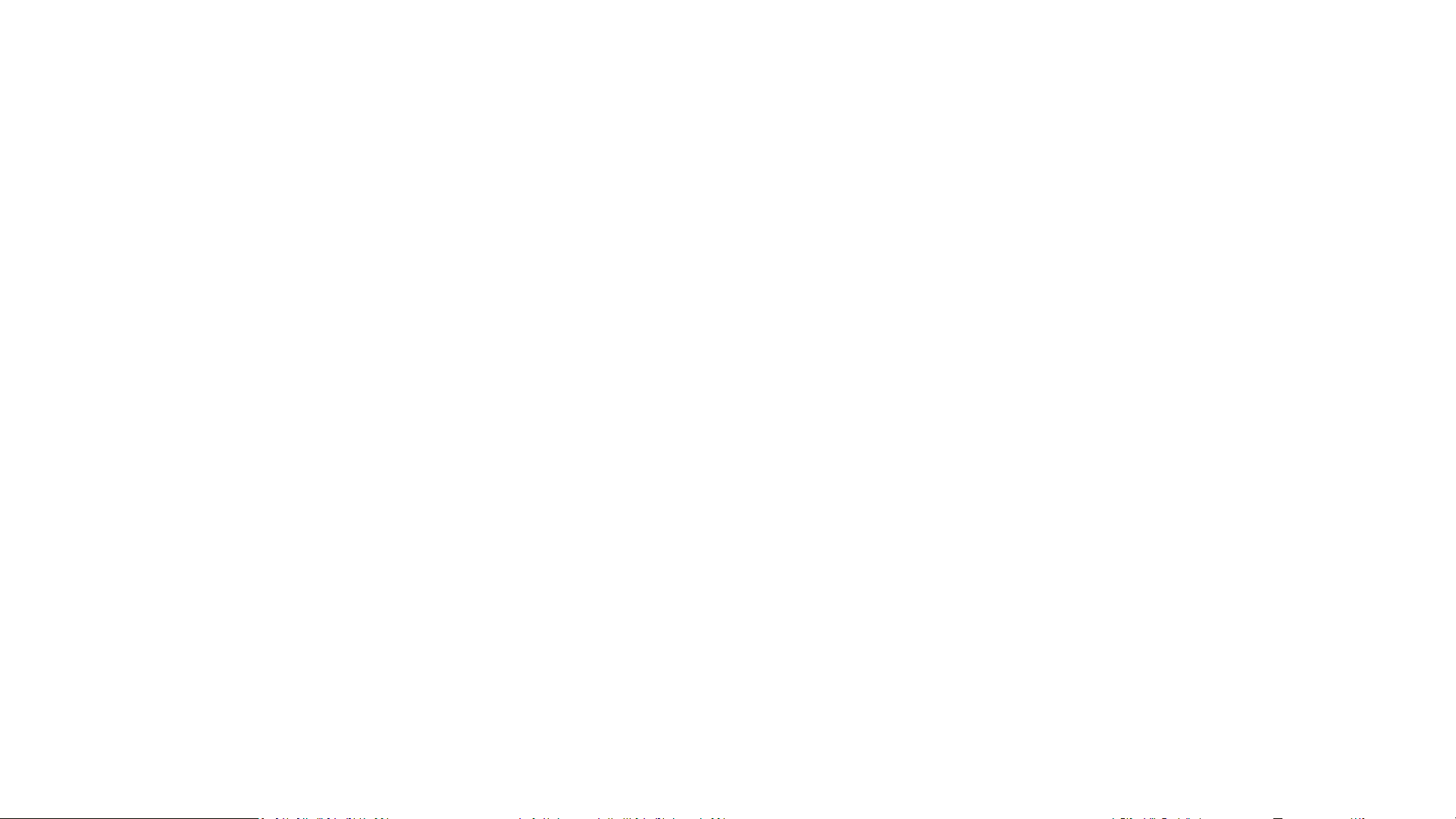
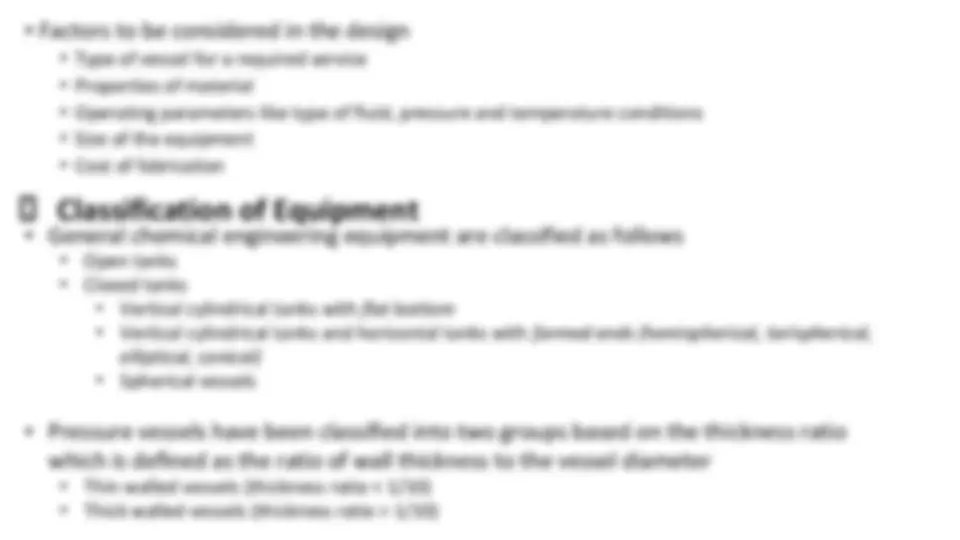
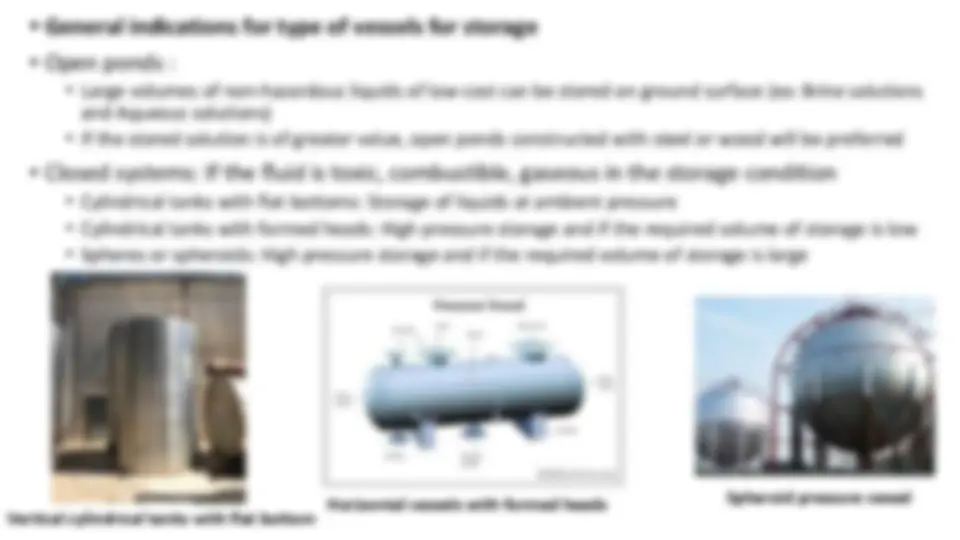
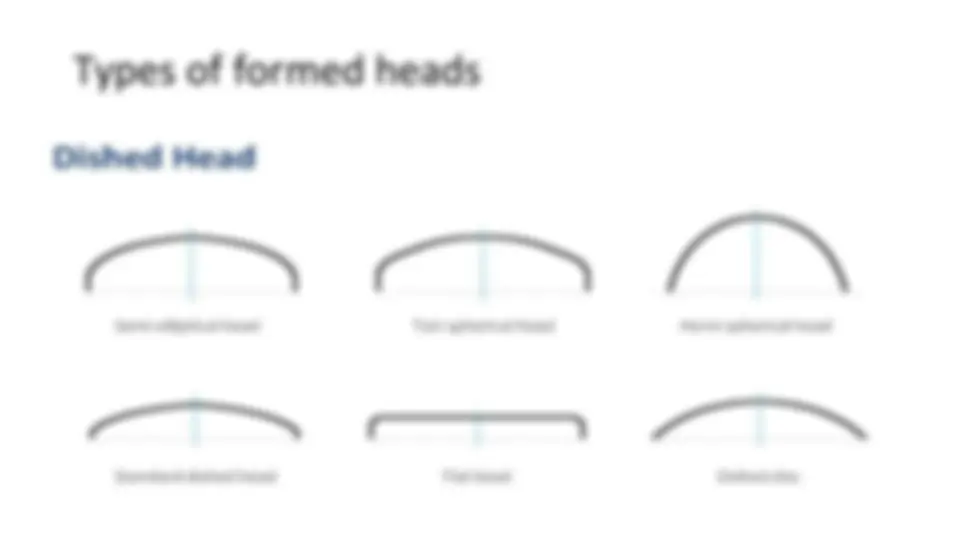
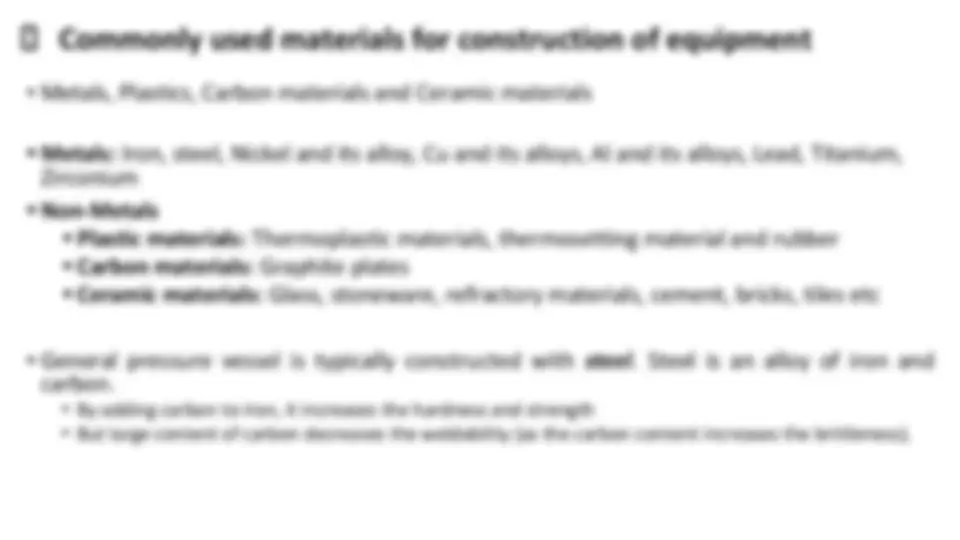
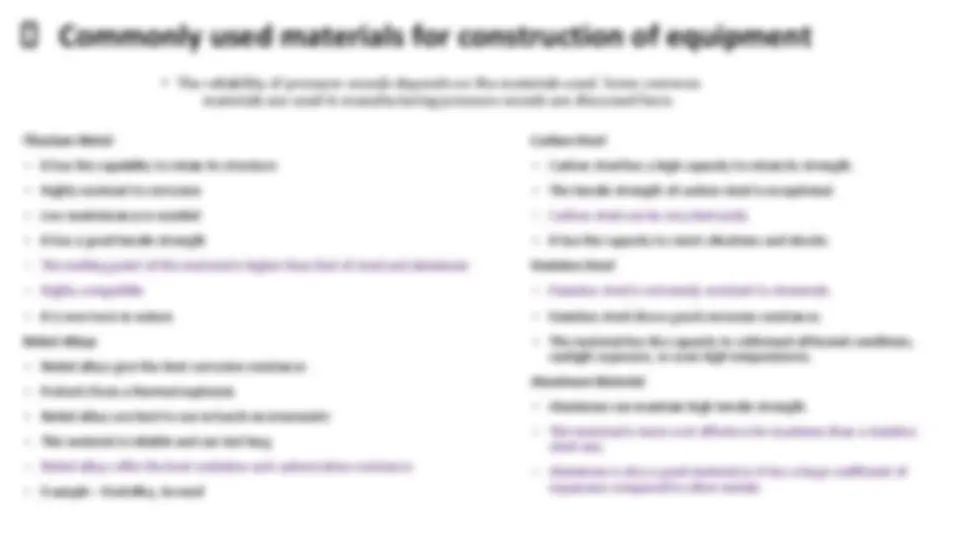
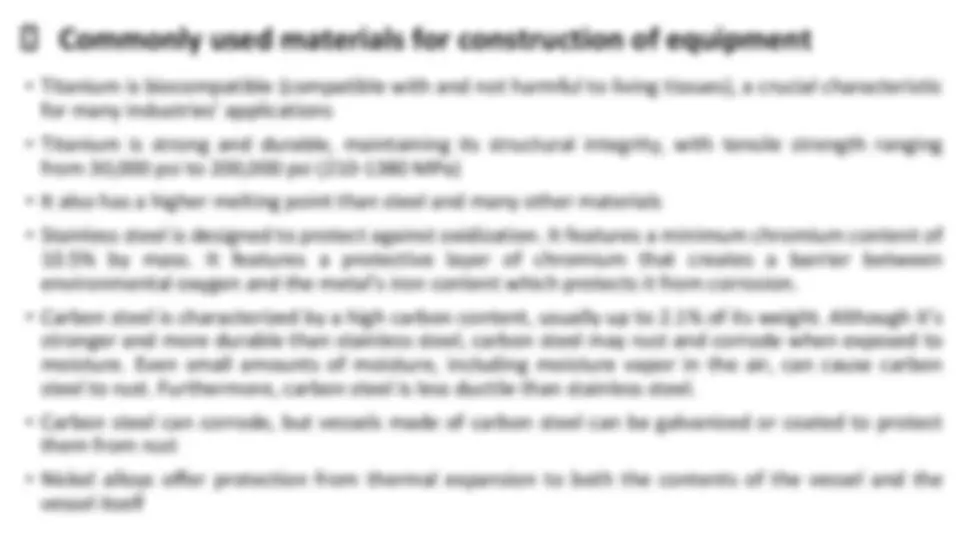
