
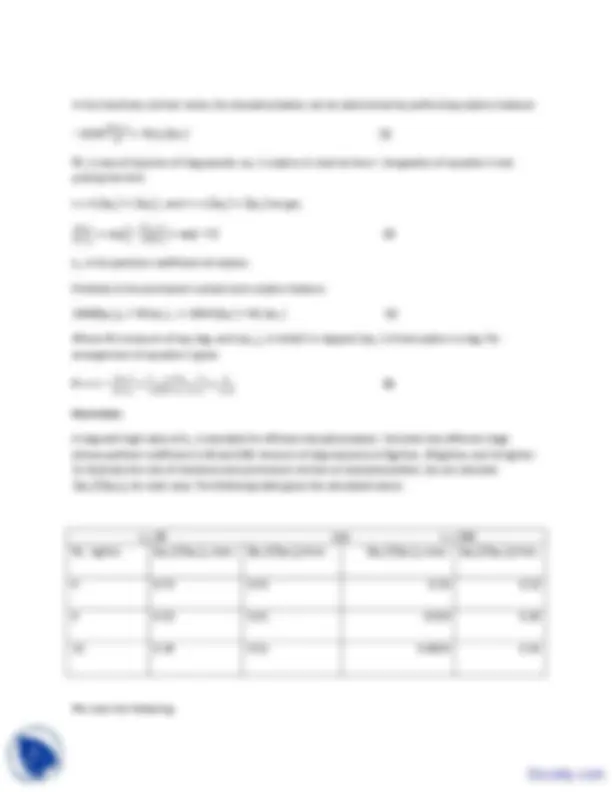
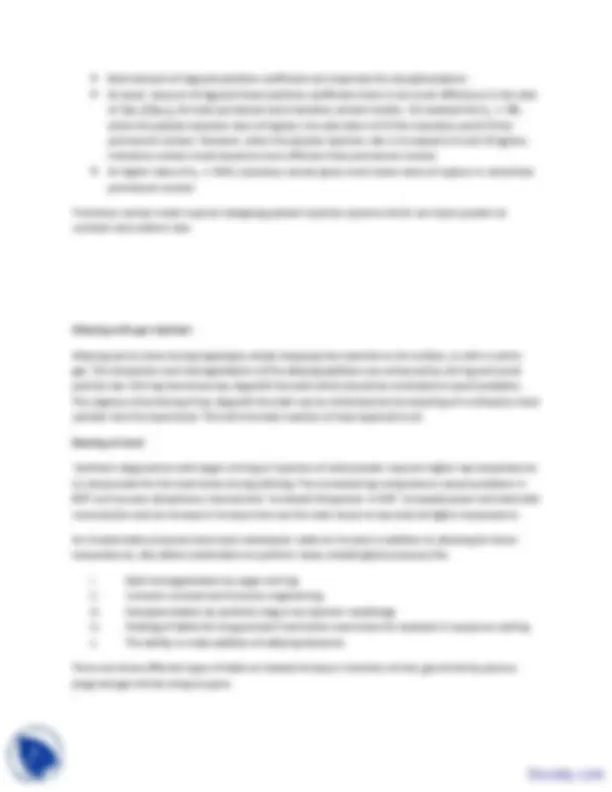
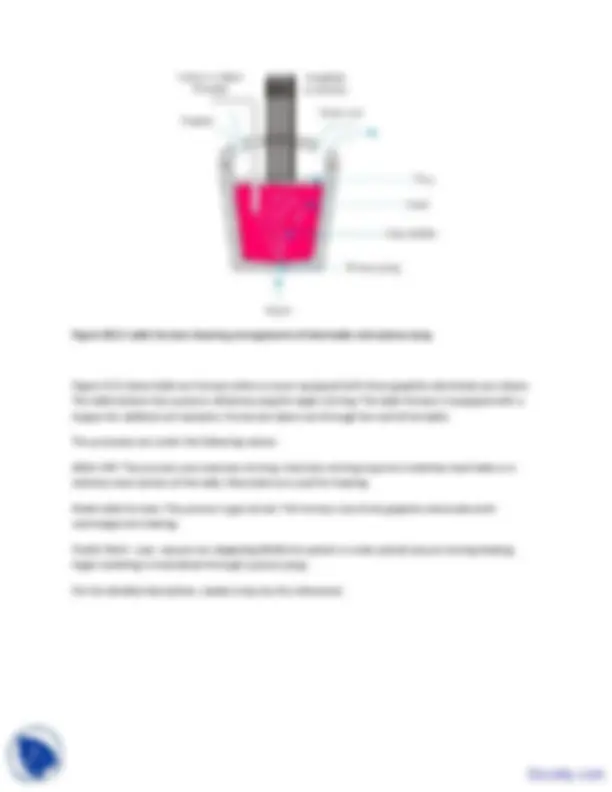
Study with the several resources on Docsity
Earn points by helping other students or get them with a premium plan
Prepare for your exams
Study with the several resources on Docsity
Earn points to download
Earn points by helping other students or get them with a premium plan
Community
Ask the community for help and clear up your study doubts
Discover the best universities in your country according to Docsity users
Free resources
Download our free guides on studying techniques, anxiety management strategies, and thesis advice from Docsity tutors
The major points which I found very informative are:Injection Ladle Metallurgy, Injection of Solid Powders, Desulphurization Mechanism, Alloying with Gas Injection, Heating of Steel, Alloying, Permanent Contact, Ladle Refining, Transitory Contact, Ladle Furnace
Typology: Study notes
1 / 5
This page cannot be seen from the preview
Don't miss anything!
