
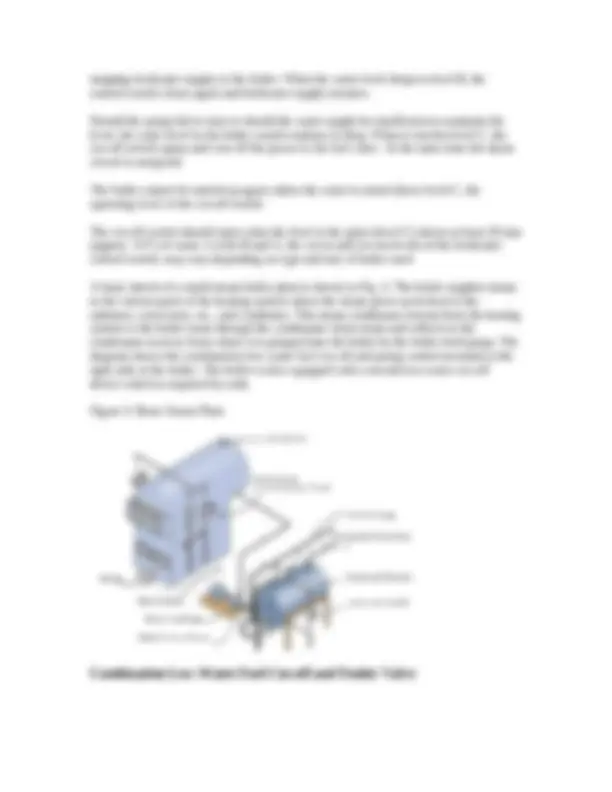
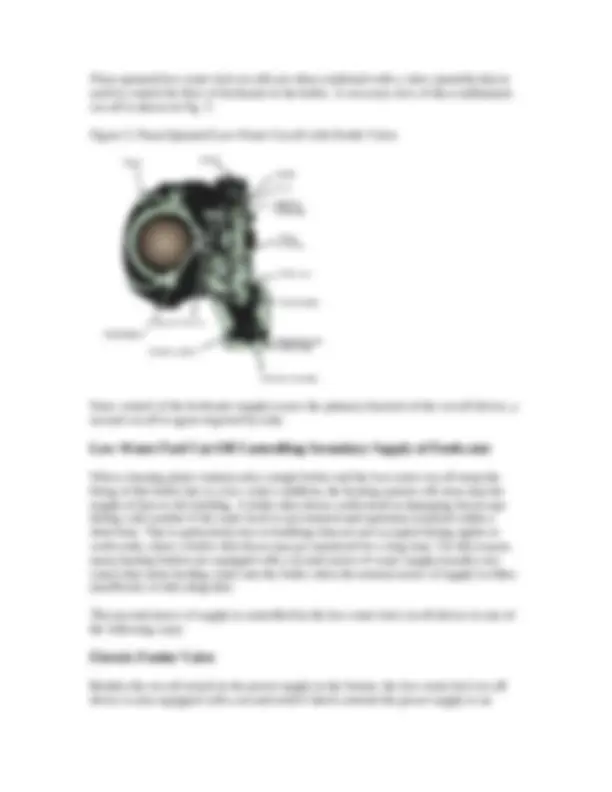
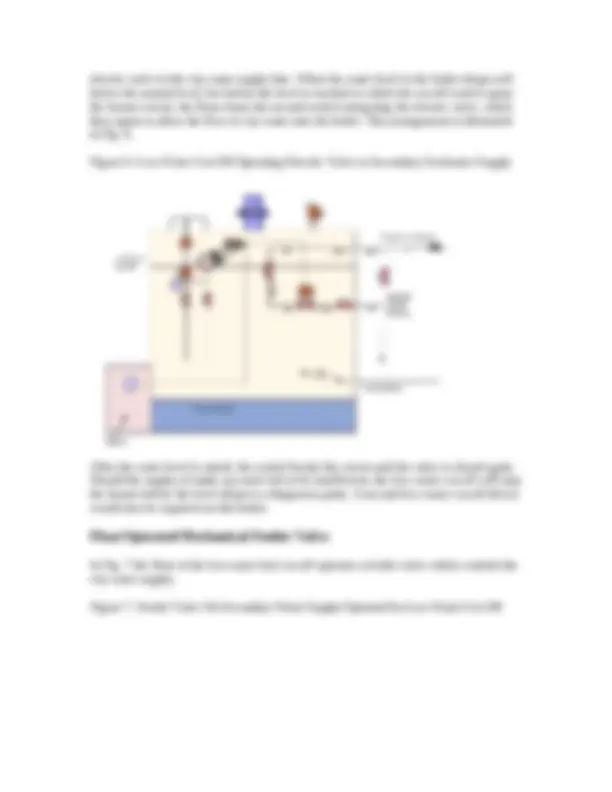
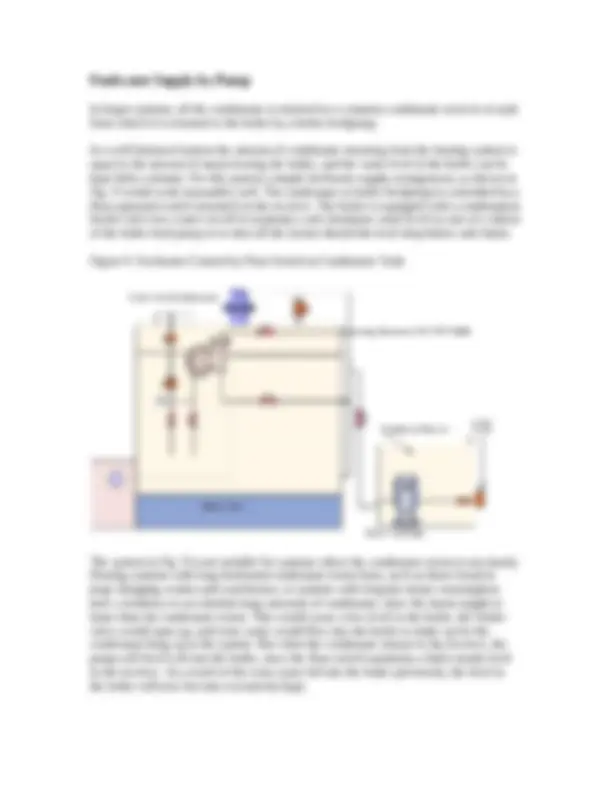
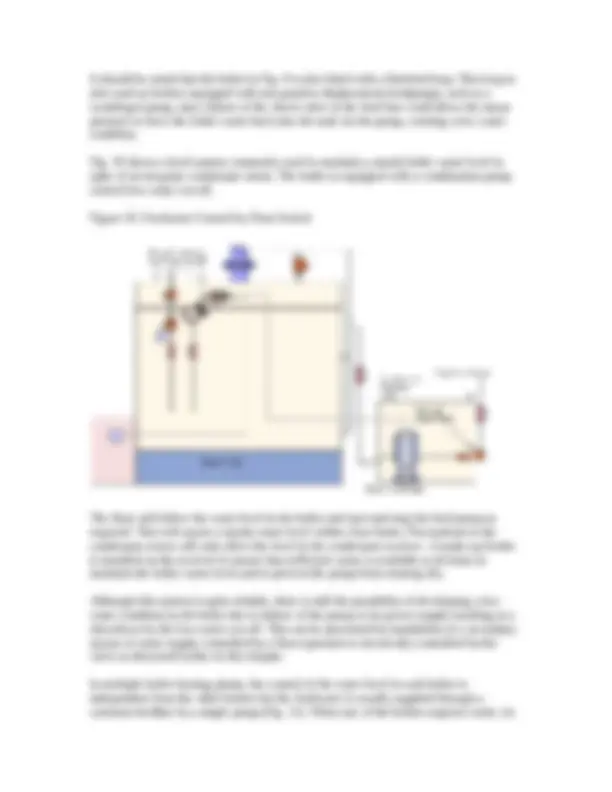

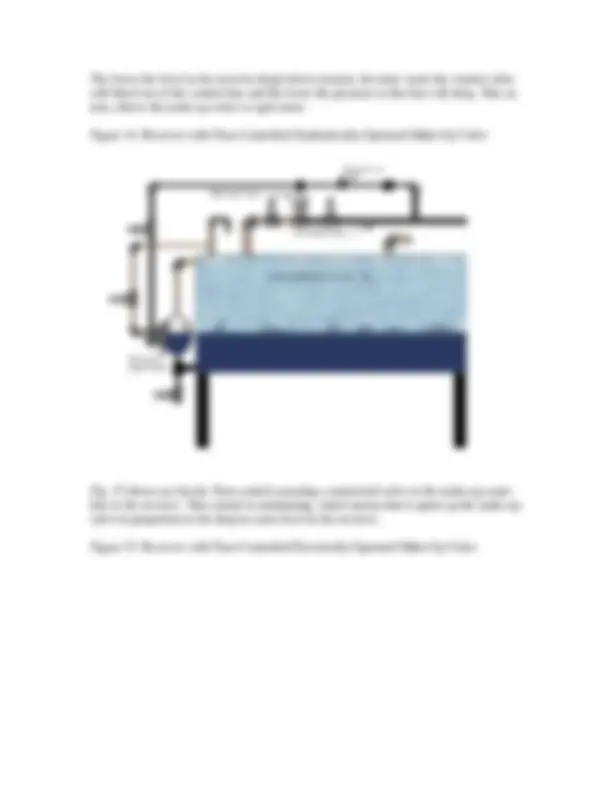
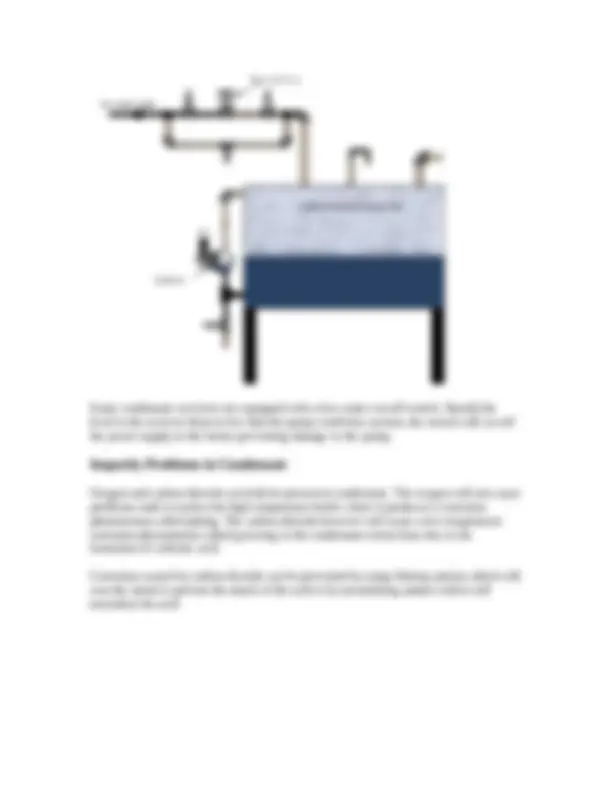
Study with the several resources on Docsity
Earn points by helping other students or get them with a premium plan
Prepare for your exams
Study with the several resources on Docsity
Earn points to download
Earn points by helping other students or get them with a premium plan
Community
Ask the community for help and clear up your study doubts
Discover the best universities in your country according to Docsity users
Free resources
Download our free guides on studying techniques, anxiety management strategies, and thesis advice from Docsity tutors
A detailed explanation of the purpose and function of heating boiler feedwater and condensate piping connections. It covers various methods of feedwater control, including float switches, low-water fuel cut-offs, and gravity feed systems. The document also discusses the importance of condensate return and the role of condensate receivers in maintaining boiler water levels. It is a valuable resource for students and professionals in the field of hvac.
Typology: Summaries
1 / 14
This page cannot be seen from the preview
Don't miss anything!
When you complete this chapter you will be able to… Describe the various feedwater control methods and devices used in low-pressure steam boilers.
Here is what you will be able to do when you complete each objective.
In low-pressure steam boilers there are several ways in which feedwater is controlled to the boiler and many ways condensate is collected and returned to the boiler. This chapter will cover some of the common methods that are in use today.
When you complete this objective you will be able to… Describe the operation of a feedwater float switch operating a valve and float switch operating a pump.
