
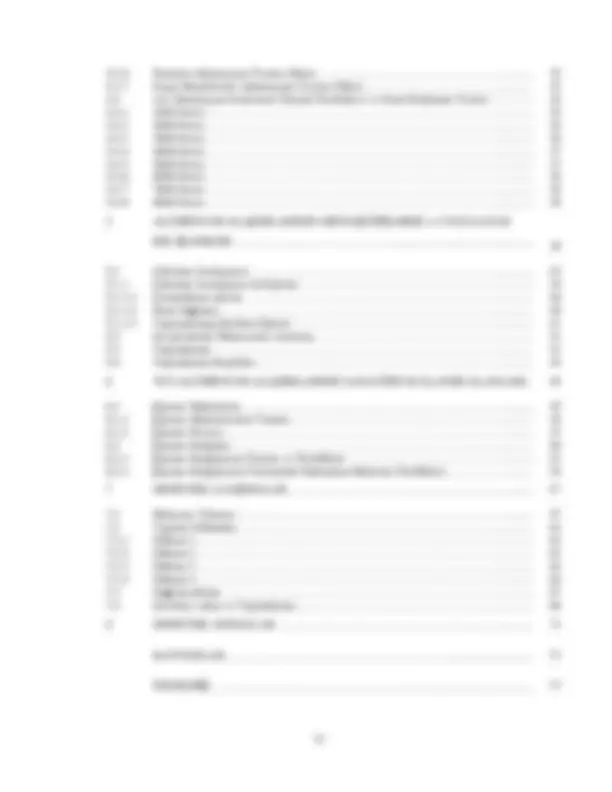
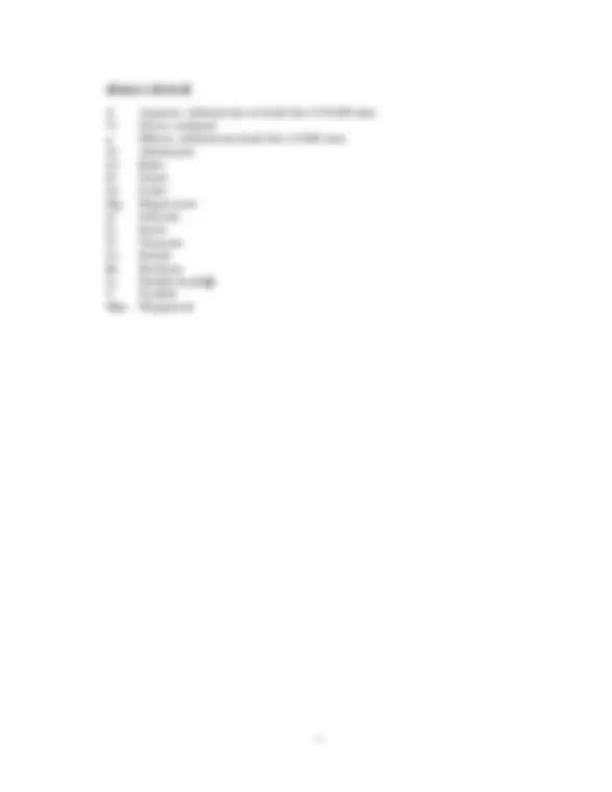
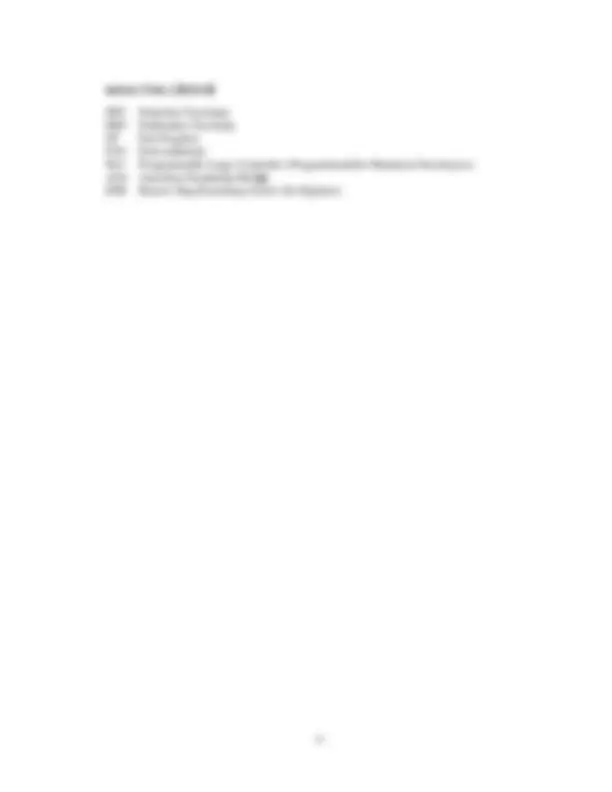
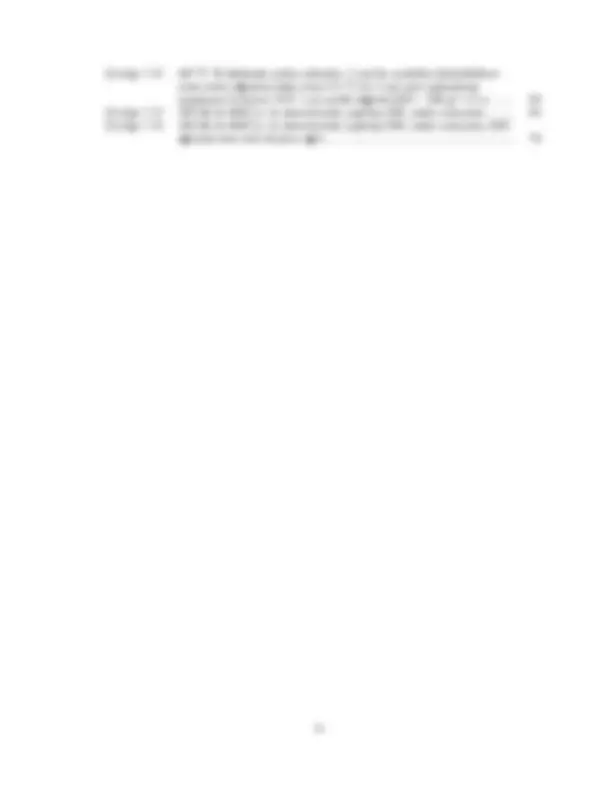
