
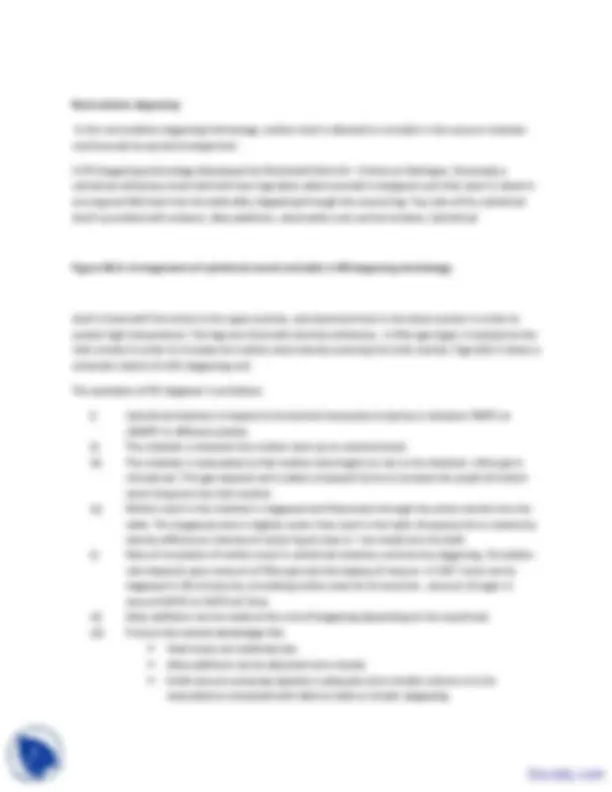
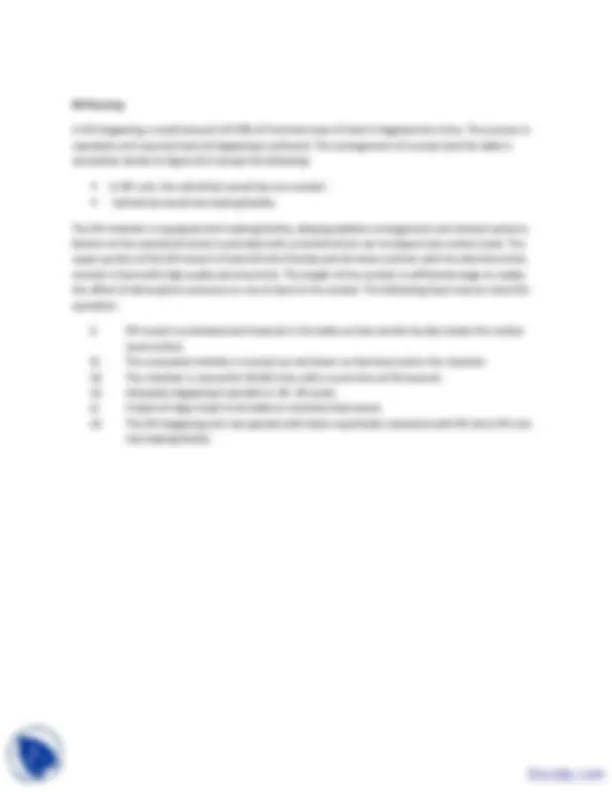
Study with the several resources on Docsity
Earn points by helping other students or get them with a premium plan
Prepare for your exams
Study with the several resources on Docsity
Earn points to download
Earn points by helping other students or get them with a premium plan
Community
Ask the community for help and clear up your study doubts
Discover the best universities in your country according to Docsity users
Free resources
Download our free guides on studying techniques, anxiety management strategies, and thesis advice from Docsity tutors
The major points which I found very informative are:Degassing Practice, Ladle Degassing, Stream Degassing, Recirculation Degassing, Circulation Degassing, Methods of Degassing, Arrangement of Ladle, Plug and Hopper for Degassing, Ladle to Mould Degassing
Typology: Study notes
1 / 4
This page cannot be seen from the preview
Don't miss anything!
