
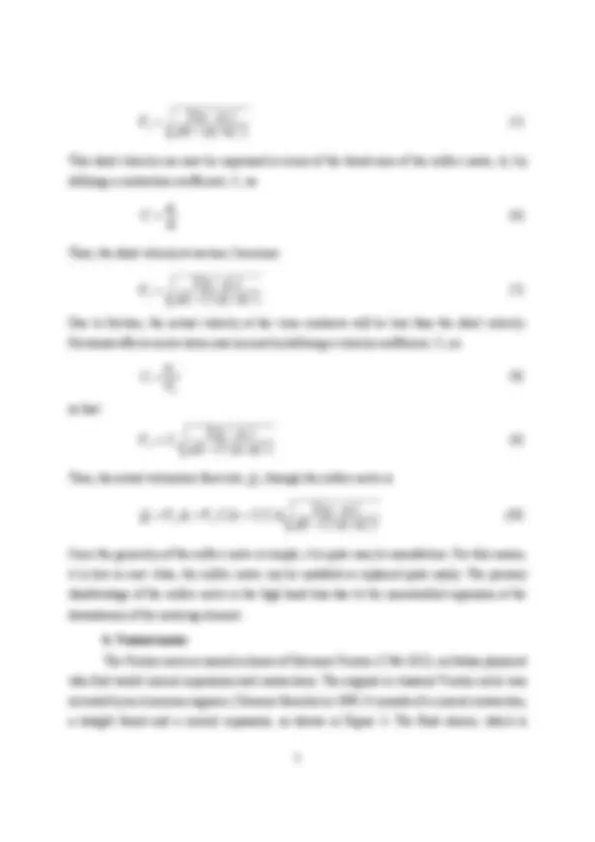
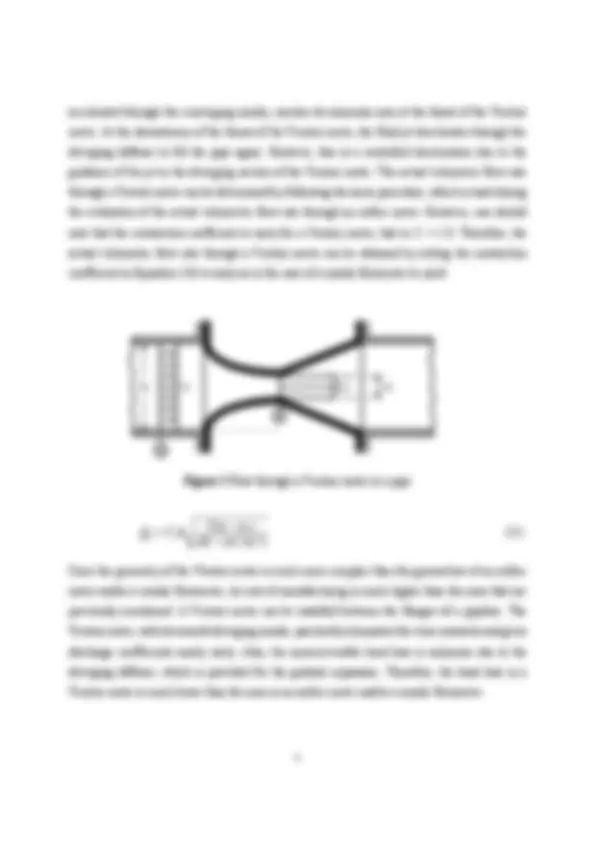
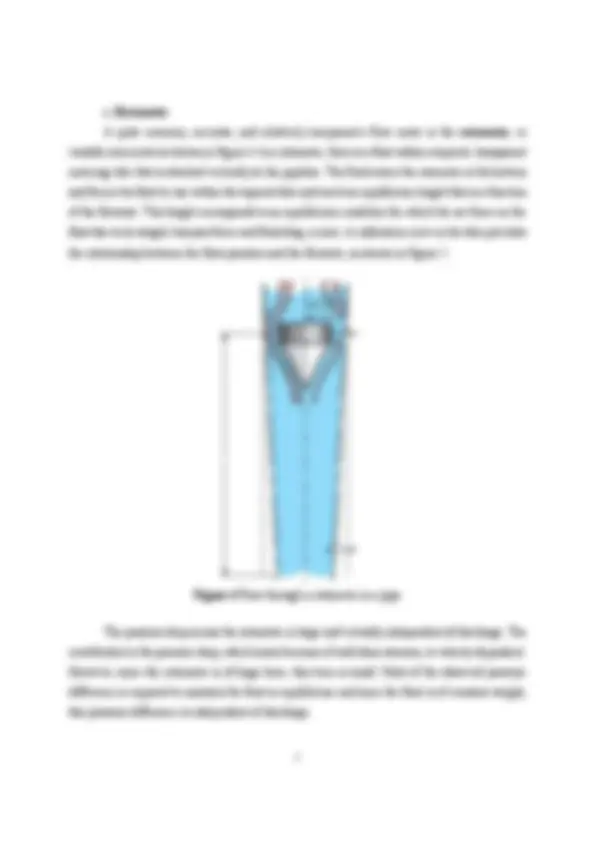
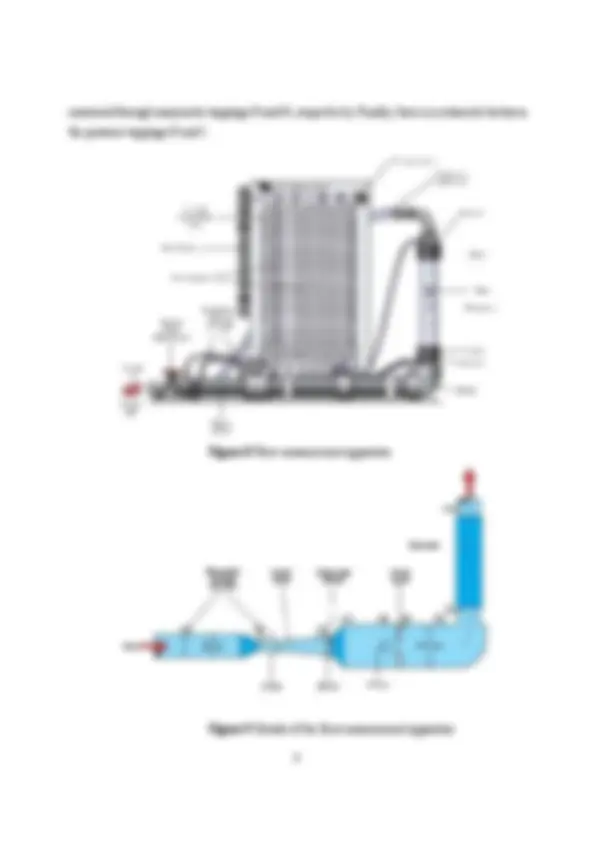
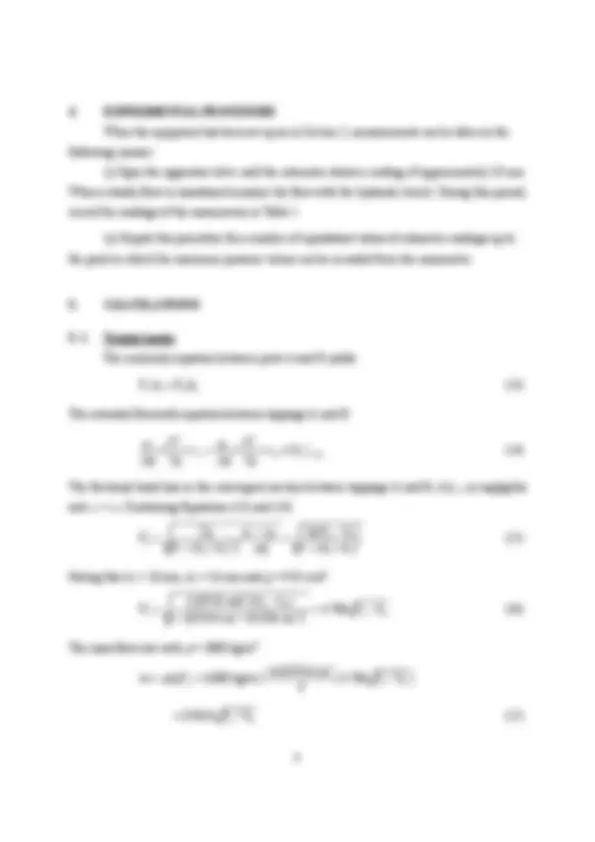
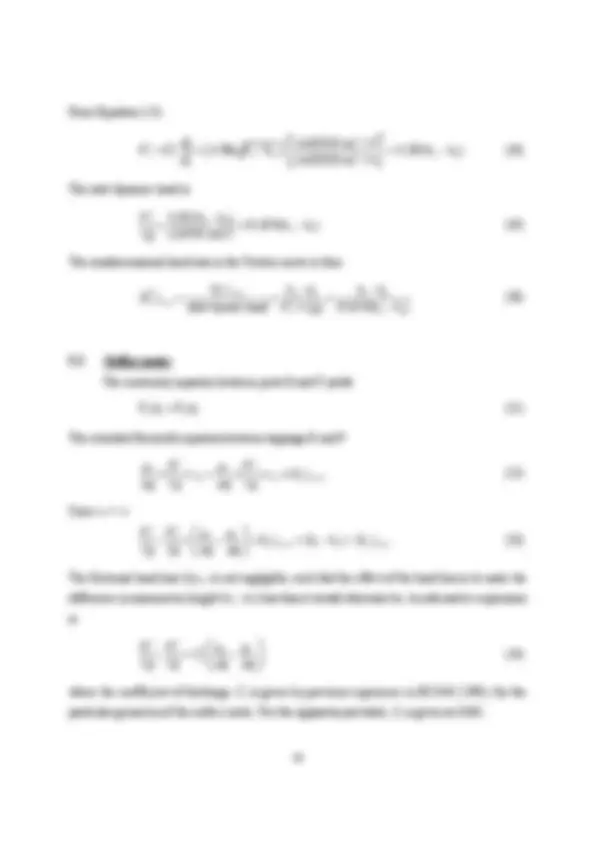
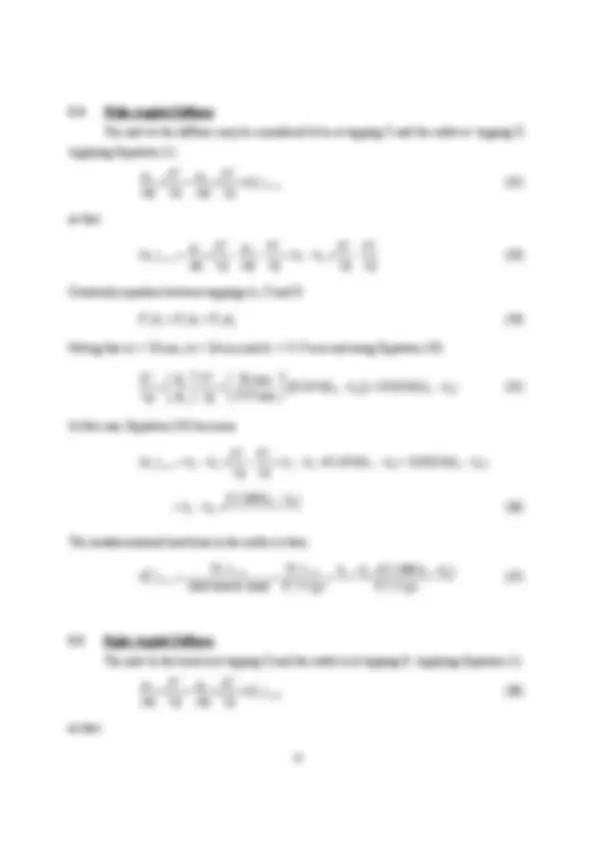
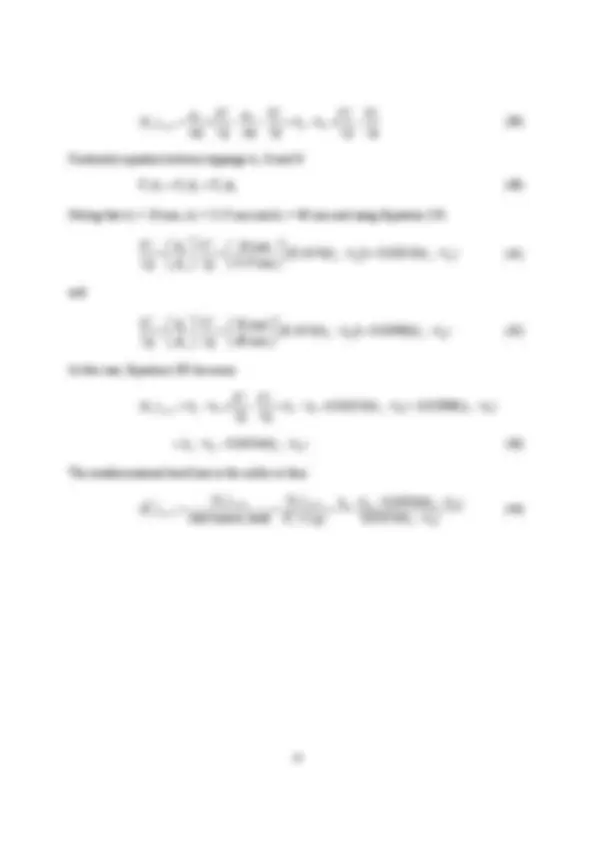
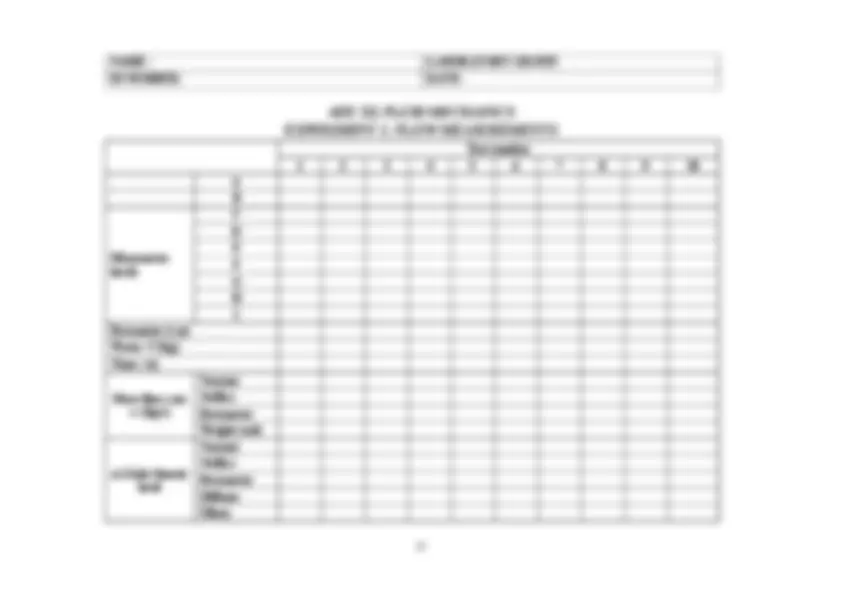
Study with the several resources on Docsity
Earn points by helping other students or get them with a premium plan
Prepare for your exams
Study with the several resources on Docsity
Earn points to download
Earn points by helping other students or get them with a premium plan
Community
Ask the community for help and clear up your study doubts
Discover the best universities in your country according to Docsity users
Free resources
Download our free guides on studying techniques, anxiety management strategies, and thesis advice from Docsity tutors
A detailed theoretical background and experimental setup for various flow measurement techniques, including the steady flow energy equation, bernoulli's equation, and the use of orifice meters, venturi meters, and rotameters. It covers the principles, equations, and experimental procedures for determining the actual volumetric flow rate through these devices. The document also discusses the frictional head losses, contraction coefficients, and velocity coefficients involved in the flow measurement process. The experimental setup includes a hydraulic bench, a venturi meter, an orifice meter, and a rotameter, with various pressure tappings to measure the pressures at different locations. The detailed calculations and equations used to analyze the experimental data and determine the flow rates and head losses. Overall, this document provides a comprehensive understanding of flow measurement techniques in fluid mechanics.