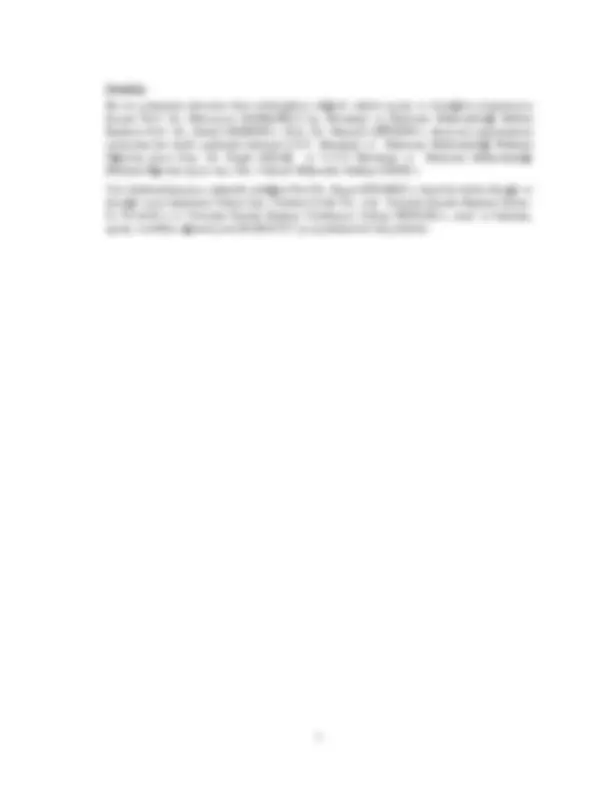
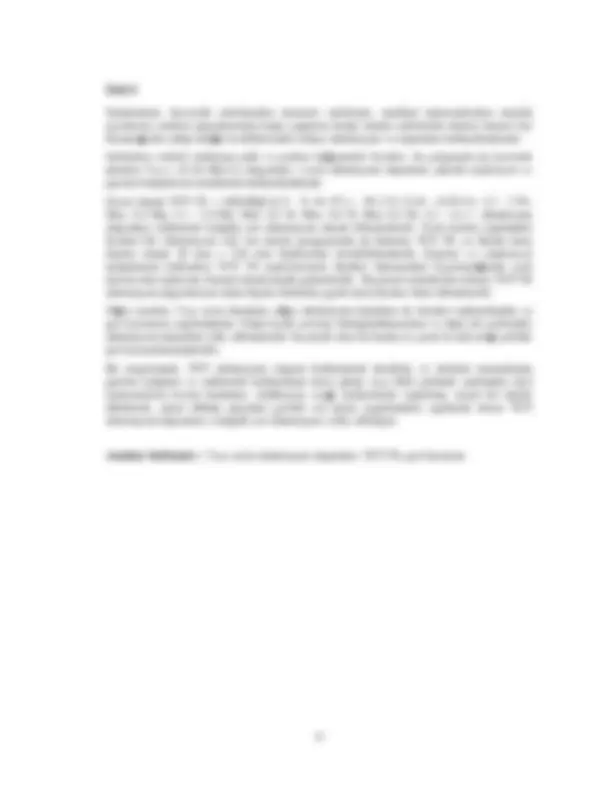

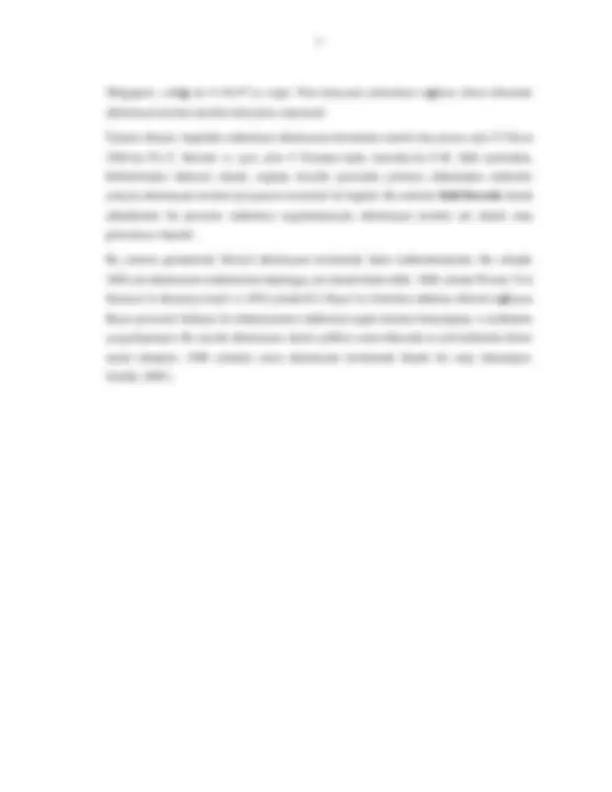
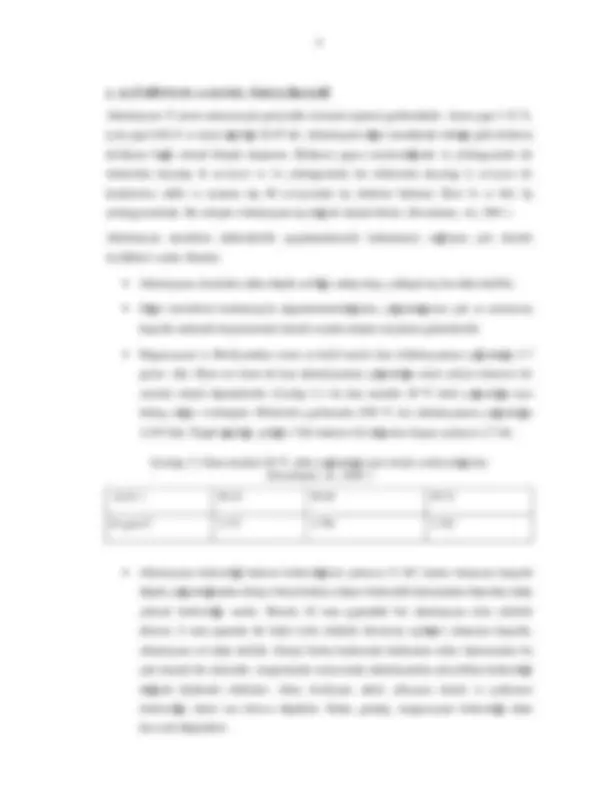
