
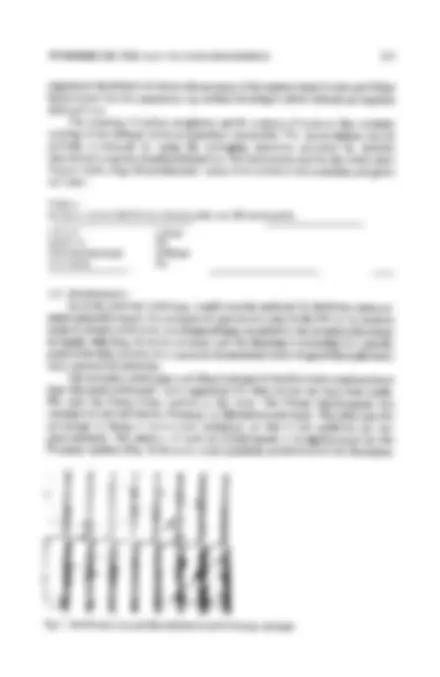
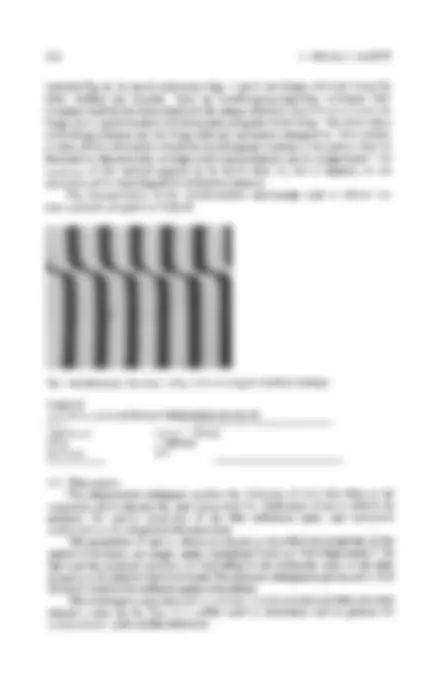
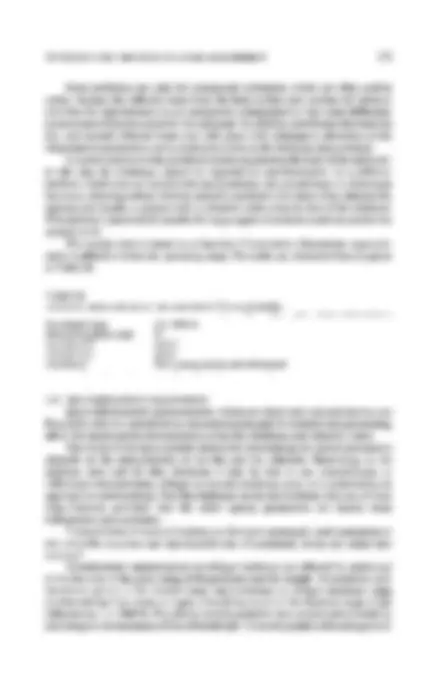
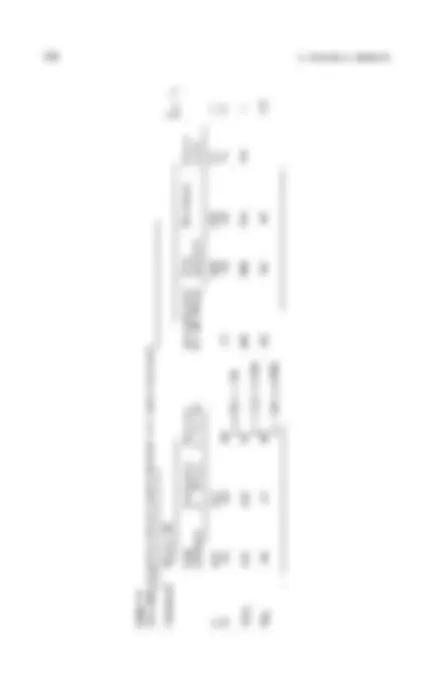
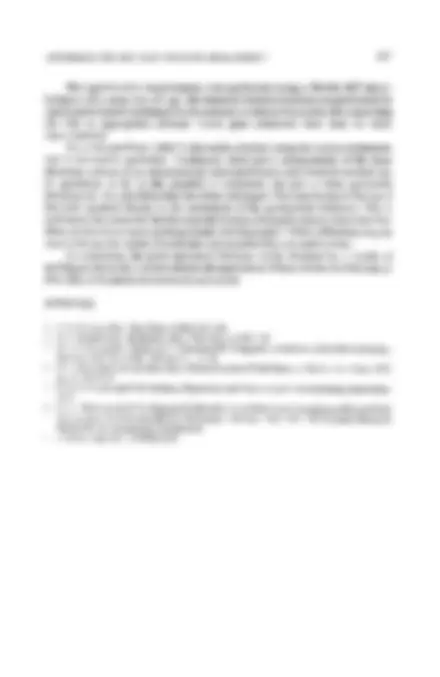
Study with the several resources on Docsity
Earn points by helping other students or get them with a premium plan
Prepare for your exams
Study with the several resources on Docsity
Earn points to download
Earn points by helping other students or get them with a premium plan
Community
Ask the community for help and clear up your study doubts
Discover the best universities in your country according to Docsity users
Free resources
Download our free guides on studying techniques, anxiety management strategies, and thesis advice from Docsity tutors
This document compares various techniques for measuring the thickness of thin films, including stylus profilometry, interferometry, ellipsometry, spectrophotometric measurements, and x-ray microanalysis. The authors discuss the advantages, disadvantages, and appropriate sample preparation for each technique. The document also provides practical suggestions for obtaining accurate thickness measurements.
