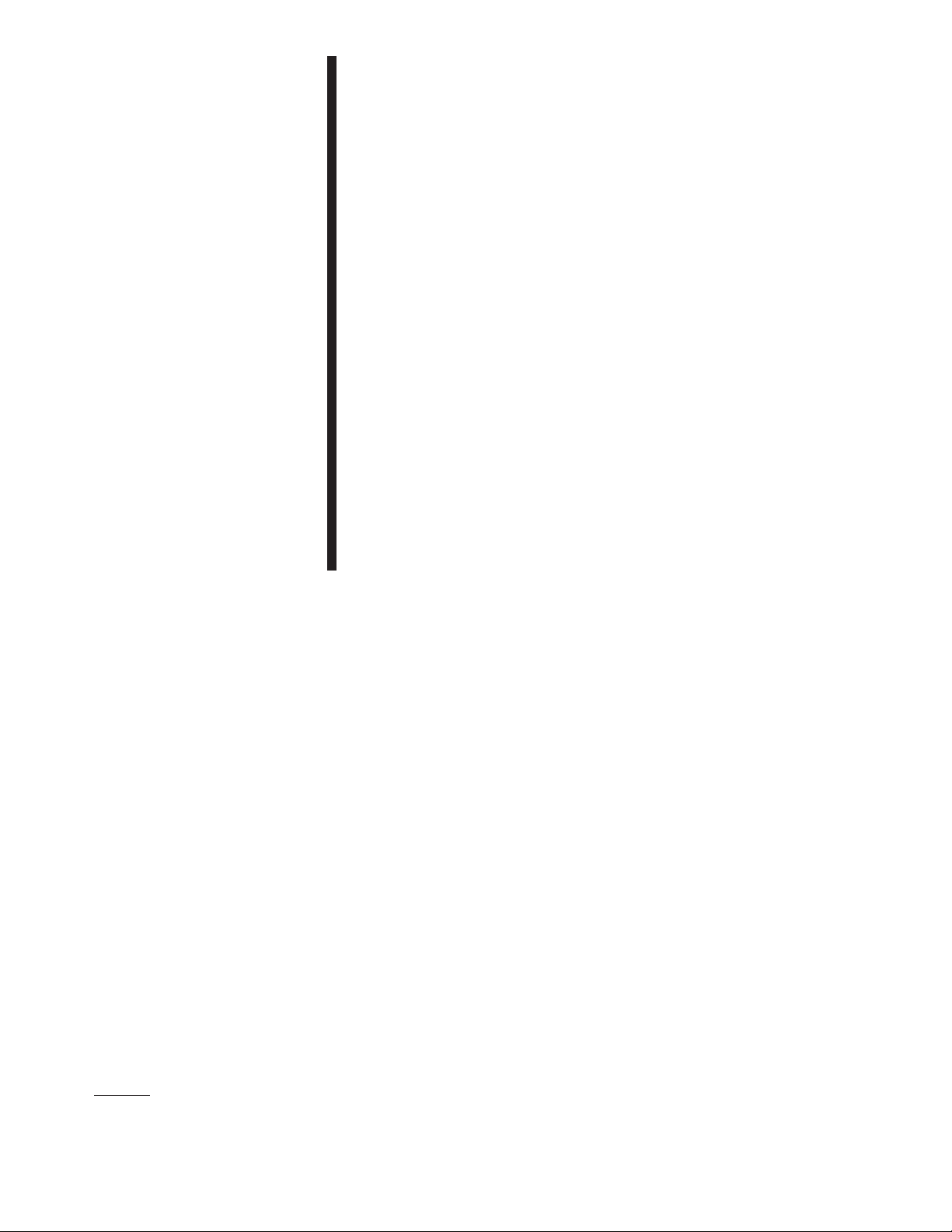
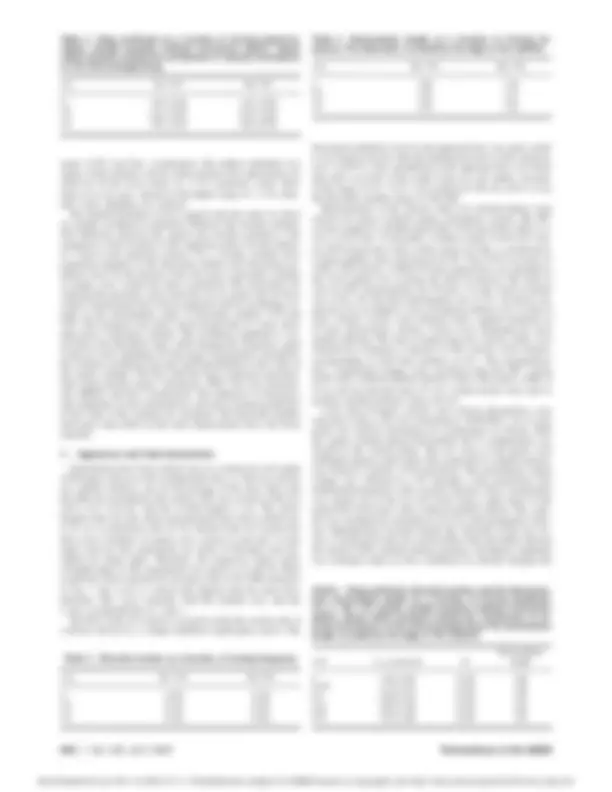
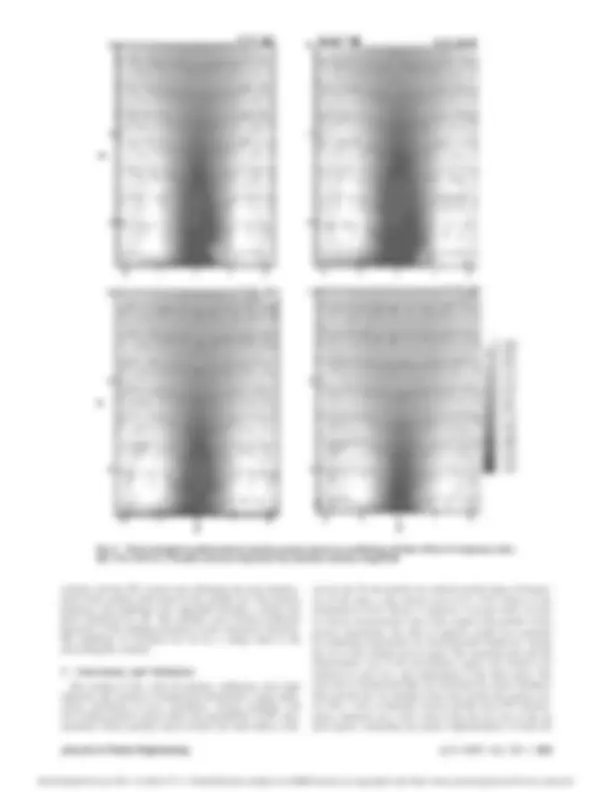
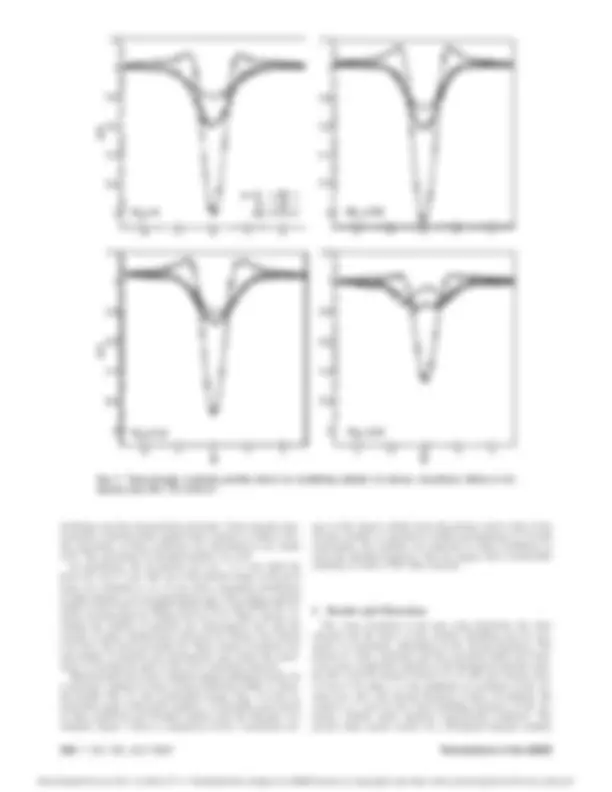
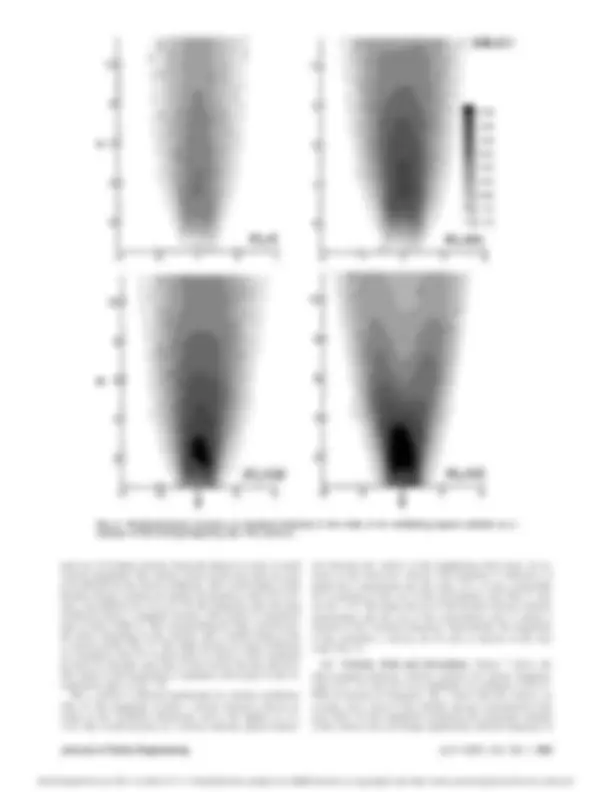

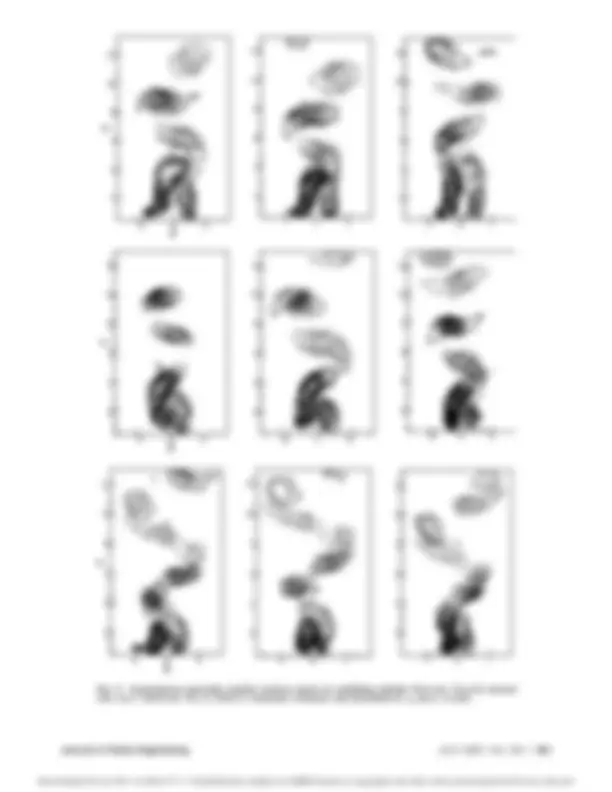
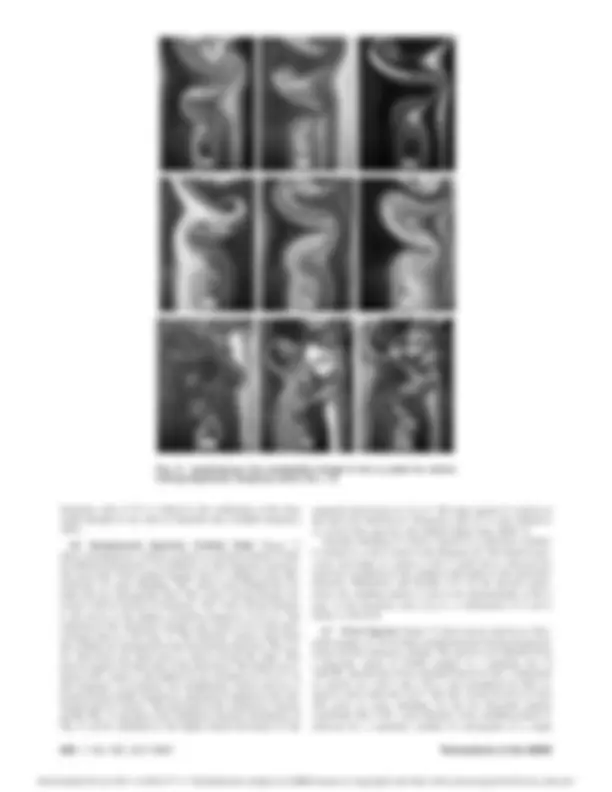
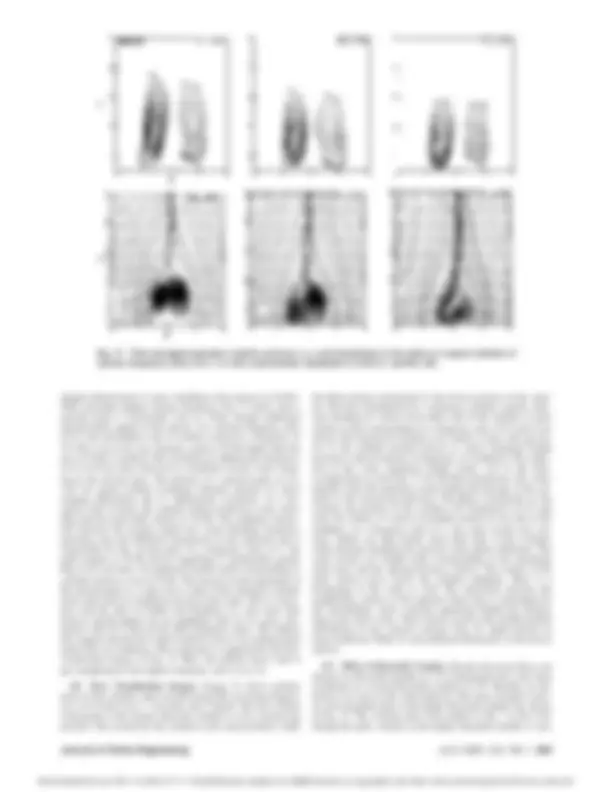
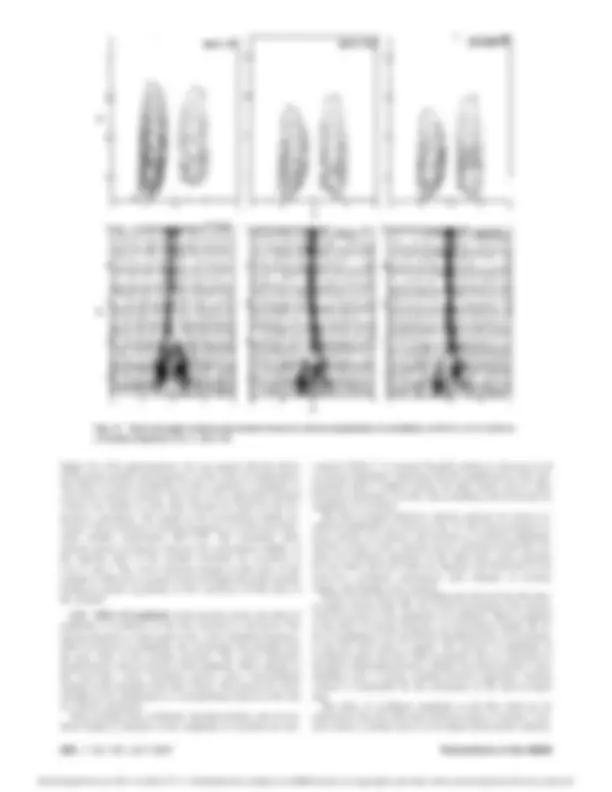
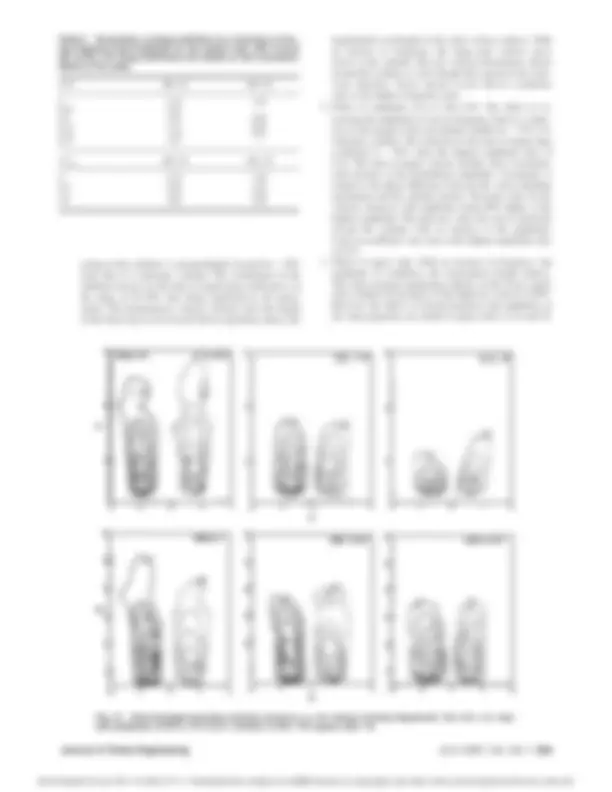
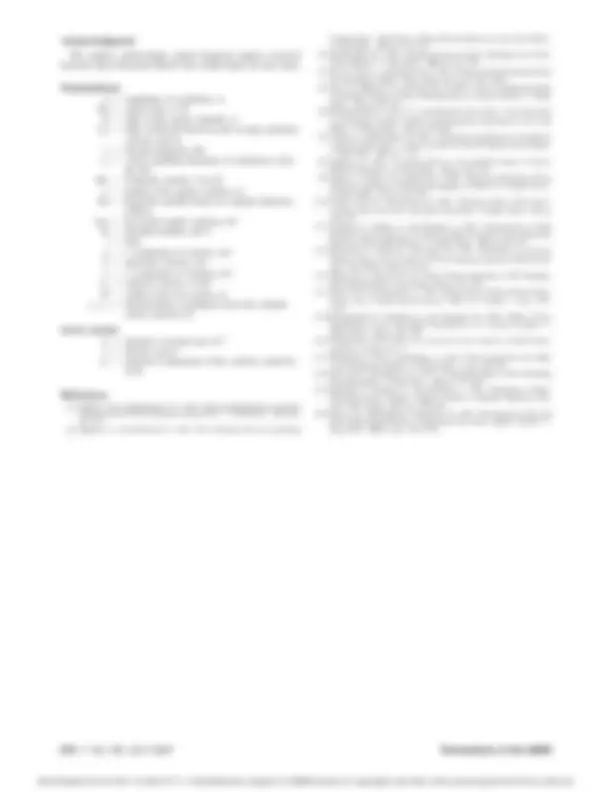
Study with the several resources on Docsity
Earn points by helping other students or get them with a premium plan
Prepare for your exams
Study with the several resources on Docsity
Earn points to download
Earn points by helping other students or get them with a premium plan
Community
Ask the community for help and clear up your study doubts
Discover the best universities in your country according to Docsity users
Free resources
Download our free guides on studying techniques, anxiety management strategies, and thesis advice from Docsity tutors
An experimental study on the flow past a square cylinder oscillating in a vertical test cell filled with air. The authors measure the time-averaged velocity and velocity fluctuations using a hot-wire anemometer and piv system. They calculate the drag coefficient and strouhal number, comparing their results with published literature. The study also discusses the influence of the keulegan-carpenter number, reduced velocity, and velocity ratio on the flow behavior.
Typology: Study notes
1 / 19
This page cannot be seen from the preview
Don't miss anything!