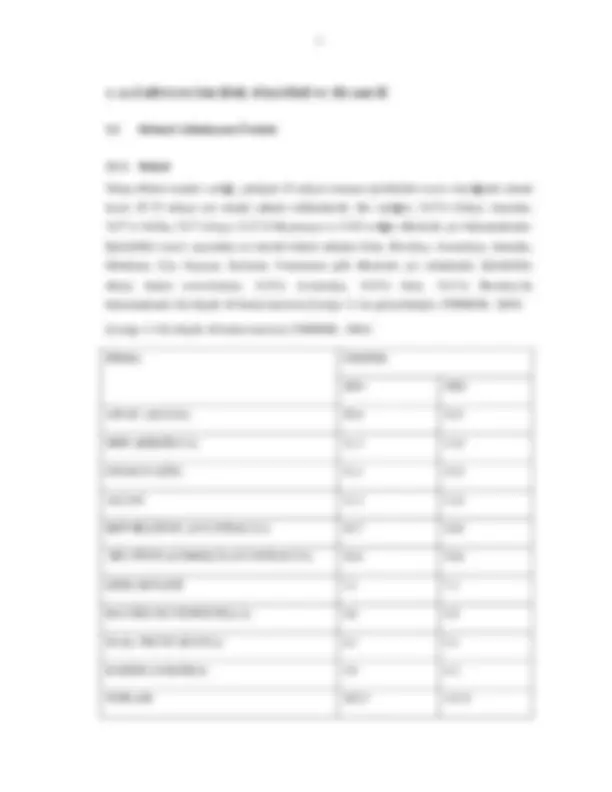
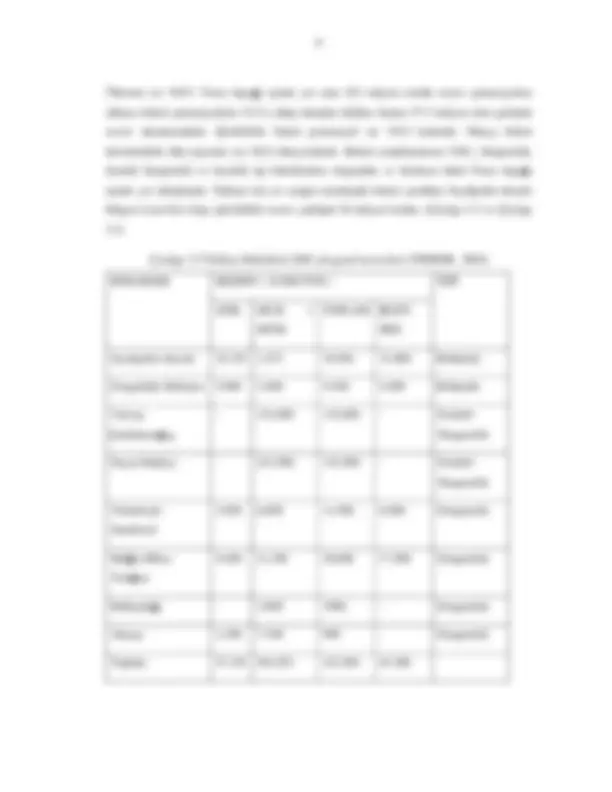
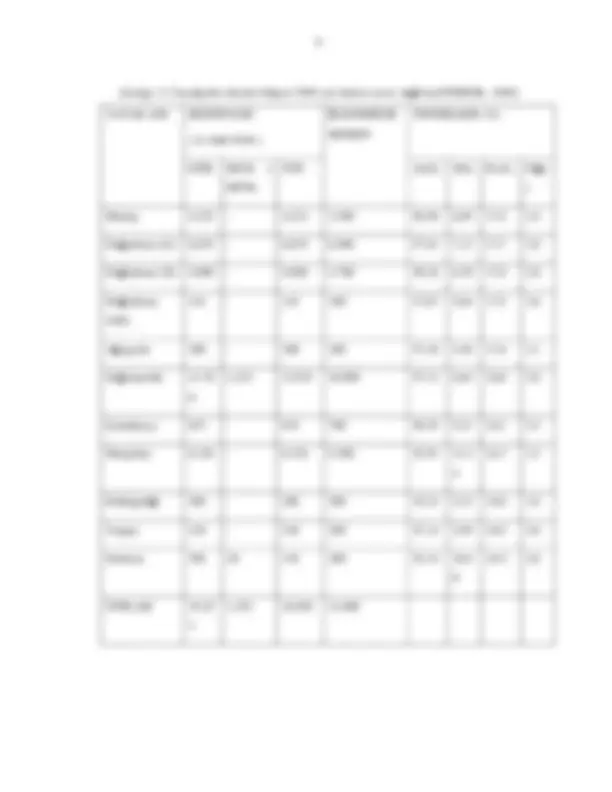
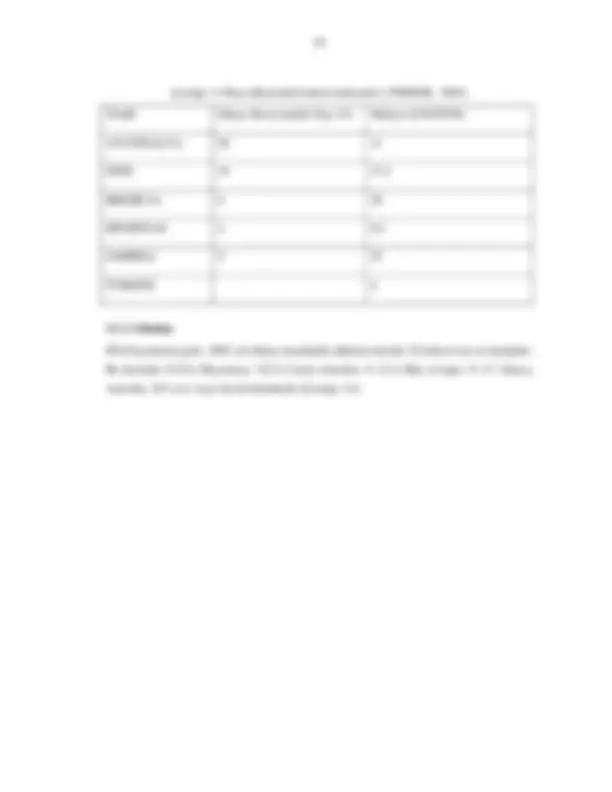
