
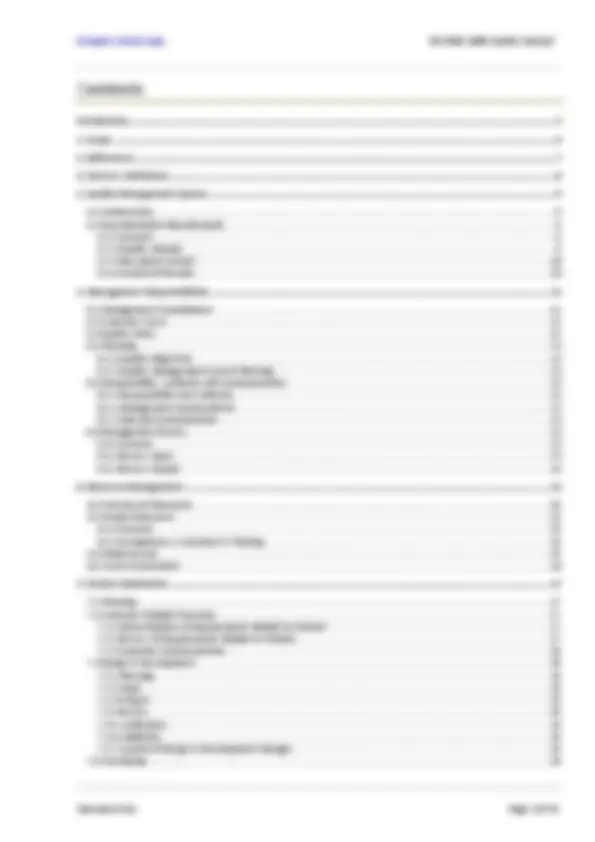
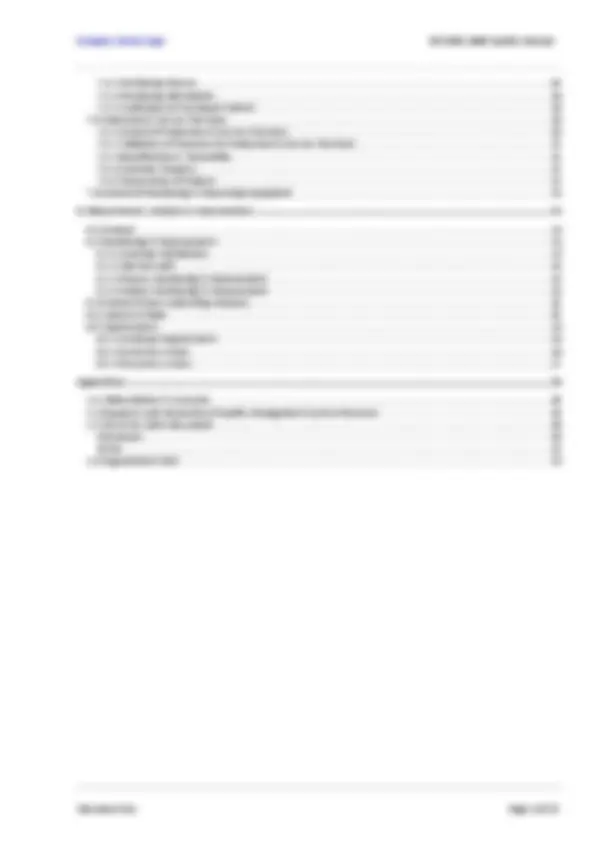
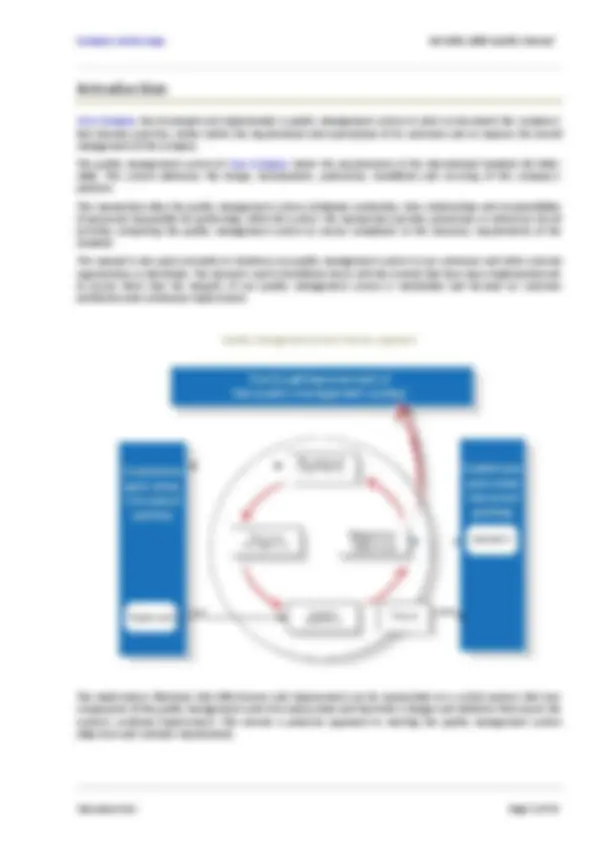
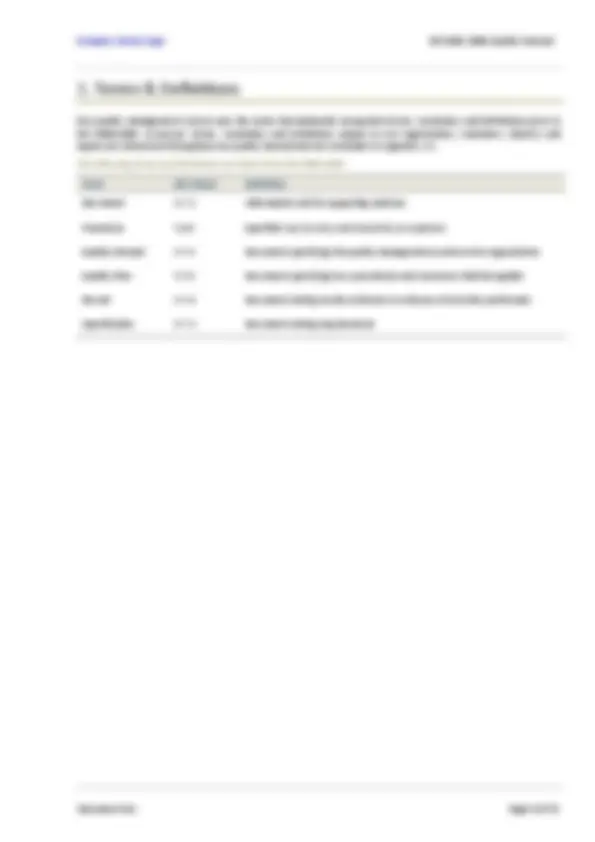
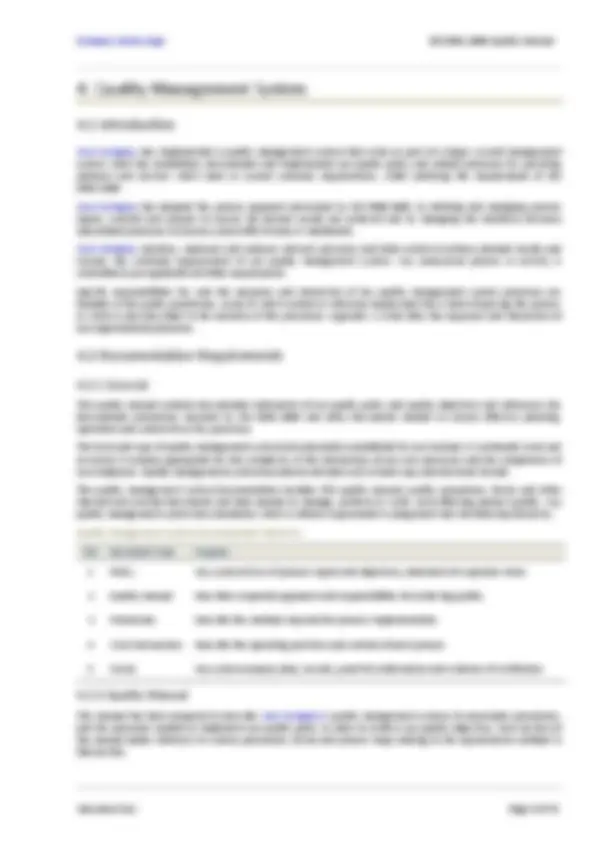
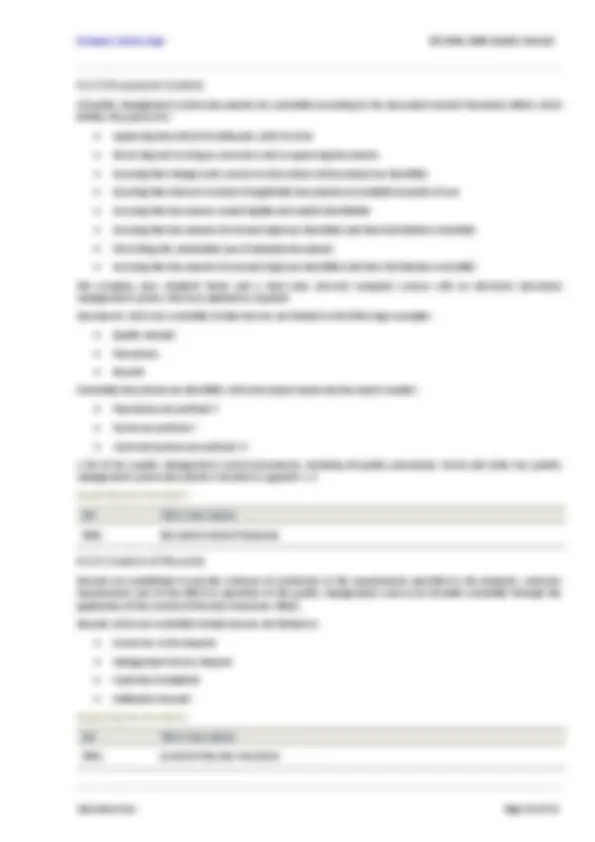
Study with the several resources on Docsity
Earn points by helping other students or get them with a premium plan
Prepare for your exams
Study with the several resources on Docsity
Earn points to download
Earn points by helping other students or get them with a premium plan
Community
Ask the community for help and clear up your study doubts
Discover the best universities in your country according to Docsity users
Free resources
Download our free guides on studying techniques, anxiety management strategies, and thesis advice from Docsity tutors
Quality management system documents and data exist in hard copy and electronic format. The quality management system documentation includes this quality manual, ...
