
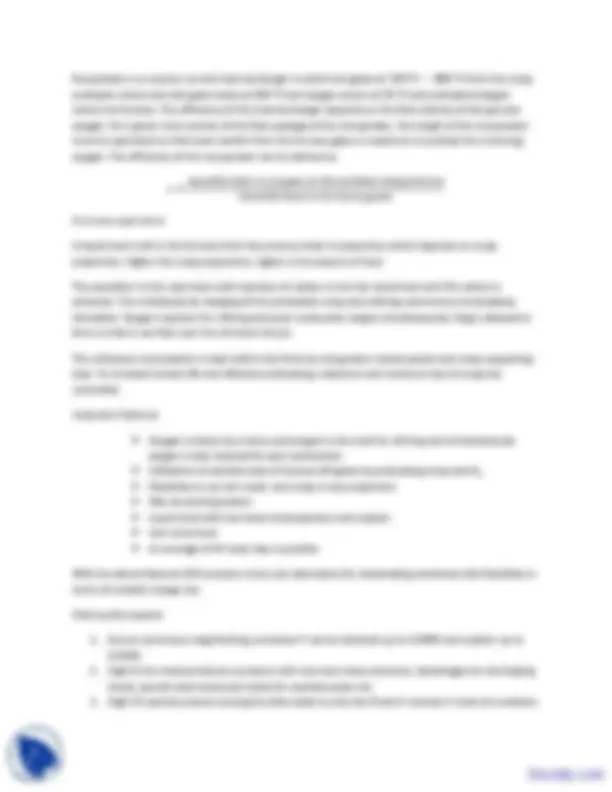
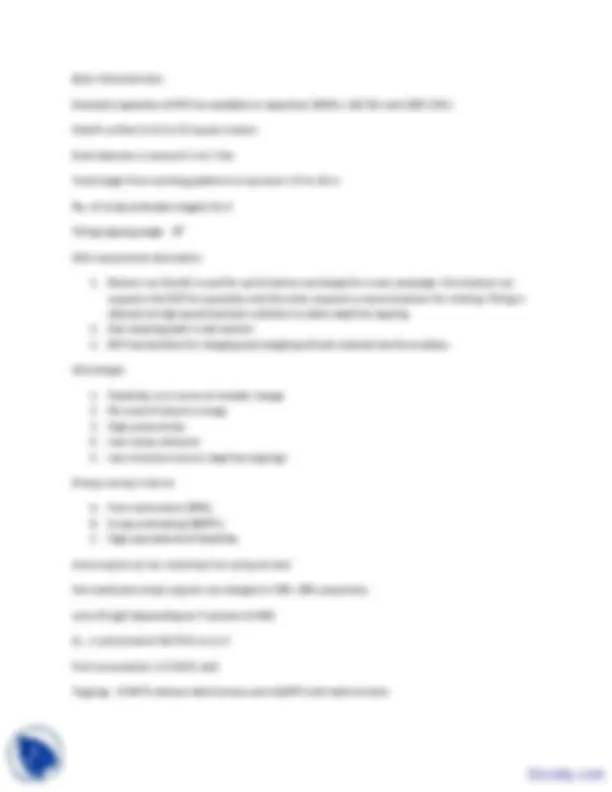
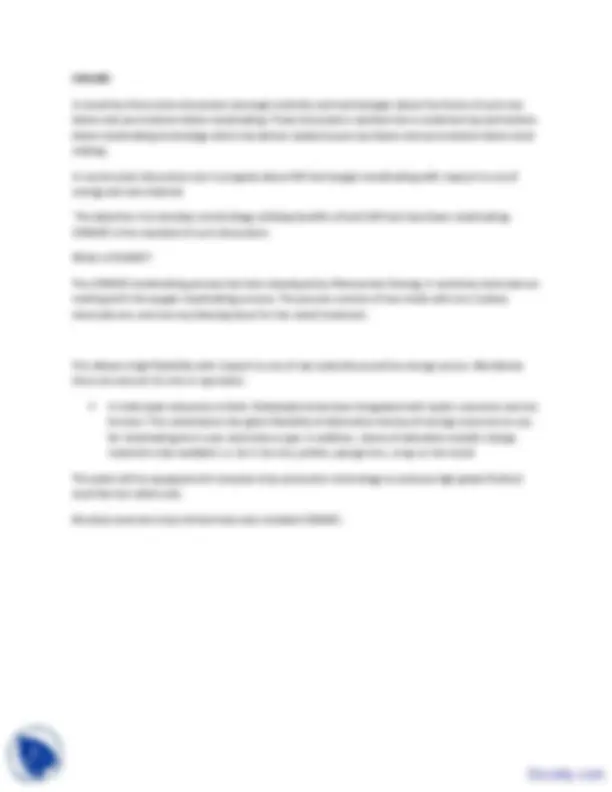
Study with the several resources on Docsity
Earn points by helping other students or get them with a premium plan
Prepare for your exams
Study with the several resources on Docsity
Earn points to download
Earn points by helping other students or get them with a premium plan
Community
Ask the community for help and clear up your study doubts
Discover the best universities in your country according to Docsity users
Free resources
Download our free guides on studying techniques, anxiety management strategies, and thesis advice from Docsity tutors
Two emerging steelmaking technologies: energy optimizing furnace (eof) and conarc. Eof is a combination of three interconnected reactors - a furnace, preheater, and recuperator - that optimizes energy usage and scrap preheating. Conarc is a combined top and bottom blown steelmaking technology that utilizes the benefits of both electric arc furnace (eaf) and oxygen steelmaking. Both technologies aim to improve steelmaking processes by reducing energy consumption and increasing flexibility in raw material usage.
Typology: Study notes
1 / 5
This page cannot be seen from the preview
Don't miss anything!
Lecture 19: Emerging Steelmaking Technologies Contents: Basis Energy Optimizing Furnace CONARC Key words: EOF, CONARC Basis:
Figure19.1: Arrangement of furnace, scrap preheating chamber and a recuperator in an Energy optimizing Furnace Design of each reactor and their integration with each other is important such that furnace off gas exits the system at a low temperature to the extent possible and at the same time scrap is heated to the desired temperature and steel of required quality is tapped. Furnace The furnace is refractory lined and has a provision for injection of carbon and oxygen. Oxygen can be injected both at high speed to promote decarburization and at low speed to promote post combustion. Preheater A preheater is installed at the top of furnace to preheat the scrap by the waste gases flowing upward from the furnace. For scrap preheating residence time (R T) of the waste gas in the preheater R T = Diameter of the preheater flow velocity of exit gas =^0.