
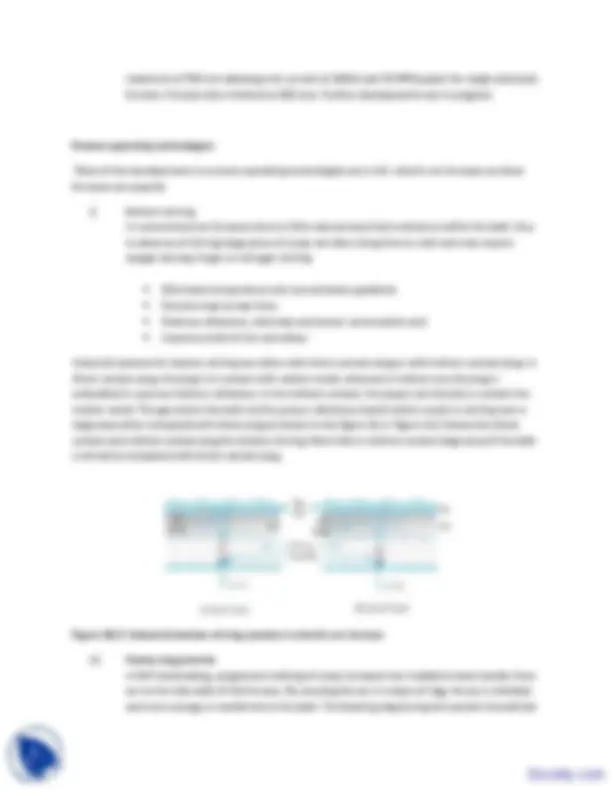
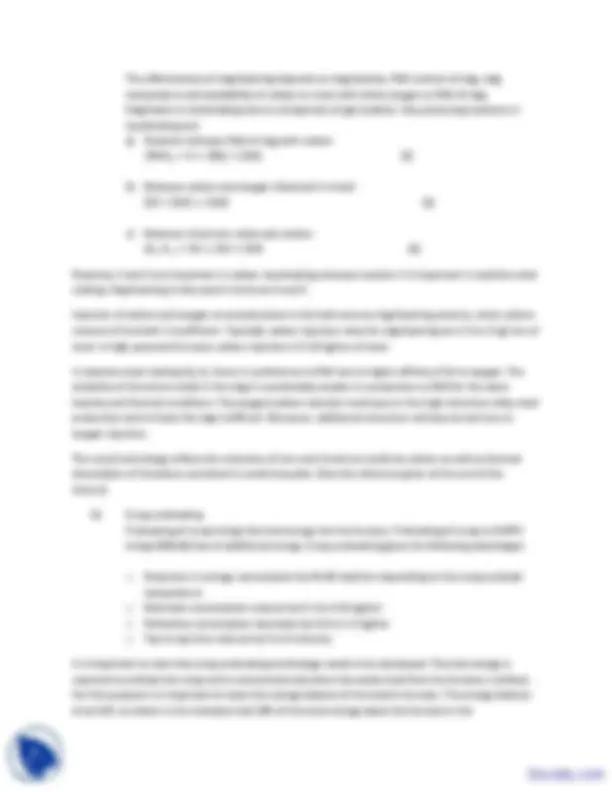
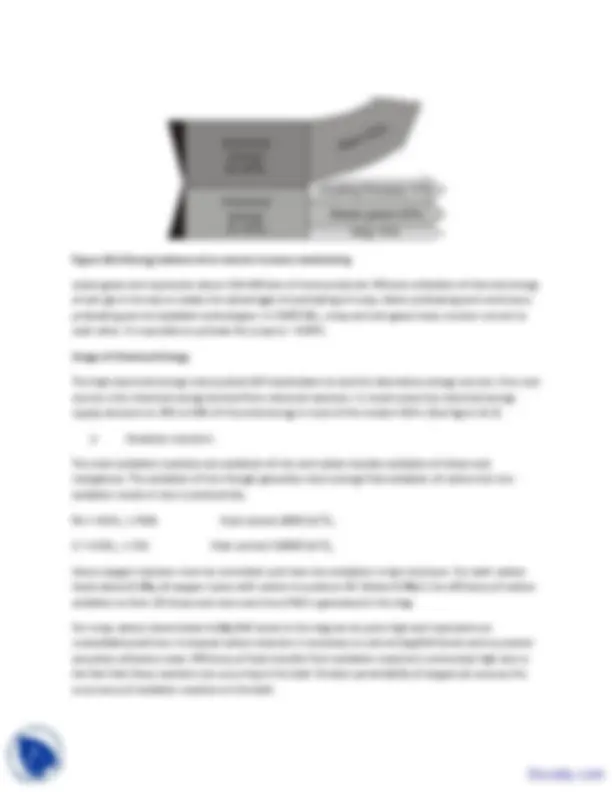
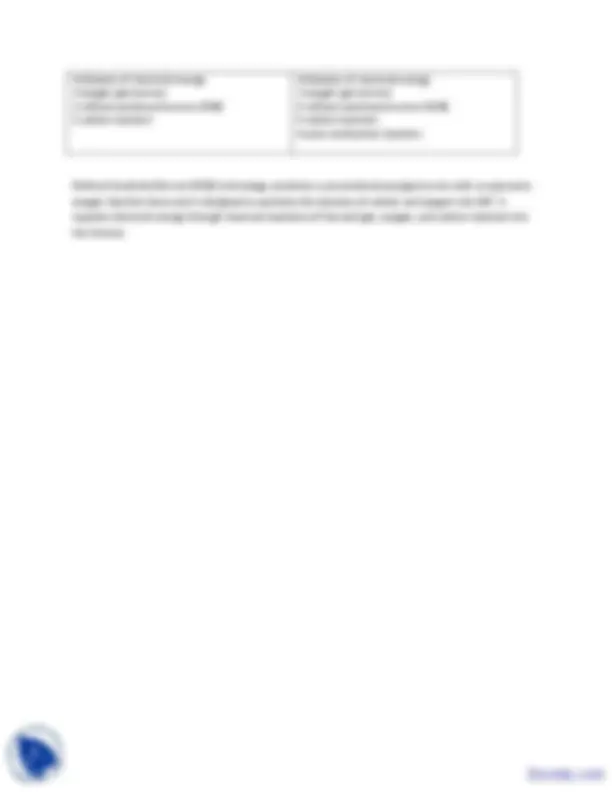
Study with the several resources on Docsity
Earn points by helping other students or get them with a premium plan
Prepare for your exams
Study with the several resources on Docsity
Earn points to download
Earn points by helping other students or get them with a premium plan
Community
Ask the community for help and clear up your study doubts
Discover the best universities in your country according to Docsity users
Free resources
Download our free guides on studying techniques, anxiety management strategies, and thesis advice from Docsity tutors
The major points which I found very informative are:Developments in Eaf Steelmaking, Furnace Design, Process Operating Technologies, Usage of Chemical Energy, Carbon Injection, Electric Steelmaking, Bottom Stirring, Scraps Preheating, Foamy Slag, Scrap Preheating
Typology: Study notes
1 / 8
This page cannot be seen from the preview
Don't miss anything!
Lecture 16 Developments in EAF steelmaking
Contents:
Introduction
Furnace design
Developments in EAF steelmaking
a) Furnace design
b) Process operating technologies
c) Usage of chemical energy
d) Carbon injection
Requirements for usage of chemical energy
Future of EAF steelmaking
Key words: Electric steelmaking, bottom stirring, scraps preheating, foamy slag, chemical energy
Introduction