Typology: Lecture notes
1 / 9
This page cannot be seen from the preview
Don't miss anything!
Thm Sohd Fdms, 124 (1985) 249- PREPARATION AND CHARACTERIZATION 249
A. PIEGARI AND E. MASETTI Laboratorto Ftlm Sottlh, Comttato Naztonale per la rwerca e per 1o svduppo dell'Energla Nucleare e delle Energte Alternatwe. Vta Angutllarese Km 1 300, 00060 Rome (Italy) (Recewed August 6, 1984, accepted October 11, 1984)
The relative merits of some techniques for measuring the thickness of thin films are discussed. The techniques chosen for this comparison are widely used in thin film characterization and are as follows: stylus profilometry, interferometry, ellipsom- etry, spectrophotometric measurements and X-ray microanalysis. The comparison is performed for areas where more than one technique can be used. Suggestions are made regarding appropriate sample preparation and instrument operation to ensure that the best results are obtained for each technique.
Owing to the important role that film thickness plays in optical coatings its measurement is of great interest, and the appropriate techniques to be used depending on the film properties are under continuous investigation. If a film with a well-defined thickness is required the preferred measurement technique is obviously one which allows the thickness to be controlled during deposition. A few methods for monitoring the film thickness during the coating process are available, but in most cases the measurements are performed after the coating process is complete. In this paper we analyse the latter class of methods which can also be used for control purposes. A detailed description of a wide range of methods can be found in general reviews t-4 in which the advantages, disadvantages, measurement range and accuracy are given for each technique. Therefore we shall not describe the physical bases of the various techniques here. However, it is of interest to describe a set of measurements carried out on the same samples using several techniques and to make some practical suggestions aimed at ensuring that the thickness measurements are performed correctly. The measurement techniques used in this work are as follows: (1) stylus profilometry; (2) interferometry; (3) ellipsometry; (4) spectro- photometry; (5) X-ray microanalysis. Microgravimetry and chemical analysis were also used as additional methods of control.
0040-6090/85/$3 30 © Elsevier Sequoia/Printed m The Netherlands
The samples were prepared by depositing films onto commercially available glass or quartz substrates. The materials and the thickness range were chosen to be characteristic of optical coatings and to allow each sample to be tested by as many techniques as possible. The metallic films were deposited by thermal evaporation and the dielectric films were deposited by r.f. sputtering.
This mechanical method requires the presence of a groove or a step between the substrate surface and the film surface such that the stylus is vertically displaced as it traverses the sample. Such grooves or steps can be produced by masking portions of the substrate during deposition or by removing parts of the film after deposition. The latter method presents some difficulties in the case of dielectric films on dielectric substrates owing to the need for suitably selective chemical etchants. Masking requires that the mask is in close contact with the substrate and is very thin in order to avoid shadowing and accumulation of material near the step edge. Therefore a painting technique is more suitable than the use of solid objects such as cover glasses or bars. In our samples the step was obtained by depositing a spot of paint made by dissolving TiO2 powder in isopropanol on the substrate before commencing the coating process. After deposition the paint was easily removed by simply rinsing the sample in deionized water. In this way we were able to obtain a step with a sharp edge as can be in Fig. 1 which is a copy of a stripchart from our instrument. A step obtained using a cover glass is shown for comparison in Fig. 2; it can be seen that the
o. o o j s o. 4 0. 2 o. o (^) | | m i i f I P " " o l o o Z O O 3 0 o 4 0 0 Fig 1. Fdm edge obtained using the painting techmque
-1, -!.6 i l , I00 200 3_ F]g 2. Film edge obtained using a cover glass
4 0 0
method (Fig. 4). As can be seen from Figs. 3 and 4, the fringes obtained using the latter method are broader. Thus an interferogram-digitizing technique with computer analysis has been employed. By using a threshold discriminator circuit the fringe centre can be located at several points along the whole fringe. The mean values of the fringe distance and the fringe shift are calculated subsequently. This method enables all the information which the interferogram contains to be used so that the fluctuations characteristic of single-point measurements can be compensated. The accuracy of this method appears to be better than 1~o but it depends on the resolution of the digitizing device (television camera). The characteristics of the lnterferometnc microscope used to obtain our measurements are given in Table II.