Department of Mechanical Engineering, Indian Institute of Technology Kanpur, Kanpur 208016, India
Sensitivity of a Square Cylinder
Wake to Forced Oscillations
The wake of a square cylinder at zero angle of incidence oscillating inline with the incoming stream has been experimentally studied. Measurement data are reported for Reynolds numbers of 170 and 355. The cylinder aspect ratio is set equal to 28 and a limited study at an aspect ratio of 16 has been carried out. The frequency of oscillation is varied around the Strouhal frequency of a stationary cylinder, and the amplitude of oscillation is 10–30% of the cylinder size. Spatial and temporal flow fields in the cylinder wake have been studied using particle image velocimetry and hot-wire anemometry, the former providing flow visualization images as well. A strong effect of forcing frequency is clearly seen in the near wake. With an increase in frequency, the recirculation length substantially reduces and diminishes the time-averaged drag coefficient. The time- averaged vorticity contours show that the large-scale vortices move closer to the cylinder. The rms values of velocity fluctuations increase in magnitude and cluster around the cylinder as well. The production of turbulent kinetic energy shows a similar trend as that of spanwise vorticity with the former showing greater asymmetry at both sides of the cylinder centerline. The instantaneous vorticity contours show that the length of the shear layer at separation decreases with increasing frequency. The effect of amplitude of oscil- lation on the flow details has been studied when the forcing frequency is kept equal to the vortex-shedding frequency of the stationary cylinder. An increase in amplitude diminishes the time-averaged drag coefficient. The peak value of rms velocity increases, and its location moves upstream. The length of the recirculation bubble decreases with ampli- tude. The reduction in drag coefficient with frequency and amplitude is broadly repro- duced in experiments with the cylinder of lower aspect ratio. DOI: 10.1115/1.2742736
Keywords: square cylinder, forced inline oscillation, drag coefficient, Strouhal number, recirculation length
Bluff body wakes have been extensively investigated in view of their applications to wind engineering, hydrodynamics, aerody- namics, and electronics cooling. Such wakes display characteris- tics that are distinct to the object shape, Reynolds number, and distance in the streamwise direction. At high Reynolds numbers, the wake structure is complex, owing to unsteadiness and turbu- lence. In the lower range of the Reynolds number, recent studies with a cylinder of square cross section show that the flow field along with unsteadiness is three-dimensional, even in nominally two-dimensional geometries. In many practical applications, the flow complexity can be exploited for attaining varying degrees of control. Active flow control using riblike structures is a recent topic of research and requires understanding of the coherent flow struc- tures. The rib can be a cylinder of square cross section. Control is implemented by using an independent external disturbance or a feedback control system resulting in cylinder oscillations. De- pending on the direction of motion with respect to the main flow direction, the oscillation may be transverse or inline. Modification of the flow field can significantly reduce or enhance the intensity of the wake. Griffin and Ramberg 1 reviewed the wake structure of a cir- cular cylinder oscillating inline with the incident steady flow at Re= 190. Vortex shedding was seen to be synchronized with the oscillation of the cylinder in a range of frequencies near twice the shedding frequency. In one experiment, two vortices of opposite sign were shed for one cycle of cylinder motion. In another, one vortex was shed for each cycle of oscillation. Ongoren and Rock-
well 2 studied near-wake flow structures arising from a trans- versely oscillating cylinder over a Reynolds number range of 584–1300 with the hydrogen bubble technique. The authors stud- ied three different geometries circular, triangular, and square over a wide range of frequencies from subharmonic to superhar- monic. The study showed a distinct phase relationship between body motion and vortex shedding for the three harmonic ranges. Roussopoulos 3 studied feedback control of vortex shedding for flow past a circular cylinder at an intermediate Reynolds number using flow visualization and hot-wire techniques. A loudspeaker was used as an actuator and the hot-wire sensor as the control. Vortex suppression was not possible if the control sensor was located too far downstream of the cylinder, even when the sensor could clearly detect the shedding. Also, suppression was not pos- sible if the feedback loop was highly tuned to the shedding fre- quency. Gu et al. 4 studied, numerically and experimentally, the timing of vortex formation for a transversely oscillating circular cylinder. With an increase in the excitation frequency, the vortices were seen to move closer to the cylinder until a limiting position was reached and the vortices switched to the opposite sides of the cylinder. Tao et al. 5 reported a feedback experiment with a hot-wire probe, wherein visualization was conducted using a dye- injection technique for flow past a circular cylinder. The flow visualization images clearly showed complete vortex suppression and enhancement for various feedback conditions. Krishnamoor- thy et al. 6 studied near-wake phenomena behind a transversely oscillating circular cylinder in the Reynolds number range of 1250–1500. While keeping the amplitude of cylinder oscillation fixed, the frequency of oscillation was varied. At the lower exci- tation frequency in the lock-in regime, the authors observed two pairs of vortices shed from the cylinder per cycle of cylinder oscillation. When the critical excitation frequency crossed the lock-in regime, one pair of vortices was shed from the cylinder.
Contributed by the Fluids Engineering Division of ASME for publication in the J OURNAL OF F LUIDS E NGINEERING. Manuscript received July 18, 2006; final manuscript received January 19, 2007. Assoc. Editor: James A. Liburdy.
852 / Vol. 129, JULY 2007 Copyright © 2007 by ASME Transactions of the ASME
Cetiner and Rockwell 7 studied lock-in phenomena and dynamic loading of a circular cylinder for streamwise forced oscillations with respect to the mean flow direction over a wide range of Reynolds number 405 Re 2482 . Particle image velocimetry was used for the study. The authors correlated the vortex pattern with the force coefficients. The authors showed that the lock-in phenomenon is possible for streamwise oscillations because it is in transverse oscillations of the cylinder. Sarpkaya 8 reviewed vortex-induced oscillations of circular cylinders and categorized fundamental aspects of the wake behavior. Yang et al. 9 numeri- cally studied flow past a transversely oscillating rectangular cyl- inder in channel flow. The authors captured flow details at a Rey- nolds number of 500. It was concluded that the wake pattern is dominated by the oscillations of the cylinder. Nobari et al. 10 reported numerical simulation results for flow past an oscillating circular cylinder for Reynolds numbers up to 300. Both transverse and inline oscillations were studied for various frequencies and amplitudes. The effect of the oscillation parameters on the time- averaged drag coefficient was discussed. The authors compared the results of their numerical simulations to experimental data and found a good match. Nishihara et al. 11 studied the effect of streamwise oscillation on wake pattern and fluid dynamic forces of a circular cylinder in a water tunnel using laser Doppler veloci-
Table 1 Comparison of the time-averaged drag coefficient with the published literature for flow past a stationary square cylinder
Authors Nature of study
Aspect ratio Blockage Re C (^) D
Davis and Moore 18 Numerical 2D — 0.170 470 1. Sohankar et al. 19 Numerical 3D 6 0.055 400 1. Saha et al. 20 Numerical 3D 6–10 0.100 400 2. Present Experimental 16 0.030 410 2. 28 0.060 420 2.