The growth of electric steel production around the world has been driven by lower investment, higher
operational flexibility and easy adoptability to market demand on long or flat products of either plain
carbon or alloy steels. Growth has been supported by updating installations and technologies to reduce
the electric energy, electrode consumption and tap to tap time. Figure16. 1 shows the developments in
electric steelmaking technologies. Developments in EAF technologies are strongly supported by
secondary steelmaking. One can note in the figure that the power consumption has decreased from 630
Kwh/ton of steel to 290kWh/ton. Similarly tap tp tap time has decreased from 180 minutes to 40
minutes and electrode consumption has decreased from arounf 6.2 kg/ton to as low as 1.2 kg/ton within
the periods of representation in the figure. This became possible with the several simultaneous
developments in the secondary steel-making method. Table shows the various developments
Developments in EAF steelmaking
Furnace design Process operating technologies Chemical energy Charge materials
Split shell design
Transformer power
DC arc furnace
Bottom stirring
Foamy slag practice
Scrap preheating
Oxidation reaction
Post combustion
oxy fuel burner
Carbon injection
Directly reduced iron,
hot metal
Furnace design:
i) Construction of hearth and lower side section of the shell of larger diameter than the top
opening. This leads to increase in shell volume which results in larger tonnage charge, lower
heat losses and improved thermal efficiency.