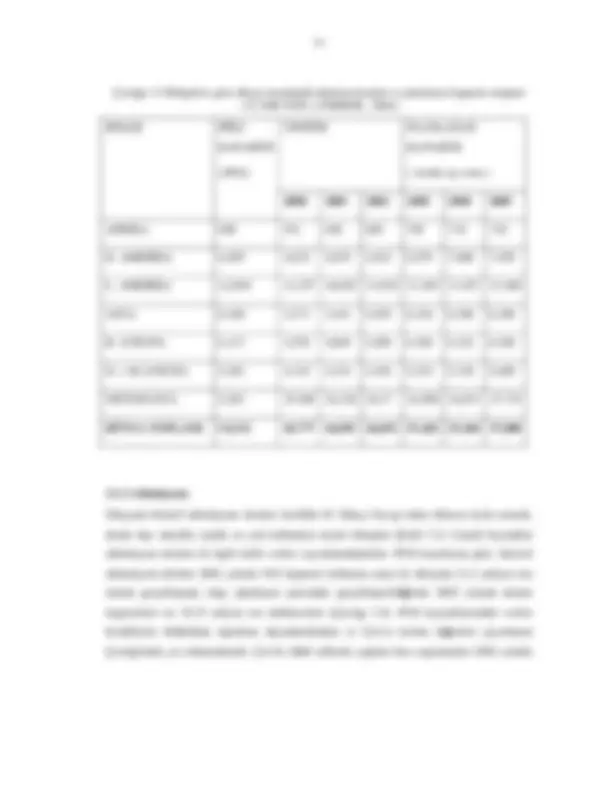
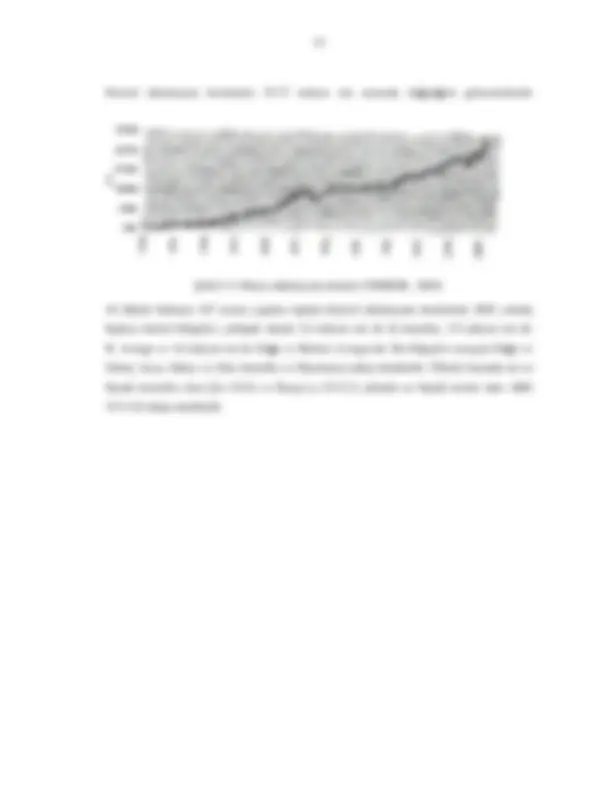
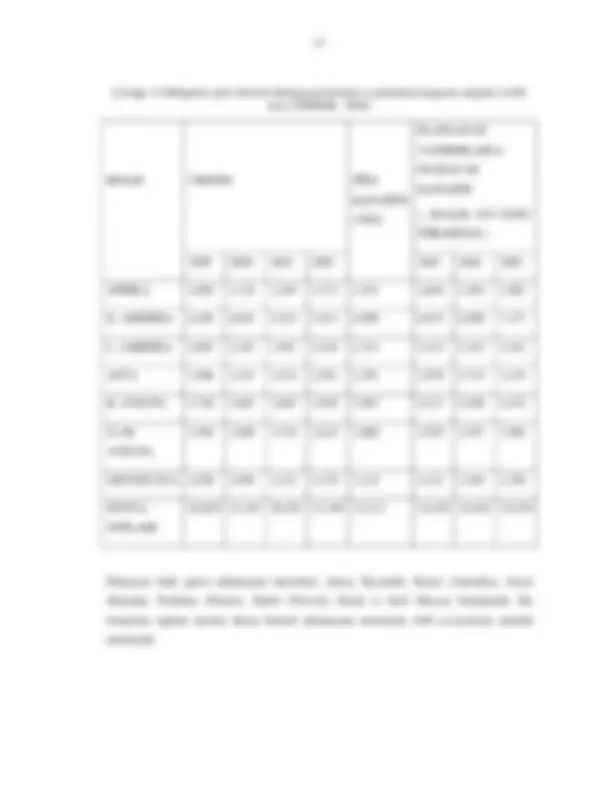
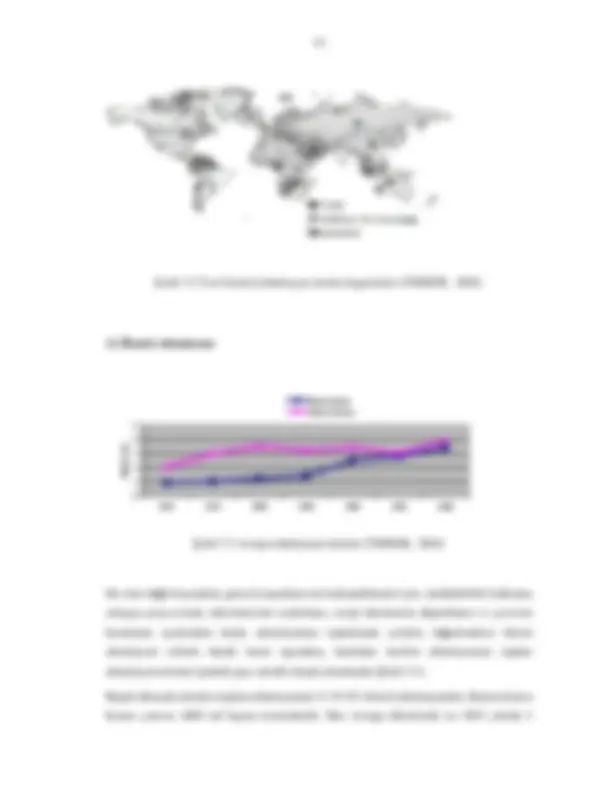
