
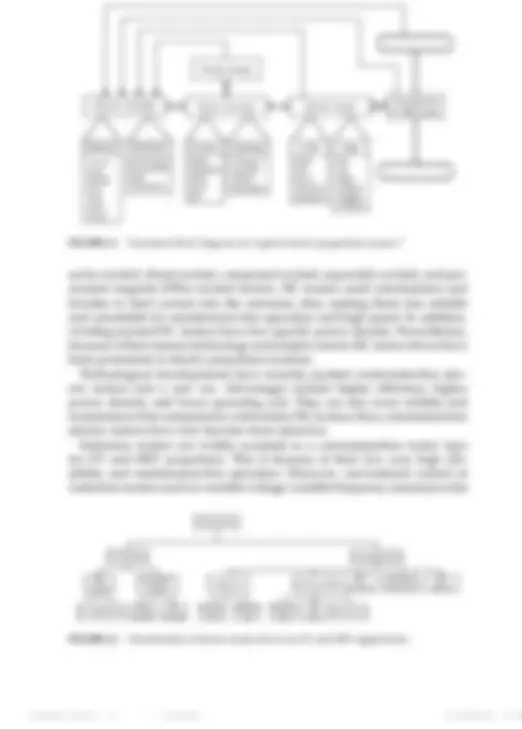
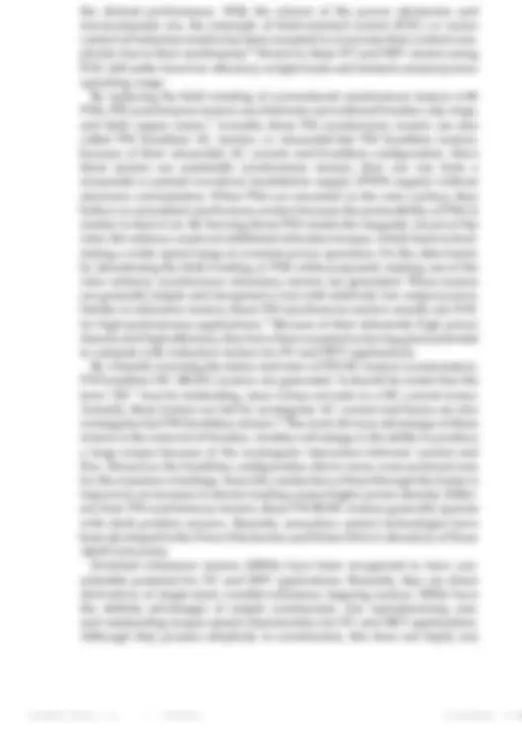
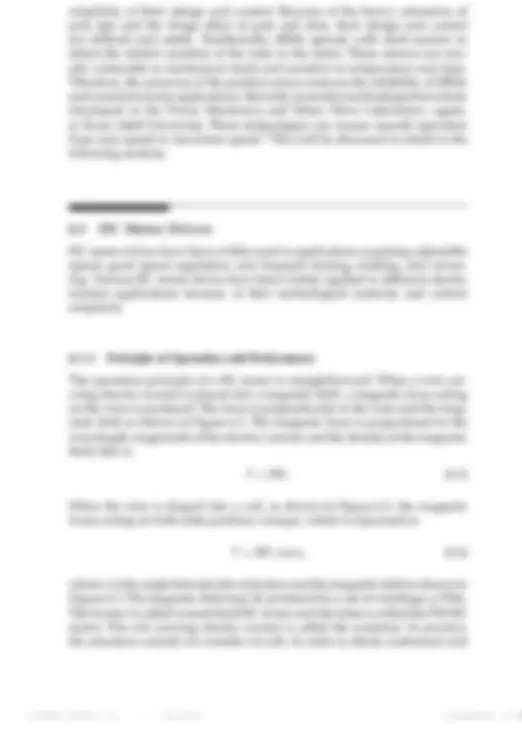
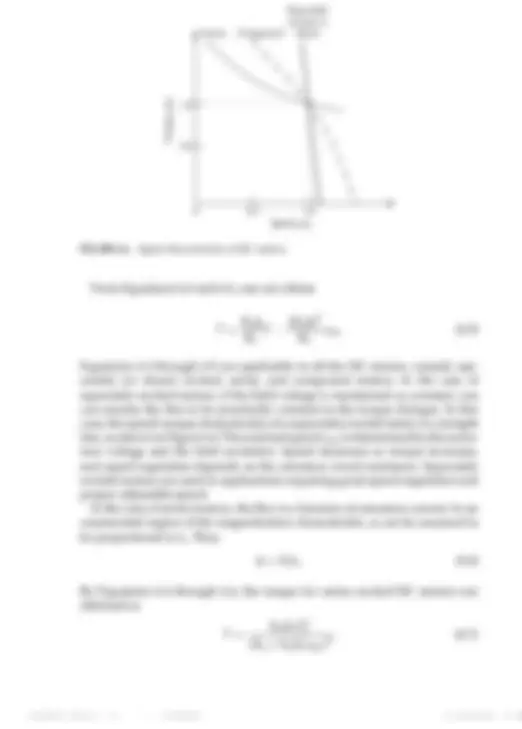

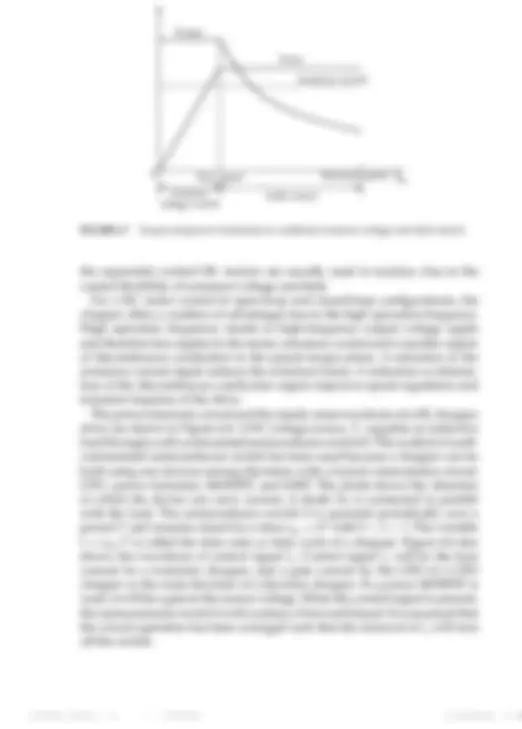
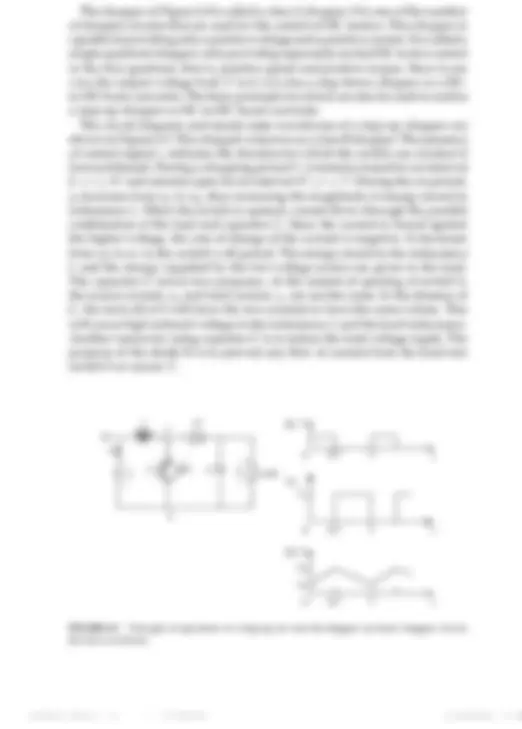
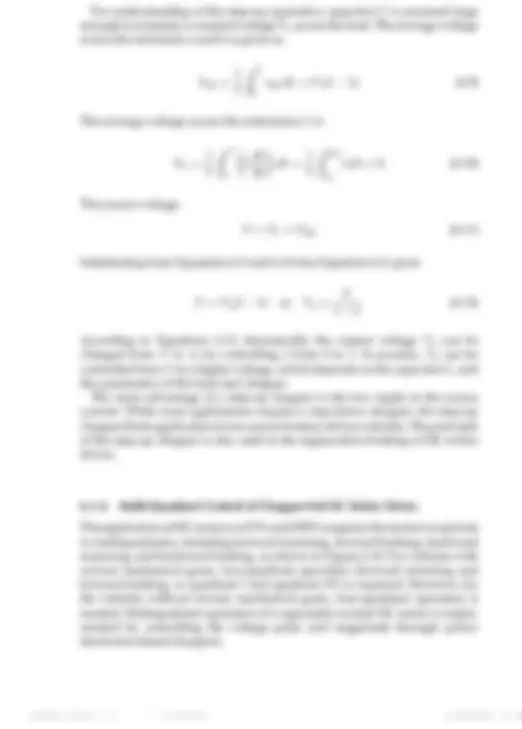
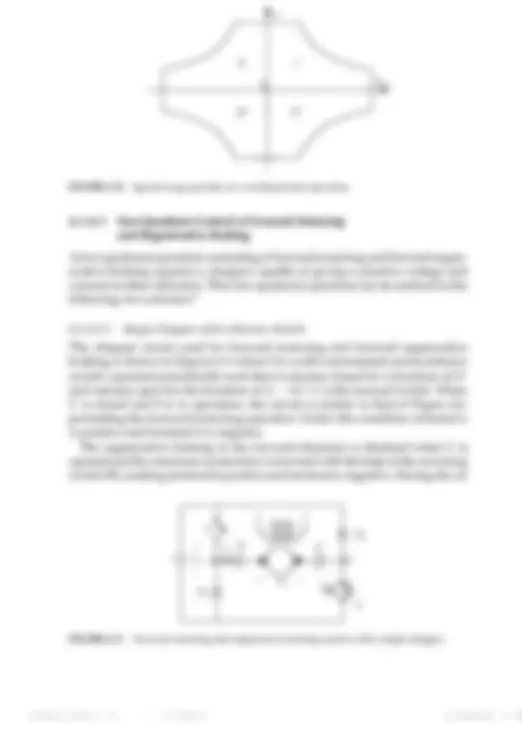
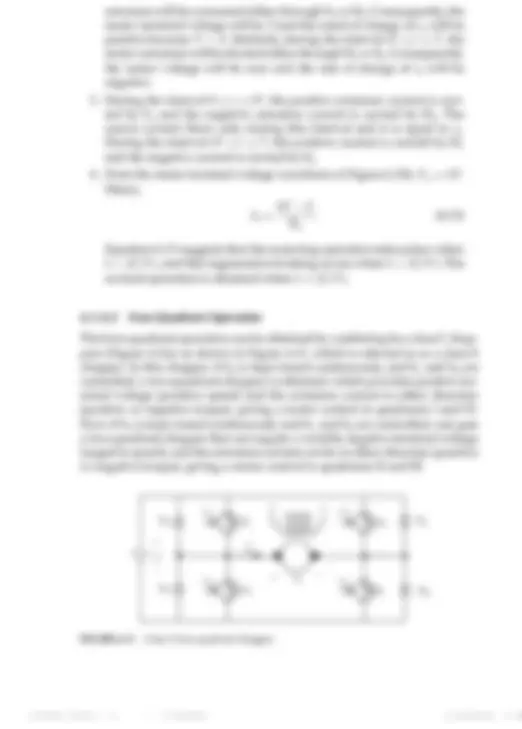
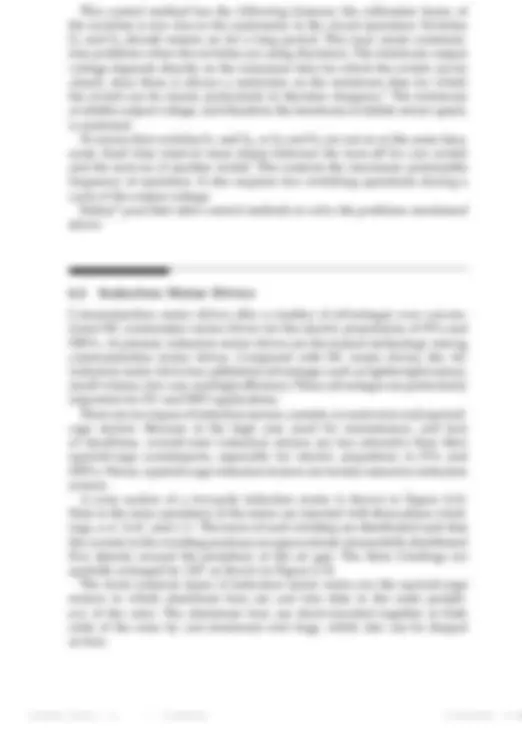
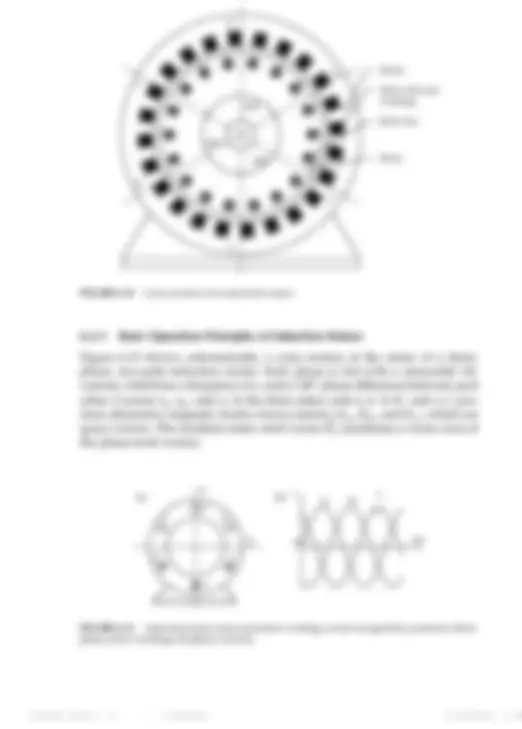
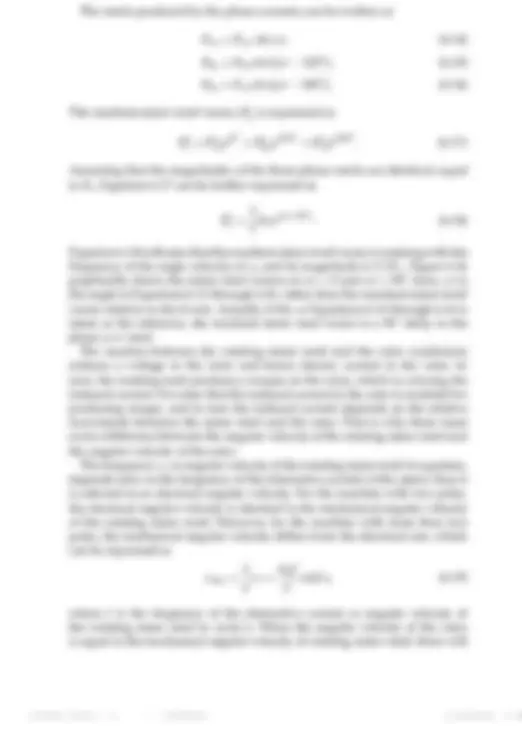
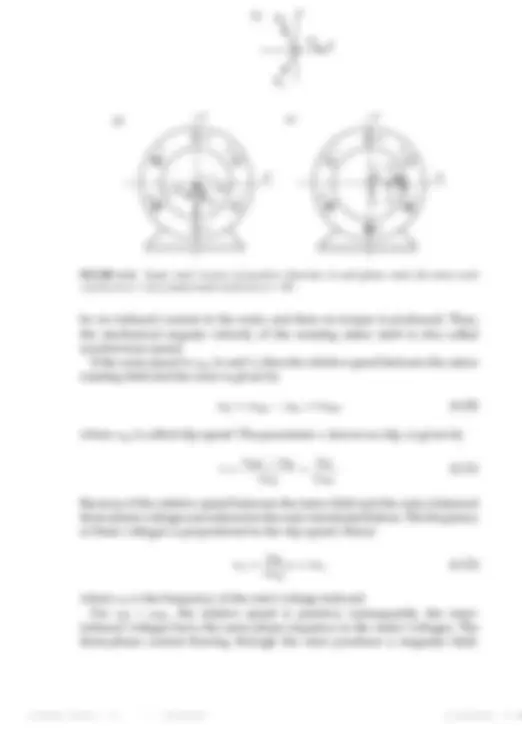
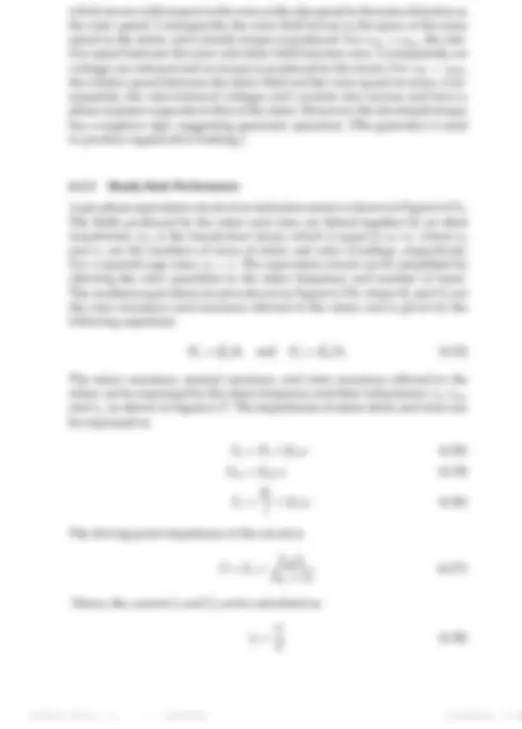
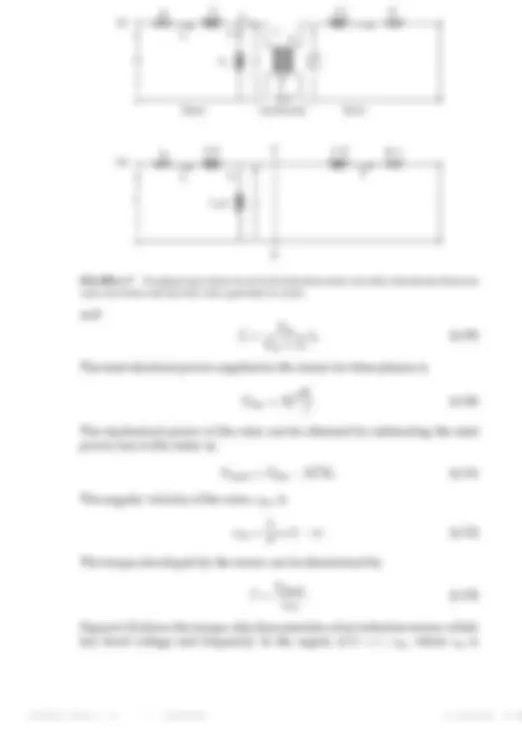
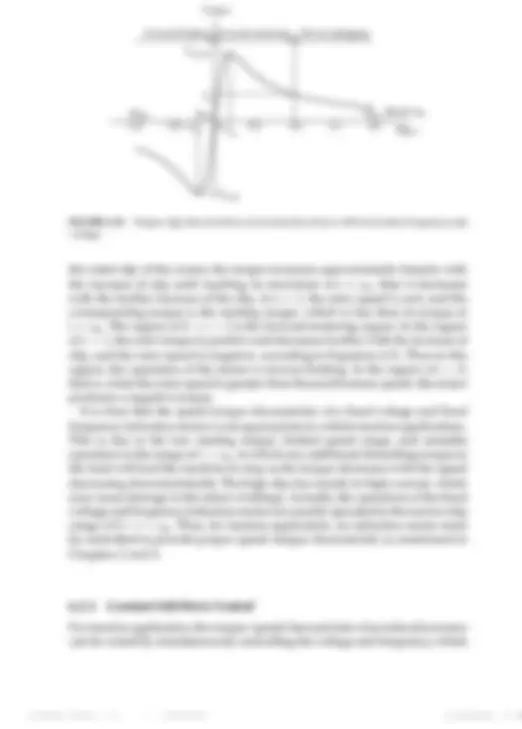
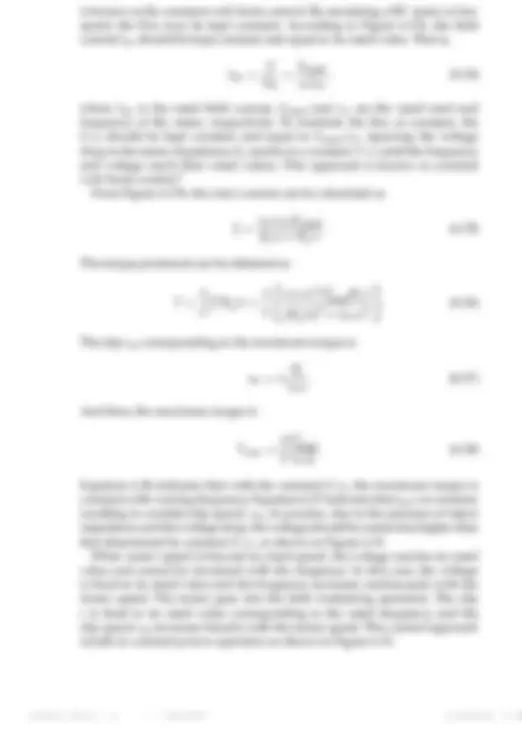
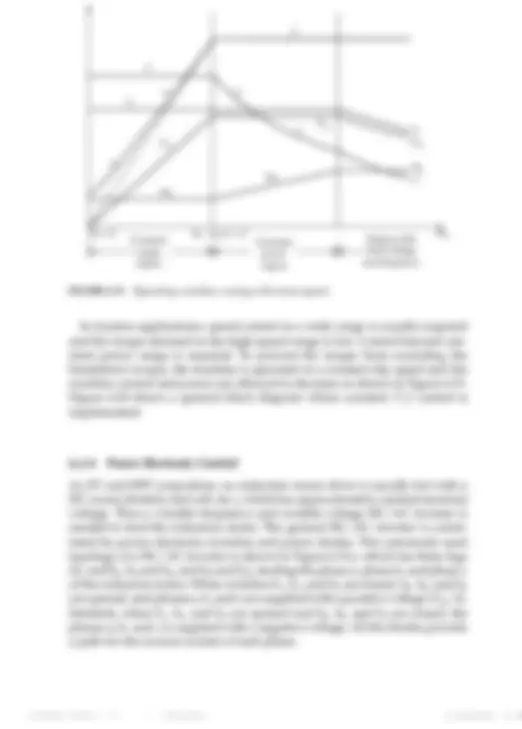
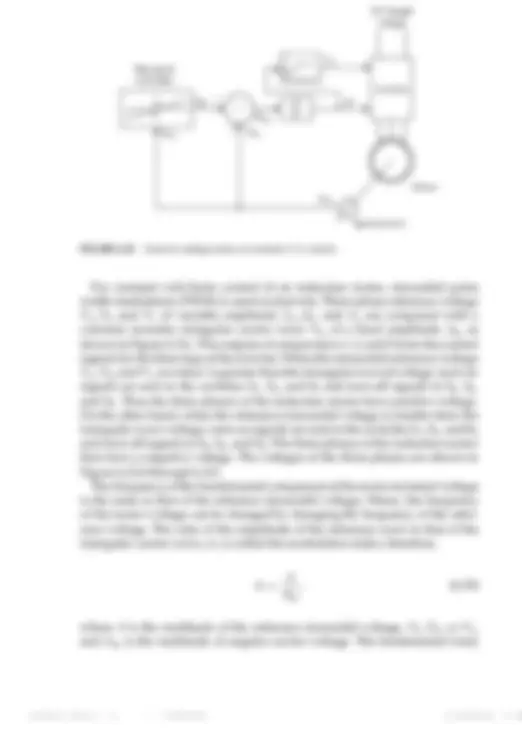
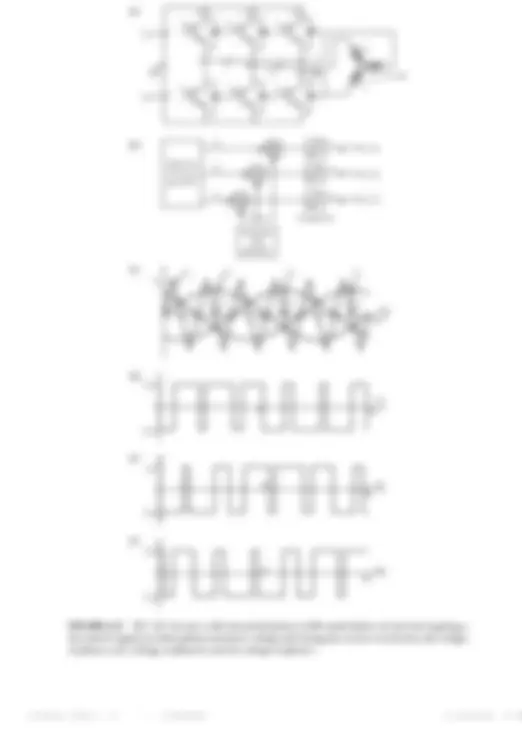
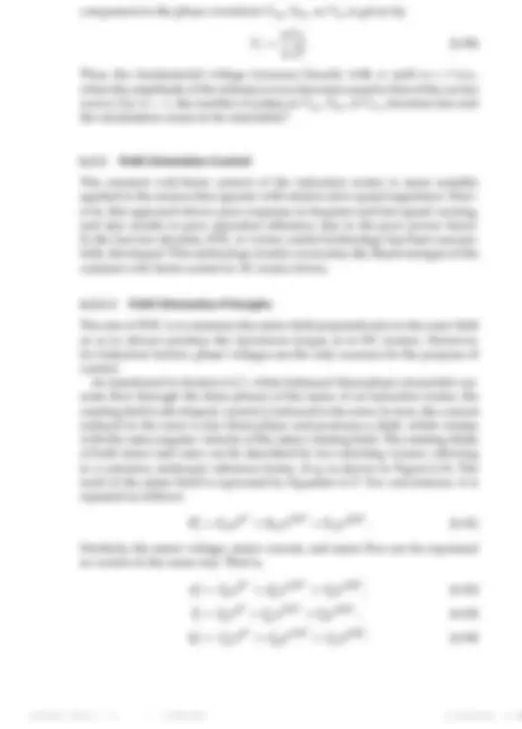
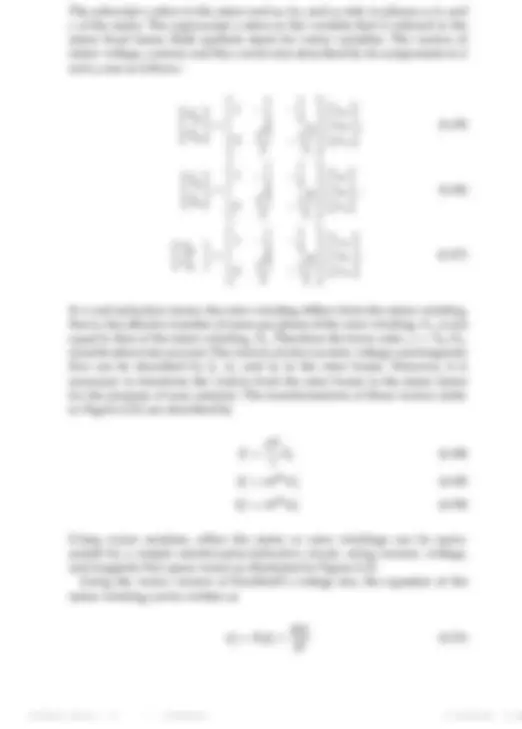
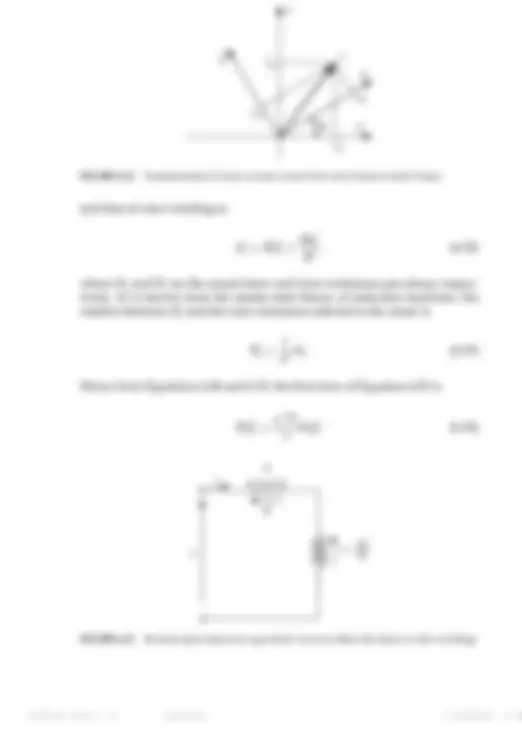
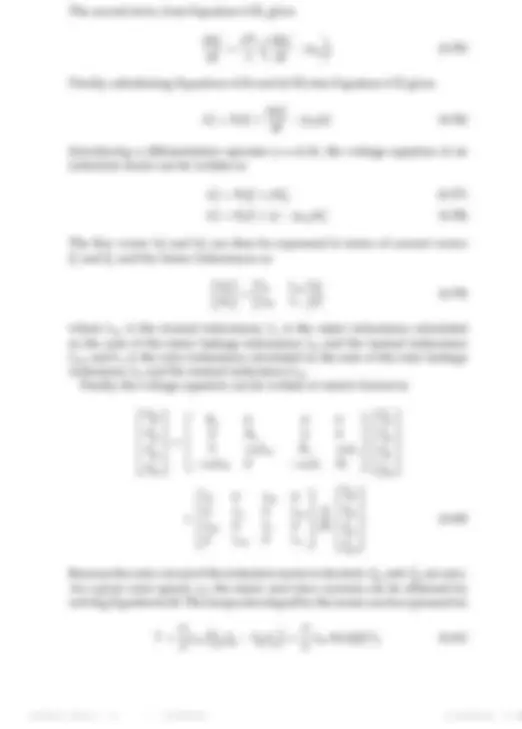
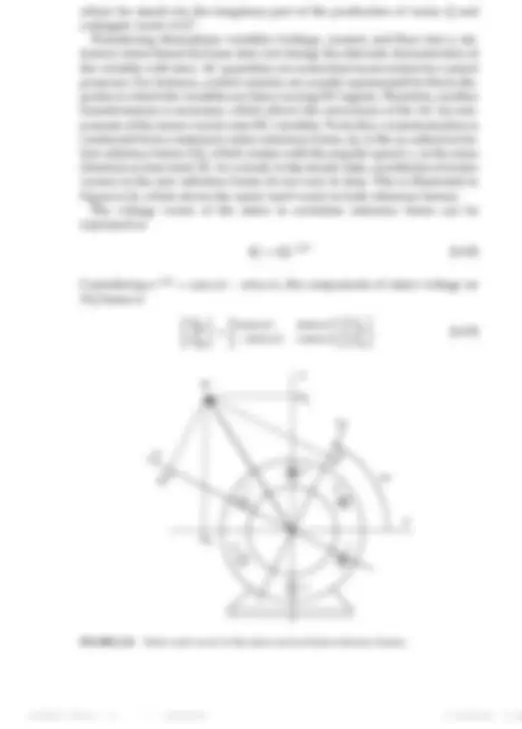
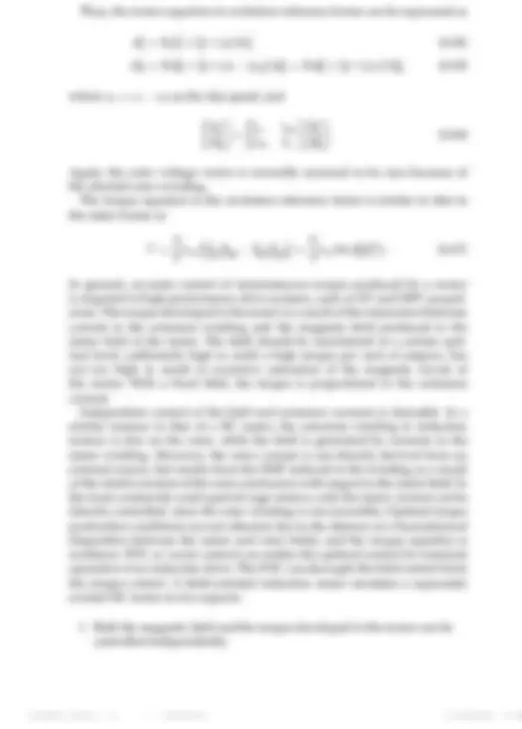
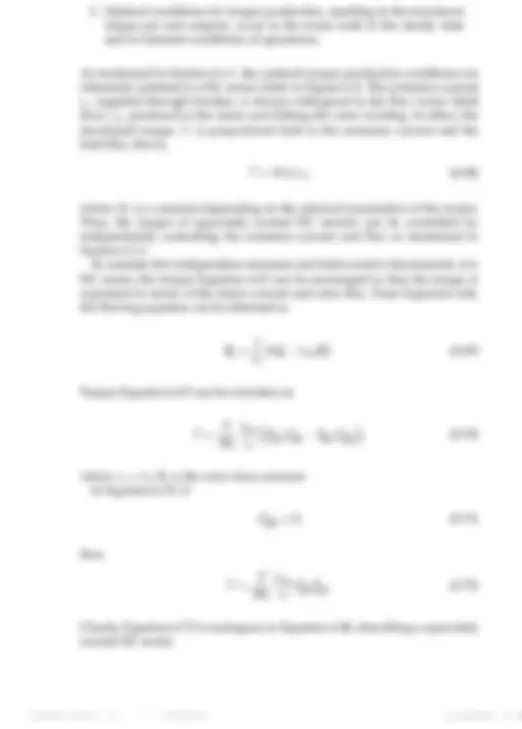
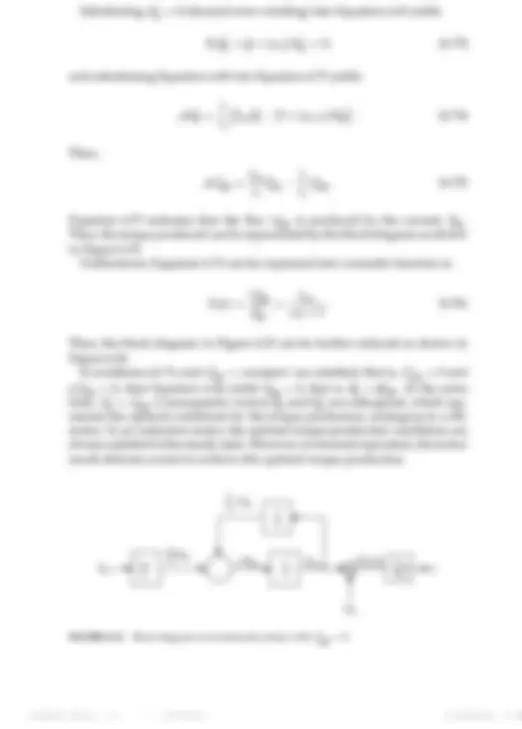
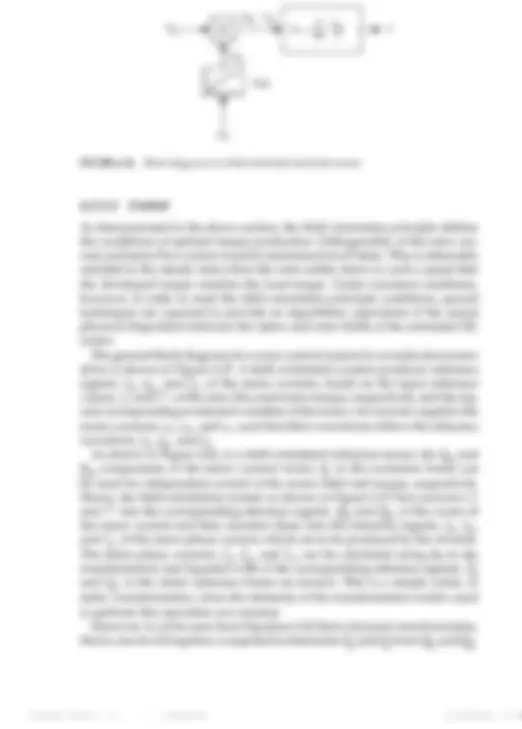
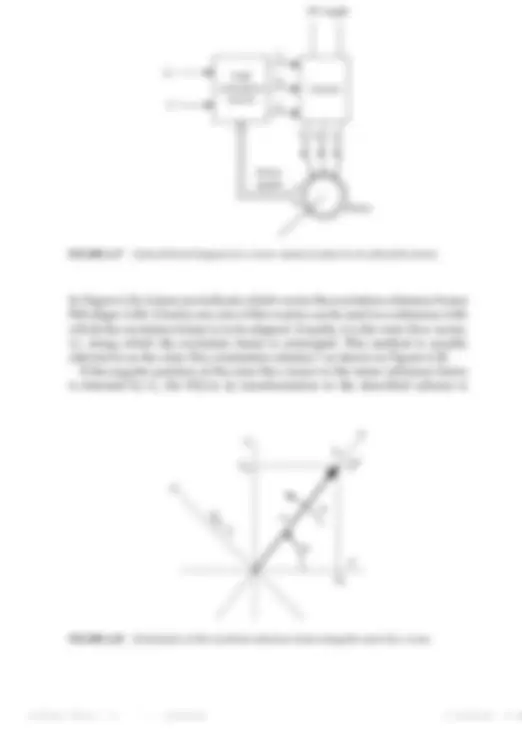
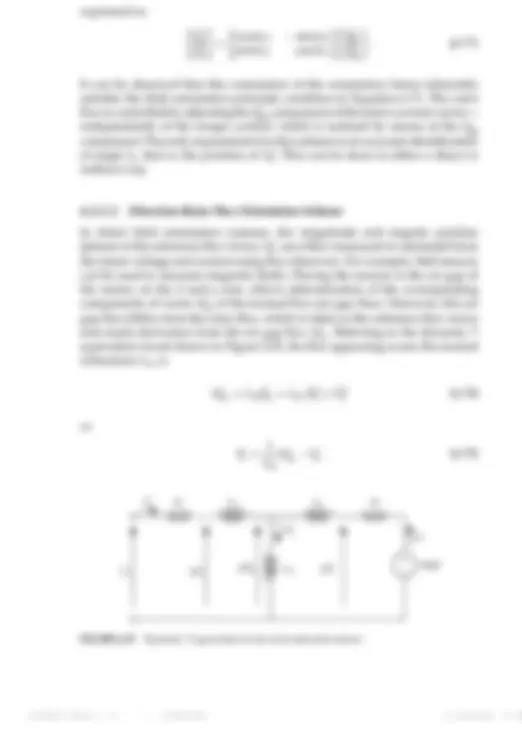
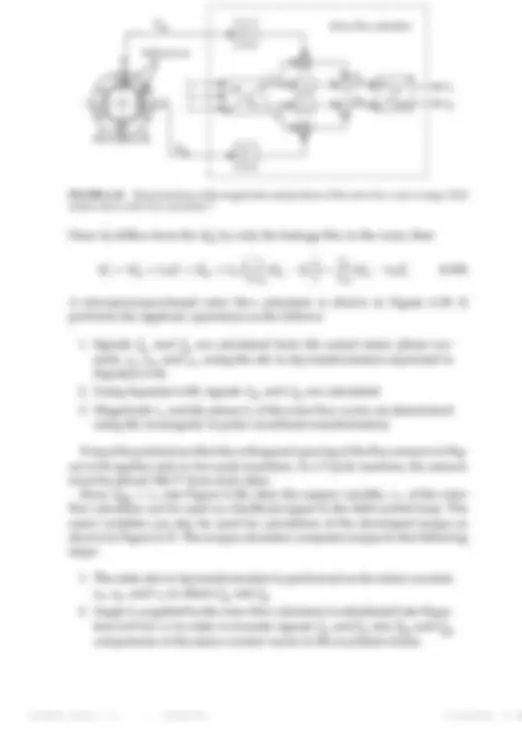
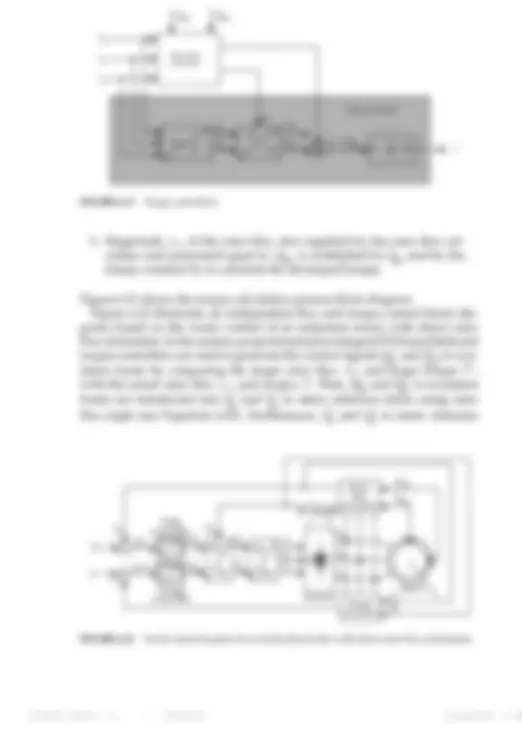
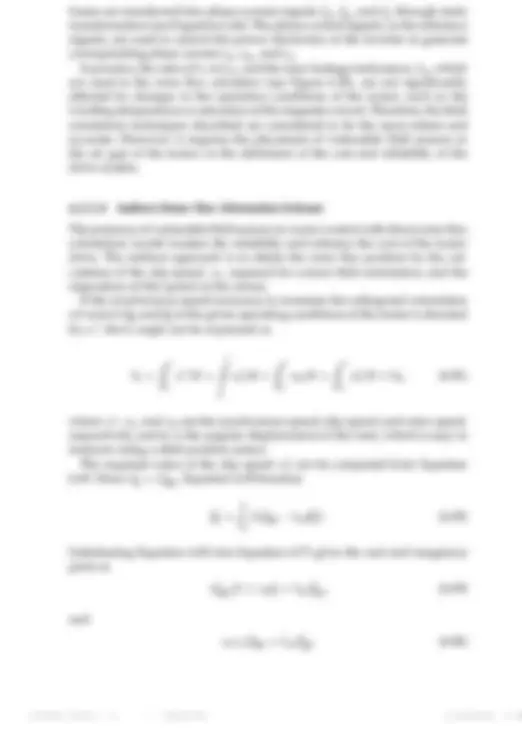
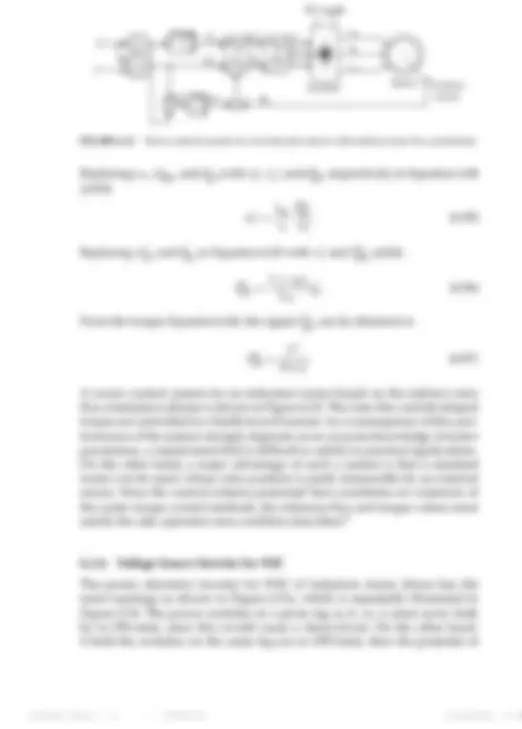
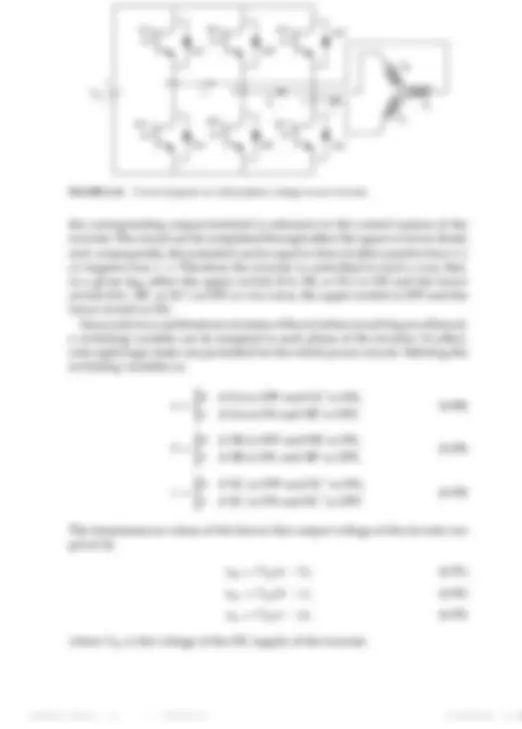
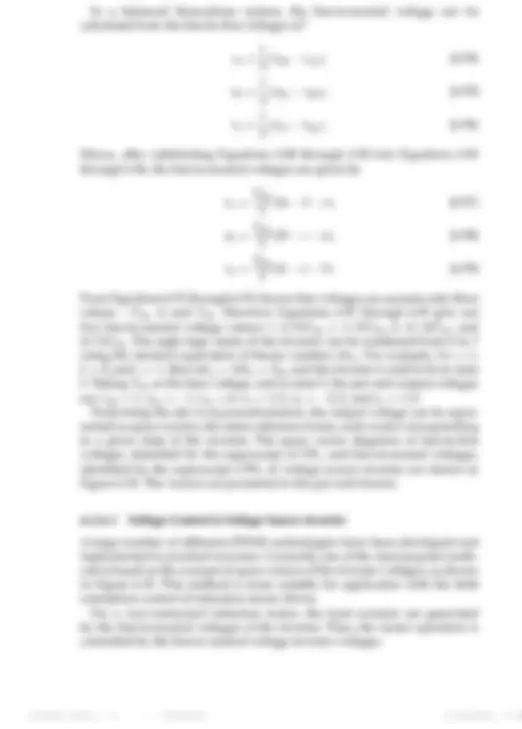
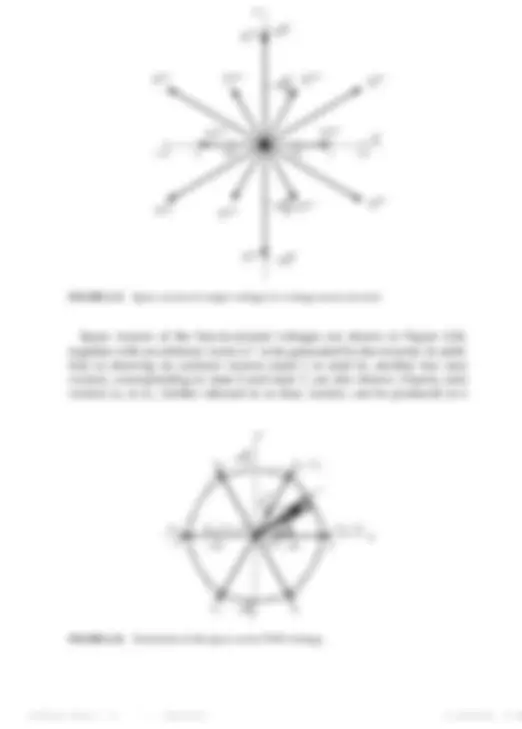

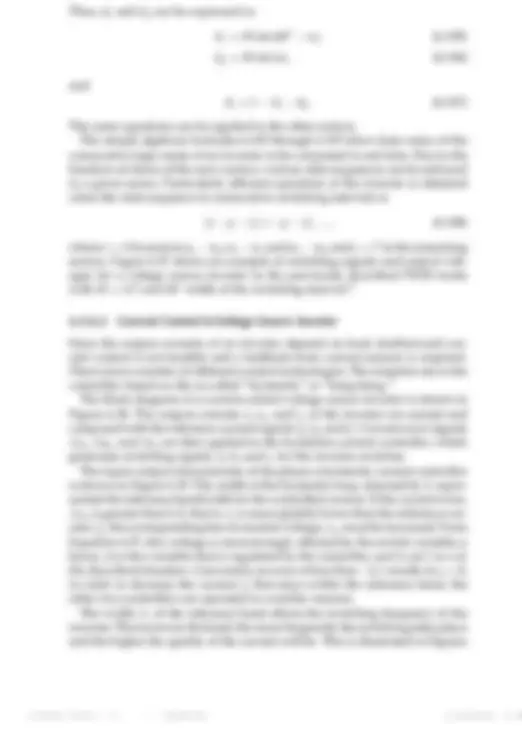
