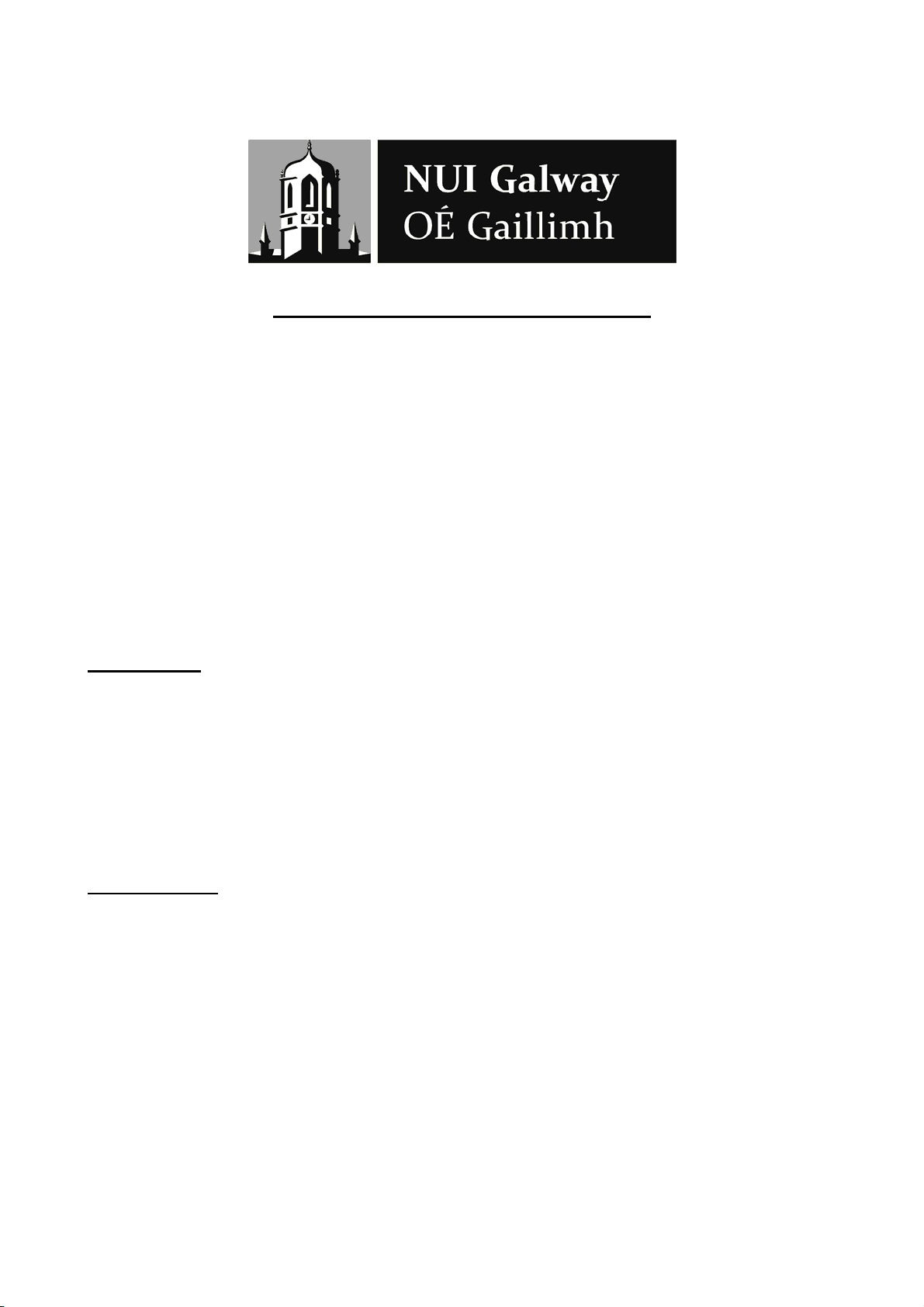
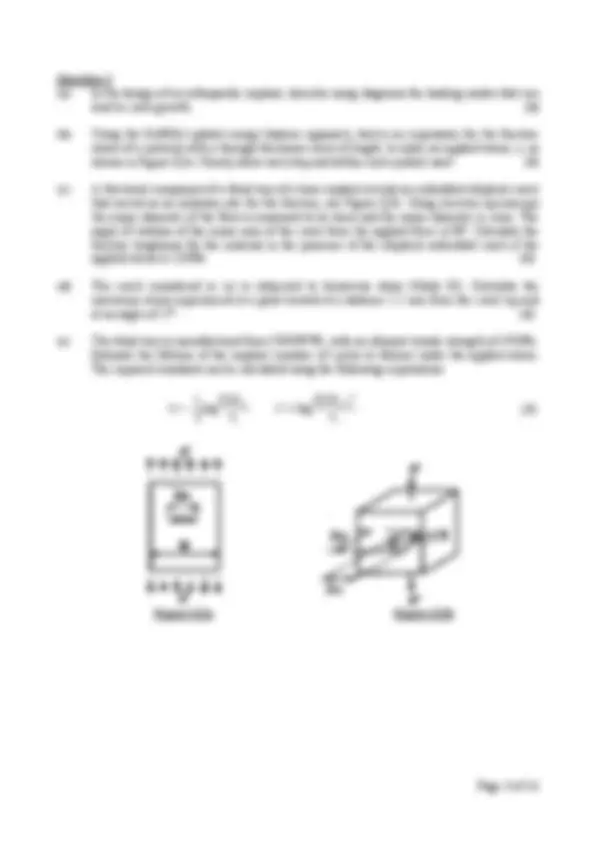
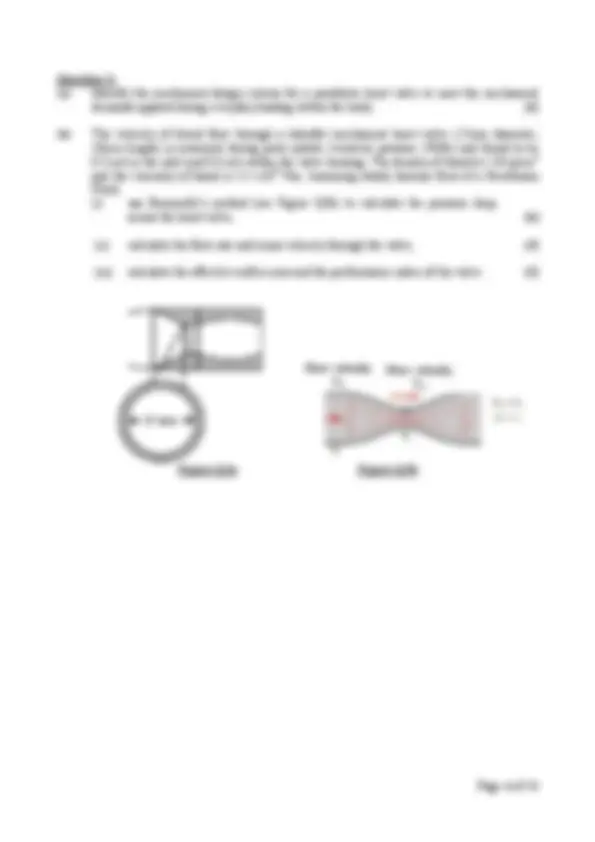
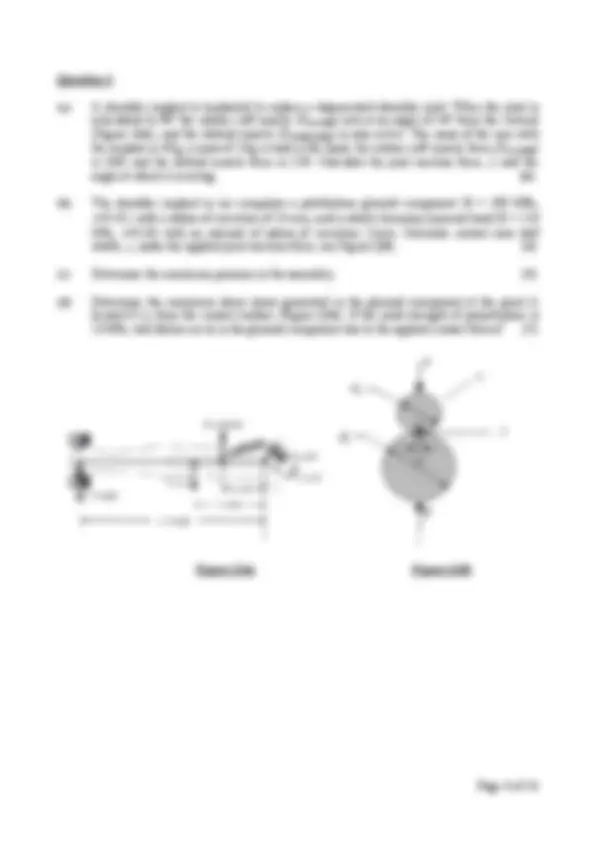
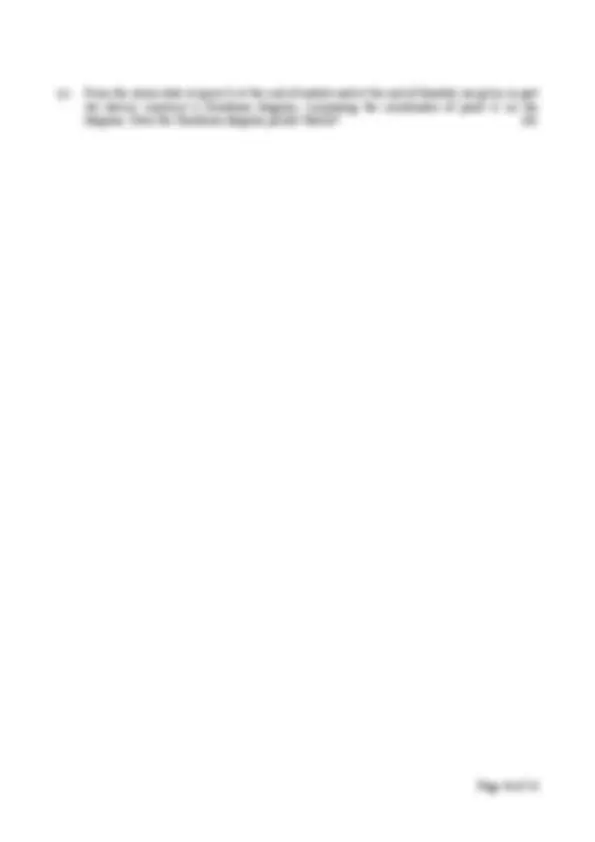
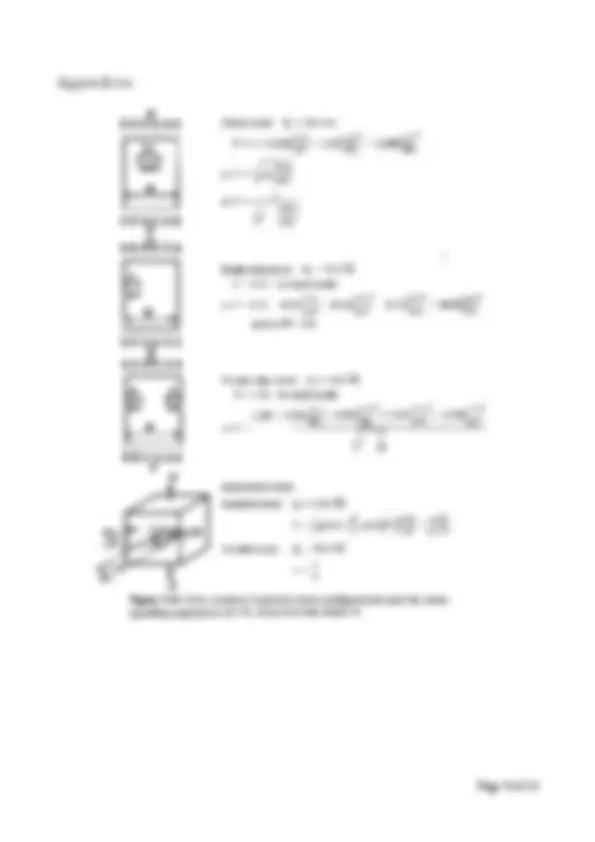
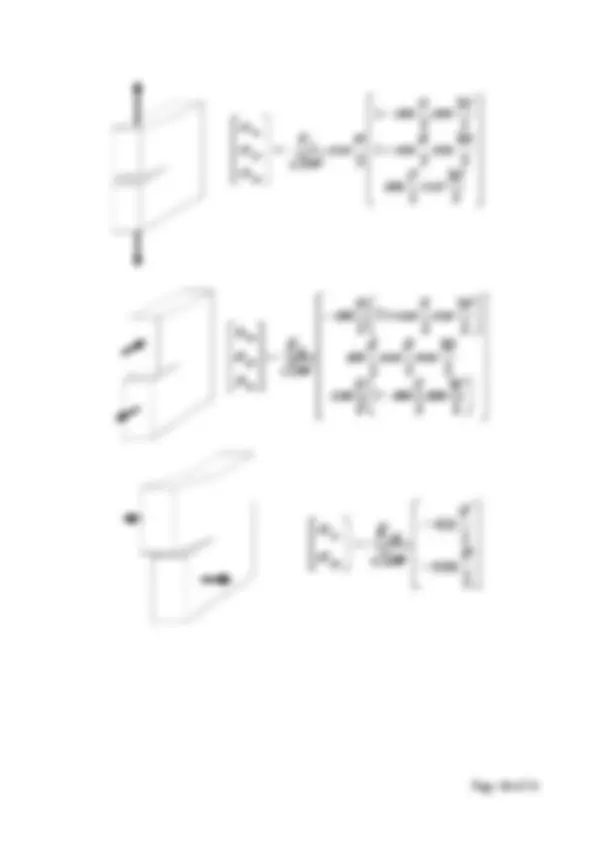
Study with the several resources on Docsity
Earn points by helping other students or get them with a premium plan
Prepare for your exams
Study with the several resources on Docsity
Earn points to download
Earn points by helping other students or get them with a premium plan
Community
Ask the community for help and clear up your study doubts