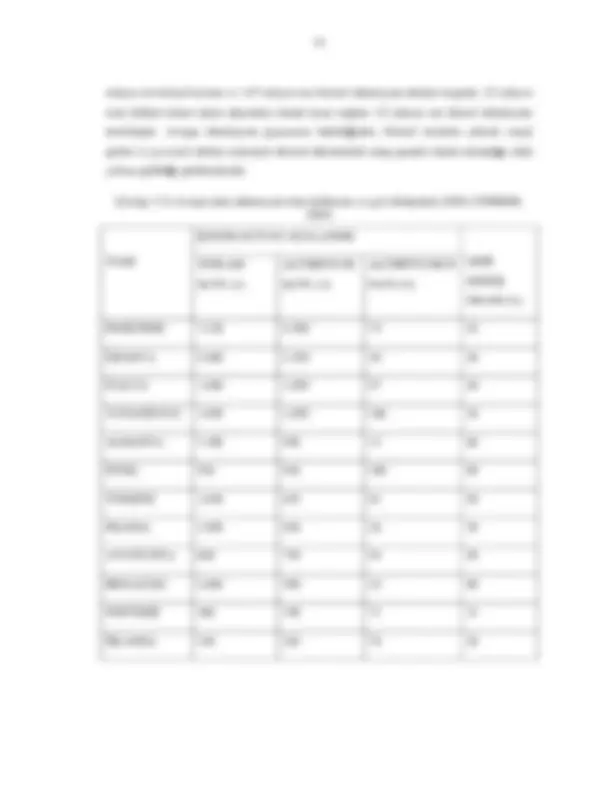
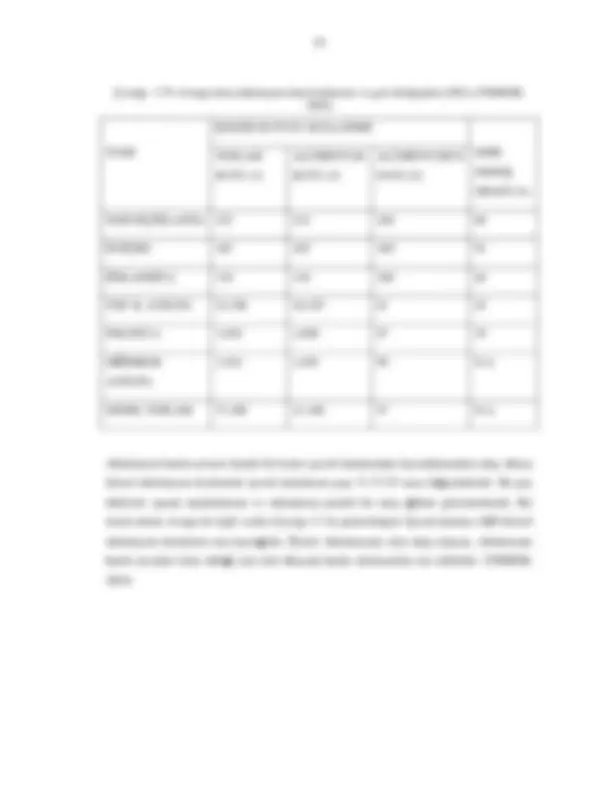
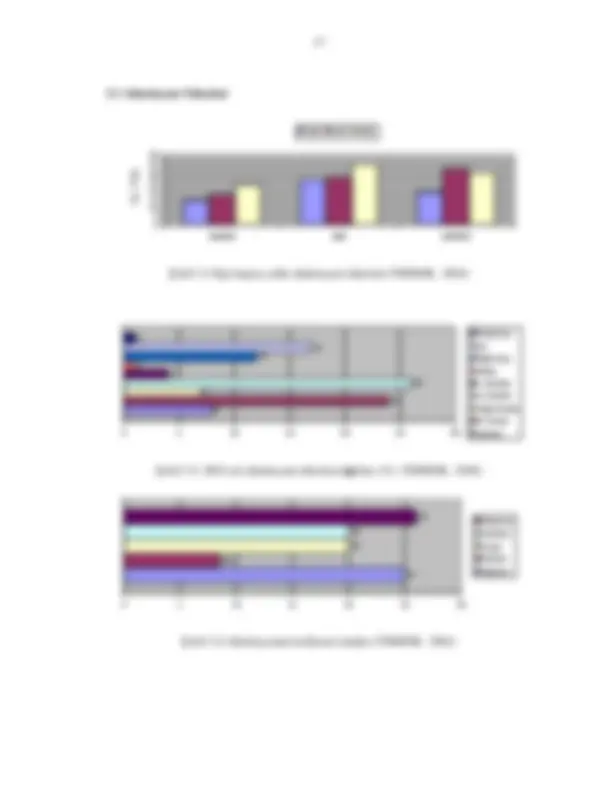
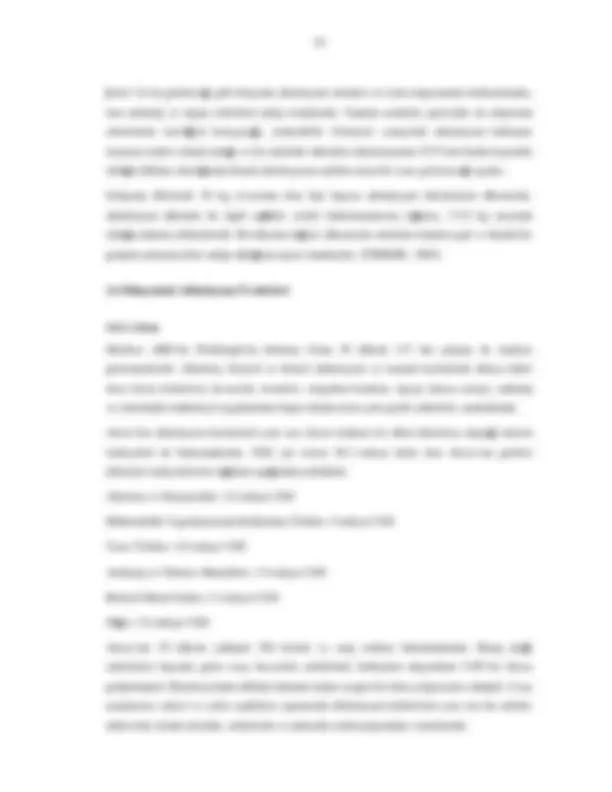
