
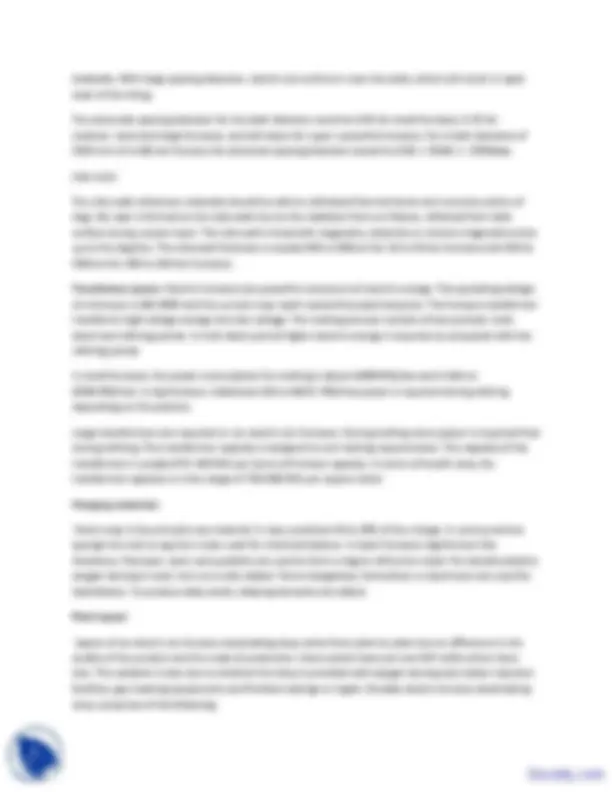
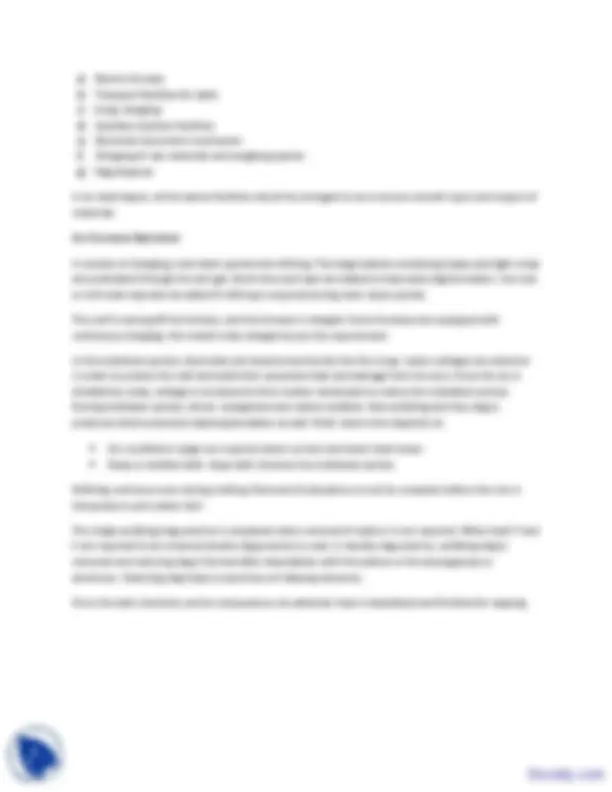
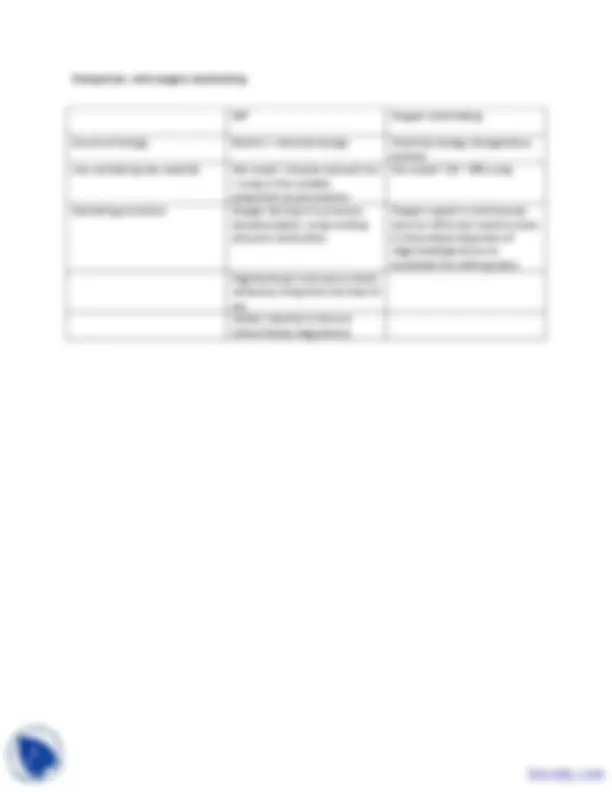
Study with the several resources on Docsity
Earn points by helping other students or get them with a premium plan
Prepare for your exams
Study with the several resources on Docsity
Earn points to download
Earn points by helping other students or get them with a premium plan
Community
Ask the community for help and clear up your study doubts
Discover the best universities in your country according to Docsity users
Free resources
Download our free guides on studying techniques, anxiety management strategies, and thesis advice from Docsity tutors
The major points which I found very informative are:Electric Furnace Steelmaking, Type of Electric Furnaces, Electric Arc Furnace, Transformer Power, Charging Materials, Plant Layout, Arc Furnace Operation, Comparison with Oxygen Steelmaking, Melt-Down Period
Typology: Study notes
1 / 5
This page cannot be seen from the preview
Don't miss anything!