Lecture 23 : Injection ladle metallurgy
Contents:
Injection of solid powders
Desulphurization Mechanism
Illustration
Alloying with gas injection
Heating of steel
Keywords: alloying, permanent contact, ladle refining, transitory contact, ladle furnace, wire feeding
Injection of solid powders
Injection techniques have the advantages of dispersing the reactants in the steel bath and at the same
time provide a large reaction surface area. The type of powders used is governed by the purpose of
injection. Table below shows the slag forming materials used for injection.
Purpose Type of powder
Dephosphorization CaO+CaF
2
+Fe
2
3
soda
Desulphurization CaO +Al
CaO + CaF 2
+Al
Ca C
2
Mg+(MgO,Al 2
3
, chloride slag)
CaC
2
3
, CaO
Alloying Fe Si, CaCN 2
, NiO, Mo O 2
Fe B, Fe Ti etc
Deoxidation and inclusion
shape control
Al, Ca Si, Ca, Si, Mn, Al,
Ca Si and Ba
Desulphurization mechanism
Desulphurization can be carried out by injecting lime based powder, for example 90 % CaO + 10 % CaF 2
or 70 % CaO + 20 % Al 2
3
2
. The injection rate varies between 2 - 4 kg/ton of melt. When
slag forming materials are injected into melt, they melt and the molten slag particles begin to rise and
accumulate at the top surface of the melt. The desulphurization reaction occurs in two ways:
desulphurization it is important that the powder becomes molten on injection. Residence time
of the rising particles in the melt is also important, which means that the gas powder injection
velocity must be suitably selected. Powder melts and the rising gas imparts mixing in the melt.
This mechanism is known as transitory contact.
top surface of the melt and after a while top slag also takes part in the desulphurization. In this
mechanism slag/metal interface area is important. Gas injection rate may be suitably selected to
produce and entrain slag droplets into the melt for the faster rates of reaction. Once all the
powder is injected, reaction between top slag and sulphur of melt governs the final sulphur
content of steel. This mechanism is known as permanent contact
It must be noted that methods for injection of powder must also be developed. The slag forming
materials are lighter than steel and deep injection would be required for the efficiency of the reaction.
Powder can be injected either through cored wire or pneumatic transport. Figure 23.1 shows
arrangement of ladle desulphurization carried out either by injecting cored wire or by pneumatic
injection through a top lance. In both argon is bubbled through a porous plug fitted at the bottom of the
ladle. The desulphurization efficiency can be estimated by the mass balance.
Figure 23.1 Ladle desulphurization carried out by powder injection technology (a) cored wire injection
and (b) Pneumatic injection through a top lance
Both amount of slag and partition coefficient are important for desulphurization
At lower amount of slag and lower partition coefficient there is not much difference in the ratio
of [m
s
]/[m
s
𝐨𝐨
for both permanent and transitory contact modes.. For example for L
s
when the powder injection rate is 4 kg/ton, the said ratio is 0.73 for transitory and 0.76 for
permanent contact. However, when the powder injection rate is increased to 8 and 12 kg/ton,
transitory contact mode becomes more efficient than permanent contact.
At higher value of L
s
= 500 , transitory contact gives much lower value of sulphur in metal than
permanent contact
Transitory contact mode requires designing powder injection systems which can inject powder at
constant and uniform rate.
Alloying with gas injection
Alloying can be done during tapping by simply dropping the material on the surface, or with a carrier
gas. The dissolution and homogenization of the alloying additions are enhanced by stirring and small
particle size. Stirring intermixes top slag with the bath which should be minimized to avoid oxidation.
The vigorous intermixing of top slag with the bath can be minimized by the lowering of a refractory lined
cylinder into the liquid steel. This will minimize reaction of steel exposed to air.
Heating of steel
Synthetic slag practice with argon stirring or injection of solid powder requires higher tap temperatures
to compensate for the heat losses during refining. This increased tap temperature causes problems in
BOF such as poor phosphorus removal and increased lining wear. In EAF increased power and electrode
consumption and an increase in furnace time are the main issues to tap steel at higher temperature.
Arc heated ladle processes have been developed. Ladle arc furnace in addition to allowing for lower
temperatures, also allows steelmakers to perform many metallurgical processes like
i. Bath homogenization by argon stirring
ii. Inclusion removal and inclusion engineering
iii. Desulphurization by synthetic slag or by injection metallurgy
iv. Holding of ladles for long periods if and when need arises for example in sequence casting.
v. The ability to make addition of alloying elements.
There are three different types of ladle arc heated furnaces: Induction stirred, gas stirred by porous
plugs and gas stirred using a tuyere.
Figure 23.2: Ladle furnace showing arrangement of electrodes and porous plug
Figure 23.2 shows ladle arc furnace where a cover equipped with three graphite electrodes are shown.
The ladle bottom has a porous refractory plug for argon stirring. The ladle furnace is equipped with a
hopper for additions of reactants. Fumes are taken out through the roof of the ladle.
The processes are under the following names:
ASEA- SKF: The process uses induction stirring. Induction stirring requires a stainless steel ladle or a
stainless steel section of the ladle. Electrodes are used for heating.
Diado ladle furnace: The process is gas stirred. The furnace uses three graphite electrodes with
submerged are heating.
FineKl- Mohr uses vacuum arc degassing (VAD) the system is under partial vacuum during heating.
Argon bubbling is maintained through a porous plug.
For the detailed description, readers may see the references.