Fig. 1 Schematic drawing of the experimental apparatus
Fig. 2 Validation in terms of Strouhal number as a function of Reynolds number for flow past a square cylinder at zero angle of incidence
Fig. 3 Flow visualization images for inline oscillations of a square cylinder „ f / f 0 = 2, below … with a circular cylinder „ above … as reported by Griffin and Ramberg † 1 ‡
Journal of Fluids Engineering JULY 2007, Vol. 129 / 853
cylinder with the PIV camera and calibrating the pixel displace- ment of the cylinder with respect to the cylinder size. The actuator frequency and amplitude were adjustable through a control unit that is interfaced to a PC. The cylinders were excited at different harmonics of the shedding frequency in the streamwise direction. The amplitude of excitation was set by a voltage input to the electromagnetic actuator.
The seeding of flow with oil particles, calibration, laser light reflection and variation in background illumination, image digiti- zation, calculation of cross correlation, velocity gradients, and out-of-plane particle motion affect the repeatability of PIV mea- surements. Tracer particles need to follow the main airflow with-
out any lag. For the particle size utilized and the range of frequen- cies in the wake, a slip velocity error of 0.3– 0.5% relative to the instantaneous local velocity is expected. A second source of error in velocity measurement is due to the weight of the particle. In the present experiments, the effect of particle weight was examined by conducting experiments at a fixed Reynolds number by varying the size of the cylinder and air speed. The streamline plot and the dimensionless size of the recirculation region were found to be identical in each case, and independent of the fluid speed. The noise due to background light was minimized by using a bandpass filter around the wavelength of the laser before the camera sen- sor. The x - and y -component velocity profiles from PIV measure- ments compared very well to those from the hot wire in the far field region, confirming the proper implementation of both the
Fig. 4 Time-averaged nondimensional velocity vectors above an oscillating cylinder: Effect of frequency ratio, Re= 170, A / B = 0.1; flooded contours represent the absolute velocity magnitude
Journal of Fluids Engineering JULY 2007, Vol. 129 / 855
techniques and the measurement procedure. From repeated mea- surements with Reynolds number kept constant to within ±1%, the uncertainty in drag coefficient was determined to be within ±5%. The uncertainty in Strouhal number was ±2%. In experiments, the oil particle size was 2 – 3 m while the pixel size was 6.7 m. The size of the particle image on the pixel array was estimated as 14– 15 m from a histogram distribution of light intensity over an interrogation spot. This yields a particle image-to-pixel ratio of slightly greater than 2 and fulfills the cri- terion recommended by Chang and Liu 13 . Other criteria, in- cluding the number of particles per interrogation spot and the average in-plane displacement discussed by Keane and Adrian 14 , have also been accounted for. These criteria of particle size and number of particles per interrogation spot reduce the uncer- tainty in locating the peak of the cross-correlation function. Measurements have been validated against published results for a stationary cylinder in terms of drag coefficient Table 1, Strou- hal number Fig. 2, and visualization images Fig. 3 in the in- termediate range of Reynolds numbers. A reasonably good match of drag coefficient and Strouhal number with the literature was obtained. Figure 3 shows a comparison of flow visualization im-
ages of the square cylinder from the present work to that of the circular cylinder, as reported by Griffin and Ramberg 1 . In both experiments, the cylinders are subjected to inline oscillations at twice the Strouhal frequency. The two images show considerable similarity in terms of the wake structure.
The vortex formation in the near wake determines the wake structure and the forces on the cylinder. Shedding may be sym- metric or asymmetric, depending on the forcing frequency. The pattern of vortex formation and the associated inline and trans- verse force components depend on the Keulegan-Carpenter num- ber, KC= 2 A / B , reduced velocity V (^) r = U / fB , and velocity ratio, U / 2 fA 7,8. Here, A is the amplitude of oscillation, B the cyl- inder size, and f the forcing frequency in hertz. In addition, the symbol f 0 is used for the vortex-shedding frequency of the sta- tionary cylinder under identical experimental conditions. The present study reports results for a Keulegan-Carpenter number
Fig. 5 Time-average u -velocity profiles above an oscillating cylinder at various x -locations: Effect of fre- quency ratio, Re= 170, A / B = 0.
856 / Vol. 129, JULY 2007 Transactions of the ASME
the cylinder, the correction arising from turbulent stresses is ex- pected to be significant. The drag coefficient has been calculated from the extended formula
−
u U
u U
−
Here, the first term is the momentum deficit of the time-averaged flow field and the second term is the contribution of the turbulent fluctuations. The Strouhal number has been calculated from the spectral peak of the velocity trace recorded by the hot-wire anemometer. Table 2 presents the drag coefficient measured at various fre- quencies of oscillation. The amplitude of oscillation is kept con- stant in these experiments at A / B = 0.1. Drag coefficients have been calculated for two Reynolds numbers Re= 170 and 355. The drag coefficient decreases with respect to a stationary cylin- der for an increase in the forcing frequency at both Reynolds numbers. There is a slight increase in drag coefficient when the frequency ratio increases from one to two at Re= 170, but the values are consistently smaller than for a stationary cylinder. The above trends are realized for a drag coefficient based on the mo- mentum deficit alone as well as the total value. These results can be understood against measurements of flow patterns described in the later sections. Table 3 presents the Strouhal number data as a function of frequency of oscillation at two Reynolds numbers Re= 170 and 355 . No significant change in Strouhal number as a function of forcing frequency is observed, although its overall value increases with an increase in Reynolds number. This result is to be inter- preted to mean that a significant spectral peak at the Strouhal
frequency of a stationary cylinder was seen for all forcing fre- quencies. However, the cylinder oscillation modifies the wake structures sufficiently to reduce the momentum deficit and hence drag coefficient with respect to the stationary cylinder. Power spectra are discussed in Sec. 4.7. The recirculation length of the time-averaged wake normalized by the edge of the cylinder in cross section is given in Table 4 as a function of frequency. This quantity diminishes with increasing frequency at both Reynolds numbers. The recirculation length scales with base pressure on the rear side of the cylinder in the sense that smaller base pressures result in longer recirculation lengths. Hence, a reduction in the recirculation length is indicative of a higher base pressure and a lower drag. Drag coefficient and Strouhal number as functions of the am- plitude of excitation are presented in Table 5. The excitation fre- quency is kept fixed and equal to that of vortex shedding of a stationary cylinder. A constant Strouhal number is observed with increase in amplitude of excitation indicating that the amplifica- tion of the fundamental mode is the highest among all modes and no other harmonic dominates over the basic vortex shedding pro- cess. The drag coefficient along with the recirculation length generally decreases with an increase in amplitude. However, when the amplitude reaches 0.32, the turbulent stresses provide a sig- nificant contribution to drag and the total drag coefficient starts to increase. The recirculation length, however, shows a continuously decreasing trend.
4.2 Velocity Field. The time-averaged velocity vectors and velocity profiles for various oscillation frequencies are shown in Figs. 4–6 for a Reynolds number of 170. Both x - and y -axes have been nondimensionalized with the cylinder size. The shaded con-
Fig. 7 Time-averaged spanwise vorticity field „ top … and streamlines „ below … in the wake of an oscillating square cylinder as a function of the forcing frequency, Re= 170, A / B = 0.