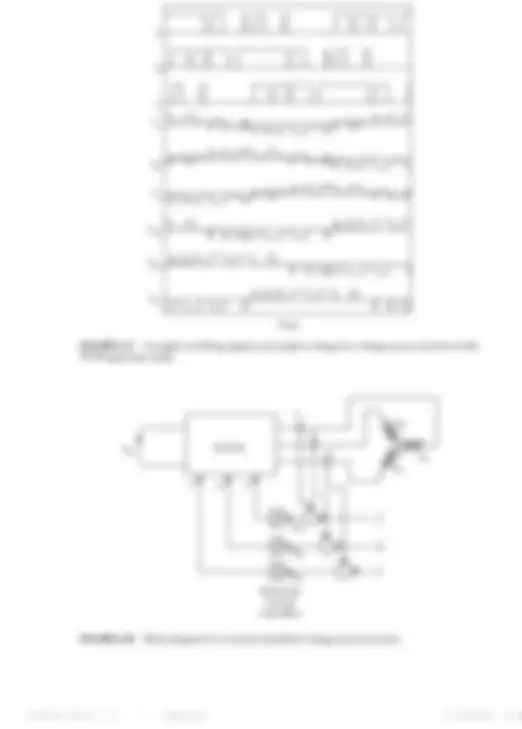
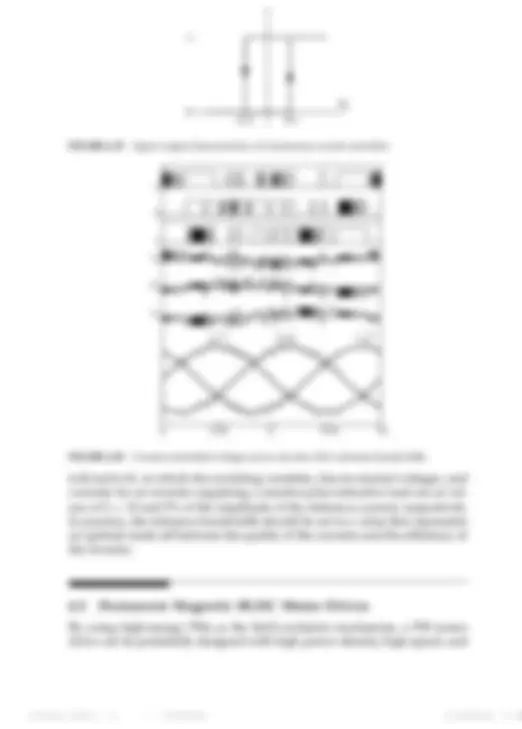
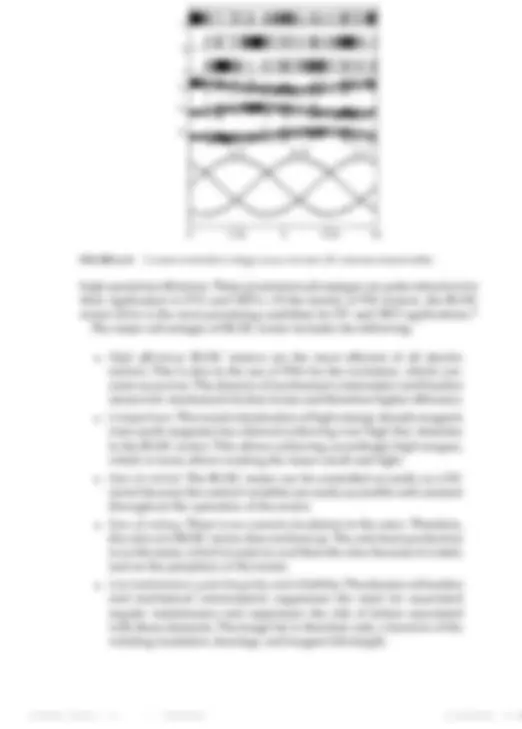
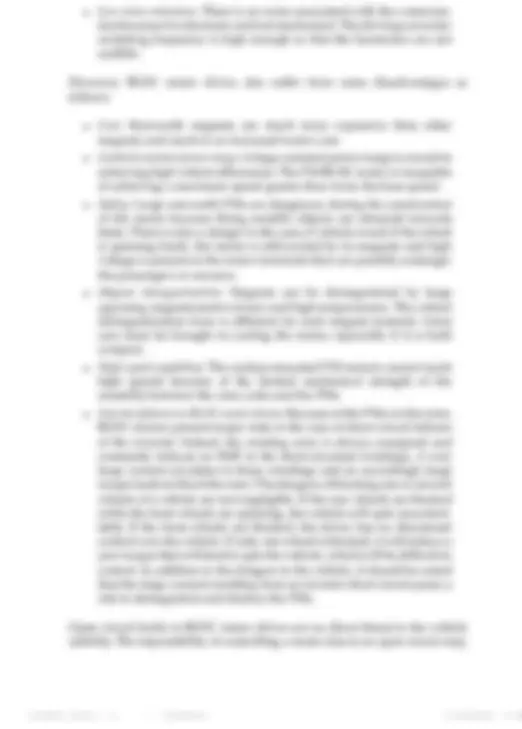
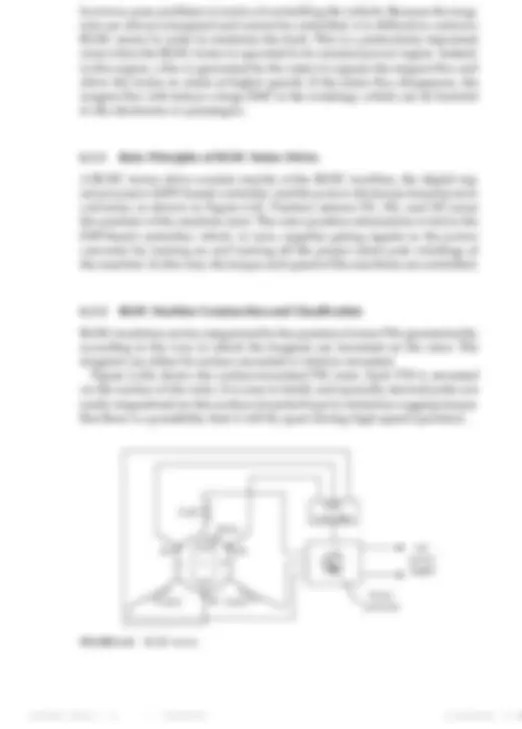
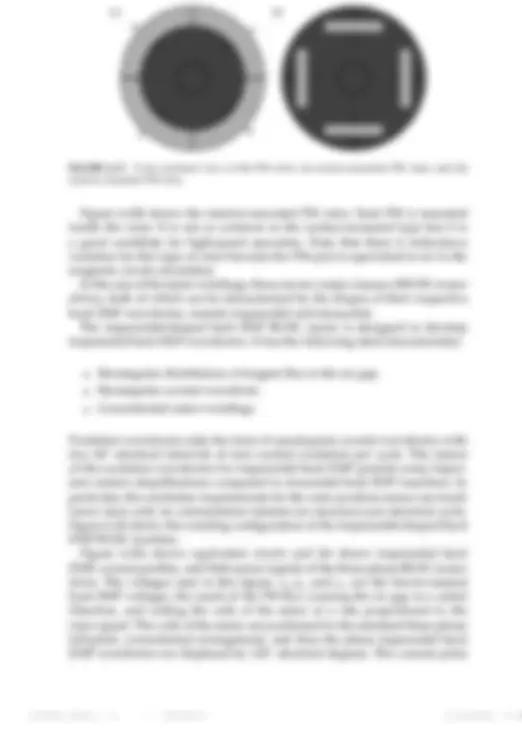
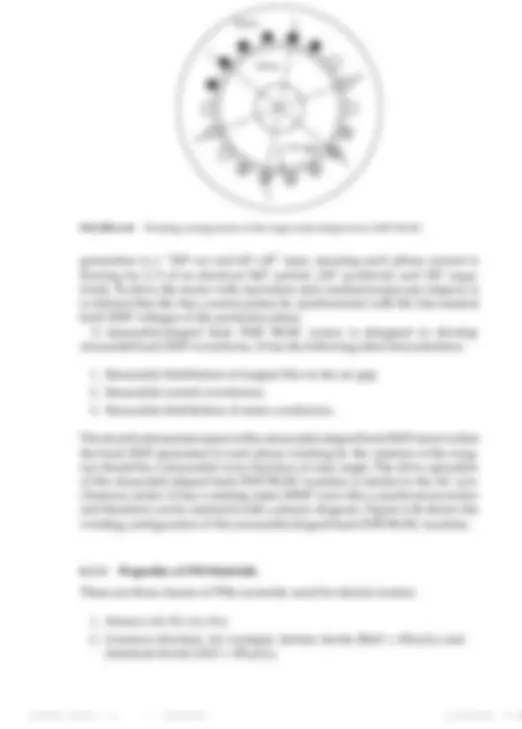
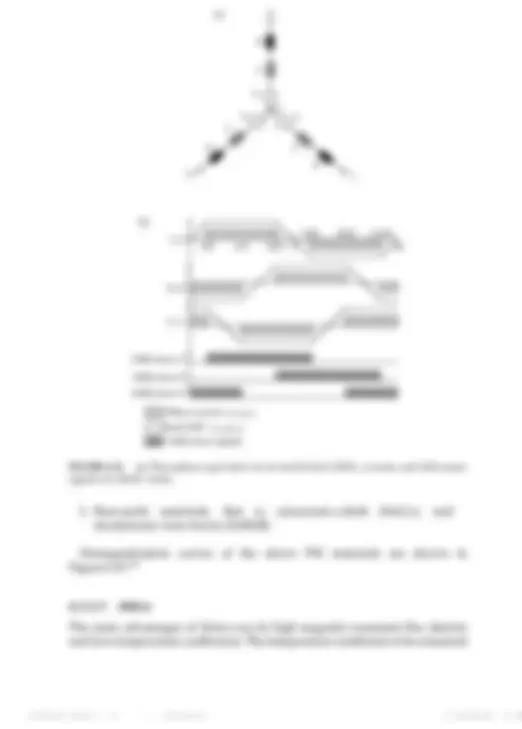
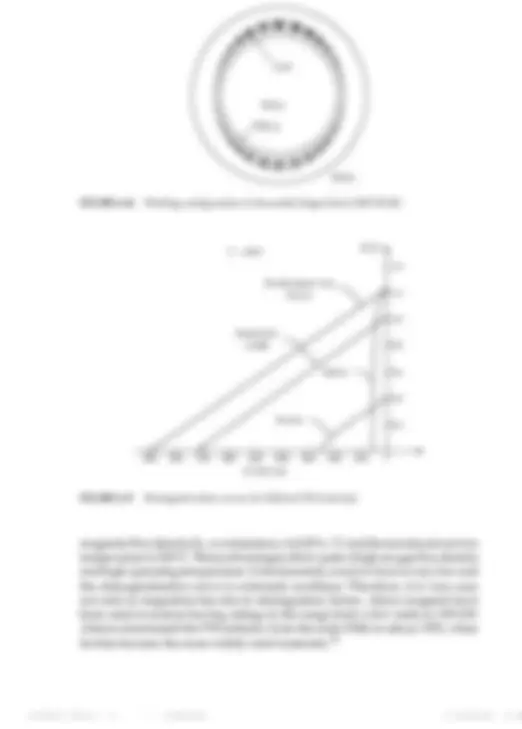

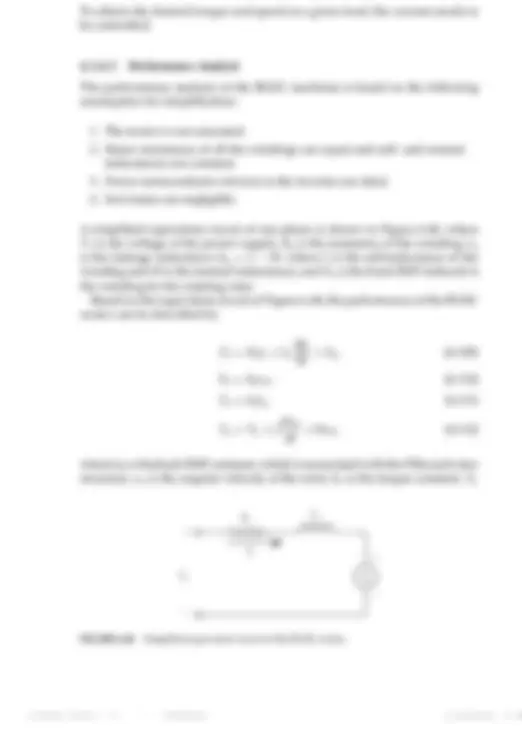
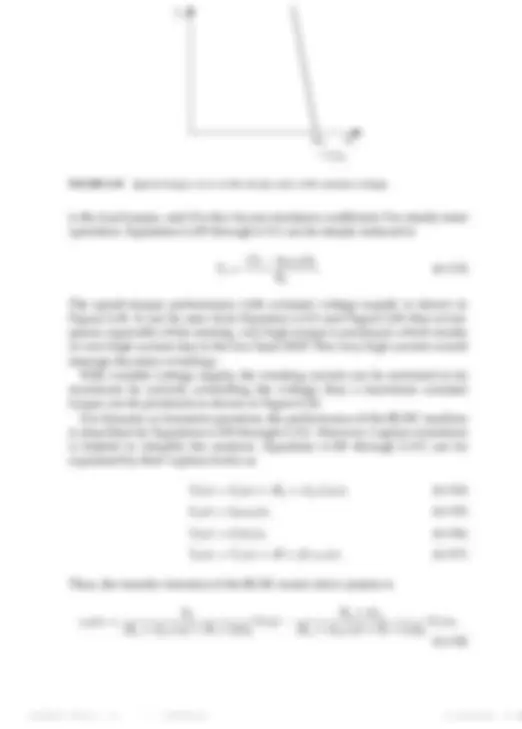
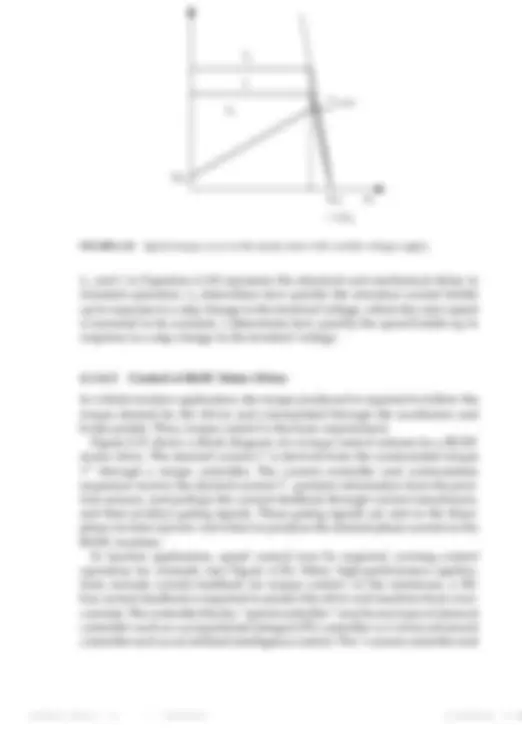
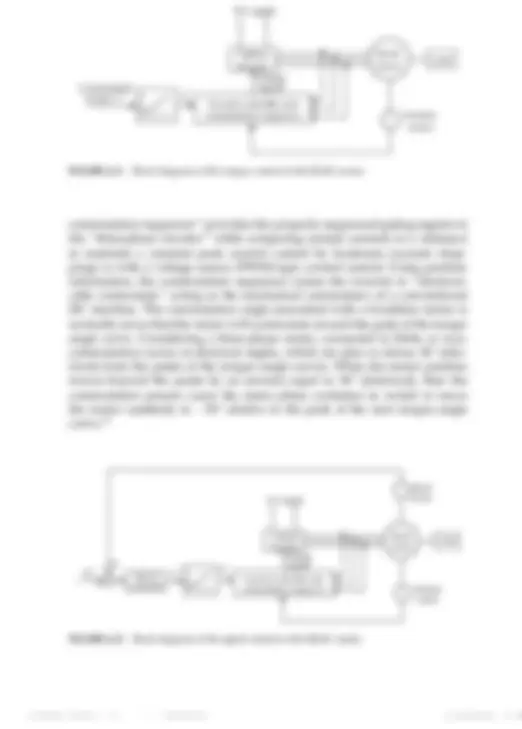
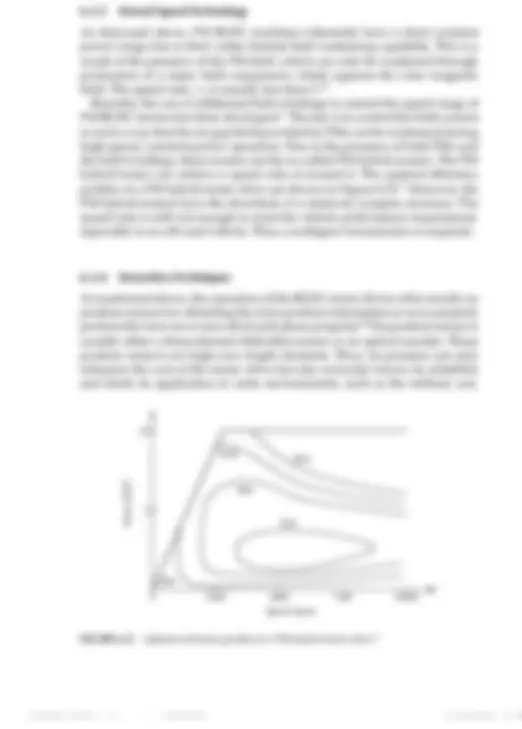
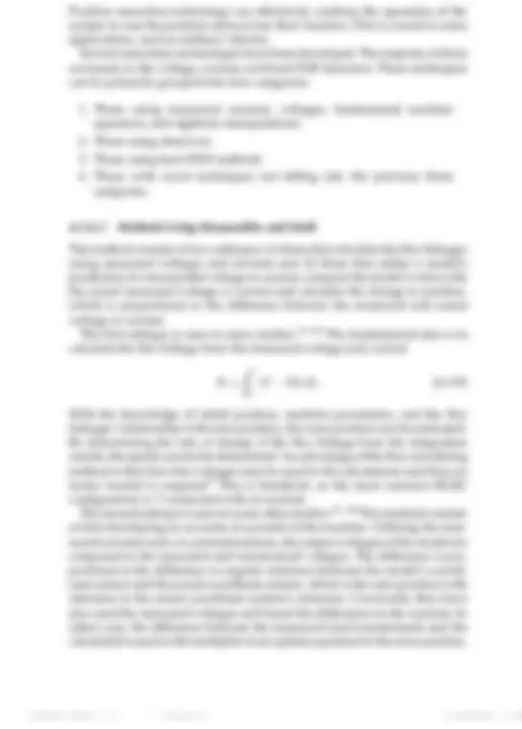
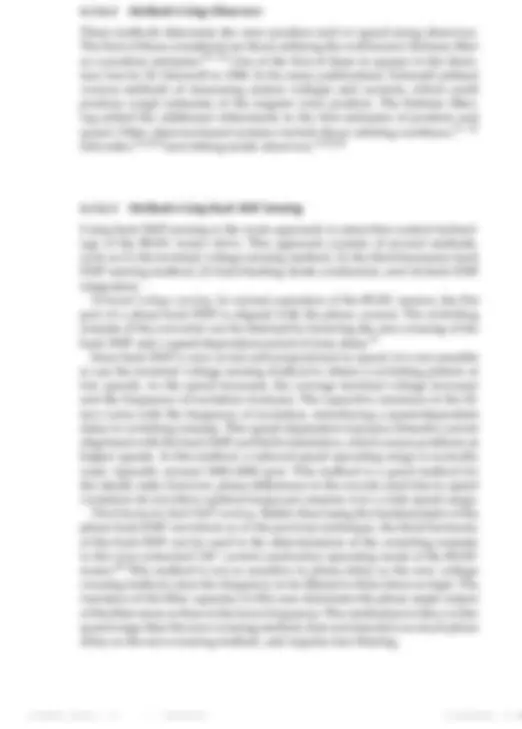
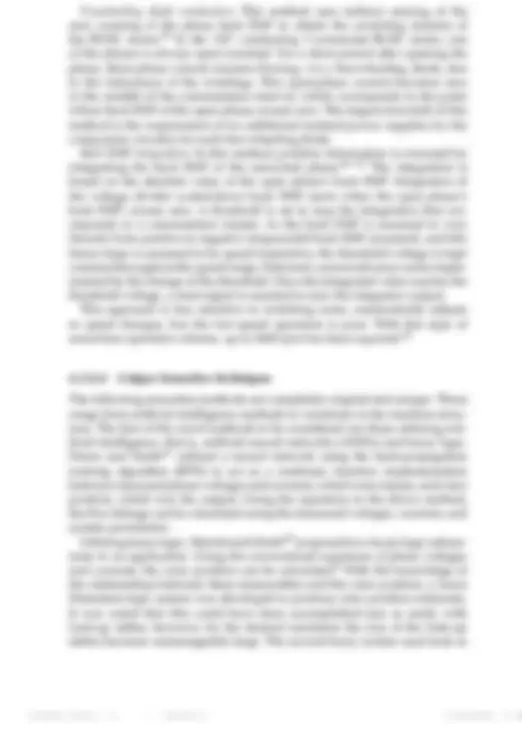
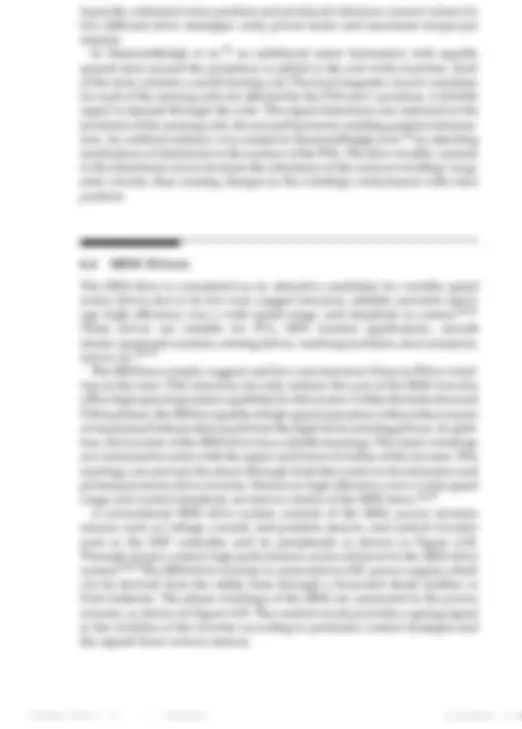
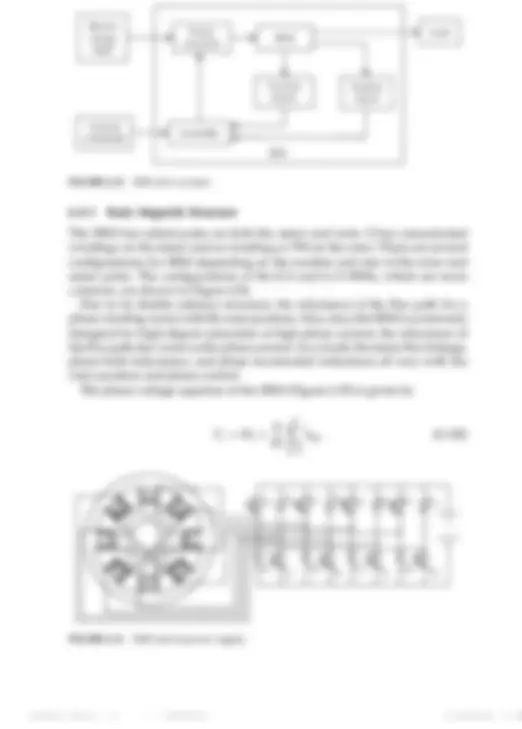
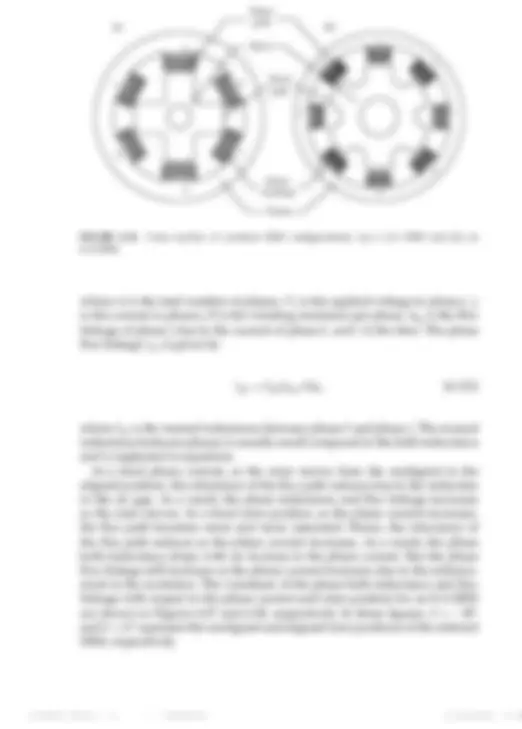
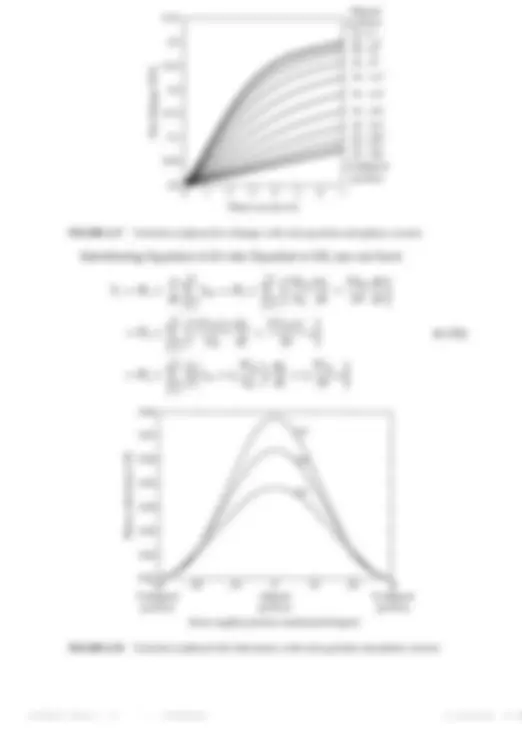
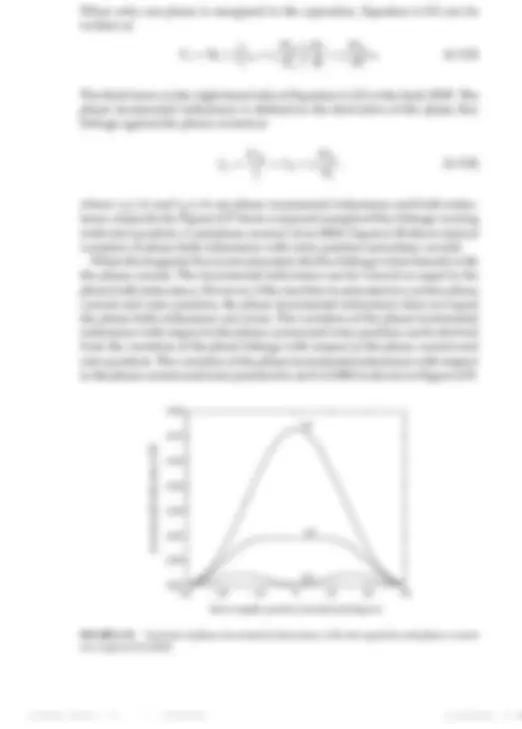
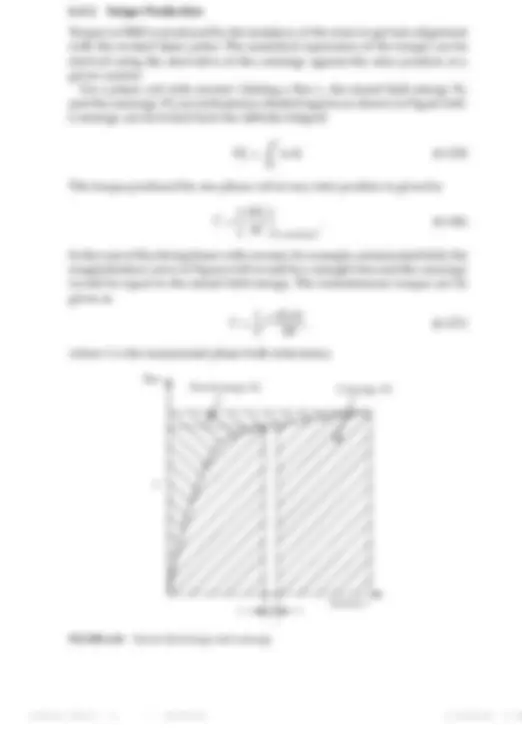
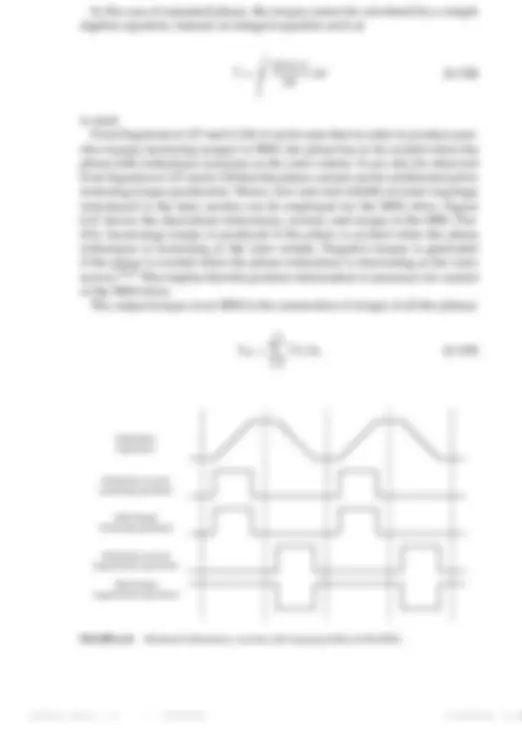
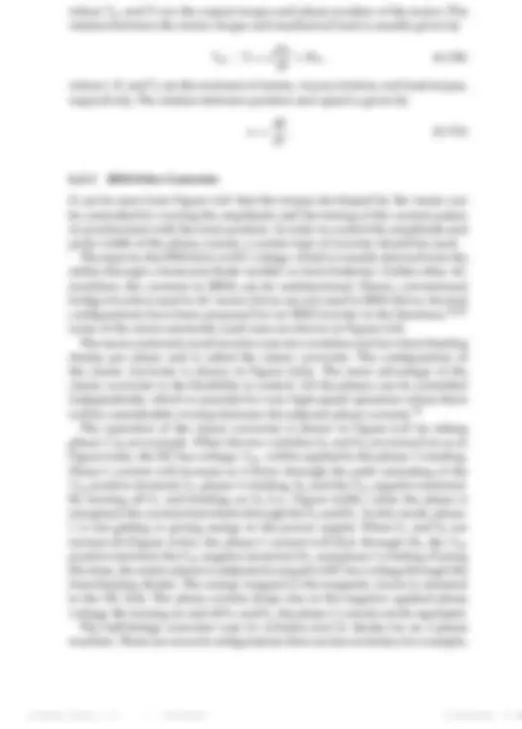
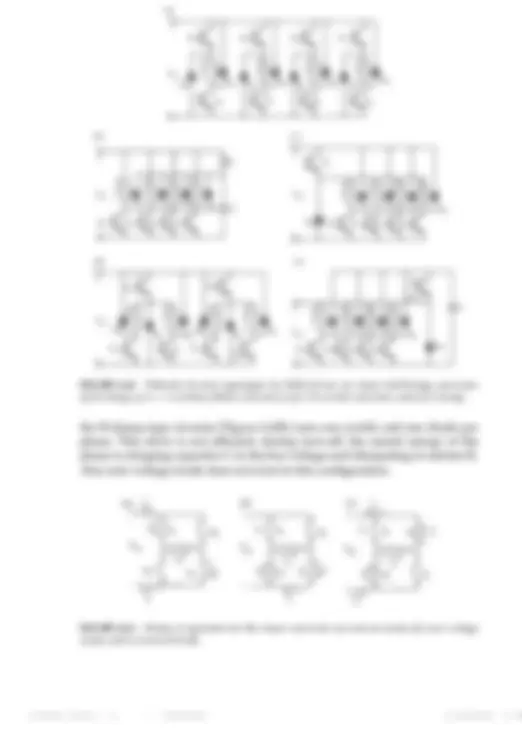
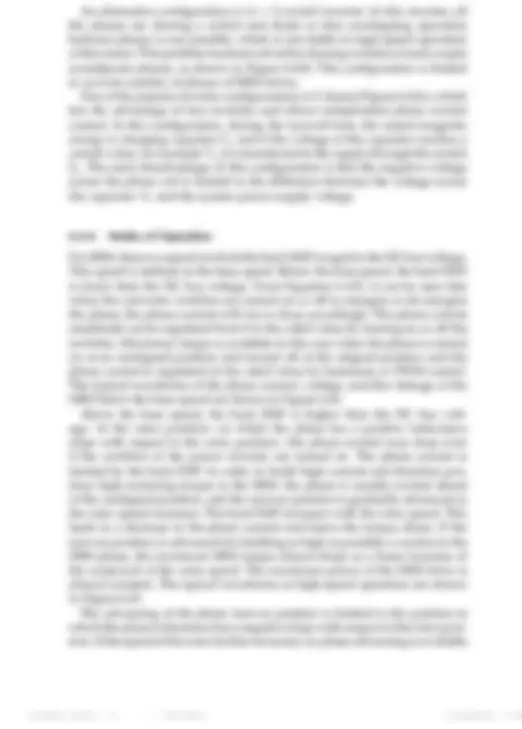
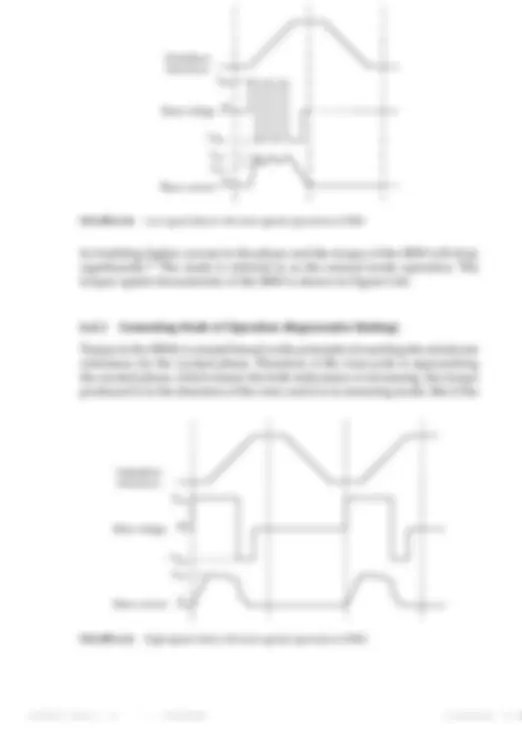
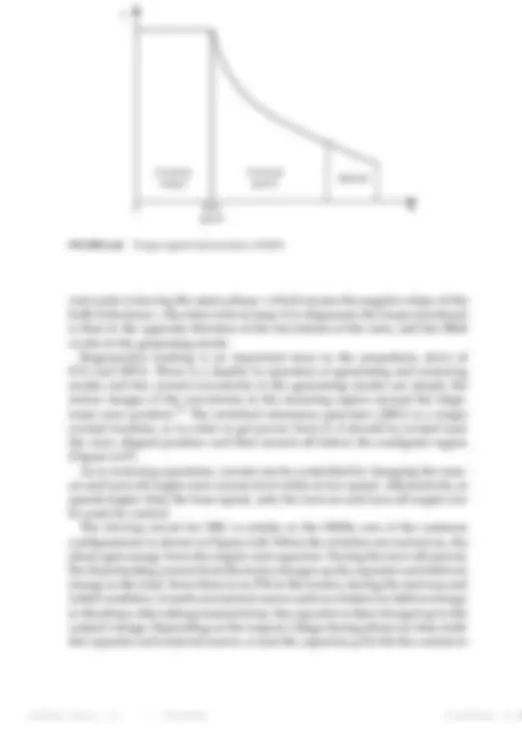
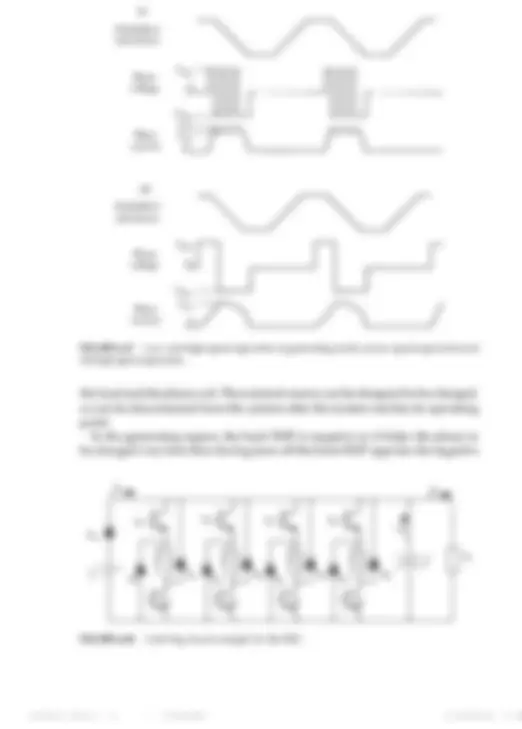
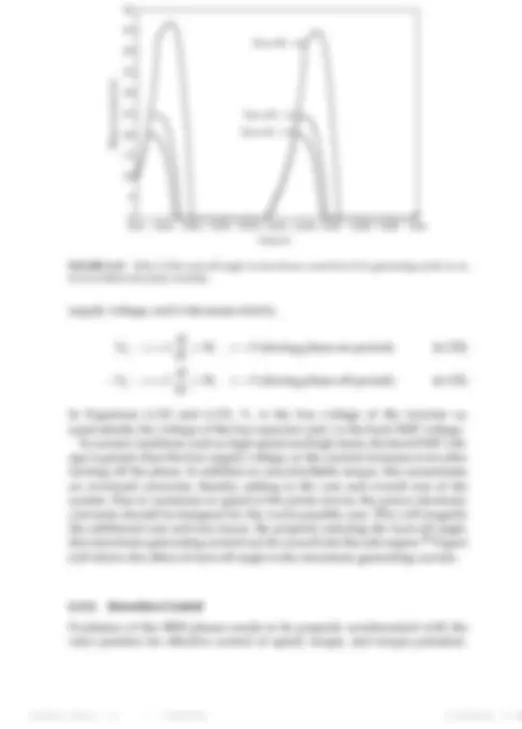
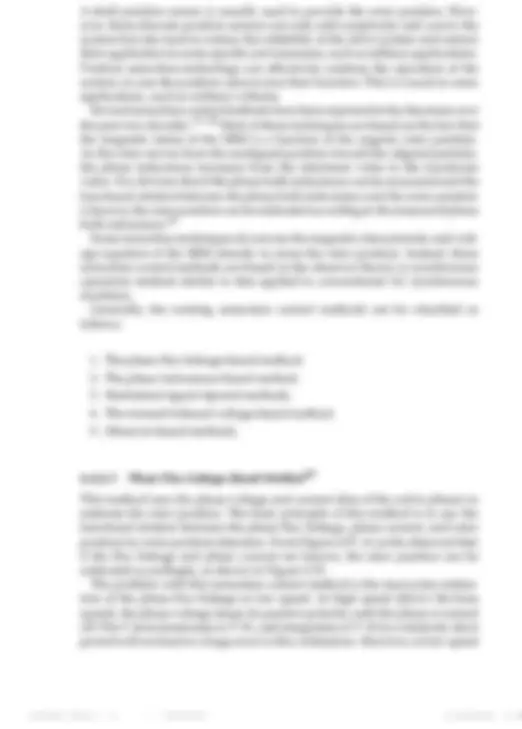
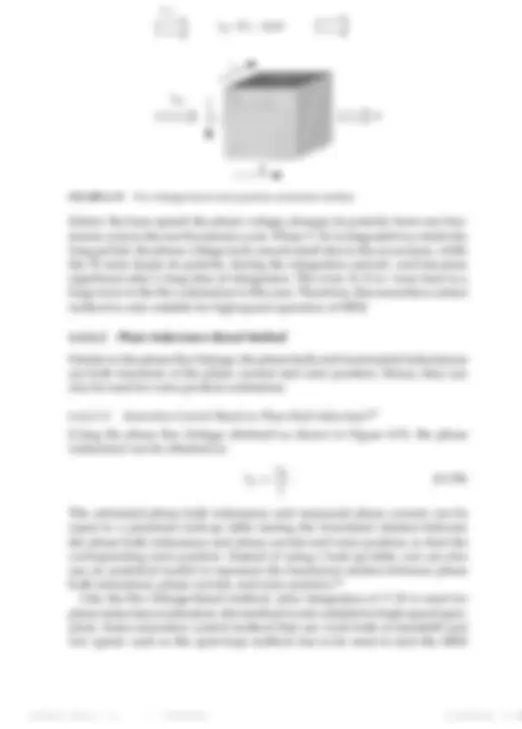
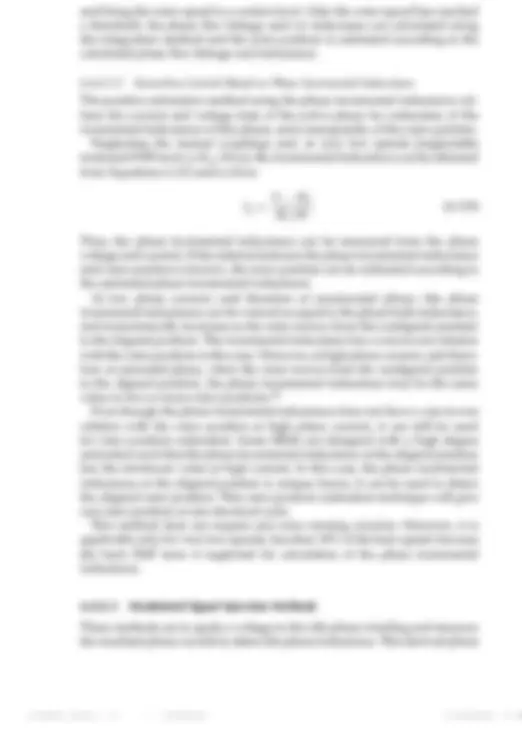
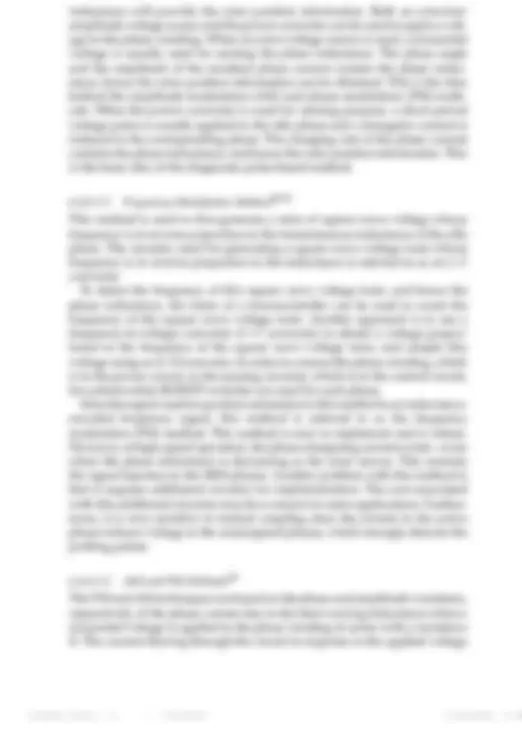
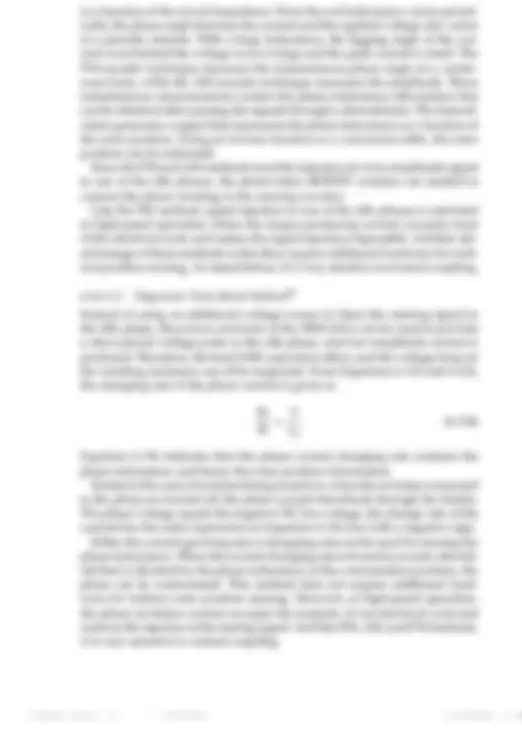
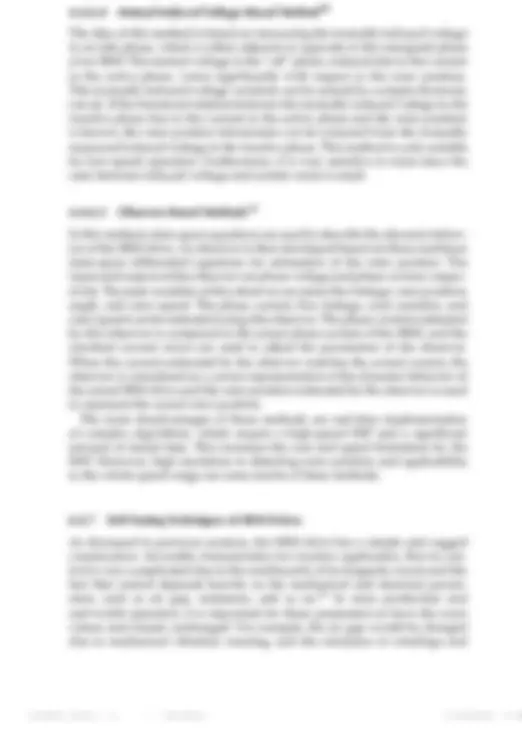
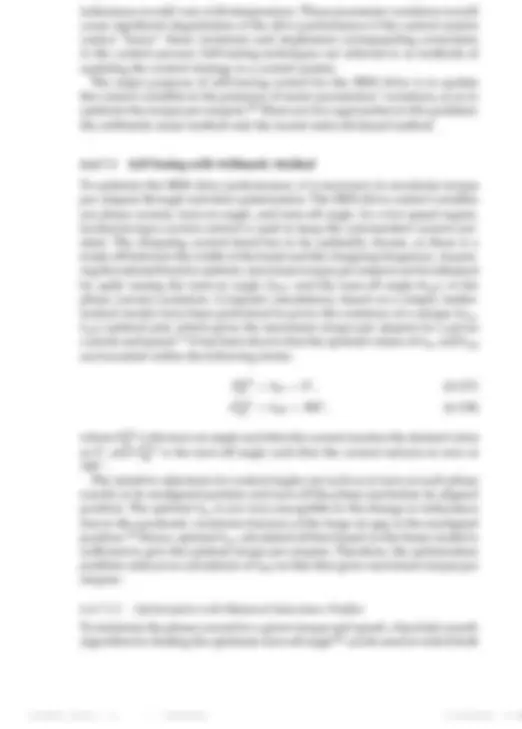
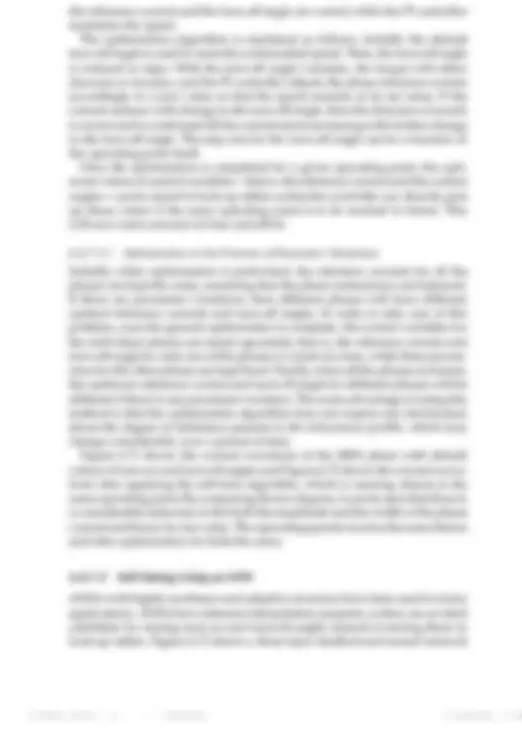
