
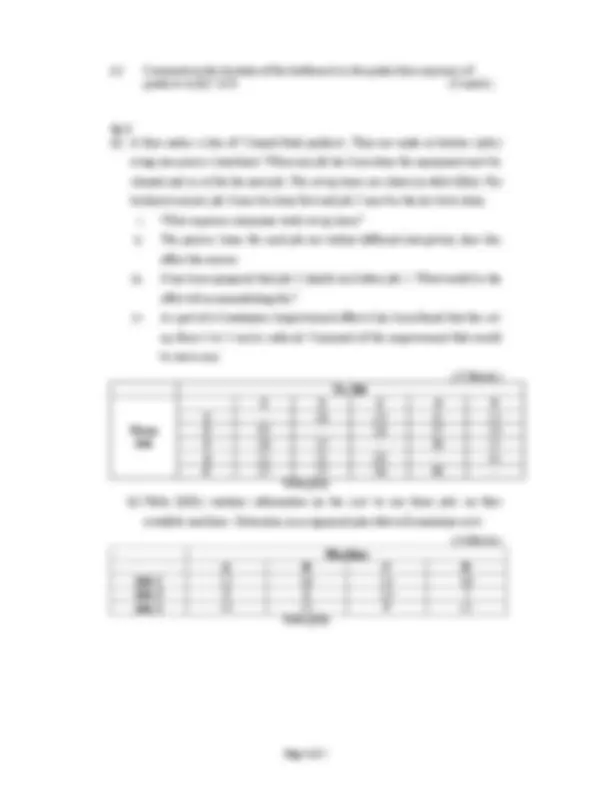
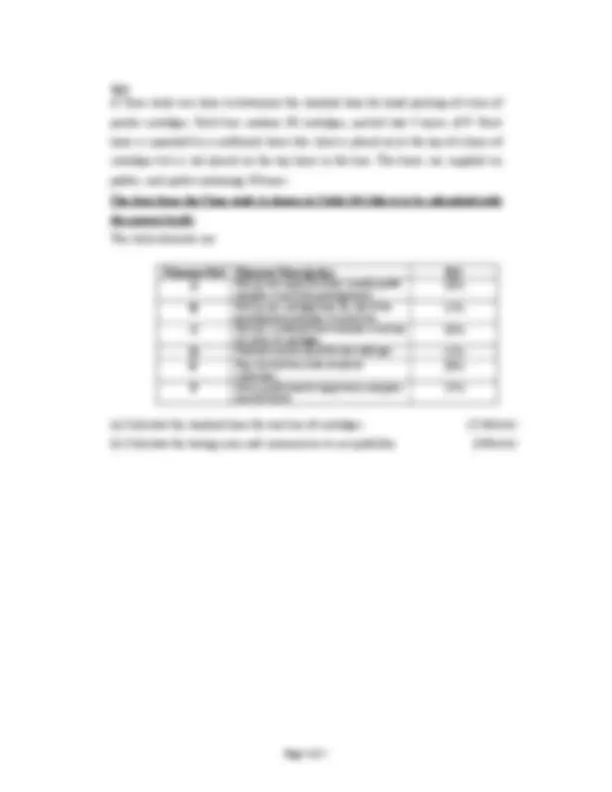
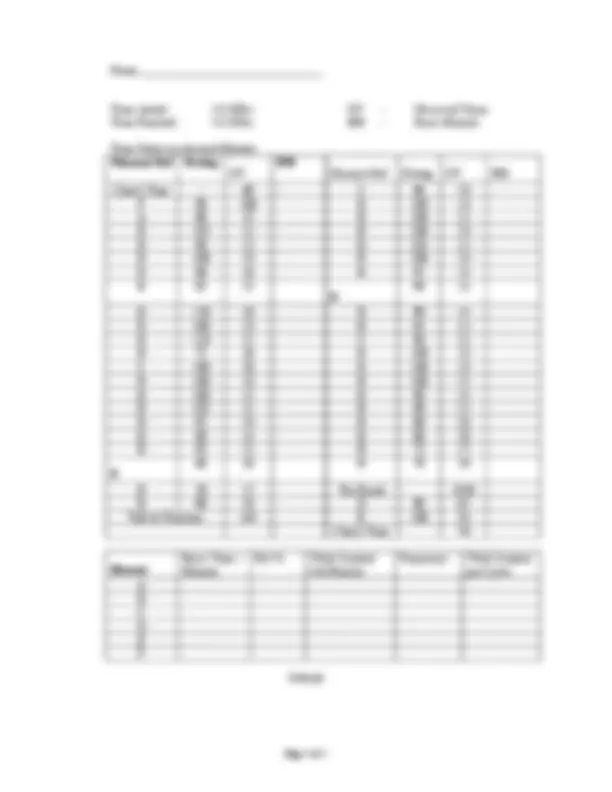
Study with the several resources on Docsity
Earn points by helping other students or get them with a premium plan
Prepare for your exams
Study with the several resources on Docsity
Earn points to download
Earn points by helping other students or get them with a premium plan
Community
Ask the community for help and clear up your study doubts
Discover the best universities in your country according to Docsity users
Free resources
Download our free guides on studying techniques, anxiety management strategies, and thesis advice from Docsity tutors
Main points of this past exam are: Balance Loss, Particular Model, Indicates, Relationship, Forecasts, Required Per Year, Positional Weight Method, Rank Positional, Precedence, Production
Typology: Exams
1 / 5
This page cannot be seen from the preview
Don't miss anything!