858 / Vol. 129, JULY 2007 Transactions of the ASME
tours are of resultant velocity, being the darkest in zones of small velocity magnitude. The velocity vectors in the near wake are seen to be affected by the forced oscillations. The overall shapes of the flooded velocity contours are similar for frequency ratios of 0, 0.5, and 1, but different for f / f 0 = 2.0. For this frequency ratio, the drag coefficient shows a marginal increase with respect to frequency ratio of unity Table 2. The corresponding far-wake velocity pro- file shows branching in the contours and a double hump in the u -velocity profile Fig. 5. The slight increase in drag coefficient at a frequency ratio of 2 with respect to unity is thus explained in terms of a broader wake that, in turn, lowers the base pressure. The origin of the broadening is explained with respect to the in- stantaneous plots of Sec. 4.5. The (^) v velocity is affected significantly by cylinder oscillations Fig. 6. The magnitude of peak v velocity increases with an in- crease in the oscillation frequencies and is the highest at f / f (^) o = 2.0. The overall increase in v velocity indicates greater interac-
tion between the vortices of the neighboring shear layer. An in- crease in the transverse velocity with frequency is indicative of higher flow entrainment into the wake. It is, in turn, responsible for a reduction in the size of the recirculation zone Fig. 4, also see Sec. 4.3. The shape and size of the flooded velocity contours demonstrates that the size of the recirculation zone is indeed a function of the excitation frequency. Equivalently, the magnitude of the centerline u velocity can be seen to increase in the near wake Fig. 5.
4.3 Vorticity Field and Streamlines. Figure 7 shows the time-averaged spanwise vorticity contours for various frequency ratios 0.5, 1.0, and 2.0 at an amplitude of oscillation A / B = 0.1. With an increase in frequency, Fig. 7 shows that the vortices, on average, move closer to the cylinder and get concentrated in the near wake. For the amplitude considered, the maximum strength of the vortices does not change significantly with the frequency of
Fig. 8 Nondimensional contours of turbulent intensity in the wake of an oscillating square cylinder as a function of the forcing frequency, Re= 170, A / B = 0.
Journal of Fluids Engineering JULY 2007, Vol. 129 / 859
Fig. 11 Instantaneous spanwise vorticity contours above an oscillating cylinder. First row: f / f 0 = 0.5; second row: f / f 0 = 1; third row: f / f 0 = 2. A / B = 0.1; maximum, minimum, and increments in z are 3 , −3 , 0.25.
Journal of Fluids Engineering JULY 2007, Vol. 129 / 861
oscillation. Vorticity concentration in the near field region has also been observed in the context of circular cylinder oscillations 4 . The movement of the point of maximum vorticity toward the cyl- inder confirms the reduction in the size of the recirculation zone of Fig. 4. Vorticity in the wake can be traced to the shear layer separating at the cylinder corners. Subsequently, it is swept along the wake, while being diffused by the fluid viscosity. The vorticity produc- tion in the wake is proportional to the velocity difference between the main stream and the cylinder centerline velocity. The time instants at which flow separation takes place on each side of the cylinder correspond to distinct phases in the cylinder oscillation. Hence, the strengths of the vortices on either side of the cylinder are not necessarily of equal strength. Vortices are also subjected to strain fields imposed by the near field vortices. The vorticity con- tours of Fig. 7 show that for the present experiments, the effect of forced oscillations on flow symmetry is small. The sizes of two oppositely oriented vortices are close to each other and the peak values are close as well. However, the mechanism of vorticity distribution or budgets in the wake region is dependent on the excitation frequency leading to the movement of maximum vor-
ticity zone closer to the cylinder for the excited case. The influ- ence on the time-averaged properties, such as drag coefficient, is, however, significant Sec. 4.1. Figure 7 also shows the streamline contours from the time- averaged velocity vectors at the midspan of the cylinder for Re 170. With an increase in excitation frequency, the streamline patterns show that the size of the recirculation bubble reduces. The shape of the streamline contour is similar to that of the vor- ticity contours except at excitation frequency f / f 0 = 2. The size of the recirculation bubble is smaller than that of the vorticity con- tour. The recirculation zone for f / f 0 = 2 is smaller than the mea- surement zone of this study. Therefore, the recirculation bubbles are not clearly seen at f / f 0 = 2. This trend has been observed for a circular cylinder by other authors, notably Konstantinides et al. 15 . Zdravkovich 16 pointed out that wakes of a cylinder forced to oscillate in either the transverse or the streamwise direction share several characteristics, including reduction in vortex forma- tion length and an increase in base pressure. The reduction in vortex formation length in the synchronization range has also been observed for a circular cylinder oscillated in the transverse
Fig. 12 Power spectra of the transverse velocity component in the wake of an oscillating cylinder; Re= 170
862 / Vol. 129, JULY 2007 Transactions of the ASME
frequency ratio of 0.5 is related to the weakening of the base region though its size starts to diminish only at higher frequency ratios.
4.6 Instantaneous Spanwise Vorticity Field. Figure 11 shows instantaneous vorticity contours at selected instants of time for different frequencies of oscillation. As the frequency increases, the near-wake vortex pattern changes due to a change in the char- acteristics of vortex shedding. The vortices grow behind the cyl- inder and are subsequently shed. The vortex roll-up distance de- creases with an increase in frequency. The vortex roll-up distance is the lowest at the highest excitation frequency f / f 0 = 2. The reduction in the streamwise length scale carries over to the time- averaged data as well Fig. 7. The alternate vortices shed from the cylinder are transported in the downstream direction. The vor- tex shed from one shear layer is drawn toward the other. This process repeats for both sides of the shear layer. The lateral move- ment of the vortices is the highest for an excitation of f / f 0 = 2. At this frequency of excitation, two neighboring vortices travel as a group having smaller streamwise separation compared to the sub- sequent pair of vortices. The dual peak in the streamwise velocity profile Fig. 5 and that in the turbulence intensity distribution of Fig. 8 can be attributed to the higher lateral movement of the
separated shear layers at f / f 0 = 2. The large spread of vorticity in the transverse direction at a frequency ratio of 2 is also indicative of a lower base pressure and slightly higher drag Table 2. Alternate shedding of vortices, typical of a stationary cylinder, is referred to as the S mode in the literature 8 . The lateral trans- verse movement of vortices is the P mode and is observed for transverse oscillation of the cylinder with respect to the mean flow direction, Williamson and Roshko 17 . In the present experi- ments, the shedding pattern is seen to be predominantly of the S type. At the frequency ratio f / f 0 = 2, a combination of P and S modes is observed.