Discover the best universities in your country according to Docsity users
Free resources
Download our free guides on studying techniques, anxiety management strategies, and thesis advice from Docsity tutors
Main points of this past exam paper are: Balloon Design, Medical Industry, Main Design Features, Balloon, Specific Function, Expression, Circumferential Hoop Strain, Compared, Balloon Burst Strength Test, Balloon Catheter Designs
Typology: Exams
1 / 11
This page cannot be seen from the preview
Don't miss anything!
Exam Code(s) 4BG Exam(s) 4 th^ Biomedical Engineering
Module Code(s) ME Module(s) Medical Implant and Device Design
Paper No. 1 Repeat Paper
External Examiner(s) Professor David Taylor Internal Examiner(s) Professor Peter McHugh Dr. Laoise McNamara Dr. Patrick McGarry
Instructions: (^) This paper contains 6 questions Answer 5 questions All questions will be marked equally Use a separate answer book for each Section
No. of Pages 11 Department(s) Mechanical & Biomedical Engineering Course Co-ordinator(s) Dr. Laoise McNamara
Requirements: Statistical/ Log Tables
Release to Library: Yes
Question 1
(a) Identify the two types of balloon design used in the medical industry. In your answer outline the specific function of the balloon and the main design features of the balloon that provide that function. [4]
(b) Derive an expression for the circumferential hoop strain in a thin walled balloon under the internal pressure due to inflation (Figure Q1a). [5]
(c) Two balloon catheter designs are compared using a Balloon Burst Strength test. The initial diameter of Balloon 1 was 6.9mm and the diameter of Balloon 2 was 3.0mm. Each balloon was filled with water and the internal pressure was increased to the maximum recommended pressure (MRP). At full inflation the internal diameter of the balloon was recorded, see Figure Q1a.