Semester 1 Examinations 2008/
Module Code: MANU 8004
School: Mechanical & Process Engineering
Programme Title: Bachelor of Engineering (Hons) in Biomedical Engineering Bachelor of Science (Hons) in Process Plant Technology Bachelor of Engineering (Hons) in Mechanical Engineering
Programme Code: EBIOM_8_Y3, EBIOM_8_Y4, EPPTE_8_Y4, EMECH_8_Y3, EMECH_8_Y
External Examiner(s): Mr. Murtagh Murphy, Dr. David Fitzpatrick Mr. Neil Kingston, Mr. Joe Phelan Mr. Peter Clarke and Prof. Robin Clarke
Internal Examiner(s): Ms. Sally Bryan
Instructions: Answer THREE questions
Duration: 2 Hours
Sitting: Winter 2008
Requirements
Note to Candidates: Please check the Programme Title and the Module Title to ensure that you are attempting the correct examination. If in doubt please contact an Invigilator.
The Precedence diagram in Figure Q1 indicates the relationship between work
elements for the production of a particular model of a toy car. Forecasts of likely
demand indicate that at least 120,000 units will be required per year. Assume 2000
working hour per year.
(a). Using the Rank Positional Weight method, obtain a suitable allocation of work
elements to work stations in the assembly line. (20 Marks)
(b). Calculate the balance delay and balance loss (4 Marks)
(c). By considering a re-distribution of work elements, show how an improvement on
the solution obtained in (a) above can be realized. (9 Marks)
Figure Q
(a). Compare synchronous manufacturing to the JIT approach (12 Marks)
(b). Four Products A, B, C and D are processed on three work centres in sequence
WC1, WC2 and WC3. Processing times, material costs and selling prices are shown in Table Q2. The plant operates 52.5 hours per week with costs of €
per week, excluding materials. The market will purchase any quantity that the plant can produce , provided that all four products are sold and the weekly output
of any one product does not exceed any other by a factor of more than five. Compare the net profit of the plant using:
i. Traditional maximizing per unit profit ii. Maximum utilization of bottleneck resource (OPT approach) (18 Marks)
Processing Times (min) Product Selling Price €
Material Costs €
Table Q
A Time study was done to determine the standard time for hand packing of a box of
printer cartridges. Each box contains 36 cartridges, packed into 4 layers of 9. Each
layer is separated by a cardboard sheet; this sheet is placed on to the top of a layer of
cartridges but is not placed on the top layer in the box. The boxes are supplied on
pallets, each pallet containing 50 boxes.
The data from the Time study is shown in Table Q4 (this is to be submitted with
the answer book)
The study elements are:
Element Ref Element Description RA A Pick up one empty box from a nearby pallet and place it on to the packing bench
B Pick up one cartridge from the side of the packing bench and place it in the box
C Pick up a cardboard sheet and place it on top of a layer of cartridges
D Fold and seal the top of the box with tape^ 12% E Place the full box aside (ready for collection)
F Fetch a pallet load of empty boxes and place near the bench
(a) Calculate the standard time for one box of cartridges (25 Marks)
(b) Calculate the timing error and comment on its acceptability (8 Marks)
Name:________________________________
Time started: 13:10Hrs OT - Observed Times Time Finished: 13:32Hrs BM - Basic Minutes
Time Shown in decimal Minutes Element Ref Rating OT
Element Ref Rating OT BM Check Time - 60 - C 80 23 F 90 180 B 100 13 A 80 45 B 100 12 B 105 12 B 100 13 B 90 15 B 105 12 B 100 13 B 100 13 B 80 16 B 95 14 B 85 15 B
B
B 70 17 Tea Break 1020 B 80 16 D 80 65 Talk to Foreman 165 E 100 34 Check Time 70
Element
Basic Time – Minutes
RA % Work Content Std Minutes
Frequency Work Content per Cycle A B C D E F
Table Q