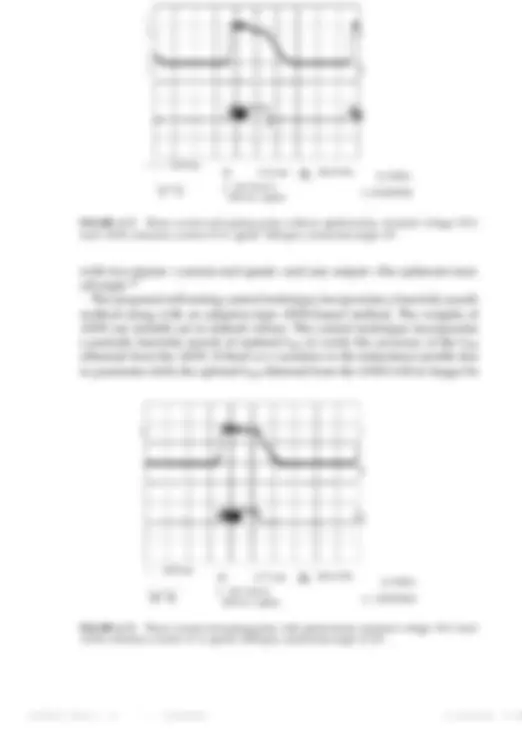

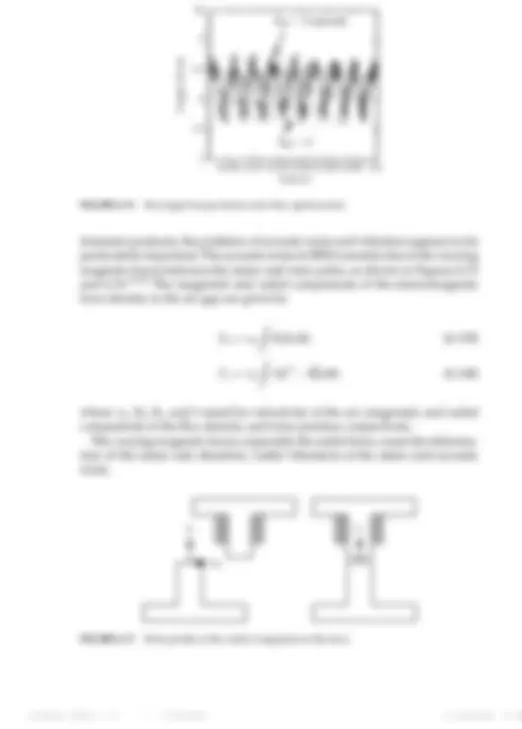
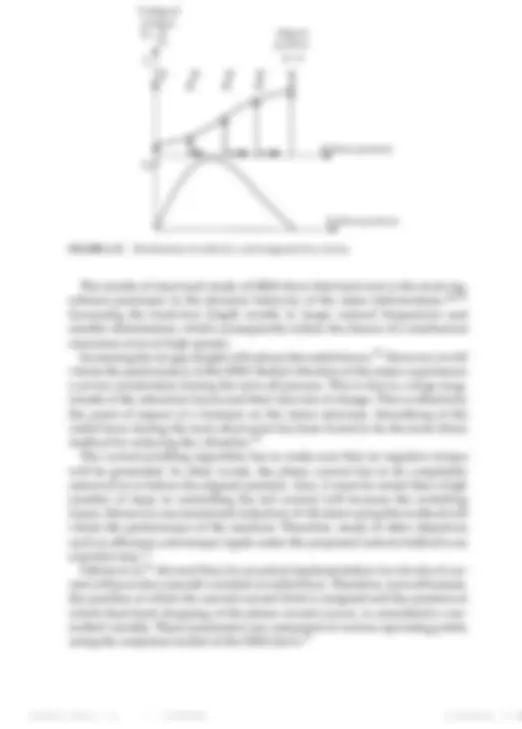
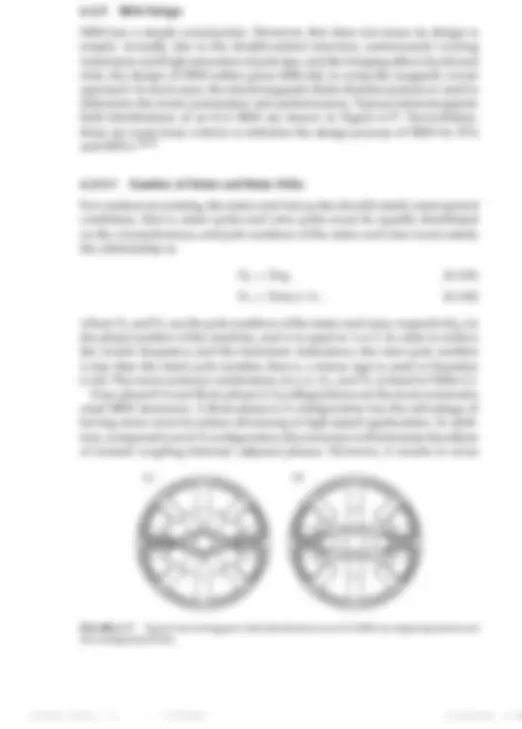
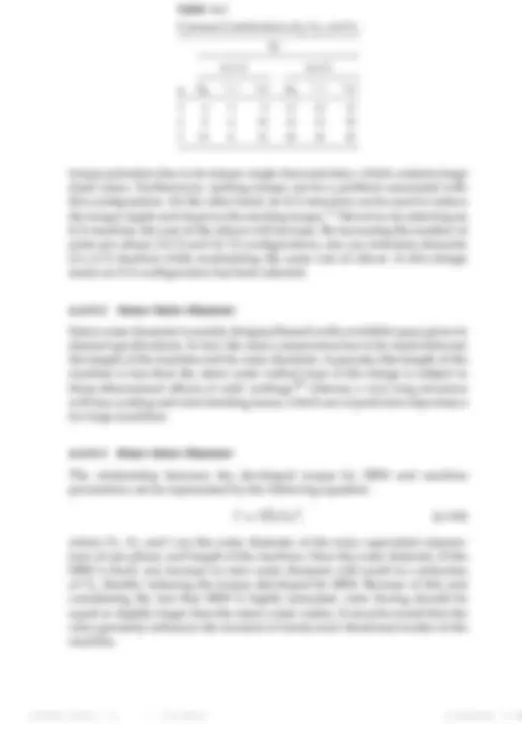
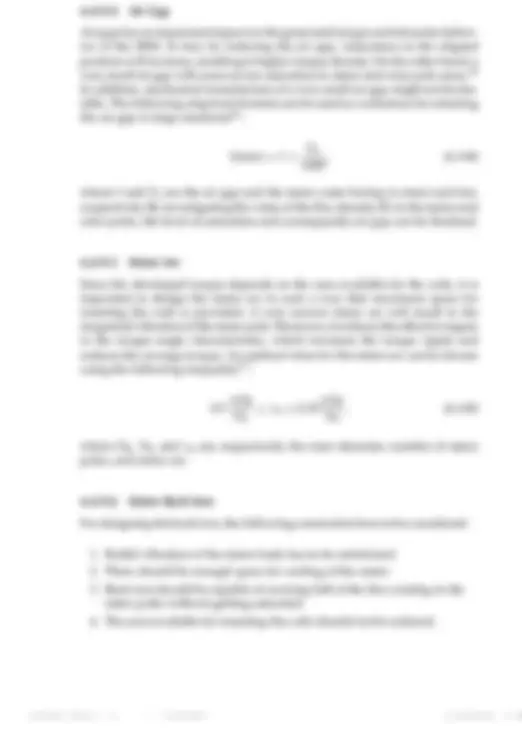
Study with the several resources on Docsity
Earn points by helping other students or get them with a premium plan
Prepare for your exams
Study with the several resources on Docsity
Earn points to download
Earn points by helping other students or get them with a premium plan
Community
Ask the community for help and clear up your study doubts
Discover the best universities in your country according to Docsity users
Free resources
Download our free guides on studying techniques, anxiety management strategies, and thesis advice from Docsity tutors
An electric vehicle (EV)[note 1] is a vehicle that uses one or more electric motors for propulsion. It can be powered by a collector system, with electricity from extravehicular sources, or it can be powered autonomously by a battery (sometimes charged by solar panels, or by converting fuel to electricity using fuel cells or a generator).[1] EVs include, but are not limited to, road and rail vehicles, surface and underwater vessels, electric aircraft , and electric spacecraft.
Typology: Study notes
1 / 96
This page cannot be seen from the preview
Don't miss anything!
Electric propulsion systems are at the heart of EVs and HEVs. They consist of electric motors, power converters, and electronic controllers. The electric motor converts the electric energy into mechanical energy to propel the vehi- cle or vice versa, to enable regenerative braking and/or to generate electricity for the purpose of charging the on-board energy storage. The power converter is used to supply the electric motor with proper voltage and current. The elec- tronic controller commands the power converter by providing control signals to it, and then controls the operation of the electric motor to produce proper torque and speed, according to the command from the driver. The electronic controller can be further divided into three functional units—sensor, inter- face circuitry, and processor. The sensor is used to translate the measurable quantities, such as current, voltage, temperature, speed, torque, and flux, into electric signals through the interface circuitry. These signals are conditioned to the appropriate level before being fed into the processor. The processor output signals are usually amplified via the interface circuitry to drive power semiconductor devices of the power converter. The functional block diagram of an electric propulsion system is illustrated in Figure 6.1. The choice of electric propulsion systems for EVs and HEVs mainly depends on a number of factors, including the driver’s expectation, vehicle constraints, and energy source. The driver’s expectation is defined by a driving profile, which includes the acceleration, maximum speed, climbing capability, brak- ing, and range. The vehicle constraints, including volume and weight, depend on the vehicle type, vehicle weight, and payload. The energy source relates to batteries, fuel cells, ultracapacitors, flywheels, and