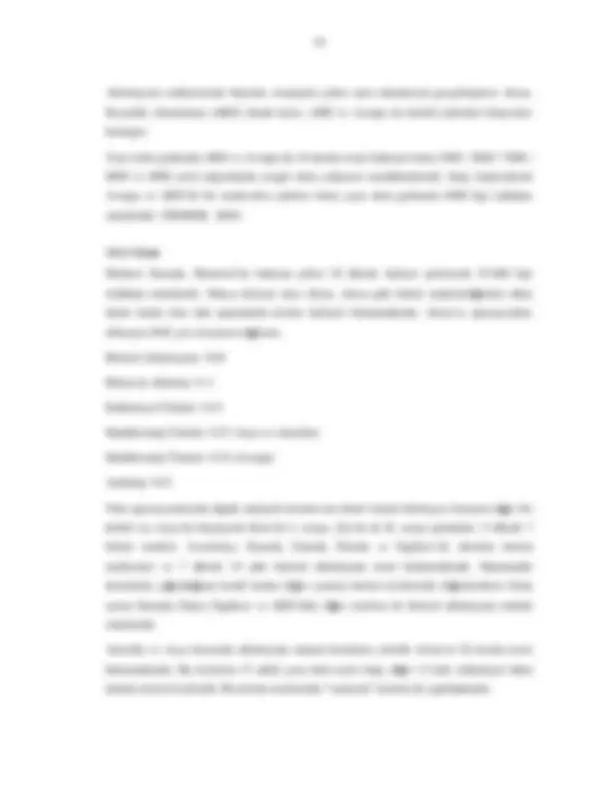

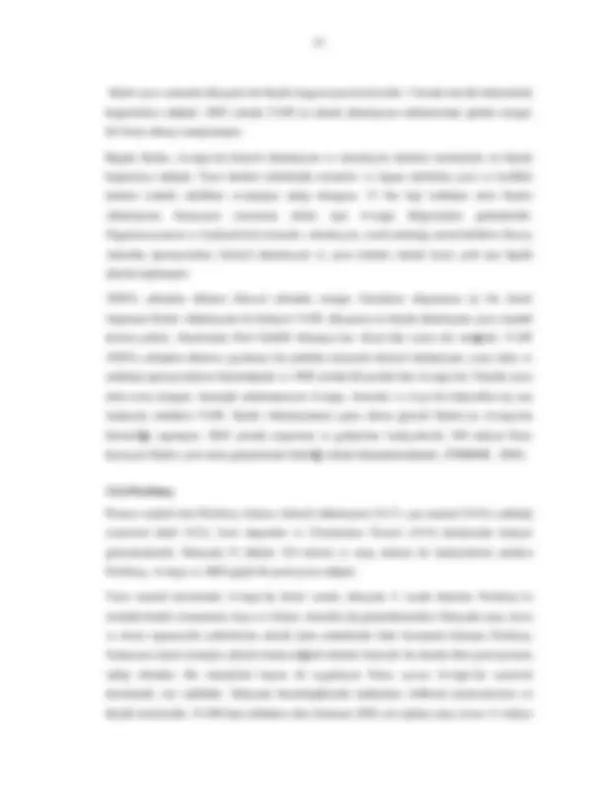
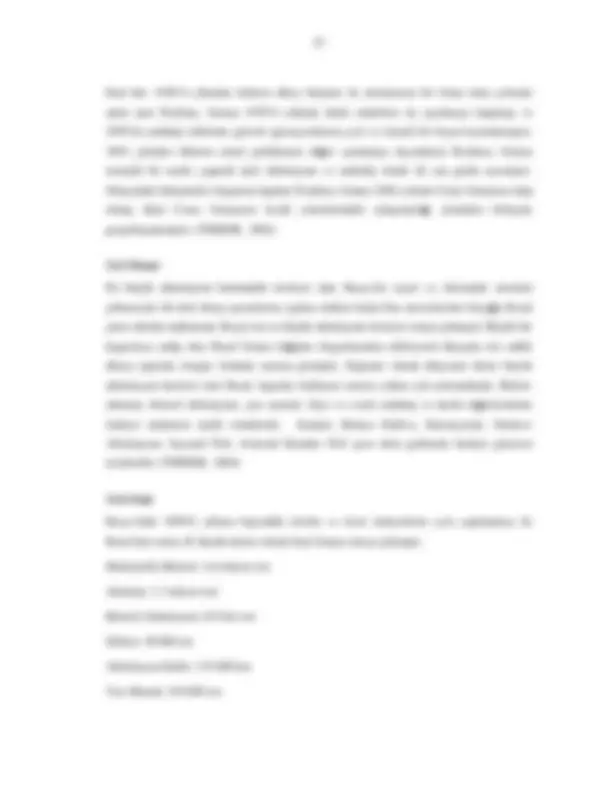
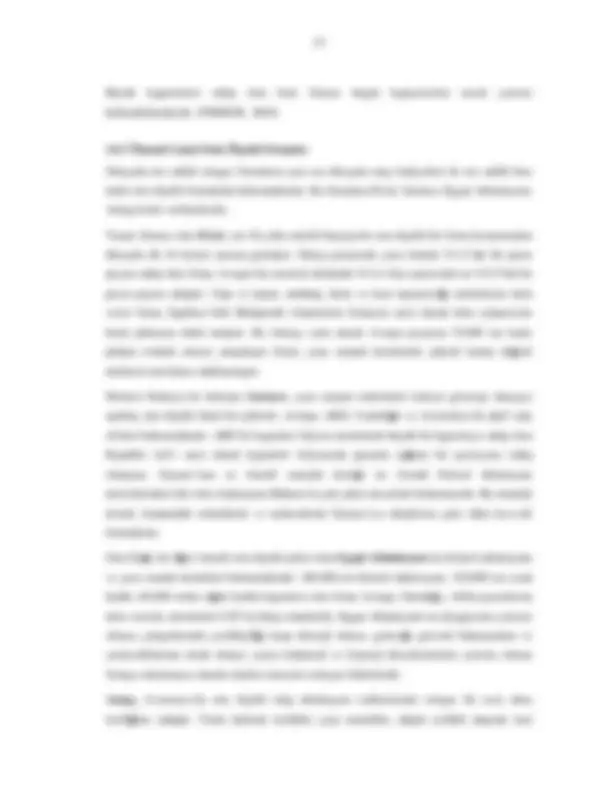