Fig 4 Interferogram of the sample m Fig. 3 obtained using the Mlchelson techmque
TABLE II LEITZ METALLOPLAN/ORTHOPLAN INTERFEROMETRIC MICROSCOPE Light source Na 10 (2 = 589 nm) Range 3-30000 n m Resolutton 30
The ellipsometric technique enables the thickness of very thin films to be measured, and it can also be used successfully for thicknesses of up to 1000/~. In addition, the optical properties of the film (refractive index and extinction coefficient) can be obtained at the same time. The parameters ~u and A, which are related to the reflection properties of the sample to be tested, are sought using a technique known as "null ellipsometry ''s. In this case the polarizer position corresponding to the minimum value of the light intensity at the detector has to be found. The data are subsequently processed to find identical solutions for different angles of incidence. This technique is non-destructive, does not involve contact and does not even require a step on the film; it is widely used in electronics and in general for semiconductor and metallic substrates.
Some problems can arise for transparent substrates, which are often used in optics, because the reflected beam from the back surface also reaches the detector and thus the light intensity is not completely extinguished so that some difficulties are encountered in the search for the null point. In addition, interference between the first and second reflected beam may take place with subsequent alteration of the ellipsometric parameters and a consequent error in the thickness measurement. A typical solution to this problem consists in grinding the back of the substrate; in this case the technique cannot be regarded as non-destructive. In a different method, which does not involve this inconvenience, the second beam is eliminated by a non-reflecting surface which is optically matched to the back of the substrate by appropriate liquids or greases with a refractive index close to that of the substrate. This method is particularly suitable for large angles of incidence and was used in the present work. The system used is based on a Gaertner Corporation ellipsometer appropri- ately modified to widen the operating range. The technical characteristics are given in Table III.
T A B L E III TECHNICAL CHARACTERISTICS OF THE GAERTNER L119 UV ELLIPSOMETER Wavelength range 250-1000 nm Minimum lncadence angle 45 ° Accuracy of ~' ___0 03 ° Accuracy of A + 0.05 ° Automation Yes (rotating analyser and null method)
3.4. Spectrol~hotometric measurements Spectr0photometric measurements, which are direct and non-destructive, are frequently used for optical device characterization and, by suitable data processing, allow the simultaneous determination of the film thickness and refractive index. The choice of the most suitable method for determining the optical parameters depends on the characteristics of the film and the substrate. Depending on the material used and the film thickness it may be best to use transmittance or reflectance measurements, oblique or normal incidence, and s or p polarization in appropriate combinations. The film thickness can be derived from only one of these measurements provided that the other optical parameters are known from independent measurements. Transmittance at normal incidence is the most commonly used measurement and provides accurate and reproducible data if systematic errors are taken into account 2. Transmittance measurements at oblique incidence are affected by additional errors because of the positioning of the polarizer and the sample. To minimize such systematic errors in the transmittance measurements at oblique incidence using p-polarized light we chose an angle of incidence equal to the Brewster angle of the substrate (at 2 = 5000 ,~). The sa~nple and the polarizer were positioned correctly by searching for the minimum of the reflected light. To avoid possible defocusing errors
xlO -I 3.O 2. o
E ,,, 1.
.D 0 " •JJ" D" Jr W"
I I I I I I 0.3 0.9 1.5 2.1 2.7 3.3 xlO -
Fig 5 Mass thickness of an alumlmum film on a quartz substrate as a function of the raUo K.
Finally, it must be stressed that X-ray microanalysis provides the mass thickness, and not the geometrical thickness, of the analysed film; large inaccuracies in the determination of geometrical thickness can occur if the density of the film is not well known. The analysis reported here was performed using a Jeol JSM U3 scanning electron microscope equipped with an O R T E C EEDS II energy-dispersive X-ray analysis system. Some characteristics of this instrument are given in Table V.
TABLE V TECHNICAL CHARACTERISTICS OF THE X-RAY MICROPROBE Thickness range
Accuracy Detectable elements
< 100 ,~ to about 1 lam (according to film composmon) 2%-5% From Z > 11 with an energy-dispersive system From Z > 6 with a wavelength-dispersive system
The measurement of the thickness of optical coatings is difficult if reliable and accurate results are expected, even if different techniques are employed. Reliable results can be obtained only after a very accurate set of operations, including setting up the instruments, measuring the same thickness using a variety of techniques, analysing the results critically and performing a suitable calibration, has been carried out. Data derived from a set of measurements carried out using the techniques described on identical samples are compiled in Table VI. As an additional control the samples were tested using other techniques. Specifically, measurements were performed using microgravimetry and elemental chemical analysis. These methods give a mass value, and thus the film thickness can be obtained for a known material density after measuring the surface area of the film. Whereas with the other techniques the thickness is measured on a small area of the sample or at a point, these techniques give a mean value of the thickness of the whole sample; this value may be different from that obtained from single-point measure- ments because of film non-uniformities.
256 A. P 1 E G A R I , E. M A S E T T I
Zr~
Z
"
r ~ ~
t~ ~
II II^ II
o ~ ¢q II II II