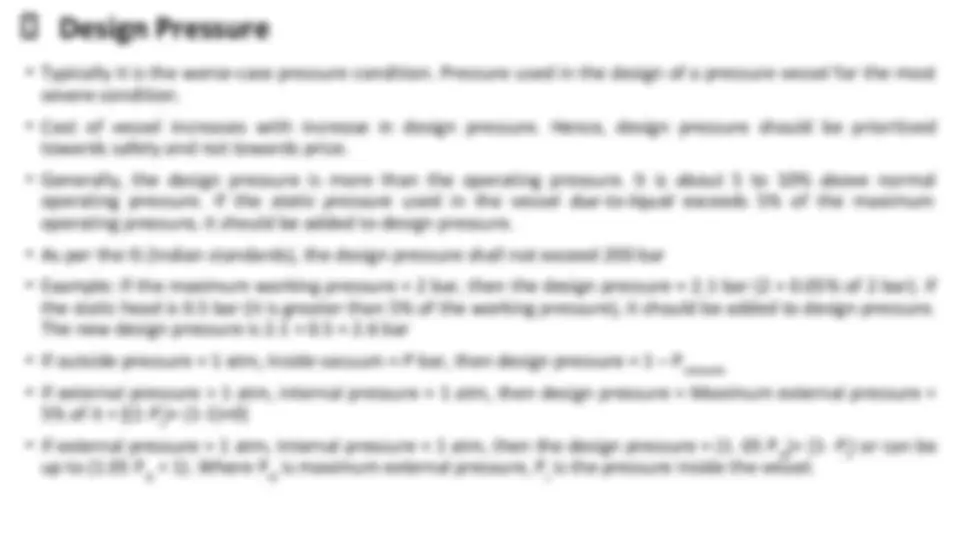
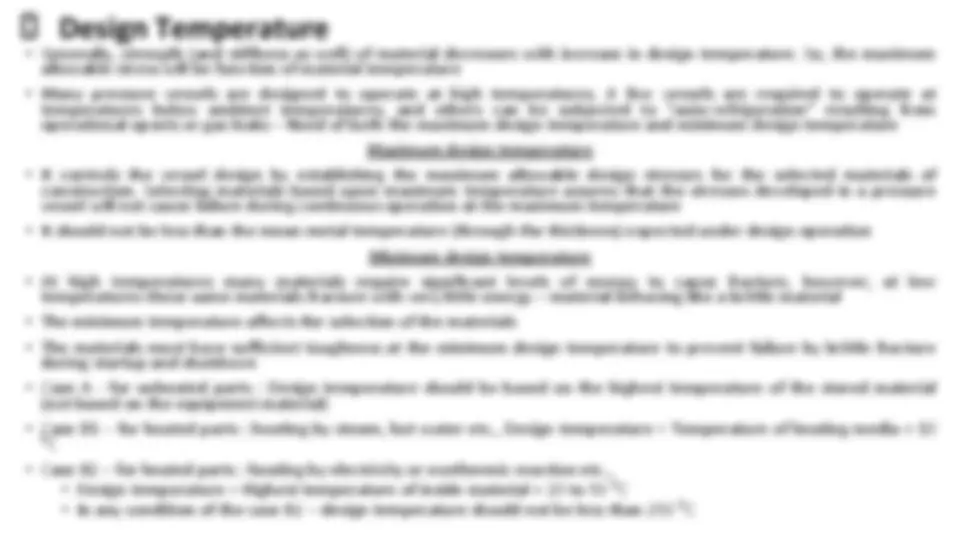
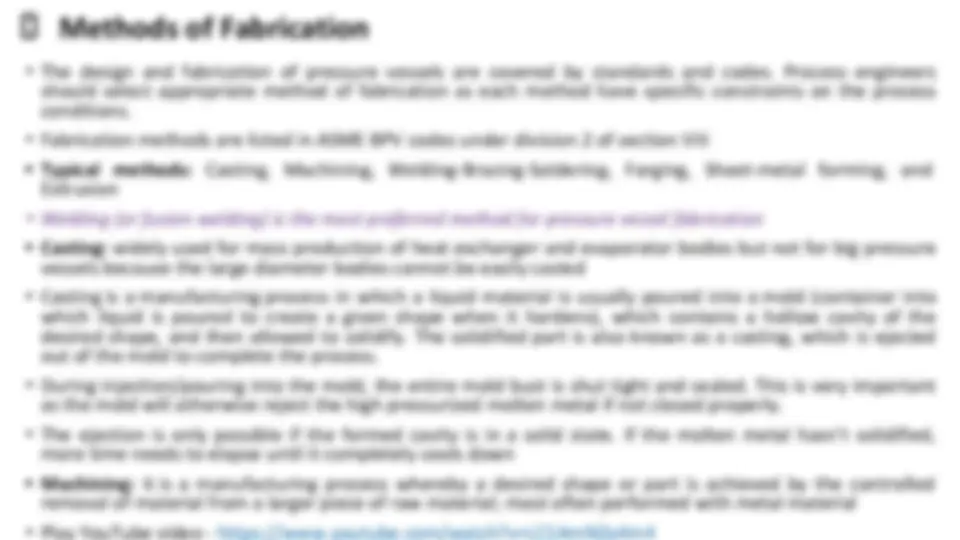
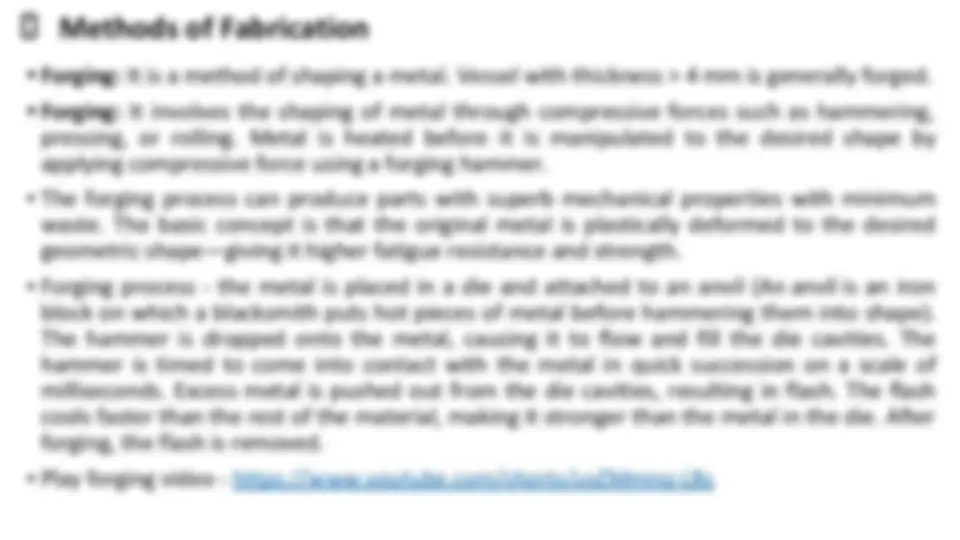
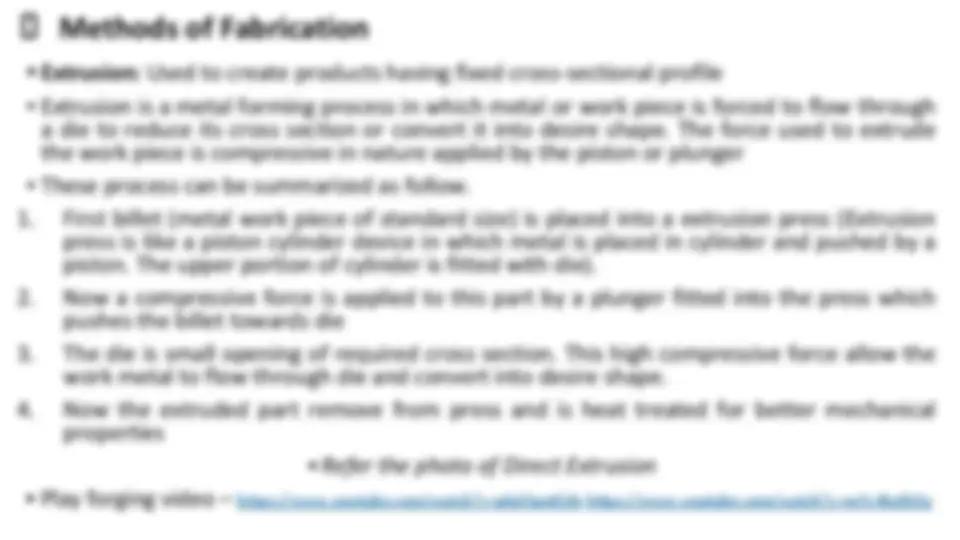
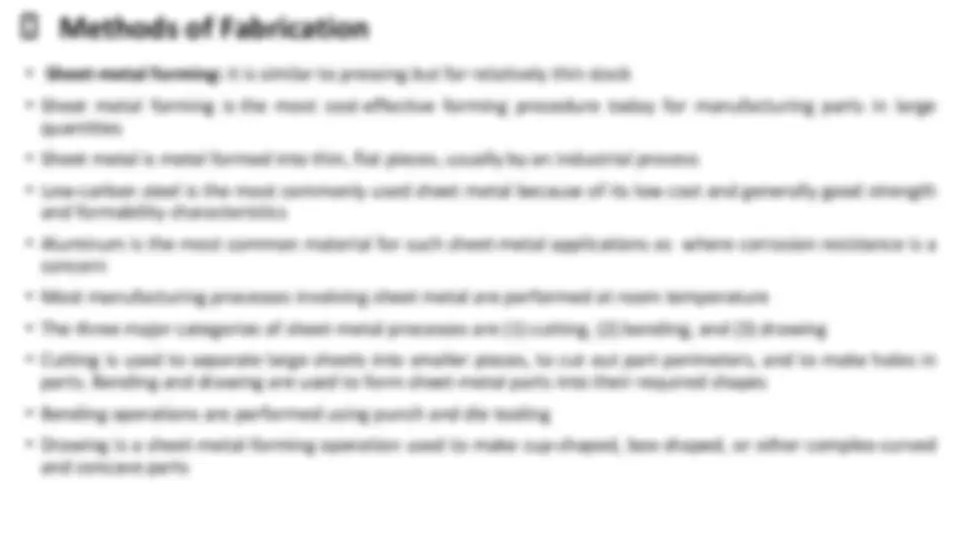
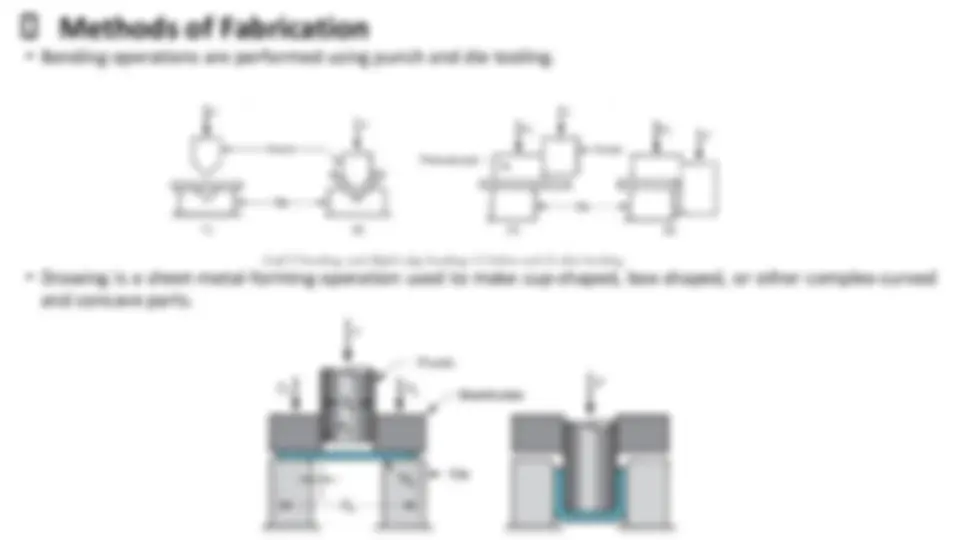