4.7 Power Spectra. Figure 12 shows power spectra at a Rey- nolds number of 170 for three nondimensional forcing frequencies along with the stationary cylinder. The spectra were obtained from a long-time signal of 20,000 samples at a sampling rate of 1000 Hz. Spectra have been calculated based on the v component of velocity at x / B = 5 and y / B = 1 and normalized by their re- spective areas under the curve. The time record involves at least 300 cycles of vortex shedding. For the low Reynolds number experiment Re= 170, a pure Karman vortex shedding pattern is observed for a stationary cylinder. It corresponds to a single
Fig. 14 Instantaneous flow visualization images in the x - y plane for various forcing frequencies „ frequency ratios 0.5, 1, 2 …
864 / Vol. 129, JULY 2007 Transactions of the ASME
sharply defined peak of vortex shedding in the spectra at 39 Hz. With externally applied forcing frequency, Fig. 12 shows that a spectral peak is consistently seen at 39 Hz, though additional spectral peaks appear in the spectra. At a forcing frequency ratio of 0.5, the unsteadiness due to cylinder motion at a frequency of 19.5 Hz is not to be seen. Instead, a peak at 78 Hz higher than the one at 39 Hz is realized. The excitation at subharmonic frequency f / f 0 = 0.5 has been observed to contribute toward vortex merg- ing in the mixing layer. The absence of a spectral peak at f / f 0 = 0.5 for square cylinder oscillation indicates absence of vortex merging phenomena due to subharmonic excitation. At a fre- quency ratio of unity, the cylinder motion reinforces vortex shed- ding and the peak shifts clearly to 39 Hz. The nonlinear interac- tion between the forcing signal and vortex-shedding frequency generates sum and difference frequencies in the spectrum and is responsible for the second peak. At a frequency ratio of 2, the peak remains at 39 Hz and its magnitude is significantly greater than at 0.5 and unity. An additional smaller peak corresponding to cylinder motion is seen at 78 Hz. The increase in the magnitude of the spectral peak to a value close to that of the stationary cylinder shows that lock-on conditions prevail in the wake. This is consis- tent with the data of Griffin and Ramberg 1 , who show that lock-on should appear for an amplitude ratio of 0.1 and a fre- quency ratio of 2, but not for other frequency ratios. The authors also suggest that the flow field would be close to two-dimensional under lock-on conditions. This conjecture is supported by the flow visualization images of Fig. 13. Here, the particle traces tend to get straightened at the highest frequency ratio f / f 0 = 2.
4.8 Flow Visualization Images. Figure 14 shows particle traces in the cylinder wake recorded using PIV at forcing frequen- cies of 0.5 first row, 1 second, and 2 third. The first column corresponds to the instant when the cylinder is at its extreme top position. The second has the cylinder at the mean position, while
the third column corresponds to the lowest position of the cylin- der. The flow distribution for a stationary cylinder, namely, alter- nate shedding of vortices from either side of the cylinder, is quite similar to that corresponding to a frequency ratio of 0.5 and is not shown. The streamwise distance over which a vortex rolls up rela- tive to the cylinder position known as vortex formation length decreases with an increase in frequency of oscillation. The reduc- tion in the vortex formation length carries over to the time- averaged data as well Fig. 7. For all three frequencies, the vortex detaches from the upstream corner during the passage of the cyl- inder in the downward direction. The phase corresponds to the extreme top position of the cylinder. For frequencies of 0.5 and unity, the centers of vortices essentially remain on one side of the midplane. At a frequency ratio of 2, the wake reveals new fea- tures. Eddies are shed jointly from both sides of the cylinder, while alternate shedding also persists with a phase difference. The wake reveals two length scales corresponding to the separating shear layer and the spacing between vortices. The centers of the shed vortices move across the cylinder midplane. There is a broadening of the wake as well. The interaction between the neighboring vortices of the opposite shear layer is interrupted by the intermediate vortex structure appearing behind the primary large-scale shed vortex. These factors result in the double-peaked distribution of rms velocity contours Fig. 8, slight increase in drag coefficient Table 2, and additional harmonics in the power spectra.
4.9 Effect of Reynolds Number. Results discussed above are mainly at a Reynolds number of 170. Experiments have also been conducted at a second Reynolds number of 355. Broadly, no dif- ference was seen in the wake behavior. The time-averaged vortic- ity and streamline plots at the higher Reynolds number are shown in Fig. 15. The vorticity plots look similar to Fig. 7 at Re= 170, though the peak vorticity at the higher Reynolds number is also
Fig. 15 Time-averaged spanwise vorticity contours „ z … and streamlines in the wake of a square cylinder at various frequency ratios „ 0.5, 1 , 2 … with a perturbation amplitude at A / B = 0.1 and Re= 355
Journal of Fluids Engineering JULY 2007, Vol. 129 / 865
posed flow is zero. For a square cylinder with inline oscillations, two fixed stagnation points at the front and back of the cylinder are available. The resulting vortex-generation process can be de- scribed as follows. As the oscillating cylinder moves in the for- ward direction, two boundary layers develop on the cylinder wall. The separating flow creates two counterrotating vortices of equal magnitude and strength, resulting in geometrically similar vortex fields. The creation of vortices stops when the maximum forward location of the cylinder is reached and the cylinder starts its back- ward motion. The vortex formation process is now repeated on the other side of the cylinder. In addition, the backward motion of the cylinder causes a splitting of the vortex pair, produced earlier by the for- ward motion, until, finally, flow reversal occurs. Thus, cylinder oscillation creates a strong damping effect in the near flow field and a concentration of vortices in the near wake of the cylinder. The higher the amplitude of oscillation is, the larger the damping effect is. One can now expect the superimposed flow to modulate the vortex-generation process described above because of vortex shedding. Figure 17 shows the nondimensional turbulence intensity field
at various amplitudes of oscillation. The turbulent intensity near the cylinder increases as more energy enters the flow field from cylinder excitation. The maximum intensity value moves toward the cylinder with an increase in excitation amplitude. The degree of asymmetry increases as well with an increase in the amplitude. Figure 18 shows the power spectra of velocity signals in the near wake at different amplitudes of oscillation. With an increase in the amplitude of oscillation, multiple harmonics of the fre- quency of vortex shedding start to appear. At a particular ampli- tude A / B = 0.32, the flow field is dominated by the forcing fre- quency and only one dominant peak is seen in the power spectra. This may be considered as a lock-on state, and the flow can be considered increasingly two-dimensional with increase in ampli- tude.
4.11 Effect of Aspect Ratio. A limited study was carried out to investigate the effect of aspect ratio on the near wake of a cylinder under oscillatory conditions. While the aspect ratio con- sidered in earlier sections was 28, the aspect ratio in the present discussion is 16. For definiteness, a Reynolds number of 170 is considered. The effects of frequency as well as amplitude of os- cillation are investigated.