^785 D^3 Q (1) should be maximum. D is diameter of preheater and Q is volume flow rate of furnace gases. Both D and Q are important. For a given Q, diameter of preheater must be such that furnace gases can cool within 700 ℃ to 800 ℃ from 1300 − 1350 ℃. The exit temperature of gas from the preheater is the inlet temperature of gas to the recuperator. Scrap size is also important to heat scrap to the desired temperature. Smaller size scrap can be preheated efficiently. Recuperator
Basic Characteristics Standard capacities of EOF are available in capacities 30/40 t, 60/ 80 t and 100/ 120 t. Hearth surface is 6.6 to 22 square meters Shell diameter is around 5.3 to 7.5m Total height from working platform to top level =17 to 25 m No. of scrap-preheater staged 1to 2 Tilting tapping angle 80 Main equipments description
In seventies there were discussions amongst scientists and technologies about the future of pure top blown and pure bottom blown steelmaking. These discussions resulted into a combined top and bottom blown steelmaking technology which has almost replaced pure top blown and pure bottom blown steel making. In recent years discussions are in progress about EAF and oxygen steelmaking with respect to use of energy and raw material. The objective is to develop a technology utilizing benefits of both EAF and top blown steelmaking. CONARC is the resultant of such discussions. What is CONARC? The CONARC steelmaking process has been developed by Mannesman Demag. It combines electrode arc melting with the oxygen steelmaking process. The process consists of two shells with one 3 phase electrode arm and one top blowing lance for hot metal treatment. This allows a high flexibility with respect to use of raw materials as well as energy source. Worldwide there are around 12 units in operation.