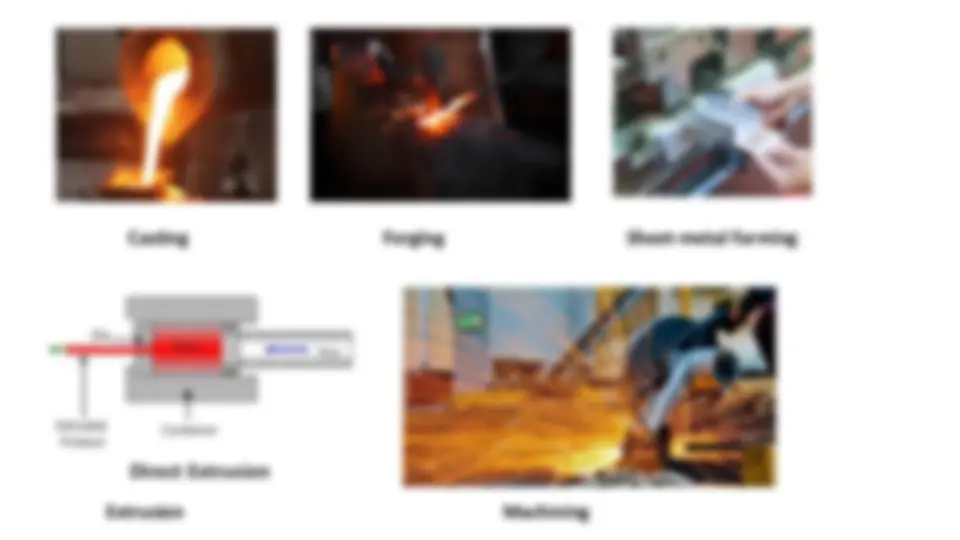
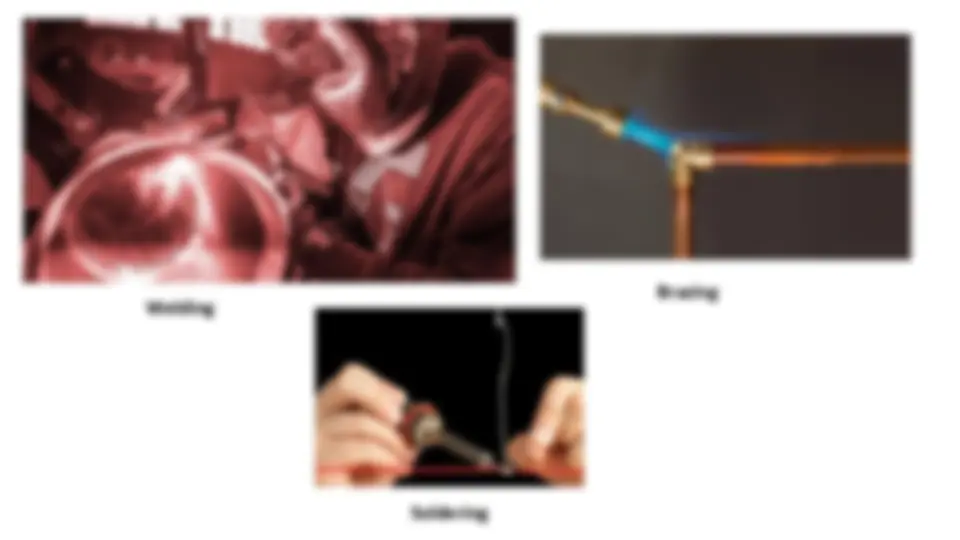
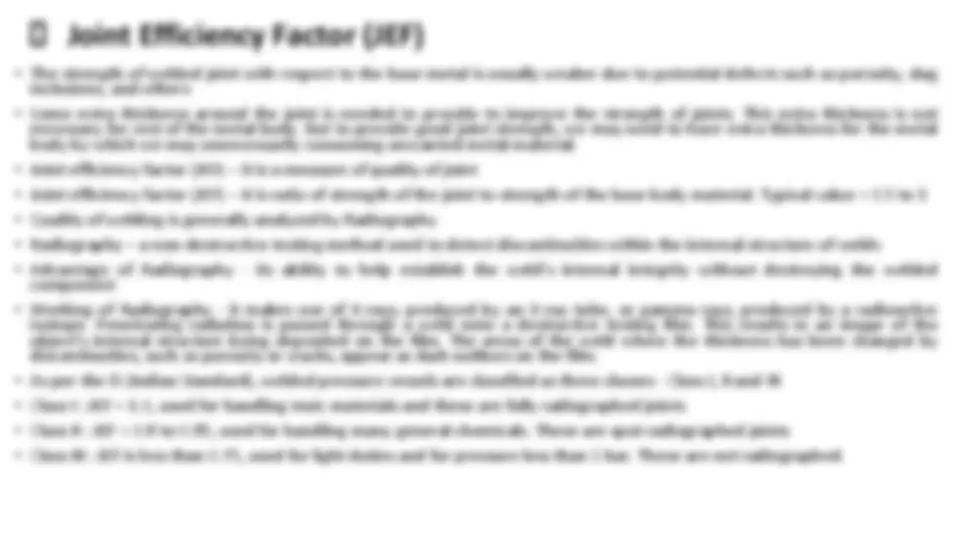
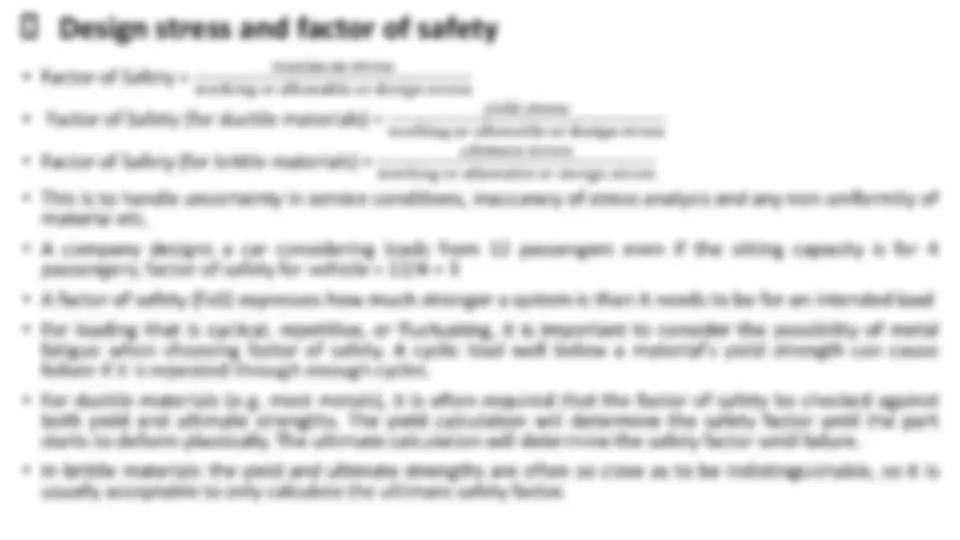
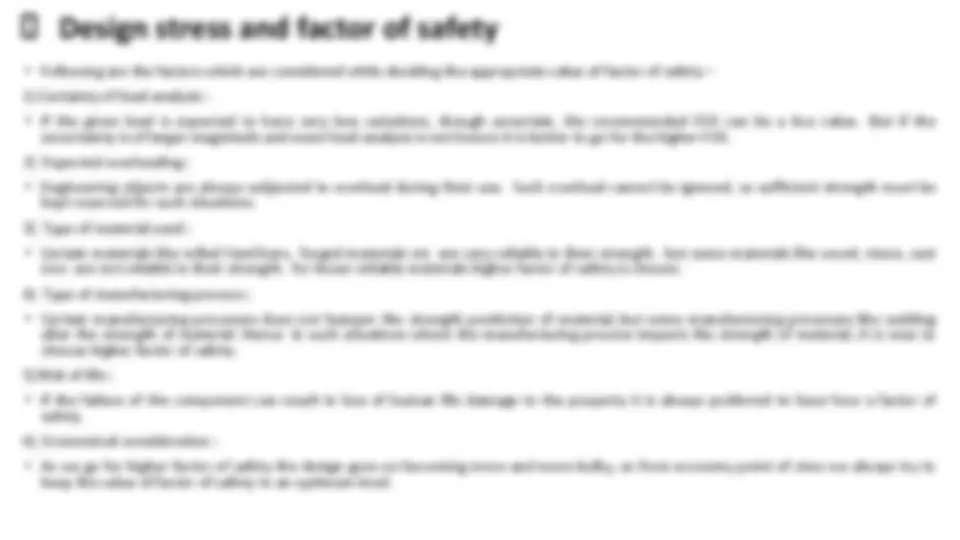
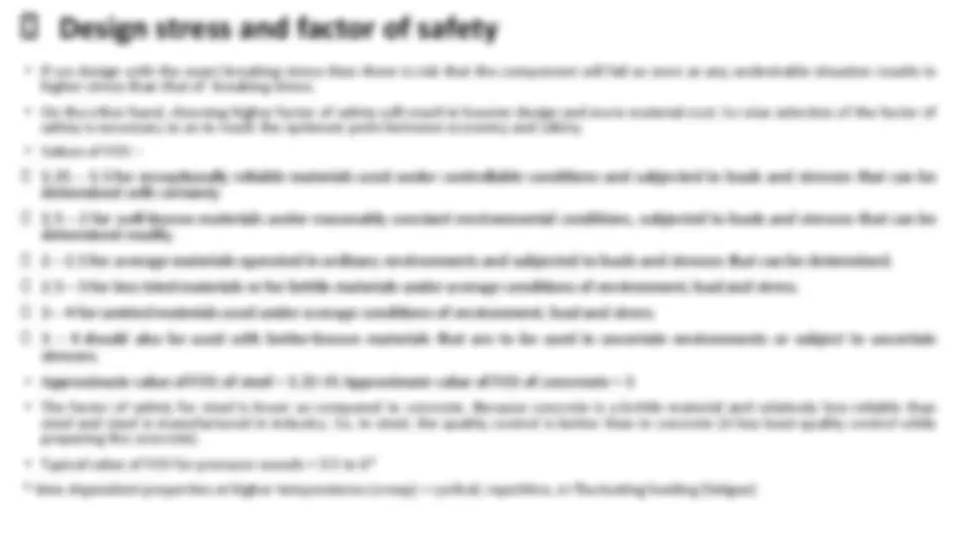