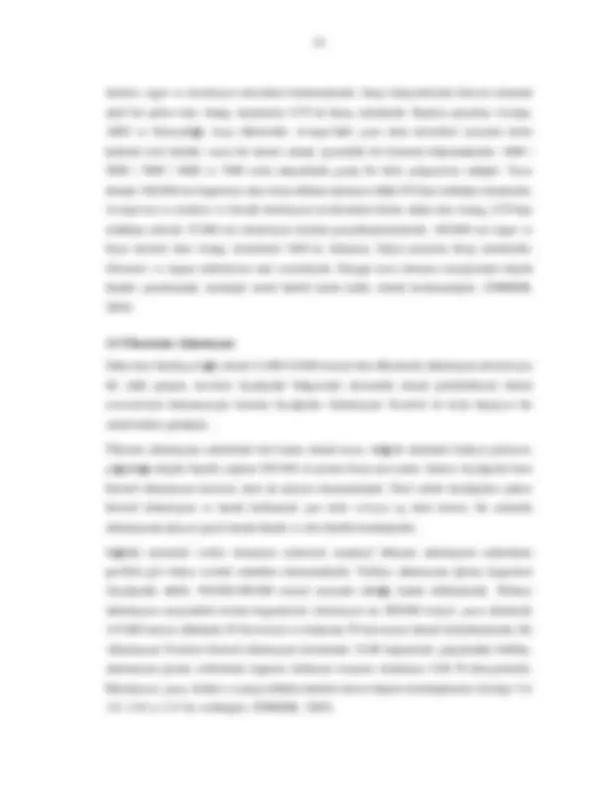
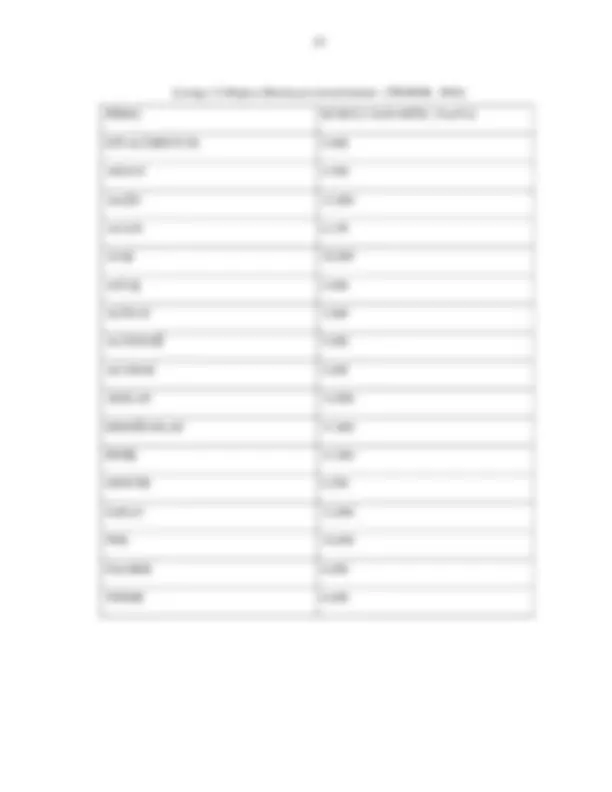
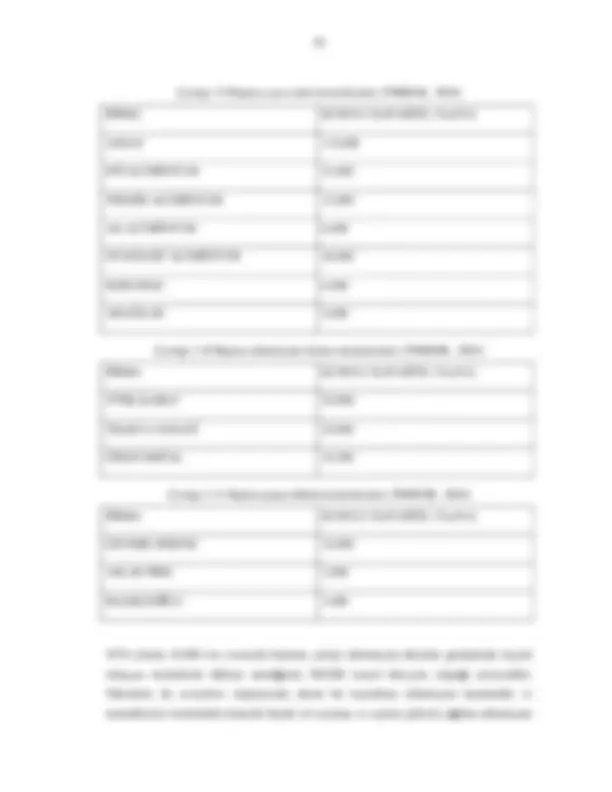
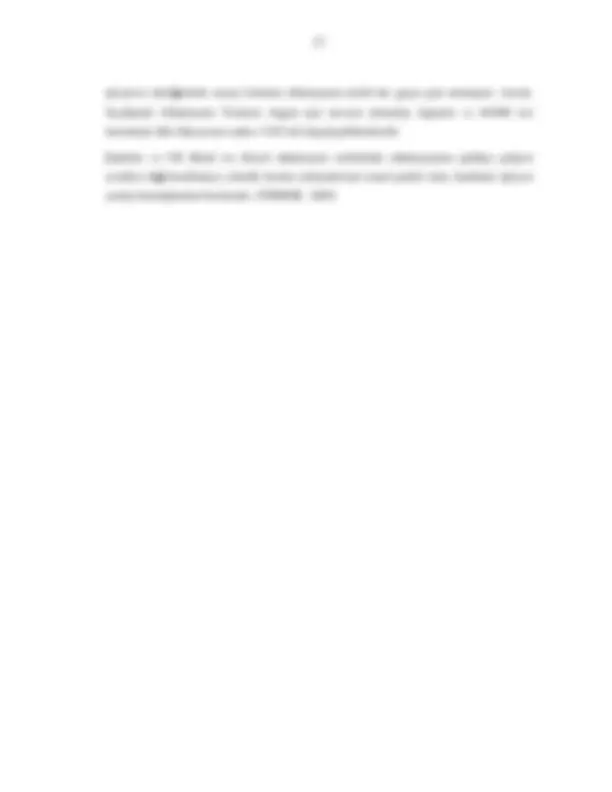