(i) Using the expression derived in (b) , determine the wall thickness of each balloon at the yield point. Balloon 1 is manufactured from Polyethylene Terephthalate PET (E= 2.7 GPa, σy = 55 MPa, ν = 0.43) and Balloon 2 is manufactured from Nylon (E= 4 GPa, σy = 75 MPa, ν = 0.4). [5]
(ii) Calculate the burst pressure of each balloon if a safety factor of 2 is assumed. [4]
(iii) Identify which balloon design is most suitable for balloon angioplasty applications and justify your choice of design. [2]
Figure Q1(a) Figure Q1(b)
Question 3: (a) Identify the mechanical design criteria for a prosthetic heart valve to meet the mechanical demands applied during everyday loading within the body. [4]
(b) The velocity of blood flow through a bileaflet mechanical heart valve (27mm diameter, 10mm length) is measured during peak systole (ventricle pressure 19kPa) and found to be 0.3 m/s in the inlet and 0.6 m/s within the valve housing. The density of blood is 1.04 g/cm^3 and the viscosity of blood is 3.2 x10-3^ Pas. Assuming steady laminar flow of a Newtonian Fluid, (i) use Bernouilli’s method (see Figure Q3b) to calculate the pressure drop across the heart valve, [6]
(ii) calculate the flow rate and mean velocity through the valve, [5]
(iii) calculate the effective orifice area and the performance index of the valve. [5]
Figure Q3a Figure Q3b
Flow velocity V 2
Flow velocity V 1
Question 4
(a) A shoulder implant is implanted to replace a degenerated shoulder joint. When the joint is articulated to 90º the rotator cuff muscle (FU-CUFF ) acts at an angle of 44º from the vertical (Figure Q4a), and the deltoid muscle (FU-DELTOID ) is also active. The mass of the arm with the implant is 3Kg, a mass of 1Kg is held in the hand, the rotator cuff muscle force (FU-CUFF ) is 34N, and the deltoid muscle force is 22N. Calculate the joint reaction force, J, and the angle at which it is acting. [6]
(b) The shoulder implant in (a) comprises a polethylene glenoid component (E = 180 MPa, =0.45), with a radius of curvature of 24 mm, and a cobalt chromium humeral head (E = 110 GPa, =0.33) with an internal of radius of curvature 22mm. Calculate contact area half width, a , under the applied joint reaction force, see Figure Q4b. [4]
(c) Determine the maximum pressure in the assembly. [3]
(d) Determine the maximum shear stress generated in the glenoid component at the point A located 0.2 a from the contact surface (Figure Q4b). If the yield strength of polyethylene is 21MPa, will failure occur in the glenoid component due to the applied contact forces? [7]
Figure Q4a Figure Q4b
Question 6
Figure Q
(a) Figure Q6 shows an NIR 316L stainless steel stent unit cell following balloon deployment to a diameter of 2mm. The recommended deployment diameter is 3mm. The yield stress of 316L stainless steel is 240MPa. The stress components at point A are as follows:
xx =-200MPa yy= 0MPa xy=70MPa
(i) Using the Tresca yield criterion determine if plastic deformation occurs at point A. [4]
(ii) Using the vonMises yield criterion determine if plastic deformation occurs at point A. [4]
(iiii) Provide a rough sketch of the Tresca and vonMises yield surfaces, indicating a possible location for point A. Which yield criterion should be used for stent design? Comment on the results of (i) and (ii) in relation to stent deployment. [4]
(b) (i) Integrate the Paris Law to derive an expression for the number of cycles to failure under fatigue loading. [1]
(ii) At the end of the systole the stress state at point A (Figure Q6) is
xx =-350MPa yy= 10MPa xy=80MPa
At the end of diastole the stress at the same point is xx =-300MPa yy= 0MPa xy=0MPa
If the stent contains a crack of length 0.5m at point A determine the number of cardiac cycles before the crack grows to a length of 50m. For 316L stainless steel the Paris Law constants are given as m =3.4 and C =1.2x10-13^ when units of m and MPa are used for crack length and stress, respectively. [3]
(c) From the stress state at point A at the end of systole and at the end of diastole (as given in part (b) above) construct a Goodman diagram, computing the coordinates of point A on the diagram. Does the Goodman diagram predict failure? [4]
Table 1: Area and stress relationships for contact between elastic bodies
3
1 2
2
2 2 1
2 1
d d
a
2
2
1 max 21
1 tan
a
a za z
z x y p
1 2
2
2 2 1
2 1
d d
l
b
b
z b
z x p 2
2
b
z b
z
b
z y p^12 1
2
2
max (^2)
2
2
max
1 b
z
p