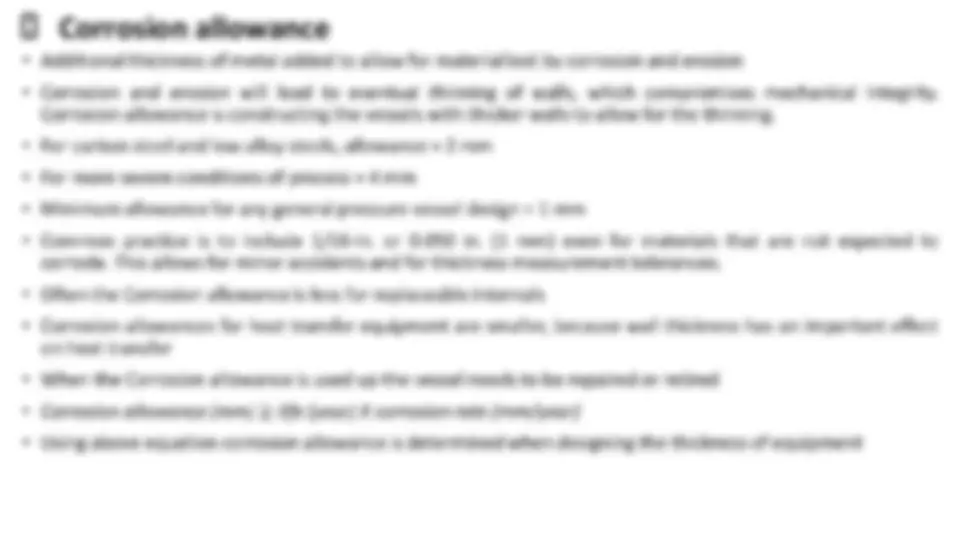
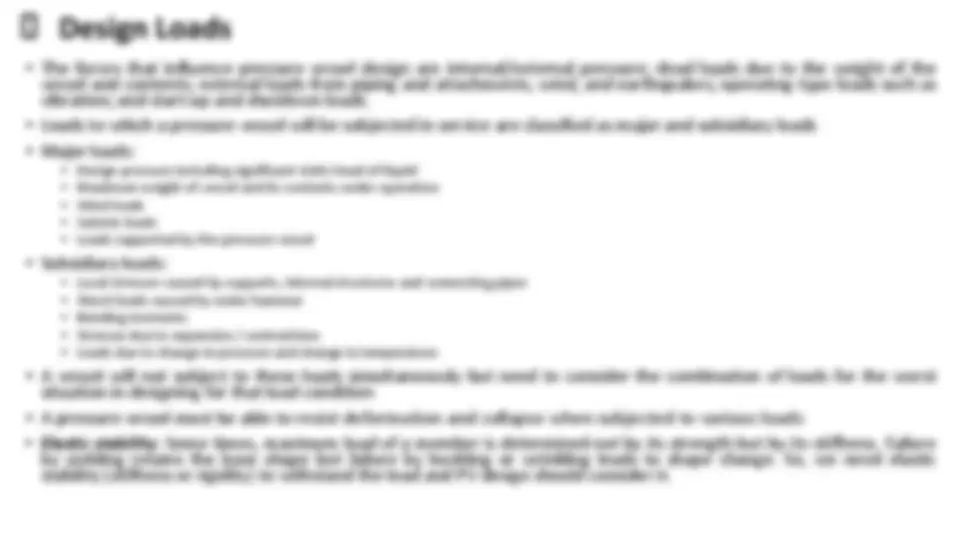
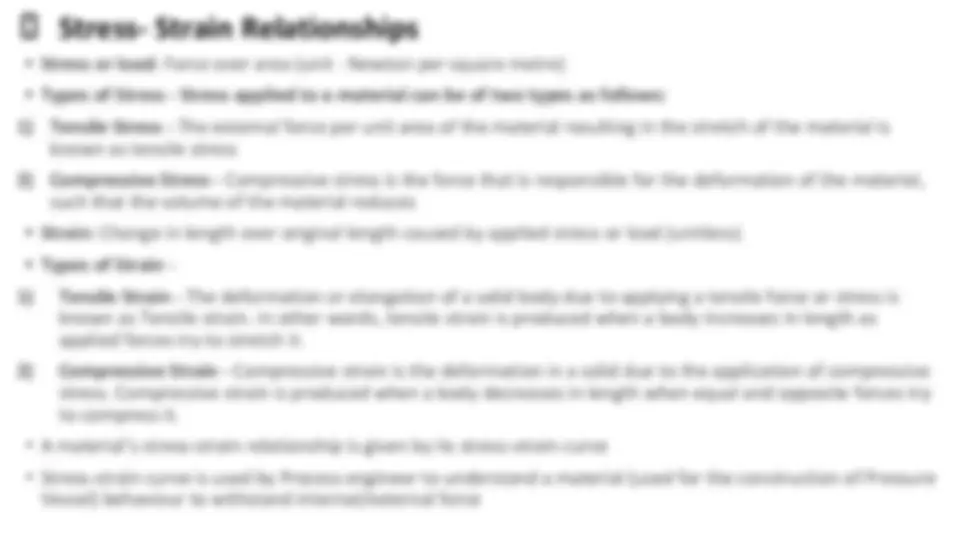
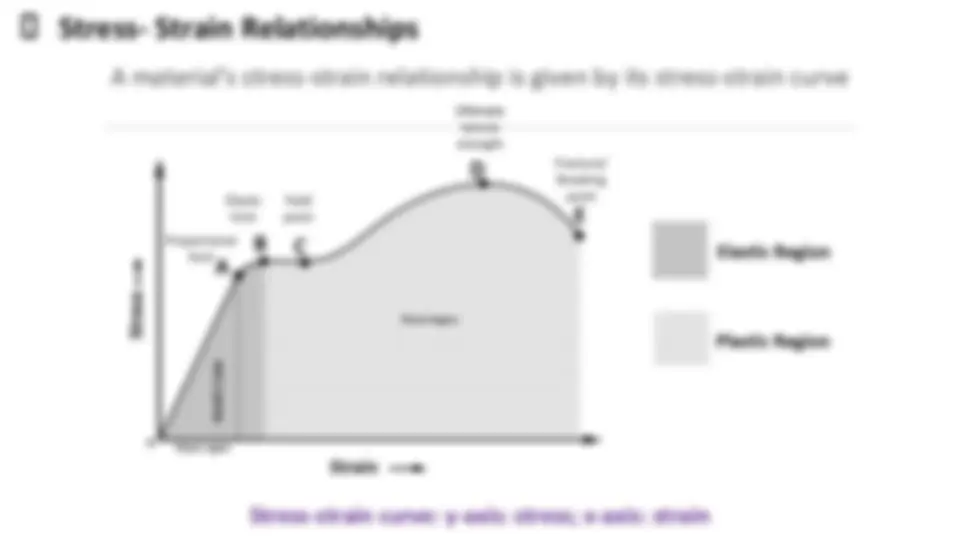

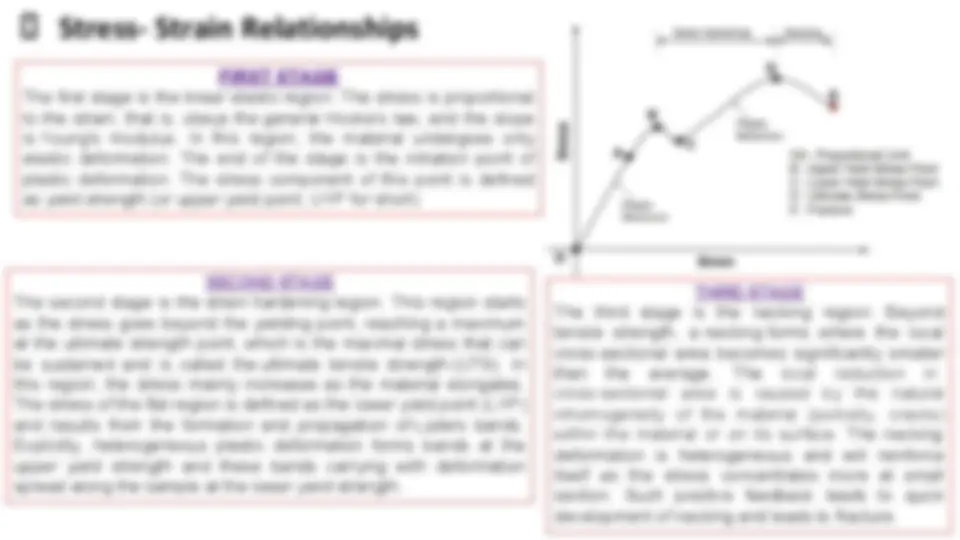
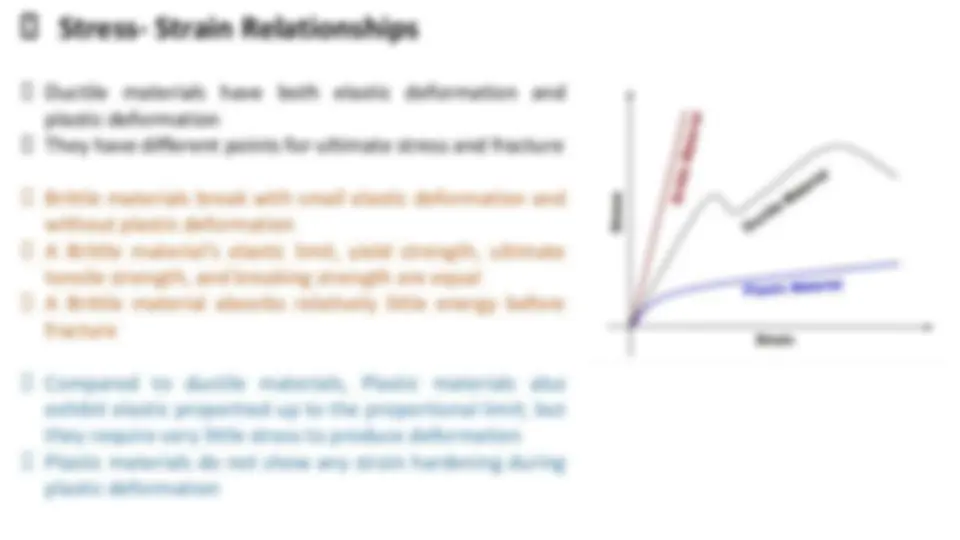
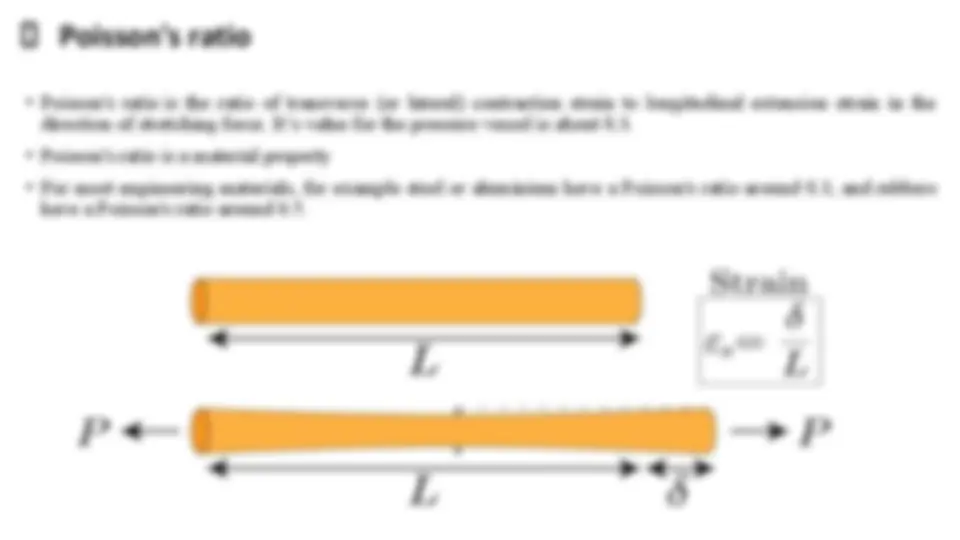
Study with the several resources on Docsity
Earn points by helping other students or get them with a premium plan
Prepare for your exams
Study with the several resources on Docsity
Earn points to download
Earn points by helping other students or get them with a premium plan
Community
Ask the community for help and clear up your study doubts
Discover the best universities in your country according to Docsity users
Free resources
Download our free guides on studying techniques, anxiety management strategies, and thesis advice from Docsity tutors
An overview of the factors influencing the design of chemical engineering equipment, focusing on vessels such as autoclaves, distillation columns, and heat exchangers. It covers the types of vessels, materials of construction, and methods of fabrication. The document also discusses the importance of design codes and safety considerations.
Typology: Lecture notes
1 / 35
This page cannot be seen from the preview
Don't miss anything!
Assistant Professor, Chemical Engineering, IIT (BHU) Varanasi
Assistant Professor, Chemical Engineering, IIT (BHU) Varanasi