Fig. 17 Rms contours for various amplitudes of oscillation, Re= 170
Journal of Fluids Engineering JULY 2007, Vol. 129 / 867
Table 6 summarizes the time-averaged drag coefficient data for two aspect ratios 16 and 28 for various frequencies and ampli- tudes of oscillation. In the study of the effect of frequency, the amplitude is kept constant at 0.1. In the second set of experiments, the forcing frequency is that of vortex shedding, while the ampli- tude is varied. The overall drag coefficient is lower at the higher aspect ratio for both unexcited and excited cylinders. A minimum in drag coefficient is seen for a frequency ratio f / f 0 = 1.0 for the two aspect ratios. This indicates that the end conditions due to the difference in aspect ratio do not alter the effect of cylinder oscil- lation. The magnitude of drag coefficient at AR= 16 is uniformly higher when compared to the higher aspect ratio experiments. This effect of aspect ratio on drag coefficient was seen for a sta- tionary cylinder as well. The drag coefficient diminishes rapidly with an increase in the amplitude of oscillation. Figure 19 shows the time-averaged spanwise vorticity contours for various frequencies f / f 0 = 0.5, 1.0, and 2.0 and amplitudes A / B = 0.1, 0.14, and 0.21 at the aspect ratio of 16. With an in- crease in the forcing frequency, the vortices concentrate near the rear surface of the cylinder. Similar trends were observed at the higher aspect ratio Fig. 7. However, the strength of vorticity is
higher in the lower aspect ratio experiment Fig. 19 when com- pared to the higher one Fig. 7. The higher vorticity at lower aspect ratio may be related to the confinement effects. The com- parison of Fig. 19 top with Fig. 19 bottom indicates similar effects of excitation amplitude and frequency. Overall, aspect ratio does not alter the characteristics of the oscillating cylinder.
An experimental study of uniform flow past an oscillating square cylinder is reported. Measurement techniques are based on PIV, HWA, and flow visualization. The Reynolds number mainly considered is 170, while selected results for Re= 355 have also been presented. The cylinder is oscillated using an electromag- netic actuator at around the vortex-shedding frequency of the equivalent stationary cylinder. The following conclusions have been arrived at in the study:
Fig. 18 Power spectra for various amplitudes of oscillation, Re= 170
868 / Vol. 129, JULY 2007 Transactions of the ASME
The authors acknowledge partial financial support received from the Naval Research Board, New Delhi, India, for this study.
A amplitude of oscillation, m AR aspect ratio, L / B B edge of the square cylinder, m C (^) D drag coefficient based on the average upstream velocity and B , f forcing frequency, Hz f (^) o vortex shedding frequency of stationary cylin- der, Hz KC Carpenter number, 2 A / B L length of the square cylinder, m Re Reynolds number based on cylinder diameter, UB / rms root-mean-square velocity, m/s St Strouhal number, fB / U t time u x component of velocity, m/s U upstream velocity, m/s v y component of velocity, m/s V (^) r reduced velocity, U / Bf W width of the test section, m x , y , z dimensionless coordinates from the cylinder center scaled by B
Greek symbols dynamic viscosity, kg/ s m 2 density, kg/ m 3 z ^ spanwise component of the vorticity scaled by U / B
1 Griffin, O. M., and Ramberg, S. E., 1976, “Vortex Shedding From a Cylinder Vibrating In-Line With an Incident Uniform Flow,” J. Fluid Mech., 75 2 , pp. 257–271. 2 Ongoren, A., and Rockwell, D., 1988, “Flow Structure From an Oscillating
Cylinder Part 1. Mechanism of Phase Shift and Recovery in the Near Wake,” J. Fluid Mech., 191 , pp. 197–223. 3 Roussopoulos, K., 1993, “Feedback Control of Vortex Shedding at Low Rey- nolds Numbers,” J. Fluid Mech., 248 , pp. 267–296. 4 Gu, W., Chyu, C., and Rockwell, D., 1994, “Timing of Vortex Formation From an Oscillating Cylinder,” Phys. Fluids, 6 11 , pp. 3677–3682. 5 Tao, J. S., Huang, X. Y., and Chan, W. K. 1996 , “A Flow Visualization Study on Feedback Control of Vortex Shedding From a Circular Cylinder,” J. Fluids Struct., 10 , pp. 965–970. 6 Krishnamoorthy, S., Price, S. J., and Paidoussis, M. P., 2001, “Cross-Flow Past an Oscillating Circular Cylinder: Synchronization Phenomena in the Near Wake,” J. Fluids Struct., 15 , pp. 955–980. 7 Cetiner, O., and Rockwell, D., 2001, “Streamwise Oscillations of a Cylinder in a Steady Current. Part 1. Locked-on States of Vortex Formation and Loading,” J. Fluid Mech., 427 , pp. 1–28. 8 Sarpkaya, T., 2004, “A Critical Review of the Intrinsic Nature of Vortex- Induced Vibrations,” J. Fluids Struct., 19 , pp. 389–447. 9 Yang, S. J., Cheng, T. R., and Fu, W. S., 2005, “Numerical Simulation of Flow Structures Around an Oscillating Rectangular Cylinder in a Channel Flow,” Comput. Mech., 35 , pp. 342–351. 10 Nobari, M. R. H., and Naderan, H., 2006, “Numerical Study of Flow Past a Cylinder With Cross Flow and Inline Oscillation,” Comput. Fluids, 35 , pp. 393–415. 11 Nishihara, T., Kaneko, S., and Watanabe, T., 2005, “Characteristics of Fluid Dynamic Forces Acting on a Circular Cylinder Oscillated in the Streamwise Direction and Its Wake Patterns,” J. Fluids Struct., 20 , pp. 505–518. 12 Westerweel, J., Dabiri, D., and Gharib, M., 1997, “The Effect of a Discrete Window Offset on the Accuracy of Cross-Correlation Analysis of PIV Record- ings,” Exp. Fluids, 23 , pp. 20–28. 13 Chang, K.-A., and Liu, P. L.-F., 2000, “Pseudo Turbulence in PIV Breaking- Wave Measurements,” Exp. Fluids, 29 , pp. 331–338. 14 Keane, R. D., and Adrian, R. J., 1990, “Optimization of Particle Image Veloci- meters. Part I: Double-Pulsed System,” Meas. Sci. Technol., 1 , pp. 1202–
15 Konstantinidis, E., Balabani, S., and Yianneskis, M., 2003, “Effect of Flow Perturbations on the Near Wake Characteristics of a Circular Cylinder,” J. Fluids Struct., 18 , pp. 367–386. 16 Zdravkovich, M. M., 2003, Flow Around Circular Cylinders , Oxford Univer- sity Press, London, Vol. 2. 17 Williamson, C. H. K., and Roshko, A., 1988, “Vortex Formation in the Wake of an Oscillating Cylinder,” J. Fluids Struct., 2 , pp. 355–381. 18 Davis, R. W., and Moore, E. F., 1984, “A Numerical Study of Vortex Shedding From Rectangles,” J. Fluid Mech., 116 , pp. 475–506. 19 Sohankar, A., Norberg, C., and Davidson, L., 1999, “Simulation of Three- Dimensional Flow Around a Square Cylinder at Moderate Reynolds Num- bers,” Phys. Fluids, 11 2 , pp. 288–306. 20 Saha, A. K., Muralidhar, K., and Biswas, G., 2003, “Investigation of Two and Three Dimensional Models of Transitional Flow Past a Square Cylinder,” J. Eng. Mech., 129 11 , pp. 1320–1329.
870 / Vol. 129, JULY 2007 Transactions of the ASME