
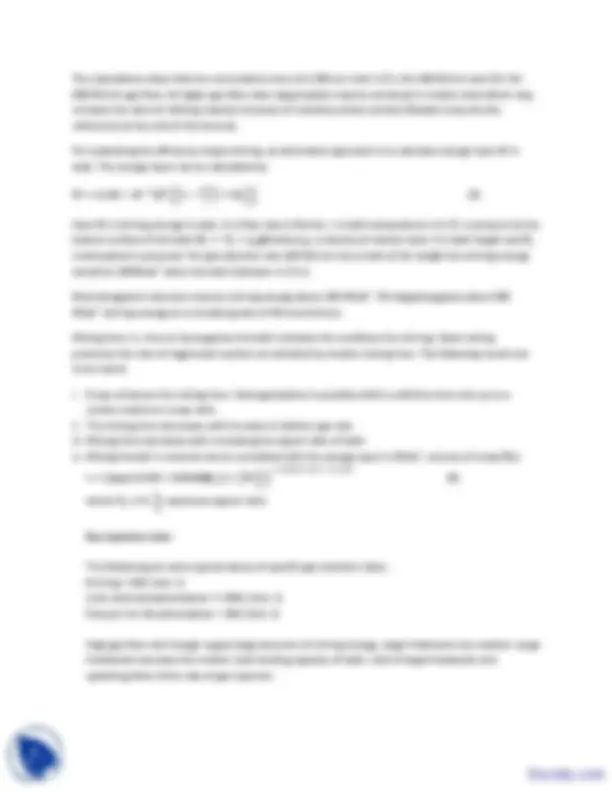
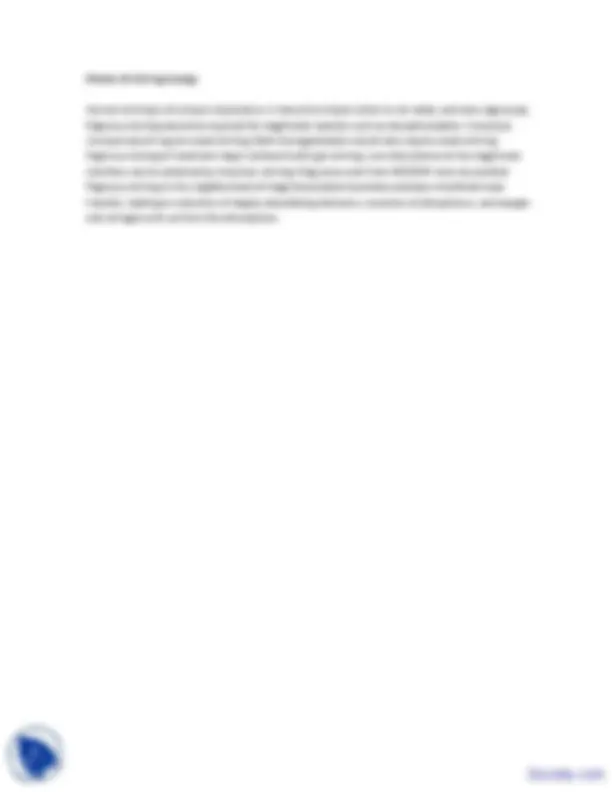
Study with the several resources on Docsity
Earn points by helping other students or get them with a premium plan
Prepare for your exams
Study with the several resources on Docsity
Earn points to download
Earn points by helping other students or get them with a premium plan
Community
Ask the community for help and clear up your study doubts
Discover the best universities in your country according to Docsity users
Free resources
Download our free guides on studying techniques, anxiety management strategies, and thesis advice from Docsity tutors
The major points which I found very informative are:Evolution of Ladle Treatment, Basics of Gas Stirring, Mixing Time, Gas Injection Rates, Choice of Stirring Energy, Ladle Metallurgy, Secondary Steelmaking, Injection Metallurgy, Synthetic Slag Practice
Typology: Study notes
1 / 4
This page cannot be seen from the preview
Don't miss anything!
Lecture 21: Evolution of ladle Treatment and Requirements Contents: Preamble What modifications are required? Basics of gas stirring Mixing time Gas injection rates Choice of stirring energy Key words: Ladle metallurgy, Secondary steelmaking, injection metallurgy, synthetic slag practice Preamble In steelmaking, ladles are employed to transfer molten steel from BOF/EAF to ingot casting or continuous casting. It has been realized that ladles can be used very effectively as a reactor which can perform any of the following functions:
Enough free board height in the ladle must be available to accommodate the quantity of slag required for refining and to absorb inclusions. Additional heating may be required to keep the molten steel to the teeming temperature. This can be achieved either by tapping steel at slightly higher temperature or to provide addition heating arrangement in the ladle itself. In many situations it is required to inject the slag forming materials either for refining or for inclusion engineering. In this case suitable injection device must also be available. Above all, the most important would be the selection of refractory (see lecture 9 and 10) to meet the refining requirements. Refractory materials for injection elements and their fixing must also be considered. Basics of gas stirring Argon is usually bubbled into the molten steel covered with slag either through the top lance or through a porous plug fitted at the bottom. A plume of gas rises upwards when gas is injected through the bottom. The stirring homogenizes bath composition and temperature. With centrally placed nozzle at the bottom, stirring action is small near the bottom of the ladle. An asymmetrically placed bubble plume gives velocities near the bottom which are greater than for symmetrically placed nozzle. The liquid flow in the ladle occurs via bulk motion of the metal. Very roughly, characteristic velocity vc for gas bubbling is vc = � Qg H^2 V � 1 / 3 (1) Where Q is gas flow rate� m^3 s �, g is� m s^2 �, H is bath height (m) and V is bath volume (m (^3) ). For gas injection at 50 l/min in a ladle of bath diameter 3.5m and bath height 3.5m, equation 1 calculates 0.14 m/s as the gas bubbling velocity. At velocities greater than 0.3 m/s at the slag/metal interface slag droplets may be entrained by the metal flowing along the interface and into the melt. For gas stirring recirculation rate of molten steel is of interest. The mass flux in (tons/s) of entrained steel passing through the top section of the bubble plume can be calculated by the following semi- empirical equation: Ṁ = 13. 3 (H + 0. 8 ) �ln � 1 + H
Choice of stirring energy Correct stirring is of utmost importance. It should be known when to stir what, and how vigorously. Vigorous stirring would be required for slag/metal reaction such as desulphurization. Inclusions removal would require weak stirring. Bath homogenization would also require weak stirring. Vigorous mixing of metal and slag is achieved with gas stirring. Less disturbance at the slag/metal interface can be obtained by induction stirring. Slag carry-over from BOF/EAF must be avoided. Vigorous stirring in the neighborhood of slag/metal phase boundary activates interfacial mass transfer, leading to reduction of slag by deoxidizing elements, reversion of phosphorus, and oxygen and nitrogen pick up from the atmosphere.