The feedwater supply to most steam heating boilers is usually controlled by a float switch; the float following the fluctuations of the boiler water level. Rather than using a separate float and housing, the feedwater control switch is commonly operated by the low-water fuel cut-off float. This arrangement is shown in Fig. 1.
Figure 1. Basic Diagram of a Float Operated Low-Water Fuel Cut-off The three-wire (double-pole) switch (Fig. 2(a)) is used as a cut-off switch for the fuel valve and as an alarm switch; the two-wire (single-pole) switch (Fig. 2(b)) controls the operation of either the feedwater pump or the feedwater control valve. Figure 2. Mercury Switches Fig. 3 shows how a combined low-water fuel cut-off and feedwater control switch controls the water level in a steam boiler. Figure 3. Control of Water Levels in a Steam Boiler At level A, the highest operating level of the water in the boiler, the feedwater supply switch opens, stopping the power supply to either feedwater pump or control valve, thus
Float operated low-water fuel cut-offs are often combined with a valve assembly that is used to control the flow of feedwater to the boiler. A cut-away view of this combination cut-off is shown in Fig. 5. Figure 5. Float-Operated Low-Water Cut-off with Feeder Valve Since control of the feedwater supply is now the primary function of the cut-off device, a second cut-off is again required by code.
When a heating plant contains only a single boiler and the low-water cut-off stops the firing of this boiler due to a low water condition, the heating system will soon stop the supply of heat to the building. A boiler shut-down could result in damaging freeze-ups during cold weather if the water level is not restored and operation resumed within a short time. This is particularly true in buildings that are not occupied during nights or week-ends, where a boiler shut down may go unnoticed for a long time. For this reason, many heating boilers are equipped with a second source of water supply (usually city water) that starts feeding water into the boiler when the normal source of supply is either insufficient or fails altogether. This second source of supply is controlled by the low-water fuel cut-off device in one of the following ways.
Besides the cut-off switch in the power supply to the burner, the low-water fuel cut-off device is also equipped with a second switch which controls the power supply to an
electric valve in the city water supply line. When the water level in the boiler drops well below the normal level, but before the level is reached at which the cut-off switch opens the burner circuit, the float closes the second switch energizing the electric valve, which then opens to allow the flow of city water into the boiler. This arrangement is illustrated in Fig. 6. Figure 6. Low-Water Cut-Off Operating Electric Valve in Secondary Feedwater Supply After the water level is raised, the switch breaks the circuit and the valve is closed again. Should the supply of make-up water fail or be insufficient, the low-water cut-off will stop the burner before the level drops to a dangerous point. A second low-water cut-off device would also be required on this boiler.
In Fig. 7 the float of the low-water fuel cut-off operates a feeder valve which controls the city water supply. Figure 7. Feeder Valve On Secondary Water Supply Operated by Low-Water Cut-Off
condenses back to water forming what is commonly called steam condensate. This condensate is then returned to the boiler to be converted to steam again. In this chapter, whenever mention is made of feedwater supplied to a low-pressure steam heating boiler, it should be understood that most, if not all, of the feedwater is actually steam condensate returned from the heating system.
In older, small steam heating systems the condensate from the various parts of the heating system is piped to a common condensate return line or return main which feeds the condensate directly back into the boiler by gravity. The condensate is fed into the boiler through a return or Hartford loop, Fig. 8. If the condensate return line would be directly connected to the feed connection in the lower part of the boiler, the possibility would exist that the steam pressure would force the boiler water back into the return line should the check valve fail to close, and the water level in the boiler could drop below the safe minimum level. Figure 8. Hartford or Return Loop The Hartford loop prevents this. The return line is connected to the loop at the height of the lowest safe water level. At that level the heights of the water in the boiler and in the loop will be equal and the steam pressure above the water in boiler and loop will be the same. Since water height and steam pressure in both boiler and loop are balanced, no water can be forced out of the boiler and sufficient water will cover the heating surfaces to prevent overheating.