Lecture 26 Degassing Practice Contents: Degassing processes Ladle degassing Stream degassing Recirculation degassing Key words: degassing, hydrogen and nitrogen in steel, ladle degassing, recirculation degassing Degassing processes There are 3 methods of degassing which are in practice i) Ladle degassing ii) Stream degassing iii) Circulation degassing All these processes are carried out in ladles. Ladle degassing Ladle containing molten steel is placed in a chamber which is then evacuated. After a determined time ladle is removed from the chamber and is teemed for casting. Figure 26.1 shows ladle degassing unit. Figure 26.1 Arrangement of ladle with porous plug and hopper for degassing Ladle is provided with a porous plug at its bottom to purge argon gas as shown in the figure. In a vacuum chamber the ladle is placed. The vacuum chamber is equipped with a hopper so as to make additions of elements as and when it is needed. For effective degassing of fully killed steel, it is necessary to purge argon through the bottom of the ladle. Stirring the bath enhances rate of gas removal. Vigorous removal of gases causes metal splashing too. Therefore ladle is not filled completely and about 25 % of its height is kept as freeboard to accommodate the splashed metal droplets. Pressure is maintained in between 1mmHg to 10mm Hg for effective degassing. During degassing additions are made for deoxidation and alloying. In certain cases ladle is heated to compensate for the loss of heat during degassing. For the effectiveness of degassing , it is necessary that carry-over slag either from BOF or EAF should be as low as possible. Carry-over slag contains FeO and since oxygen content of steel is in equilibrium with FeO content of slag, oxygen content of steel increases. Stirring gas is introduced either from top through the roof by a submerged refractory tube or through the porous plug fitted at the bottom of the ladle.
Electromagnetic stirring is employed for degassing. For this purpose ladle has to be made of non magnetic austenitic stainless steel or stainless window could be provided. For certain grades of alloy steels, both induction stirring and arc heating are employed for degassing. The final content of gas in steel depends on degree of vacuum and time of treatment. Hydrogen is generally reduced to below 2ppm from 4 to 6ppm, nitrogen content of steel is also reduced. The pick-up of nitrogen from the atmospheric air may occur during open pouring of steel, which must be controlled. Ladles are generally lined with high alumina bricks at upper part of the ladle while the lower portion is lined with fireclay. Stream degassing In stream degassing technology, molten steel is teemed into another vessel which is under vacuum. Sudden exposure of molten stream in vacuum leads to very rapid degassing due to increased surface area created by breakup of stream into droplets. The major amount of degassing occurs during the fall of molten stream. Height of the pouring stream is an important design parameter. Stream degassing technology has following variants in the practice i. Ladle to mould degassing Preheated mold with hot top is placed in vacuum chamber. Above the chamber a tundish is placed. Steel tapped in the ladle at superheat equivalent to 30 ℃ is placed above the tundish. Steel is bottom poured in the tundish. One ingot could weigh around as high as 400tons and several heats from different furnaces are used for casting. Figure 26.2 shows arrangement of vessels Figure 26.2: Arrangement of ladle, tundish and mold to degass molten steel ii. Ladle to ladle degassing In ladle to ladle degassing, a ladle with the stopper rod is placed in a vacuum chamber. Ladle containing molten steel from BOF or EAF is placed on top of the vacuum chamber and the gap is vacuum sealed. Alloy additions are made under vacuum. Stream is allowed to fall in the ladle where molten steel is degassed. Alloy additions are made under vacuum. In some plants degassing is done during tapping. In this arrangement molten steel from EAF is tapped into tundish or pony ladle. From the pony ladle molten stream is allowed to fall into a ladle which is evacuated. Ladle is closed from top with a special cover which contains exhaust opening. Steel with 25 ℃ to 30 ℃ superheat is tapped into ladle.
DH Gassing In DH degassing, a small amount 10-15% of the total mass of steel is degassed at a time. The process is repeated until required level of degassing is achieved. The arrangement of a vessel and the ladle is somewhat similar to figure 26.3 except the following: