
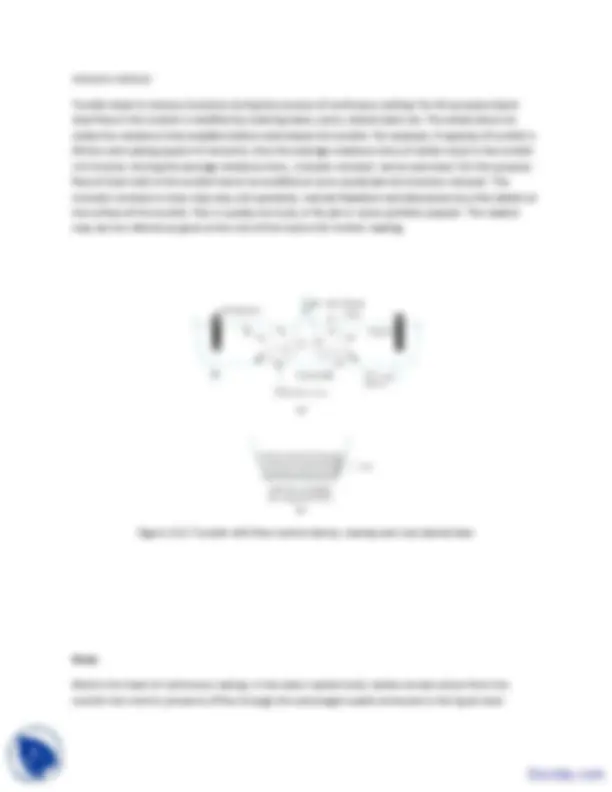
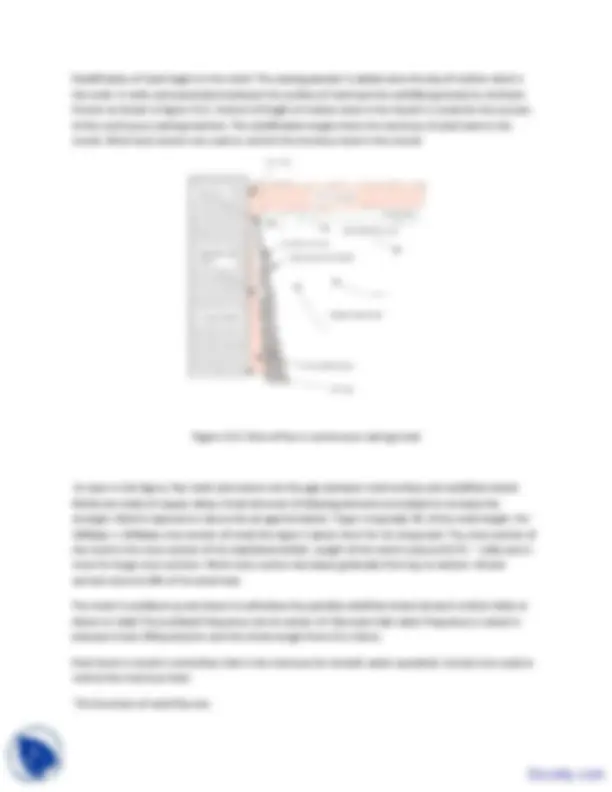
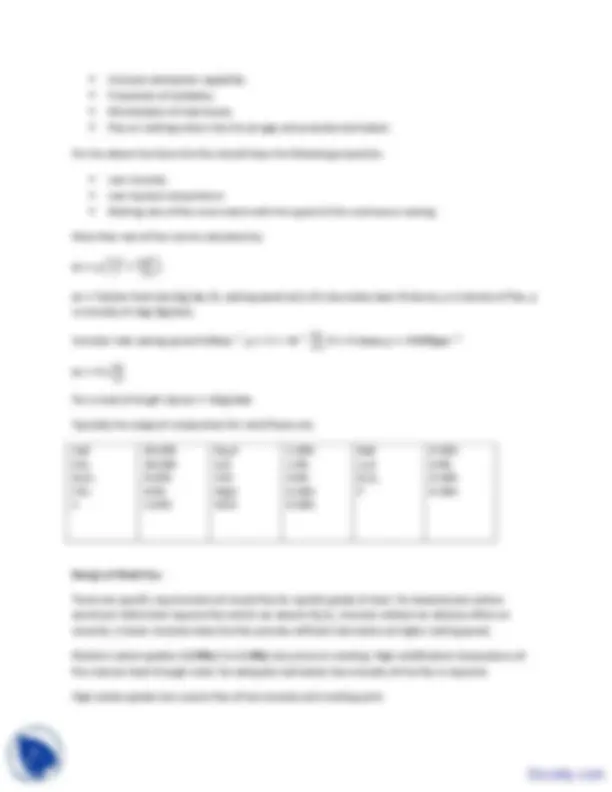
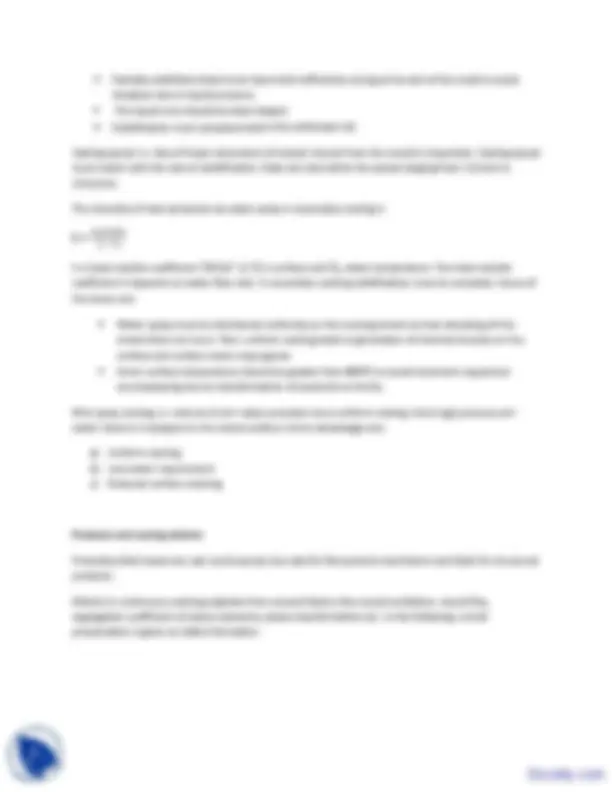
Study with the several resources on Docsity
Earn points by helping other students or get them with a premium plan
Prepare for your exams
Study with the several resources on Docsity
Earn points to download
Earn points by helping other students or get them with a premium plan
Community
Ask the community for help and clear up your study doubts
Discover the best universities in your country according to Docsity users
Free resources
Download our free guides on studying techniques, anxiety management strategies, and thesis advice from Docsity tutors
The major points which I found very informative are:Continuous Casting of Steel, Tundish Metallurgy,, Mold Secondary Cooling, Heat Transfer, Product and Casting Defect, Reservoir of Molten Steel, Inclusion Removal, Flow Control Device, Mold Level Sensors
Typology: Study notes
1 / 8
This page cannot be seen from the preview
Don't miss anything!
Lecture 33 continuous casting of steel
Content s Introduction How casting is done continuously Tundish Mold secondary cooling Heat transfer in continuous casting Product and casting defect
Keywords: continuous casting, tundish metallurgy, secondary cooling, defects in cast product
Introduction In the continuous casting, molten steel is poured from the tundish in the water cooled mold and partially solidified bloom/billet or slab (hereafter called strand) is withdrawn from the bottom of the mold into water spray so that solidified bloom/billet or slab is produced constantly and continuously. Continuous casting is widely adopted by steelmakers. The advantages of continuous casting over ingot casting are
How casting is done continuously?
The essential components of a continuous casting machine are tundish, water cooled mold, water spray and torch cutters. Tundish, mold and water spray are arranged such that molten stream is poured from tundish to mold and solidified strand (billet/bloom/billet) is produced continuously. The required length of the strand is cut by torch cutter. In figure 32.1, the arrangement of tundish, mold and water spray is shown.
Figure 33.1 Arrangement of tundish, mold and water spray in a curved mold machine (paste figure 2.3a)
Tundish
Tundish is a refractory lined vessel. Liquid steel is usually tapped from ladle into tundish. The stream is shrouded as it enters from ladle to tundish. The functions of the tundish are:
Reservoir of molten steel
Tundish acts as a reservoir for molten steel. It supplies molten steel in presence of a slag cover to all continuous casting molds constantly and continuously at constant steel flow rate. The flow rate is maintained constant by maintaining a constant steel bath height in the tundish through teeming of molten steel from the ladle. The number of mold is either one or more than one. Normally bloom and billet casting machines are multi‐strand i.e. number of molds are either 4 or 6 or 8. Slab casters usually have either single or two molds. During sequence casting and ladle change‐ over periods, tundish supplies molten steel to the molds.
Distributor
Tundish distributes molten steel to different molds of the continuous casting machine at constant flow rant and superheat which is required for stand similarly with reference to solidification microstructure. Control of superheat is required in all the moulds to reduce break‐out. Location of ladles stream in the tundish is important. It may be located symmetric or asymmetric to the centre of the tundish depending on the number of mold. For single strand machines, molten stream enters from one side and exits the other side of the tundish. In multi‐strand tundishes, ladle stream is either at the centre of the tundish or displaced to the width side of the tundish.
Solidification of steel begins in the mold. The casting powder is added onto the top of molten steel in the mold. It melts and penetrates between the surface of mold and the solidifying strand to minimize friction as shown in figure 33.2. Control of height of molten steel in the mould is crucial for the success of the continuous casting machine. The solidification begins from the meniscus of steel level in the mould. Mold level sensors are used to control the meniscus level in the mould.
Figure 33.2: Role of flux in continuous casting mold
As seen in the figure, flux melts and enters into the gap between mold surface and solidified strand. Molds are made of copper alloys. Small amounts of alloying elements are added to increase the strength. Mold is tapered to reduce the air gap formation. Taper is typically 1% of the mold length. For cross section of mold the taper is about 1mm for 1m long mold. The cross section of the mold is the cross section of the slab/bloom/billet. Length of the mold is around 0.7 and is more for large cross sections. Mold cross section decreases gradually from top to bottom. Mould extracts around 10% of the total heat.
100mm ൈ 100mm 5 െ 1.4m
The mold is oscillated up and down to withdraw the partially solidified strand (strand is either billet or bloom or slab).The oscillated frequency can be varied. At Tata steel slab caster frequency is varied in between 0 and 250cycles/min and the stroke length from 0 to 12mm.
Steel level in mould is controlled, that is the meniscus for smooth caster operation. Sensors are used to control the meniscus level.
The functions of mold flux are.
For the above functions the flux should have the following properties.
Mass flow rate of flux can be calculated by
mሶ ൌ ρ ቀUଶ^ ౩^ ஔ ஔ^
య ଵଶஜ ቁ
mሶ ൌ /sm, U (^) ୱ δ g/msሻ
msି ଵ^ , μ ൌ 3 ൈ 10ି ଵ^ ୫ୱ୩
Powder feed rate kg casting speed m/s, is boundary layer thickness, ρ is density of flux, μ is viscosity of slag ሺk.
Consider slab casting speed 0.05 , δ ൌ 0.1mm, ρ ൌ 3000kgmିଷ
mሶ ൌ 0.1 (^) ୱ୫୩
For a mold of length 1m, mሶ ൌ 6 kg/min
Typically the range of composition for mold fluxes are.
CaO 25 ‐45% Na 2 O 1 ‐20% BaO 0 ‐10% SiO (^2) Al 2 O 3 TiO (^2) C
FeO MgO MnO
Li 2 O B 2 O 3 F
Design of Mold flux
There are specific requirements of mould flux for specific grade of steel. For example,low carbon
cient
Medium carbon grades ሺ0.08% C to 0.18%ሻ are prone to cracking. High solidification temperature of h mold. For adequa
aluminum killed steel requires flux which can absorb Alଶ O (^) ଷ inclusion without an adverse effect on viscosity. A lower viscosity helps the flux provide suffi lubrication at higher casting speed.
flux reduces heat throug te lubrication low viscosity of the flux is required.
High carbon grades too require flux of low viscosity and melting point.
In secondary cooling, number of nozzles is distributed over the surface of the moving strand. Overlapping of spray may occur. Distance between nozzles is important.
Heat transfer in continuous casting takes place in mold and in secondary cooling by a combination of
. Figure 33.3 shows heat transfer in the mold and secondary cooling.
Figure 33.3: Heat transfer in the mold and secondary cooling zone and the formation of solid shell. Mushy zone and liquid core can also be seen
In the mold air gap formation influences heat transfer. The higher heat flux in mould can lead to higher asting speeds. Heat flux depends on.
or curve
oling
Heat transfer in continuous casting
conduction, convection and radiation
c
The major requirements for secondary co
re the withdrawl roll.
m the mould is important. Casting speed must match with the rate of solidification. Slabs are cast within the speed ranging from 1.5/min to
y of heat extraction by water spray in secondary cooling is
T౩ି T (^) ౭
Casting speed i.e. rate of linear movement of strand/ minute fro
2.5m/min.
The intensit
h ൌ ୦ୣୟ୲ f୪୳୶
h is heat tra coefficient ሺW m⁄^ ଶ^. sሻ, Tୱ is surface and T୵ water temperature. The heat transfer coefficient h depends on water flow rate. In secondary cooling solidification must be complete. Some of
r spray must be distributed uniformly on the moving strand so that reheating of the strand does not occur. Non‐ uniform cooling leads to generation of thermal stresses on the
tion of austenite to ferrite.
Mist ling. Here high pressure air+ water mixture is sprayed on the metal surfaces. Some advantages are:
b) Less water requirement cracking
roducts and casting defects
continuously into slab for flat products and bloom and billet for structural
continuous casting originate from several factors like mould oscillation, mould flux, segregation coefficient of solute elements; phase transformation etc. In the following, a brief
nsfer
the issues are:
surface and surface cracks may appear.
spray cooling i.e. mixture of air+ water provides more uniform coo
a) Uniform cooling
c) Reduced surface
Presently killed steels are cast products.
Defects in
presentation is given on defect formation.