
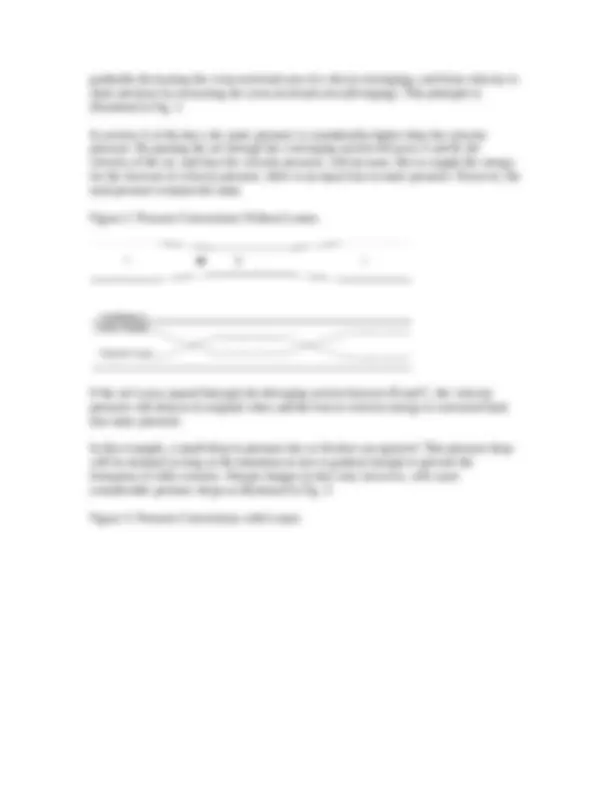
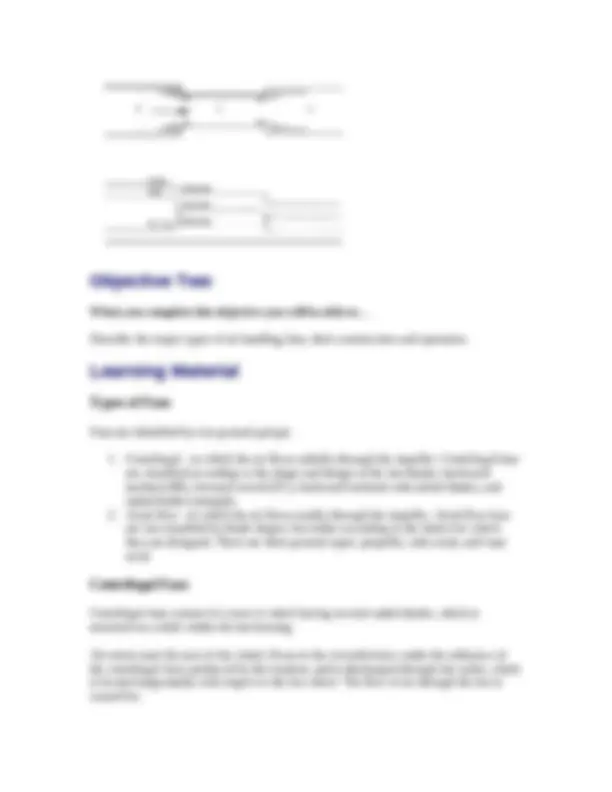
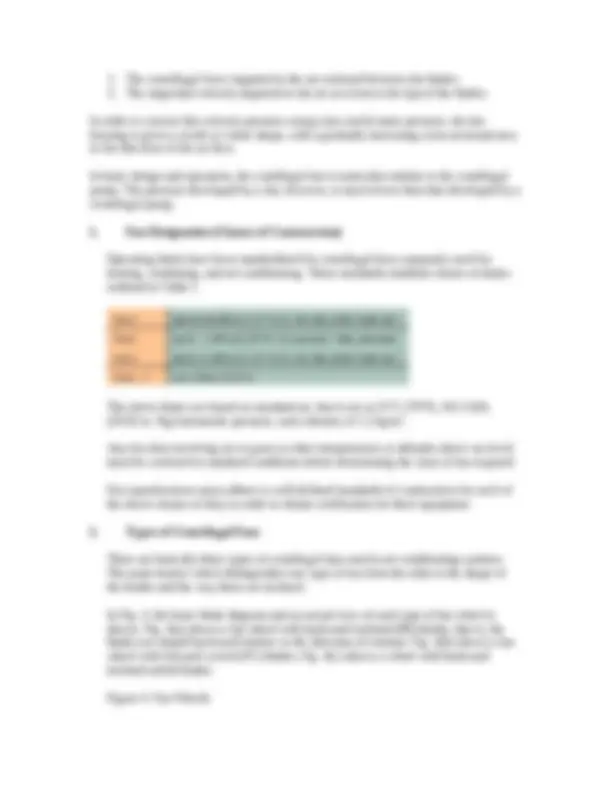
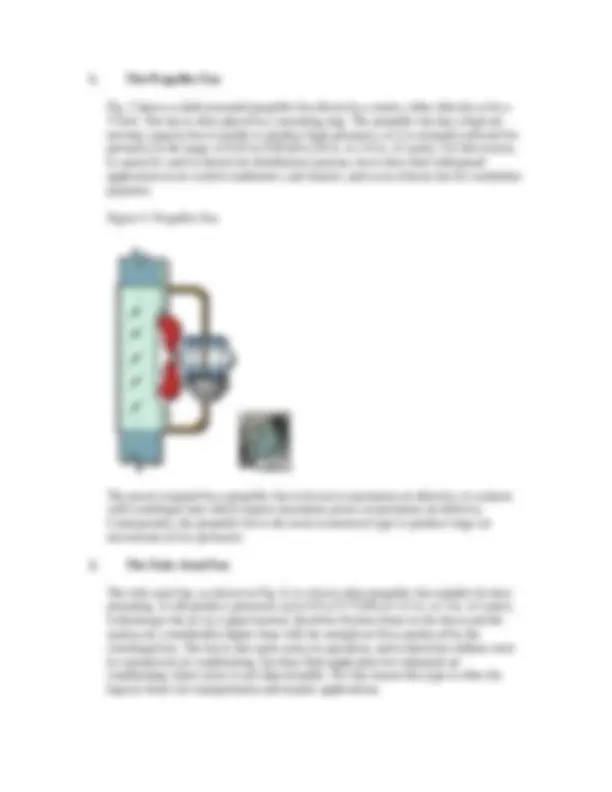
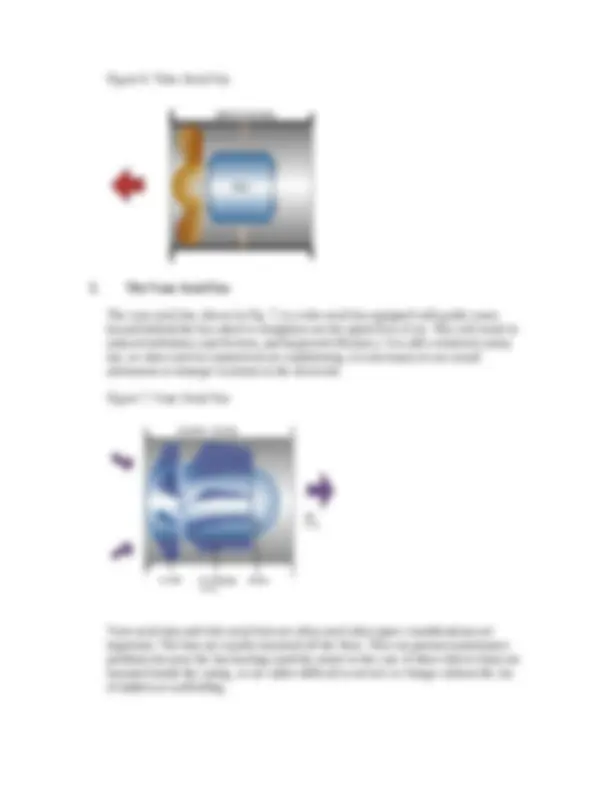
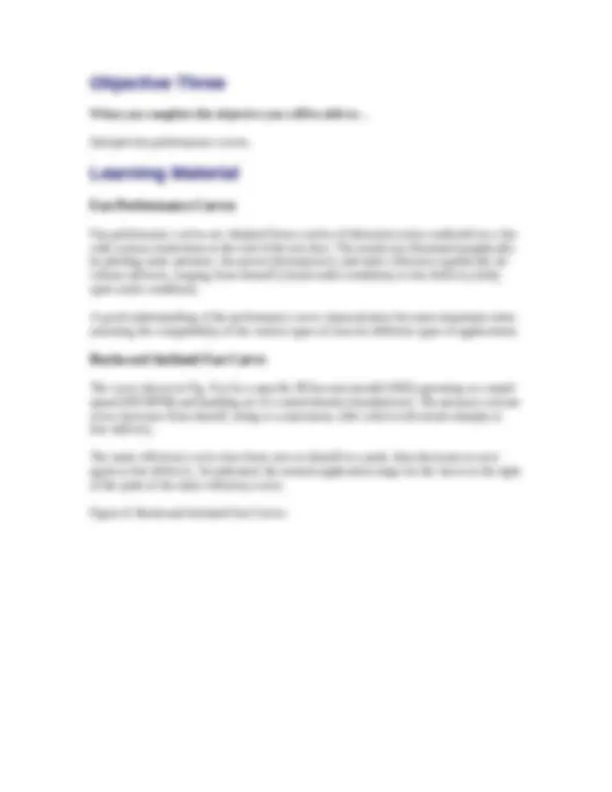
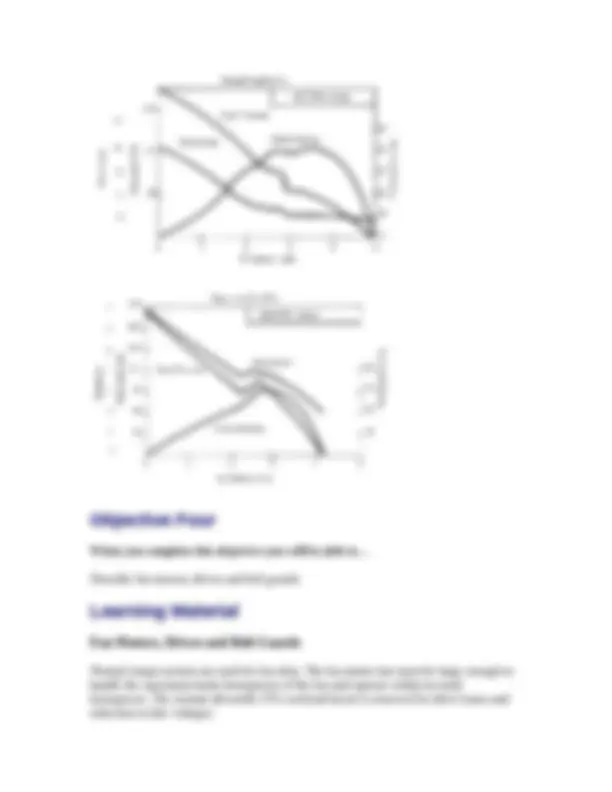
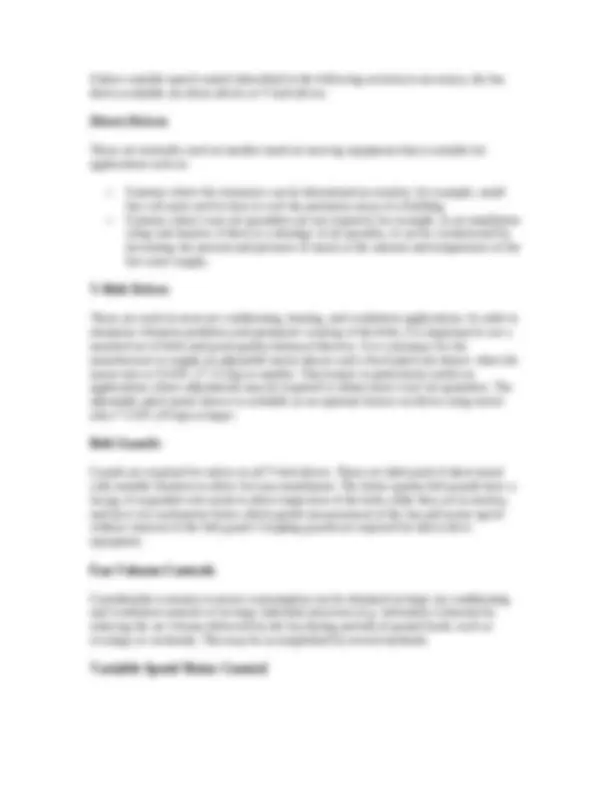
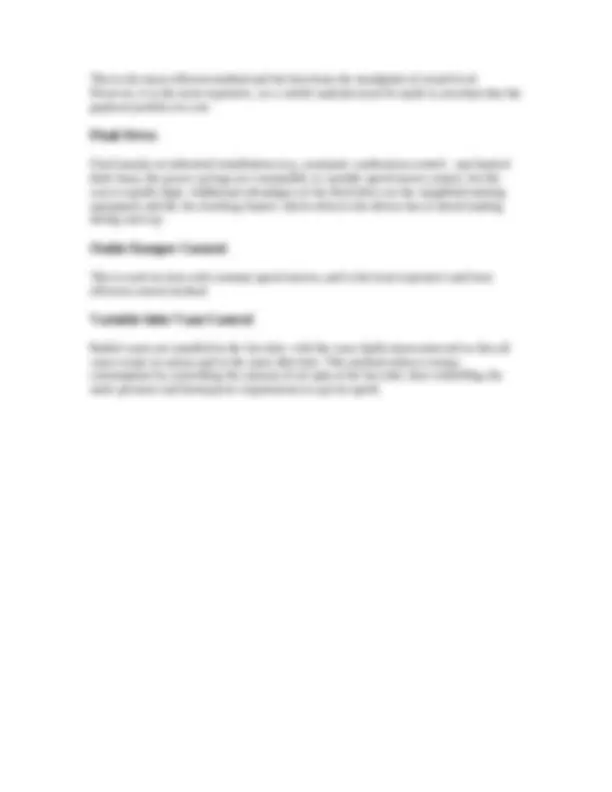
Study with the several resources on Docsity
Earn points by helping other students or get them with a premium plan
Prepare for your exams
Study with the several resources on Docsity
Earn points to download
Earn points by helping other students or get them with a premium plan
Community
Ask the community for help and clear up your study doubts
Discover the best universities in your country according to Docsity users
Free resources
Download our free guides on studying techniques, anxiety management strategies, and thesis advice from Docsity tutors
A comprehensive overview of air distribution systems, focusing on the role of fans in air movement. It delves into the types of fans used in air conditioning systems, their construction, operation, and performance characteristics. The document also explores fan motors, drives, and belt guards, highlighting their importance in fan operation and energy efficiency.
Typology: Summaries
1 / 15
This page cannot be seen from the preview
Don't miss anything!
When you complete this chapter you will be able to… Describe the air flow behaviour and movement of air through distribution systems.
Here is what you will be able to do when you complete each objective.
An air conditioning system consists of a group of components that operate together in a controlled manner to produce specific conditions in the air within a space or building: This chapter will cover the principles of the following air conditioning components:
When you complete this objective you will be able to… Discuss the theory of air flow and pressure conversions.
Before taking a look at the various types of fans used in air moving systems, first consider what is involved in air movement.
The energy imparted to the air by a fan is in the form of pressure energy. This pressure is normally quite small, and manometers can be used to measure it. There are three different kinds of pressure developed by a fan: static, velocity, and total pressure. Each pressure can be read separately, depending upon the way the manometer is connected to the outlet duct. Static pressure is that pressure exerted by the air on duct walls; it is similar to the pressure exerted by steam or water on the interior walls of piping. This pressure can be read by connecting the manometer at right angles to the duct as shown in Fig. 1(a). It is the static pressure of the air that overcomes the resistance of ducts, filters, etc. Velocity pressure is pressure over and above static pressure. It is caused by the impact of the air flowing through a duct and it is felt only by the surfaces the air actually strikes. Assume that the duct in Fig. 1 is under pressure but that the end is closed off by a damper so that there is no air flow. If a vane is hung in this duct, the static pressure on either side will be equal, thus the vane will change vertically. When the damper is opened again, the vane will tip backwards due to the impact of the moving air striking it. This added pressure is velocity pressure. By connecting one end of the manometer at right angles to the duct wall and the other end with the opening facing the air flow, as in Fig. 1(b), the velocity pressure can be measured. The total pressure, the sum of static and velocity pressure, can be measured by connecting the manometer as shown in Fig. 1(c). Figure 1. Measuring Air Pressure in a Duct
Under certain conditions it may be necessary to convert static pressure in duct systems to velocity pressure and vice versa. Conversion of static to velocity pressure is done by
When you complete this objective you will be able to… Describe the major types of air handling fans, their construction and operation.
Fans are identified by two general groups:
Centrifugal fans consist of a rotor or wheel having several radial blades, which is mounted on a shaft within the fan housing. Air enters near the axis of the wheel, flows to the circumference under the influence of the centrifugal force produced by the rotation, and is discharged through the outlet, which is located tangentially with respect to the fan wheel. The flow of air through the fan is caused by:
Example 1: This is a comparison of centrifugal fan performance delivering 8.166 m^3 /s (17 303 cfm) against 0.625 kPa (2.5 in.) static pressure: 900 mm (36 in.) diameter backward incline fan: 810 r/min; 6.7 kW (9 bhp) 900 mm (36 in.) diameter forward curved fan: 450 r/min; 8.12 kW (10. bhp) 900 mm (36 in.) diameter backward inclined airfoil: 815 r/min; 6.6 kW (8.8 bhp) This example illustrates the difference in speed required for each type of fan. It also shows that both fans with the backward inclined blades require less horsepower to deliver the specified air volume, and are consequently more efficient than the forward curved fans. Higher efficiencies result in the backward inclined fans being quieter in operation. This conclusion holds true for medium to large sized fans. In sizes smaller than 600 mm (24 in.) diameter, the high speed of both types of backward inclined fans may require high belt speeds, causing more noise. Conversely, the lower speed (for the same air volume) of the forward curved design makes them more desirable for small fans. The above example also points out that the backward inclined airfoil fan is more efficient than the backward inclined fan because the aerodynamic shape of the airfoil blades permits smoother airflow through the wheel. But the magnitude of this difference in efficiency can rarely justify the higher initial cost of the airfoil fan when the system involved operates in the low pressure range; i.e. lower than 0.75 kPa (3 in.) static pressure. This is the reason why the backward inclined airfoil fan is mostly used for high capacity, high pressure applications, where power savings may outweigh its higher initial cost. The low rotation speed characteristic of the forward curved fan is sometimes highly desirable. For instance, this feature is particularly adaptable to factory assembled air handling units having two or more fans on a common shaft. The higher speed of the backward inclined fan may require a shaft of prohibitive size.
While air flows radially away from the shaft in the centrifugal fan, the flow in axial fans is parallel to the shaft. Axial fans can be divided into three general types:
1. The Propeller Fan Fig. 5 shows a shaft-mounted propeller fan driven by a motor, either directly or by a V-belt. The fan is often placed in a mounting ring. The propeller fan has a high air- moving capacity but is unable to produce high pressures, so it is normally selected for pressures in the range of 0.03 to 0.06 kPa (1/8 in. to 1/4 in. of water). For this reason, it cannot be used in ducted air distribution systems, but it does find widespread application in air-cooled condensers, unit heaters, and as an exhaust fan for ventilation purposes. Figure 5. Propeller Fan The power required by a propeller fan is lowest at maximum air delivery, in contrast with centrifugal fans which require maximum power at maximum air delivery. Consequently, the propeller fan is the most economical type to produce large air movements at low pressures. 2. The Tube Axial Fan The tube axial fan, as shown in Fig. 6, is a heavy-duty propeller fan suitable for duct mounting. It will produce pressures up to 0.6 or 0.75 kPa (2 1/2 in. or 3 in. of water). It discharges the air in a spiral motion, therefore friction losses in the ducts and the system are considerably higher than with the straight air flow produced by the centrifugal fan. The fan is also quite noisy in operation, and is therefore seldom used in commercial air conditioning, but does find application for industrial air conditioning where noise is not objectionable. For this reason this type is often the logical choice for transportation and marine applications.