Typology: Study Guides, Projects, Research
1 / 16
This page cannot be seen from the preview
Don't miss anything!
Figure 1 The steady flow energy equation
For steady, adiabatic flow of an incompressible fluid along a stream tube, as shown in
Figure 1, the Bernoulli's equation can be written in the form:
2 2
1 1 2 2
1 2
s f
p V p V
z z h h
g g g g
The term, h f , represents the frictional work per unit weight and is known as the friction head. The
vertical coordinate, z, is called the elevation head. The term p/( g) is known as the static pressure
head, while the term V
2
/(2g) is often referred to as the velocity head. Now, the total head, ht, can
be defined as
z
g
g
p
h t
2
The frictional head loss, h f , may be assumed to arise as a consequence of the vortices in the stream.
Because the flow is viscous a wall shear stress exists and a pressure force must be applied to
overcome it. The consequent increase in flow work appears as an increase in internal energy, and
because the flow is viscous, the velocity profile at any section is nonuniform.
The flow rate in a closed conduit can be measured by using orifice meters, Venturi meters
and rotameters
a. Orifice meter
The orifice meter is a thin plate with an opening, which is usually circular. The fluid stream,
which is accelerated through the orifice, causes flow separation at the sharp edge of the orifice
meter as shown in Figure 2. As a result, a recirculation zone is formed at the downstream of the
orifice meter. The main stream flow continues to accelerate after the throat of the orifice meter to
form a vena contracta at section 2 and then decelerates again to fill the pipe. At the vena contracta,
the flow area passes through a minimum, the streamlines are essentially straight and the pressure
is uniform across this cross section. Applying the continuity equation for the steady flow of an
incompressible and inviscid fluid to the control volume, which is shown in Figure 2, it is possible
to obtain
Figure 2 Flow through an orifice meter in a pipe
1 1 2 2
i i
where V 2 i represents the ideal velocity at section 2. The Bernoulli equation for the steady flow of
an incompressible and inviscid fluid can now be applied between points 1 and 2 along the
streamline, which is shown in Figure 2, to yield
2
2 2
2
1 1 i i
p V p V
Combining Equations (3) and (4) and solving for V 2 i , it is possible to obtain
2
2
Control volume Recirculation zone
Streamline
1
1
accelerated through the converging nozzle, reaches its minimum area at the throat of the Venturi
meter. At the downstream of the throat of the Venturi meter, the fluid jet decelerates through the
diverging diffuser to fill the pipe again. However, this is a controlled deceleration due to the
guidance of the jet in the diverging section of the Venturi meter. The actual volumetric flow rate
through a Venturi meter can be determined by following the same procedure, which is used during
the evaluation of the actual volumetric flow rate through an orifice meter. However, one should
note that the contraction coefficient is unity for a Venturi meter, that is C c = 1.0. Therefore, the
actual volumetric flow rate through a Venturi meter can be obtained by setting the contraction
coefficient in Equation (10) to unity as in the case of a nozzle flowmeter to yield
Figure 3 Flow through a Venturi meter in a pipe
2
1
1 2
p p
t
a v t
Since the geometry of the Venturi meter is much more complex than the geometries of an orifice
meter and/or a nozzle flowmeter, its cost of manufacturing is much higher than the ones that are
previously mentioned. A Venturi meter can be installed between the flanges of a pipeline. The
Venturi meter, with its smooth diverging nozzle, practically eliminates the vena contracta and gives
discharge coefficients nearly unity. Also, the nonrecoverable head loss is minimum due to the
diverging diffuser, which is provided for the gradual expansion. Therefore, the head loss in a
Venturi meter is much lower than the ones in an orifice meter and/or a nozzle flowmeter.