Typology: Lecture notes
1 / 10
This page cannot be seen from the preview
Don't miss anything!
Document No Rev
Uncontrolled Copy Controlled Copy Date
COMPANY PROPRIETARY INFORMATION
Prior to use, ensure this document is the most recent revision by checking the Master Document List. To request a change, submit a Document Change Request to the Document Control Representative.
The signatures below certify that this quality manual has been reviewed and accepted, and demonstrates that the signatories are aware of all the requirements contained herein and are committed to ensuring their provision.
Name Signature Position Date
Prepared by
Reviewed by
Approved by
This quality manual is reviewed to ensure its continuing relevance to the systems and process that it describes. A record of contextual additions or omissions is given below:
Page No. Context Revision Date
Introduction
Your Company has developed and implemented a quality management system in order to document the company’s best business practices, better satisfy the requirements and expectations of its customers and to improve the overall management of the company.
The quality management system of Your Company meets the requirements of the international standard ISO 9001:
This manual describes the quality management system, delineates authorities, inter relationships and responsibilities of personnel responsible for performing within the system. The manual also provides procedures or references for all activities comprising the quality management system to ensure compliance to the necessary requirements of the standard.
This manual is also used externally to introduce our quality management system to our customers and other external organizations or individuals. The manual is used to familiarise them with the controls that have been implemented and to assure them that the integrity of our quality management system is maintained and focused on customer satisfaction and continuous improvement.
Quality Management System Process Approach
The model above illustrates that effectiveness and improvement can be represented as a cyclical process that uses components of the quality management system to analyze data and then direct changes and initiatives that ensure the system’s continual improvement. This ensures a proactive approach to meeting the quality management system objectives and customer requirements.
In addition to ISO 9001:2008, the company will also make reference to relevant British and or international standards as well as customer specifications appropriate to the product and its market.
Standard Title Title & Description
ISO 9000:2005 Quality management systems Fundamentals and vocabulary
ISO 9001:2008 Quality management systems Requirements
ISO 9004:2000 Quality management systems Guidelines for performance improvements
Our quality management system uses the same internationally recognised terms, vocabulary and definitions given in ISO 9000:2005. Acronyms, terms, vocabulary and definitions unique to our organization, customers, industry and region are referenced throughout our quality manual and are contained in Appendix A.1.
The following terms and definitions are taken from ISO 9000:2005:
Term ISO Clause Definition
Document 3.7.2 Information and its supporting medium
Procedure 3.4.5 Specified way to carry out an activity or a process
Quality Manual 3.7.4 Document specifying the quality management system of an organization
Quality Plan 3.7.5 Document specifying how procedures and resources shall be applied
Record 3.7.6 Document stating results achieved or evidence of activities performed
Specification 3.7.3 Document stating requirements
All quality management system documents are controlled according to the Document Control Procedure (P001) which defines the process for:
Approving documents for adequacy prior to issue
Reviewing and revising as necessary and re-approving documents
Ensuring that changes and current revision status of documents are identified Ensuring that relevant versions of applicable documents are available at points of use
Ensuring that documents remain legible and readily identifiable
Ensuring that documents of external origin are identified and their distribution controlled
Preventing the unintended use of obsolete documents Ensuring that documents of external origin are identified and their distribution controlled
The company uses standard forms and a local area network computer system with an electronic document management system which are updated as required.
Documents which are controlled include but are not limited to the followings examples:
Quality manual
Procedures Records
Controlled documents are identified with a document name and document number:
Procedures are prefixed P
Forms are prefixed F
Work instructions are prefixed W
A list of key quality management system documents; including all quality procedures, forms and other key quality management system documents is located in Appendix A.3.
Supporting documentation:
Ref Title & Description
P001 Document Control Procedure
Records are established to provide evidence of conformity to the requirements specified by the standard, customer requirements and of the effective operation of the quality management system are formally controlled through the application of the Control of Records Procedure (P002).
Records which are controlled include but are not limited to:
Corrective Action Reports Management Review Reports
Customer Complaints
Calibration Records
Supporting documentation:
Ref Title & Description
P002 Control of Records Procedure