When you complete this objective you will be able to… Interpret fan performance curves.
Fan performance curves are obtained from a series of laboratory tests conducted on a fan with various restrictions at the end of the test duct. The results are illustrated graphically by plotting static pressure, fan power (horsepower), and static efficiency against the air volume delivery, ranging from shutoff (closed outlet condition) to free delivery (fully open outlet condition). A good understanding of the performance curve characteristics becomes important when assessing the compatibility of the various types of fans for different types of applications.
The curve shown in Fig. 8 is for a specific BI fan size (model #365) operating at a stated speed (850 RPM) and handling air of a stated density (standard air). The pressure-volume curve increases from shutoff, rising to a maximum, after which it decreases sharply to free delivery. The static efficiency curve rises from zero at shutoff to a peak, then decreases to zero again at free delivery. As indicated, the normal application range for the fan is to the right of the peak of the static efficiency curve. Figure 8. Backward Inclined Fan Curves
The power characteristic curve rises from shutoff to a maximum and then falls off when approaching free delivery. This is the reason why the BI fan is referred to as a non- overloading fan. The following example illustrates this point: Example 2: Assume that the model 365 BI fan was selected to deliver 6.0 m^3 /s (12 713 cfm) of air against 0.75 kPa (3 in.) S.P. (point A on the curve in Fig. 8). The corresponding fan power requirement is 6.7 kW (9 bhp). After the installation was completed, the actual measured static pressure was only 0.5 kPa (2 in.), meaning that the fan was delivering 7. m^3 /s (15 885 cfm) (point B) instead of 6.0 m^3 /s and the fan power was approximately 6. kW (8.8 bhp); i.e. a 3% decrease in power. As will be seen in the following discussion, the results are drastically different when a similar situation occurs with a FC fan.
The curve shown in Fig. 9 for an FC fan shows that the static pressure curve falls off slightly as the air volume increases from shutoff, then rises to a maximum, after which it decreases to free delivery. The power requirements rise from a minimum at shutoff to a maximum at free delivery. Again, the normal application range for the fan is to the right of the peak of the static efficiency curve because the fan operation can be unstable when operating on the left portion of the curve. Figure 9. Forward Curved Fan Curves
When you complete this objective you will be able to… Describe fan motors, drives and belt guards.
Normal torque motors are used for fan duty. The fan motor size must be large enough to handle the maximum brake horsepower of the fan and operate within its rated horsepower. The normal allowable 15% overload factor is reserved for drive losses and reduction in line voltages.
Unless variable speed control (described in the following section) is necessary, the fan drives available are direct drives or V-belt drives.
These are normally used on smaller sized air moving equipment that is suitable for applications such as: Systems where the resistance can be determined accurately; for example, small fan coil units used to heat or cool the perimeter areas of a building. Systems where exact air quantities are not required; for example, in an installation using unit heaters, if there is a shortage of air quantity, it can be counteracted by increasing the amount and pressure of steam or the amount and temperature of the hot water supply.
These are used on most air conditioning, heating, and ventilation applications. In order to minimize vibration problems and premature wearing of the belts, it is important to use a matched set of belts and good quality balanced sheaves. It is customary for the manufacturer to supply an adjustable motor sheave and a fixed pitch fan sheave when the motor size is 5.6 kW, (7 1/2 hp) or smaller. This feature is particularly useful on applications where adjustments may be required to obtain more exact air quantities. The adjustable pitch motor sheave is available as an optional feature on drives using motor sizes 7.5 kW (10 hp) or larger.
Guards are required for safety on all V-belt drives. These are fabricated of sheet metal with suitable brackets to allow for easy installation. The better quality belt guards have a facing of expanded wire mesh to allow inspection of the belts while they are in motion, and have two tachometer holes which permit measurement of the fan and motor speed without removal of the belt guard. Coupling guards are required for direct drive equipment.
Considerable economy in power consumption can be obtained on large air conditioning and ventilation systems or on large industrial processes (e.g. laboratory exhausts) by reducing the air volume delivered by the fan during periods of partial loads, such as evenings or weekends. This may be accomplished by several methods.