1
V 2 A t V 1 A 1
2
c. Rotameter
A quite common, accurate, and relatively inexpensive flow meter is the rotameter, or
variable area meter as shown in Figure 4. In a rotameter, there is a float within a tapered, transparent
metering tube that is attached vertically to the pipeline. The fluid enters the rotameter at the bottom
and forces the float to rise within the tapered tube and reach an equilibrium height that is a function
of the flowrate. This height corresponds to an equilibrium condition for which the net force on the
float due to its weight, buoyant force and fluid drag, is zero. A calibration curve in the tube provides
the relationship between the float position and the flowrate, as shown in Figure 5.
Figure 4 Flow through a rotamet
Figure 4 Flow through a rotameter in a pipe
The pressure drop across the rotameter is large and virtually independent of discharge. The
contribution to the pressure drop, which arises because of wall shear stresses, is velocity dependent.
However, since the rotameter is of large bore, this term is small. Most of the observed pressure
difference is required to maintain the float in equilibrium and since the float is of constant weight,
this pressure difference is independent of discharge.
Figure 6 Flow measurement apparatus
The sketch of this set-up is provided in Figure 7. The flow rate of the water is controlled by
the gate valve and determined by a Venturi meter, orifice meter and rotameter simultaneously. A
multitube manometer is used to measure pressures at different points of the flow measurement
apparatus. There are eleven manometers in the multitube manometer and nine of these are
connected to the tapping in the pipework and two are left free for other measurements.
The details of the flow measurement apparatus are shown in Figure 3. Water from the
hydraulic bench enters the equipment through a 26 mm pipe, where the pressure is measured
through the manometer tapping A and passes through a Venturi meter. The Venturi meter consists
of a gradually converging section, followed by a throat, and a long gradually diverging section.
Pressures at the throat and the exit of the Venturi meter are measured by using the manometer
tappings B and C, respectively. After a change in cross-section through a rapidly diverging section,
the flow continues along a settling length and through an orifice plate meter. The pressure tappings
D, E and F are used to measure the pressures at the entrance of the larger 51.9 mm diameter pipe,
inlet of the orifice and exit of the orifice, respectively. This is manufactured in accordance with
BS1042, from a plate with a hole of 20 mm diameter through which the fluid flows. There is a 90
0
elbow between the orifice meter and rotameter and pressures at the inlet and exit of the elbow are
measured through manometer tappings G and H, respectively. Finally, there is a rotameter between
the pressure tappings H and I.