LECTURE 15 Electric Furnace Steelmaking Contents: Introduction Type of Electric furnaces Construction of AC Electric Arc Furnace Transformer power Charging materials Plant layout Arc furnace operation Comparison with oxygen steelmaking Key words: Electric arc furnace, Melt-down period, Transformer power Introduction: Steelmaking in electric arc furnace has emerged as an important steelmaking process in recent years. The flexibility and easy adoptability of EAF steelmaking to accommodate the fluctuating market demand have evolved into the concept of mini steel plants to produce different grades of finished products (long or flat or mixed ) of plain carbon or alloy steels from scrap and other metallic charge materials. Although scrap is the preferred raw material but sponge iron and iron carbide are being used regularly in most plants because of shortage of steel scrap and to dilute the concentration of tramp elements. Several developments in the design and operation have made EAF steelmaking to contribute significantly to the overall total production of steel in the world. According to an estimate, the proportion of electric steel is around 40 to 45% in the total world steel production. It must be noted that EAF consumes lot of electric energy and hence the cost and availability of electrical power are important issues in electric steel development. Type of Electric furnaces: In principle an electric arc is formed between the electrode and the metallic charge and charge is heated from the arc radiation. Electric arc furnaces are of two type (a) alternating current and (b) direct current. In alternating current, furnace operates by means of electric current flowing from one electrode of three to another through the metallic charge. In direct current, the current flows from carbon electrode, which acts as cathode, to an anode embedded in the bottom of the furnace.
Construction of AC Electric Arc Furnace The furnace consists of a steel shell, lined with suitable refractory materials and is mounted on the tilting mechanism. The shell thickness is around 0.005 times the shell diameter. Three electrodes enter through the roof. The hood may be swung away for charging. Heat is generated by the hot area formed between the electrodes and the charge. Hearth The hearth contains metal and slag. The hearth lining consists of backing lining and working lining. The backing lining is few layers of high fired magnesite bricks on which working lining is rammed with either dolomite or magnesite mass. Permeable blocks or porous refractory elements are introduced through the bottom to inject inert gas for stirring. The EAF steel bath is shallow; the aspect ratio of the bath is around 0.2 to 0.22. Roof The roof is exposed to more heat than other furnace elements. Its lining is also subjected to radiant heat reflected from the walls and slag. High alumina bricks and magnesite – chromite bricks are used for roof lining. The roof lining is water cooled which increases the life of refractory lining to at least 10-20 times more than without water cooling. The roof has three holes to allow insertion of the electrodes. Electrode A typical alternating current operated EAF has three electrodes. Electrodes are round in section, and typically in segments with threaded coupling, so that as the electrodes wear, new segments can be added. Graphite electrodes are preferred over carbon electrodes because of better electrical conductivity. The electrodes are automatically raised and lowered by a positioning system. Electrode consumption depends on
a) Electric furnace b) Transport facilities for ladle c) Scrap charging d) Auxiliary injection facilities e) Electrode movement mechanism f) Charging of raw materials and weighing system g) Slag disposal. In an ideal layout, all the above facilities should be arranged so as to ensure smooth input and output of materials. Arc Furnaces Operation It consists of charging, melt down period and refining. The large baskets containing heavy and light scrap are preheated through the exit gas. Burnt lime and spar are added to help early slag formation. Iron one or mill scale may also be added if refining is required during melt- down period. The roof is swung off the furnace, and the furnace is charged. Some furnaces are equipped with continuous charging. Hot metal is also charged as per the requirement. In the meltdown period, electrodes are lowered and bored into the scrap. Lower voltages are selected in order to protect the roof and walls from excessive heat and damage from the arcs. Once the arc is shielded by scrap, voltage is increased to form molten metal pool to reduce the meltdown period. During meltdown period, silicon, manganese and carbon oxidizes. Also oxidizing and limy slag is produces which promotes dephosphorization as well. Melt- down time depends on
Comparison with oxygen steelmaking EAF Oxygen steelmaking Source of energy Electric + chemical energy Chemical energy; Autogeneous process Iron containing raw material Hot metal + directly reduced iron