ii) In the split shell design, shell structure is constructed in two sections: lower section which
contains hearth and free board allowance for slag, and upper section containing side wall
and roof. The two sections are coupled such that the upper section can be repaired easily.
This reduces the downtime and increases furnace availability.
iii) High powered transformers are the current trends. Most modern furnaces operate at
500 k VA⁄ ton and the trend is towards ultra high power ranging in between 700 k VA⁄ ton
to 1000 k VA⁄ ton. Developments are in progress to install transformer with 1500 k VA⁄ ton
capacity. It is claimed that a 120 tons operating at 180 MVA transformer capacity and by
using refining combined burner technology through oxygen gas and carbon injection, it is
possible to increase capacity by up to 50%. The largest transformer in AC EAF corresponds to
a rated power 0f 240 MVA for 300 ton furnace.
iv) Eccentric bottom taping reduces tap times, temperature losses and slag carry over into
ladle. The strip producing plants are equipped with eccentric bottom tapping in electric arc
furnaces.
v) DC (direct current) arc furnaces represent a different concept in arc furnace design. Most DC
furnaces are with single electrode where current flows down from the carbon electrode to
an anode mounted in the bottom of the furnace. Reduced electrode consumption of the
order of 50 to 60 % is the major benefit of a dc furnace compared to a convectional three-
phase arc furnace. Noise levels for the dc furnaces are lower. Lower maintenance costs are
claimed and refractory costs are less for sidewall but more for the furnace bottom. A dc arc
furnace requires an addition of the bottom electrode (anode), a dc reactor, and a thyristor
all of which add cost to a dc furnace. The electrode technology limits diameter to a
The effectiveness of slag foaming depends on slag basicity, FeO content of slag, slag
temperature and availability of carbon to react with either oxygen or FeO of slag.
Slag foams in steelmaking due to entrapment of gas bubbles. Gas producing reactions in
steelmaking are:
a) Reaction between FeO of slag with carbon
(FeO)
l
b) Between carbon and oxygen dissolved in metal
c) Between chromium oxide and carbon:
Cr
2
3
Reactions 1 and 2 are important in carbon steelmaking whereas reaction 3 is important in stainless steel
making. Slag foaming is discussed in lectures 4 and 5.
Injection of carbon and oxygen at several places in the bath assures slag foaming practice, when carbon
content of the bath is insufficient. Typically carbon injection rates for slag foaming are 2.5 to 5 kg/ ton of
steel. In high powered furnaces carbon injection is 5-10 kg/ton of steel.
In stainless steel making Cr 2
3
forms in preference to FeO due to higher affinity of Cr to oxygen. The
solubility of chromium oxide in the slag is considerably weaker in comparison to FeO for the same
basicity and thermal conditions. The oxygen/carbon injection technique in the high chromium alloy steel
production and to foam the slag is difficult. Moreover, additional chromium will also be lost due to
oxygen injection.
The novel technology utilizes the reduction of iron and chromium oxide by carbon as well as thermal
dissociation of limestone contained in small briquette. (See the reference given at the end of the
lecture)
iii) Scrap preheating
Preheating of scrap brings thermal energy into the furnace. Preheating of scrap to 540 ℃
brings 81 kwh/ton of additional energy. Scrap preheating gives the following advantages:
o Reduction in energy consumption by 40-60 kwh/ton depending on the scrap preheat
temperature
o Electrode consumption reduces by 0.3 to 0.36 kg/ton
o Refractory consumption decreases by 0.9 to 1 .4 kg/ton
o Tap to tap time reduces by 5 to 8 minutes.
It is important to note that scrap preheating technology needs to be developed. Thermal energy is
required to preheat the scrap and is economical only when the waste heat from the furnace is utilized.