various hybrid sources. Thus, the process of identifying the preferred feature and package options for electric propulsion has to be carried out at the system level. The interaction of subsystems and the likely impacts of system trade-offs must be examined. Differing from the industrial applications of motors, the motors used in EVs and HEVs usually require frequent starts and stops; high rates of accelera- tion/deceleration; high torque and low-speed hill climbing; low torque and high-speed cruising, and a very wide speed range of operation. The motor drives for EVs and HEVs can be classified into two main groups, namely the commutator motors and commutatorless motors, as illustrated in Figure 6.2. Commutator motors mainly are the traditional DC motors, which include
151
the desired performance. With the advent of the power electronics and microcomputer era, the principle of field-oriented control (FOC) or vector control of induction motors has been accepted to overcome their control com- plexity due to their nonlinearity.^2 However, these EV and HEV motors using FOC still suffer from low efficiency at light loads and limited constant-power operating range. By replacing the field winding of conventional synchronous motors with PMs, PM synchronous motors can eliminate conventional brushes, slip rings, and field copper losses. 3 Actually, these PM synchronous motors are also called PM brushless AC motors, or sinusoidal-fed PM brushless motors, because of their sinusoidal AC current and brushless configuration. Since these motors are essentially synchronous motors, they can run from a sinusoidal or pulsed waveform modulation supply (PWM supply) without electronic commutation. When PMs are mounted on the rotor surface, they behave as nonsalient synchronous motors because the permeability of PMs is similar to that of air. By burying those PMs inside the magnetic circuit of the rotor, the saliency causes an additional reluctance torque, which leads to facil- itating a wider speed range at constant power operation. On the other hand, by abandoning the field winding or PMs while purposely making use of the rotor saliency, synchronous reluctance motors are generated. These motors are generally simple and inexpensive, but with relatively low output power. Similar to induction motors, these PM synchronous motors usually use FOC for high-performance applications.^3 Because of their inherently high power density and high efficiency, they have been accepted as having great potential to compete with induction motors for EV and HEV applications. By virtually inverting the stator and rotor of PM DC motors (commutator), PM brushless DC (BLDC) motors are generated. It should be noted that the term “DC” may be misleading, since it does not refer to a DC current motor. Actually, these motors are fed by rectangular AC current and hence are also rectangular-fed PM brushless motors.^4 The most obvious advantage of these motors is the removal of brushes. Another advantage is the ability to produce a large torque because of the rectangular interaction between current and flux. Moreover, the brushless configuration allows more cross-sectional area for the armature windings. Since the conduction of heat through the frame is improved, an increase in electric loading causes higher power density. Differ- ent from PM synchronous motors, these PM BLDC motors generally operate with shaft position sensors. Recently, sensorless control technologies have been developed in the Power Electronics and Motor Drive Laboratory at Texas A&M University. Switched reluctance motors (SRMs) have been recognized to have con- siderable potential for EV and HEV applications. Basically, they are direct derivatives of single-stack variable-reluctance stepping motors. SRMs have the definite advantages of simple construction, low manufacturing cost, and outstanding torque–speed characteristics for EV and HEV applications. Although they possess simplicity in construction, this does not imply any
simplicity of their design and control. Because of the heavy saturation of pole tips and the fringe effect of pole and slots, their design and control are difficult and subtle. Traditionally, SRMs operate with shaft sensors to detect the relative position of the rotor to the stator. These sensors are usu- ally vulnerable to mechanical shock and sensitive to temperature and dust. Therefore, the presence of the position sensor reduces the reliability of SRMs and constrains some applications. Recently, sensorless technologies have been developed in the Power Electronics and Motor Drive Laboratory—again, at Texas A&M University. These technologies can ensure smooth operation from zero speed to maximum speed. 5 This will be discussed in detail in the following sections.