In larger systems, all the condensate is returned to a common condensate receiver or tank from which it is returned to the boiler by a boiler feedpump. In a well balanced system the amount of condensate returning from the heating system is equal to the amount of steam leaving the boiler, and the water level in the boiler can be kept fairly constant. For this system a simple feedwater supply arrangement, as shown in Fig. 9 would work reasonably well. The condensate or boiler feedpump is controlled by a float-operated switch mounted on the receiver. The boiler is equipped with a combination feeder valve low-water cut-off to maintain a safe minimum water level in case of a failure of the boiler feed pump or to shut off the burner should the level drop below safe limits. Figure 9. Feedwater Control by Float Switch in Condensate Tank The system in Fig. 9 is not suitable for systems where the condensate return is not steady. Heating systems with long horizontal condensate return lines, such as those found in large shopping centres and warehouses, or systems with irregular steam consumption have a tendency to accumulate large amounts of condensate, since the steam supply is faster than the condensate return. This would cause a low level in the boiler, the feeder valve would open up, and extra water would flow into the boiler to make up for the condensate hung up in the system. But when the condensate returns to the receiver, the pump will feed it all into the boiler, since the float switch maintains a fairly steady level in the receiver. As a result of the extra water fed into the boiler previously, the level in the boiler will now become excessively high.
float operated control switch closes, energizing the motorized valve in the feedwater branch line to the boiler. As soon as this valve reaches the open position, it closes an attached pump starting switch, and the condensate starts flowing from the receiver to the boiler. When the water in the boiler reaches its maximum level, the pump control switch opens the circuit, the motorized valve closes and the pump stops. Figure 11. Multiple Boiler System with Feedpump and Motorized Valves If any of the other boilers requires feedwater while the pump is already feeding into one boiler, its pump control switch will energize the motorized feedwater valve on that boiler and the pump will then supply both boilers. Since the second motorized valve also closes an attached pump starting switch, it will be the valve closing last that will shut the feedwater pump down.
When you complete this objective you will be able to… Explain the purpose and function of heating boiler feedwater and condensate piping connections.
An important requirement of a well-designed boiler feedwater system is a condensate receiver of adequate size together with a reliable method of make-up water supply to the receiver. An undersized receiver may cause loss of condensate, while an unreliable make-
up feeder could result in boiler shut-downs due to low water conditions if the boilers are not equipped with feeder valves. As a general rule, the size of the receiver should be sufficient to hold a volume of condensate equivalent to the water evaporated by the boiler in a 1/3 to 1/2 hour period at normal load. The smaller size receiver may be used when the condensate returns easily as in heating systems used in high-rise buildings. In systems extended over a large area (factories, warehouses, etc.), condensate return will be lengthy and the larger size tank should be used. The make-up valve should have sufficient capacity to supply the water required at the normal firing rate of the boiler. If a make-up valve of smaller capacity is used, the valve is commonly installed in the upper part of the receiver, leaving a small volume available for accumulation of condensate. Enough water will be stored in the receiver to supply the feed to the pump during its operating cycle. Various arrangements of make-up water feeders and controls are shown in Figs. 12 and
Figure 12. Receiver with Internal Float Make-Up Valve The float mechanism of the feeder shown in Fig. 12 is mounted directly in the tank. The disadvantage of this arrangement is obvious. The water level in a condensate receiver can
The lower the level in the receiver drops below normal, the more water the control valve will bleed out of the control line and the lower the pressure in this line will drop. This, in turn, allows the make-up valve to open more. Figure 14. Receiver with Float Controlled Hydraulically Operated Make-Up Valve Fig. 15 shows an electric float control actuating a motorized valve in the make-up water line to the receiver. This control is modulating, which means that it opens up the make-up valve in proportion to the drop in water level in the receiver. Figure 15. Receiver with Float Controlled Electrically Operated Make-Up Valve
Some condensate receivers are equipped with a low-water cut-off switch. Should the level in the receiver drop so low that the pump could lose suction, the switch will cut off the power supply to the motor preventing damage to the pump.
Oxygen and carbon dioxide can both be present in condensate. The oxygen will not cause problems until it reaches the high temperature boiler where it produces a corrosion phenomenon called pitting. The carbon dioxide however will cause a low temperature corrosion phenomenon called grooving in the condensate return lines due to the formation of carbonic acid. Corrosion caused by carbon dioxide can be prevented by using filming amines which will coat the metal to prevent the attack of the acid or by neutralizing amines which will neutralize the acid.