
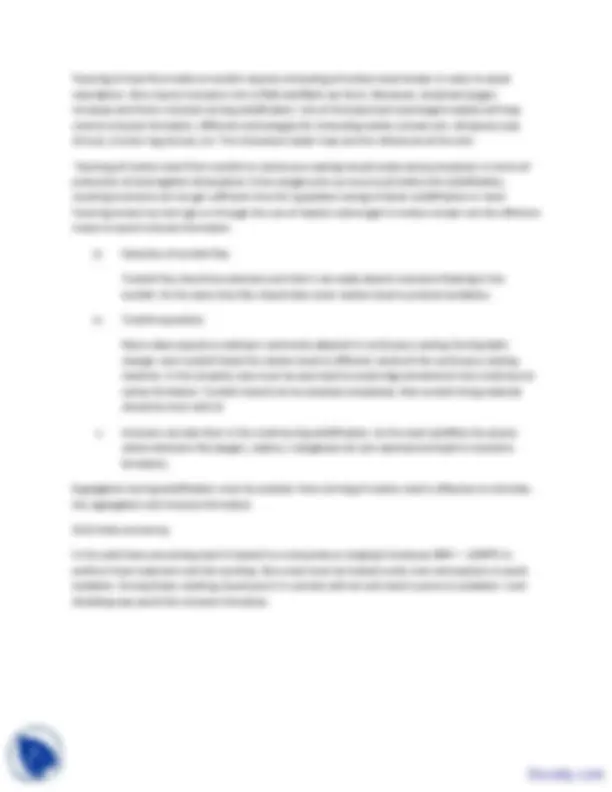
Study with the several resources on Docsity
Earn points by helping other students or get them with a premium plan
Prepare for your exams
Study with the several resources on Docsity
Earn points to download
Earn points by helping other students or get them with a premium plan
Community
Ask the community for help and clear up your study doubts
Discover the best universities in your country according to Docsity users
Free resources
Download our free guides on studying techniques, anxiety management strategies, and thesis advice from Docsity tutors
The major points which I found very informative are:Inclusion Sources and Control, Inclusion Formation, Control of Inclusions, Inclusion in Steel, Inclusion Engineering, Clean Steel, Teeming Stream, Tapping of Molten Stream, Liquid State Processing, Tundish Flux
Typology: Study notes
1 / 3
This page cannot be seen from the preview
Don't miss anything!
Lecture 28: inclusion sources and control Why inclusion control is necessary Sources of inclusion formation Control of inclusions Key words: Inclusion in steel, inclusion engineering, clean steel Why inclusion control is necessary? Impact properties are adversely affected with an increase in volume fraction of inclusion as well as inclusion length; spherical inclusions are better. Brittle inclusions or inclusions that have low bond strength with the matrix break up during early straining and create voids at the inclusion/ matrix interface. Hot fatigue strength of high strength steel is reduced by surface and subsurface inclusions those have lower expansion coefficient than steel The hot workability of steel is affected by the low deformability of inclusions Anisotropy of a property is caused by orientation of elongated inclusions along the direction of working. Macro inclusions of sulphides are desirable for better steel machining properties. In view of the above, control of inclusion in steel is necessary. It must be mentioned and as pointed out earlier (see A. iv), macro- inclusions are harmful and they must be controlled. Sources of inclusion formation Inclusions can form either ( a ) during transfer of molten steel from one reactor to other or (b) during solidification of steel (lecture 27) or during solid state processing by any of the following mechanisms: i. Reaction between rejected solute elements during solidification, for example, reaction between sulphur and manganese, and between oxygen and aluminium etc. ii. Mechanical and chemical erosion of refractory and other materials. iii. Oxygen pickup by teeming stream and consequent oxide formation. iv. Chemical reactions. Inclusions produced by mechanism ( i) are called endogenous, whereas mechanisms ii and iii produce exogenous inclusions. Inclusions can form during
a) Tapping of molten stream from BOF/EAF to ladle. Erosion of launder refractory is the possible source. Pick up of oxygen from atmosphere and formation of FeO. b) Treatment of steel in ladle. Here molten steel is in contact with the refractory. Also during deoxidation and synthetic slag treatment oxide/sulphide inclusions may form c) Teeming of molten stream. Molten steel is in contact with stopper and nozzle refractory and elements like Ti, Mg etc., which can form oxides. Air entrainment into molten steel stream brings oxygen and FeO formation is initiated. d) Solidification in mould due to precipitation of excess solute elements. e) Final finishing operations like heat treatment and deformation processing. Here steel is heated to high temperature which may cause surface oxidation, surface sulphurization, inner oxidation,etc. f) Fusion welding. Oxidation of weld pool, electrode coatings are the possible source of inclusions in fusion welding processes. Control of inclusions Inclusions can be controlled either at (a) during liquid steel processing stage or (b) during solid state processing. Liquid state processing During liquid state processing inclusion control can be exercised at tapping and teeming of steel. i. During tapping of molten stream from BOF/EAF carry- over of slag must be minimized if not prevented. BOF slags are highly oxidizing in nature and contain oxides like FeO, MnO, SiO 2 , CaO, MgO etc. These oxides react with Al during ladle treatment and lead to inclusion formation. Consider the reaction 3 FeO(l) + 2 Al = Al 2 O 3 + 3 Fe 3 MnO(l) + 2 Al = Al 2 O 3 + 3 Mn Carry over of 1 kg FeO in slag decreases Al by 0.286 kg. which in turn forms 0.51kg Al 2 O 3. Assuming spherical shape inclusion of 1mm dia (in practice different diameter of inclusions can form) and density of Al 2 O 3 = 4000 kg m^3 , number of inclusions are 240/kg carry-over^ FeO^ of slag. Thus carry-over^ of slag must be minimized by adopting slag free tapping technologies. Another way for inclusion formations is reoxidation of tapping stream. Tapping stream exposes very large surface area in the atmosphere and hence oxygen pick up leads to oxide inclusion formation. ii. Molten steel stream after treatment in the ladle is teemed into tundish and then from tundish to mould in the continuous casting.