For this purpose it is important to know the energy balance of the electric furnace. The energy balance
of an EAF, as shown in the indicates that 20% of the total energy leaves the furnace in the
Figure 16. 3 Energy balance of an electric furnace steelmaking
waste gases and represents about 130 kWh/ton of steel produced. Efficient utilization of thermal energy
of exit gas is the key to realize the advantages of preheating of scrap. Batch preheating and continuous
preheating are the available technologies. In CONSTEEL, scrap and exit gases move counter current to
each other. It is possible to preheat the scrap to ~ 320 ℃.
Usage of Chemical Energy
The high electrical energy costs pushed EAF steelmakers to look for alternative energy sources. One such
source is the chemical energy derived from chemical reactions. In recent years the chemical energy
supply amounts to 35% to 40% of the total energy in most of the modern EAFs. (See figure 16.3)
i) Oxidation reactions
The main oxidation reactions are oxidation of iron and carbon besides oxidation of silicon and
manganese. The oxidation of iron though generates more energy than oxidation of carbon but iron
oxidation results in loss in productivity.
Fe + 0. 5 O
2
= FeO; Heat content 6 kW/m
3
2
2
= CO; Heat content 3. 5 kW/m
3
2
Hence oxygen injection must be controlled such that iron oxidation is kept minimum. For bath carbon
levels above 0. 3 %, all oxygen reacts with carbon to produce CO. Below 0. 3 % C, the efficiency of carbon
oxidation to form CO drops and more and more FeO is generated in the slag.
For scrap carbon levels below 0. 1 %, FeO levels in the slag can be quite high and represents an
unavoidable yield loss. Increased carbon injection is necessary to control slag FeO levels and to prevent
excessive refractory wear. Efficiency of heat transfer from oxidation reactions is extremely high due to
the fact that these reactions are occurring in the bath. Greater penetrability of oxygen jet ensures the
occurrence of oxidation reactions in the bath.
Hold mode (to prevent plugging)
Burner mode (to heat and melt scrap)
Soft lancing mode (for post combustion)
Supersonic lancing mode (for decarburization and slag foaming)
Carbon injection mode (when slag foaming is required)
Injectors are either fixed type or moveable type. Submercible hand lances arc used through the slag
door. Large opening in EAF shell is required. Slag and metal splashing restricts the device movement.
Excessive repairs and down- time are associated with this technology.
An innovative design is CO-jet injectors which are fixed type and can be mounted on the furnace shell.
CO-jet injectors are highly flexible in usage. The reader may see the references given in this lecture.
The next lecture deals with charge mix in EAF steelmaking.
Future of EAF steelmaking
The EAF needs a metallurgical reactor that has the largest growth potential both in terms of production
capacity and technology evolution. Future EAF will be equipped with all modern technologies- like Ultra
high power input (up to 1500 kVA/t), latest oxygen and carbon injection technology and design
features- like ultra high shell design, heavy mill type components.
This combination leads to an Electric Arc Furnace where the tap to tap times can be extremely short and
the corresponding productivity reaches the level of larger furnace sizes or converter plants.
The two main reasons for this are:
the same size (tap weight) standard furnace.
It is interesting to compare a conventional 120ton EAF with the ultimate 120 ton EAF.
Conventional 120 ton EAF Ultimate 120 ton EAF
2 - bucket charge
Scrap bucket 130 m
3
Furnace volume 145 m
3
1 - bucket charge
Scrap bucket 185 m
3
Furnace volume 210 m
3
Transformer design upto 1,000kVA/t,
120MVA for 120 ton tapping weight,
Secondary voltage up to 1,200V
Transformer design upto 1,500kVA/t,
180MVA for 120 ton tapping weight,
Secondary voltage up to 1,500V
Utilization of chemical energy
3 oxygen gas burners
3 refined combined burners (RCB)
2 carbon injectors
Utilization of chemical energy
3 oxygen gas burners
5 refined combined burners (RCB)
4 carbon injectors
4 post combustion injectors
Refined Combined Burner (RCB) technology combines a conventional oxy/gas burner with a supersonic
oxygen injection lance and is designed to optimize the injection of carbon and oxygen into EAF. It
supplies chemical energy through chemical reactions of fuel and gas, oxygen, and carbon injected into
the furnace.