DC motor drives have been widely used in applications requiring adjustable speed; good speed regulation; and frequent starting, braking, and revers- ing. Various DC motor drives have been widely applied to different electric traction applications because of their technological maturity and control simplicity.
6.1.1 Principle of Operation and Performance
The operation principle of a DC motor is straightforward. When a wire car- rying electric current is placed into a magnetic field, a magnetic force acting on the wire is produced. The force is perpendicular to the wire and the mag- netic field as shown in Figure 6.3. The magnetic force is proportional to the wire length, magnitude of the electric current, and the density of the magnetic field; that is,
F = BIL. (6.1)
When the wire is shaped into a coil, as shown in Figure 6.3, the magnetic forces acting on both sides produce a torque, which is expressed as
T = BIL cos α, (6.2)
where α is the angle between the coil plane and the magnetic field as shown in Figure 6.3. The magnetic field may be produced by a set of windings or PMs. The former is called wound-field DC motor and the latter is called the PM DC motor. The coil carrying electric current is called the armature. In practice, the armature consists of a number of coils. In order to obtain continuous and
Ia
Ia
A 1
S (^1)
Ia^ Ia
S (^2) A 1 F (^1)
S 1 S
F (^2)
A
A 2 A
F1 F
F 2 F (^2) Separately Shunt
Series Cumulative compound
If
If
Va Vf Va
Va Va
A
(^) +
FIGURE 6.4 Wound-field DC motors.
a DC motor are
V a = E + R a I a , E = K eφωm (6.3) T = K eφ I a , (6.4)
where φ is the flux per pole in webers, I a is the armature current in A, V a is the armature voltage in volts, R a is the resistance of the armature circuit in ohms, ωm is the speed of the armature in rad/s, T is the torque developed by the motor in N m, and K e is a constant.
Va
Ra
E = Ke f wm
Ia
FIGURE 6.5 Steady-state equivalent circuit of the armature circuit of a DC motor.
Separately excited or Series Compound shunt
Speed, p.u.
Torque, p.u.
0
0.5 1.
FIGURE 6.6 Speed characteristics of DC motors.
From Equations 6.3 and 6.4, one can obtain
K eφ R a
( K eφ)^2 R a
ωm. (6.5)
Equations 6.3 through 6.5 are applicable to all the DC motors, namely sep- arately (or shunt) excited, series, and compound motors. In the case of separately excited motors, if the field voltage is maintained as constant, one can assume the flux to be practically constant as the torque changes. In this case, the speed–torque characteristic of a separately excited motor is a straight line, as shown in Figure 6.6. The nonload speed ωm is determined by the arma- ture voltage and the field excitation. Speed decreases as torque increases, and speed regulation depends on the armature circuit resistance. Separately excited motors are used in applications requiring good speed regulation and proper adjustable speed. In the case of series motors, the flux is a function of armature current. In an unsaturated region of the magnetization characteristic, φ can be assumed to be proportional to I a. Thus
φ = K f I a. (6.6)
By Equations 6.4 through 6.6, the torque for series excited DC motors can obtained as
K e K f V a^2 ( R a + K e K f ωm)^2
Power
Torque
(^0) Base speed
Armature current
Maximum speed (^) wm Armature Field control voltage control
FIGURE 6.7 Torque and power limitations in combined armature voltage and field control.
the separately excited DC motors are usually used in traction, due to the control flexibility of armature voltage and field. For a DC motor control in open-loop and closed-loop configurations, the chopper offers a number of advantages due to the high operation frequency. High operation frequency results in high-frequency output voltage ripple and therefore less ripples in the motor armature current and a smaller region of discontinuous conduction in the speed–torque plane. A reduction in the armature current ripple reduces the armature losses. A reduction or elimina- tion of the discontinuous conduction region improves speed regulation and transient response of the drive. The power electronic circuit and the steady-state waveform of a DC chopper drive are shown in Figure 6.8. A DC voltage source, V , supplies an inductive load through a self-commutated semiconductor switch S. The symbol of a self- commutated semiconductor switch has been used because a chopper can be built using any devices among thyristors with a forced commutation circuit: GTO, power transistor, MOSFET, and IGBT. The diode shows the direction in which the device can carry current. A diode D F is connected in parallel with the load. The semiconductor switch S is operated periodically over a period T and remains closed for a time t on = δ T with 0 < δ < 1. The variable δ = t on/ T is called the duty ratio or duty cycle of a chopper. Figure 6.8 also shows the waveform of control signal i c. Control signal i c will be the base current for a transistor chopper, and a gate current for the GTO of a GTO chopper or the main thyristor of a thyristor chopper. If a power MOSFET is used, it will be a gate to the source voltage. When the control signal is present, the semiconductor switch S will conduct, if forward biased. It is assumed that the circuit operation has been arranged such that the removal of i c will turn off the switch.
Self commutated semiconductor switch
Va Load
Va
Va T
T
0
0
d T
d T
t
t
(^0) d T T t
(^0) d T T t
V
V DF
ic
is
ic
ia
ia
is
ia
ia ia
ia
(a)
(b)
(c)
(d)
(e)
FIGURE 6.8 Principle of operation of a step down (or class A) chopper: (a) basic chopper circuit; (b)–(e) waveforms.
During the on interval of the switch (0 ≤ t ≤ δ T ), the load is subjected to a voltage V and the load current increases from i a1 to i a2. The switch is opened at t = δ T. During the off period of the switch (δ T ≤ t ≤ 1), the load inductance maintains the flow of current through diode D F. The load terminal voltage stays zero (if the voltage drop on the diode is ignored in comparison to V ) and the current decreases from i a2 to i a1. The internal 0 ≤ t ≤ δ T is called the duty interval and the interval δ T ≤ t ≤ T is known as the freewheeling interval. Diode D F provides a path for the load current to flow when switch S is off, and thus improves the load current waveform. Furthermore, by maintaining the continuity of the load current at turn-off, it prevents transient voltage from appearing across switch S, due to the sudden change of the load current. The source current waveform is also shown in Figure 6.8e. The source current flows only during the duty interval and is equal to the load current. The direct component or average value of the load voltage V a is given by
V a =
0
v a d t =
∫ (^) δ T
0
V d t = δ V. (6.8)
By controlling δ between 0 and 1, the load voltage can be varied from 0 to V ; thus a chopper allows a variable DC voltage to be obtained from a fixed voltage DC source.
The chopper of Figure 6.8 is called a class A chopper. It is one of the number of chopper circuits that are used for the control of DC motors. This chopper is capable of providing only a positive voltage and a positive current. It is called a single-quadrant chopper, only providing separately excited DC motor control in the first quadrant, that is, positive speed and positive torque. Since it can vary the output voltage from V to 0, it is also a step-down chopper or a DC- to-DC buck converter. The basic principle involved can also be used to realize a step-up chopper or DC-to-DC boost converter. The circuit diagram and steady-state waveforms of a step-up chopper are shown in Figure 6.9. This chopper is known as a class B chopper. The presence of control signal i c indicates the duration for which the switch can conduct if forward-biased. During a chopping period T , it remains closed for an interval 0 ≤ t ≤ δ T and remains open for an interval δ T ≤ t ≤ T. During the on period, i S increases from i S1 to i S2 , thus increasing the magnitude of energy stored in inductance L. When the switch is opened, current flows through the parallel combination of the load and capacitor C. Since the current is forced against the higher voltage, the rate of change of the current is negative. It decreases from i S2 to i S1 in the switch’s off period. The energy stored in the inductance L and the energy supplied by the low-voltage source are given to the load. The capacitor C serves two purposes. At the instant of opening of switch S, the source current, i S , and load current, i a , are not the same. In the absence of C, the turn-off of S will force the two currents to have the same values. This will cause high induced voltage in the inductance L and the load inductance. Another reason for using capacitor C is to reduce the load voltage ripple. The purpose of the diode D is to prevent any flow of current from the load into switch S or source V.
L
0 d^ T^ T t
0 d T T t
d T T
(a)
(b)
(c)
(d)
0 t
V Va Va
iS iS iS
Load
b
S C
a D
ic
is
ic
FIGURE 6.9 Principle of operation of a step-up (or class B) chopper: (a) basic chopper circuit; (b)–(d) waveforms.
For understanding of the step-up operation, capacitor C is assumed large enough to maintain a constant voltage V a across the load. The average voltage across the terminals a and b is given as
V ab =
0
v ab d t = V a( 1 − δ). (6.9)
The average voltage across the inductance L is
0
d i d t
d t =
∫ (^) i S
i S
L d i = 0. (6.10)
The source voltage
V = VL + V ab. (6.11)
Substituting from Equations 6.9 and 6.10 into Equation 6.11 gives
V = V a( 1 − δ) or V a =
1 − δ
According to Equations 6.12, theoretically the output voltage V a can be changed from V to ∞ by controlling δ from 0 to 1. In practice, V a can be controlled from V to a higher voltage, which depends on the capacitor C, and the parameters of the load and chopper. The main advantage of a step-up chopper is the low ripple in the source current. While most applications require a step-down chopper, the step-up chopper finds application in low-power battery-driven vehicles. The principle of the step-up chopper is also used in the regenerative braking of DC motor drives.
6.1.4 Multi-Quadrant Control of Chopper-Fed DC Motor Drives
The application of DC motors on EVs and HEVs requires the motors to operate in multiquadrants, including forward motoring, forward braking, backward motoring, and backward braking, as shown in Figure 6.10. For vehicles with reverse mechanical gears, two-quadrant operation (forward motoring and forward braking, or quadrant I and quadrant IV) is required. However, for the vehicles without reverse mechanical gears, four-quadrant operation is needed. Multiquadrant operation of a separately excited DC motor is imple- mented by controlling the voltage poles and magnitude through power electronics-based choppers.
period of the switch S, the motor current flows through a path consisting of the motor armature, switch S, and diode D 1 , and increases the energy stored in the armature circuit inductance. When S is opened, the current flows through the armature diode D 2 , source V , diode D 1 and back to the armature, thus feeding energy into the source. During motoring, the change over to regeneration is done in the following steps. Switch S is deactivated and switch C is opened. This forces the armature current to flow through diode D 2 , source V and diode D 1. The energy stored in the armature circuit is fed back to the source and the armature current falls to zero. After an adequate delay to ensure that the current has indeed become zero, the armature connection is reversed and switch S is reactivated with a suitable value of δ to start regeneration.
6.1.4.1.2 Class C Two-Quadrant Chopper
In some applications, a smooth transition from motoring to braking and vice versa is required. For such applications, the class C chopper is used as shown in Figure 6.12. The self-commutated semiconductor switch S 1 and diode D 1 constitute one chopper and the self-commutator switch S 2 , and diode D (^2) form another chopper. Both the choppers are controlled simultaneously, both for motoring and regenerative braking. The switches S 1 and S 2 are closed alternately. In the chopping period T , S 1 is kept on for a duration δ T and S 2 is kept on from δ T to T. To avoid a direct short-circuit across the source, care is taken to ensure that S 1 and S 2 do not conduct at the same time. This is generally achieved by providing some delay between the turn-off of one switch and the turn-on of another switch. The waveforms of the control signals, v a , i a , and i s and the devices under conducting during different intervals of a chopping period are shown in Figure 6.11b. In drawing these waveforms, the delay between the turn-off of one switch and turn-on of another switch has been ignored because it is usually very small. The control signals for the switches S 1 and S 2 are denoted by i c1 and i c2 , respectively. It is assumed that a switch conducts only when the control signal is present and the switch is forward biased. The following points are helpful in understanding the operation of this two-quadrant circuit.
S 1
D
D
ic
ic
V
(a)
(b)
Va
ic
ic
ia
is
D 2 D 2 D 2
d T T + d T 2 T t
S 1 D 1 S 2 S 1 D 1 S 2
Va V
0
0
0
0
0
ia
is
S 2
T
d T (^) T T + d T 2 T t
d T (^) T T + d T 2 T t
d T (^) T T + d T 2 T t
d T T T + d T 2 T t
FIGURE 6.12 Forward motoring and regenerative braking control using class C two-quadrant chopper: (a) chopper circuit; (b) waveforms.
remaining zero for a finite interval of time. Similarly, the energy trans- fer will be present when S 2 is off and D 2 is conducting—that is, during the interval 0 ≤ t ≤ δ T. If the current falls to zero during this interval, S 1 will conduct immediately because i c is present and V > E. The armature current will flow, preventing discontinuous conduction.
This control method has the following features: the utilization factor of the switches is low due to the asymmetry in the circuit operation. Switches S 3 and S 2 should remain on for a long period. This may create commuta- tion problems when the switches are using thyristors. The minimum output voltage depends directly on the minimum time for which the switch can be closed, since there is always a restriction on the minimum time for which the switch can be closed, particularly in thyristor choppers. 7 The minimum available output voltage, and therefore the minimum available motor speed, is restricted. To ensure that switches S 1 and S 4 , or S 2 and S 3 are not on at the same time, some fixed time interval must elapse between the turn-off for one switch and the turn-on of another switch. This restricts the maximum permissible frequency of operation. It also requires two switching operations during a cycle of the output voltage. Dubey 6 provided other control methods to solve the problems mentioned above.
Commutatorless motor drives offer a number of advantages over conven- tional DC commutator motor drives for the electric propulsions of EVs and HEVs. At present, induction motor drives are the mature technology among commutatorless motor drives. Compared with DC motor drives, the AC induction motor drive has additional advantages such as lightweight nature, small volume, low cost, and high efficiency. These advantages are particularly important for EV and HEV applications. There are two types of induction motors, namely, wound-rotor and squirrel- cage motors. Because of the high cost, need for maintenance, and lack of sturdiness, wound-rotor induction motors are less attractive than their squirrel-cage counterparts, especially for electric propulsion in EVs and HEVs. Hence, squirrel-cage induction motors are loosely named as induction motors. A cross section of a two-pole induction motor is shown in Figure 6.14. Slots in the inner periphery of the stator are inserted with three phase wind- ings, a–a′, b–b′, and c–c′. The turns of each winding are distributed such that the current in the winding produces an approximate sinusoidally distributed flux density around the periphery of the air gap. The three windings are spatially arranged by 120◦^ as shown in Figure 6.14. The most common types of induction motor rotors are the squirrel-cage motors in which aluminum bars are cast into slots in the outer periph- ery of the rotor. The aluminum bars are short-circuited together at both ends of the rotor by cast aluminum end rings, which also can be shaped as fans.
Stator
Rotor bar
Rotor
c ′
a
b ′
c
b
120º
120º
120º
a ′
Stator slot and windings
FIGURE 6.14 Cross section of an induction motor.
6.2.1 Basic Operation Principles of Induction Motors
Figure 6.15 shows, schematically, a cross section of the stator of a three- phase, two-pole induction motor. Each phase is fed with a sinusoidal AC current, which has a frequency of ω and a 120◦^ phase difference between each other. Current i as , i bs , and i cs in the three stator coils a–a′, b–b′, and c–c′^ pro- duce alternative magnetic motive forces (mmfs), F as , F bs , and F cs , which are space vectors. The resultant stator mmf vector F ss constitutes a vector sum of the phase mmf vectors.
q
d (^0)
i (^) ias ibs
w t
ic s
a
a ′
b ′ c ′
c
(a) (b) b
FIGURE 6.15 Induction motor stator and stator winding current: (a) spatially symmetric three- phase stator windings; (b) phase currents.