Figure 8 Flow measurement apparatus
Figure 9 Details of the flow measurement apparatus
From Equation (13)
2
2 2 2
2 2
2 2
( )(0.016 m) / 4
( )(0.026 m) / 4
B
A B A B A B
A
V V h h h h
The inlet dynamic head is
2
2
2 (2)(9.81 m/s )
A A B
A B
V h h
h h
g
The nondimensional head loss in the Venturi meter is then
2
Inlet kinetic head / (2 ) 0.1674( )
f A C A C A C
f A C
A A B
h h h h h
h
V g h h
5.2 Orifice meter
The continuity equation between ports E and F yields
E E F F
The extended Bernoulli equation between tappings E and F
2 2
E E F F
E F f E F
p V p V
z z h
g g g g
Since zE = zF
2 2
F E E F
f E F E F f E F
V V p p
h h h h
g g g g
The frictional head loss (h f
E-F is not negligible, such that the effect of the head loss is to make the
difference in manometric height (h E
is:
2 2
2
F E E F
d
V V p p
g g g g
where the coefficient of discharge C d is given by previous experience in BS1042 (1981) for the
particular geometry of the orifice meter. For the apparatus provided, C d is given as 0.601.
Combining Equations (21) and (22)
2 2
E F E F
F d d
F E F E
g p p g h h
A A g A A
Noting that d E = 51.9 mm and d F = 20 mm
2
2 2 2
(2)(9.81 m/s )( )
1 [(0.020 m) / (0.0519 m) ]
E F
F E F
h h
V h h
The mass flow rate is then
2
3
( )(0.020 m)
(1000 kg/m ) 2.
F F E F
m A V h h
E F
h h (27)
Applying Equation (1) between tappings E and F by substituting kinetic and hydrostatic
heads would give an elevated value to the head loss for the meter. This is because at an obstruction
such as an orifice plate, there is a small increase in pressure on the pipe wall due to part of the
impact pressure on the plate being conveyed to the pipe wall. BS1042 (Section 1.1 1981) gives an
approximate expression for finding the head loss and generally this can be taken as 0.83 times the
measured head difference.
f E F E F
h h h
Continuity equation between tappings A and F
A A E E
so that using Equation (19)
2 4 2 2
26 mm
2 2 51.9 mm
E A A
A B A B
E
h h h h
g A g
The nondimensional head loss in the orifice is then
2
Inlet kinetic head / (2 ) 0.01054( )
f E F f E F E F
f E F
E A B
h h h h
h
V g h h
5.4 Wide-Angled Diffuser
The inlet to the diffuser may be considered to be at tapping C and the outlet at tapping D.
Applying Equation (1):
2 2
C C D D
f C D
p V p V
h
g g g g
so that
2 2 2 2
C C D D C D
f C D C D
p V p V V V
h h h
g g g g g g
Continuity equation between tappings A, C and D
A A C C D D
Noting that d A = 26 mm, d C = 26 mm and d D = 51.9 mm and using Equation (19)
2 4 2 2
26 mm
2 2 51.9 mm
D A A
A B A B
D
h h h h
g A g
In this case, Equation (33) becomes
2 2
A D
f C D C D C D A B A B
h h h h h h h h h
g g
A B
C D
h h
h h
The nondimensional head loss in the orifice is then
2 2
Inlet kinetic head / (2 ) / (2 )
f C D f C D C D A B
f C D
C A
h h h h h h
h
V g V g
5.5 Right Angled Diffuser
The inlet to the bend is at tapping G and the outlet is at tapping H. Applying Equation (1):
2 2
G G H H
f G H
p V p V
h
g g g g
so that
2 2 2 2
G G H H G H
f G H G H
p V p V V V
h h h
g g g g g g
Continuity equation between tappings A, G and H
A A G G H H
Noting that d A = 26 mm, d G = 51.9 mm and d H = 40 mm and using Equation (19)
2 4 2 2
26 mm
2 2 51.9 mm
G A A
A B A B
G
h h h h
g A g
and
2 4 2 2
26 mm
2 2 40 mm
H A A
A B A B
H
h h h h
g A g
In this case, Equation (39) becomes
2 2
G H
f G H G H G H A B A B
h h h h h h h h h
g g
G H A B
h h h h (43)
The nondimensional head loss in the orifice is then
2
Inlet kinetic head / (2 ) 0.01054( )
f G H f G H G H A B
f G H
G A B
h h h h h h
h
V g h h