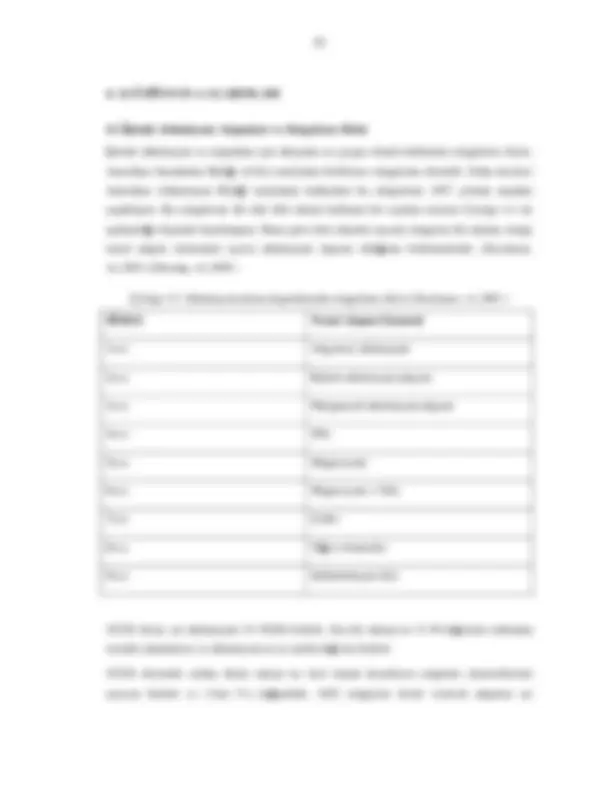
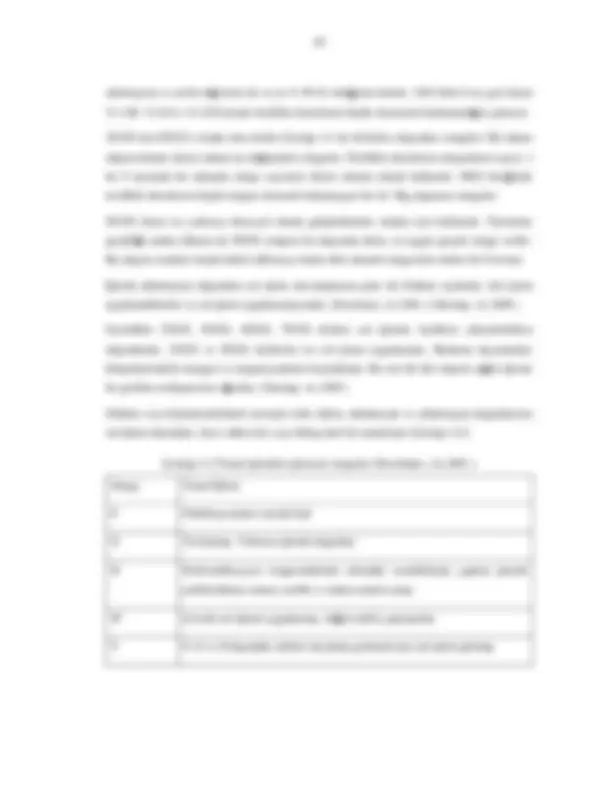
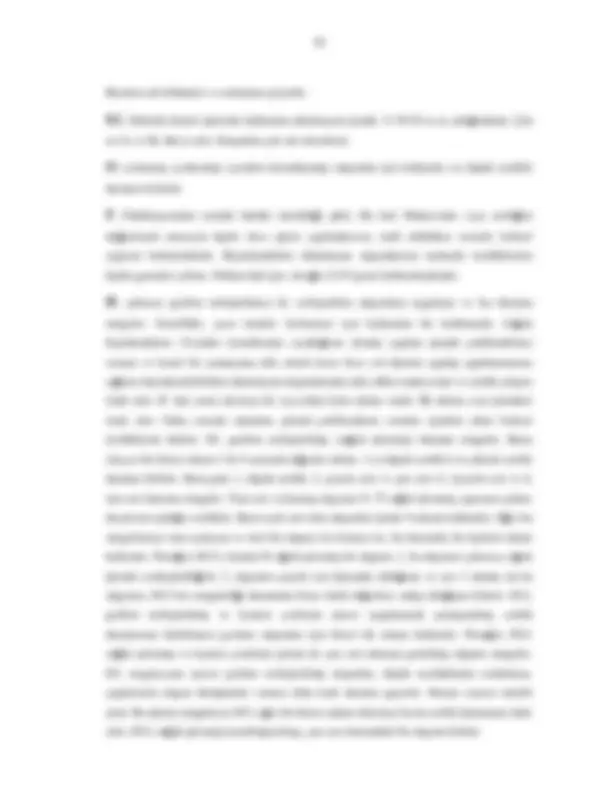
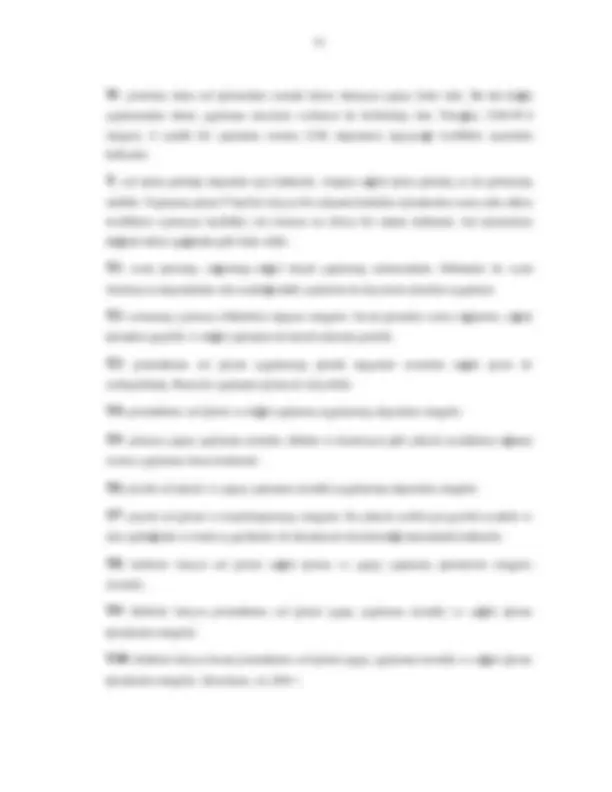
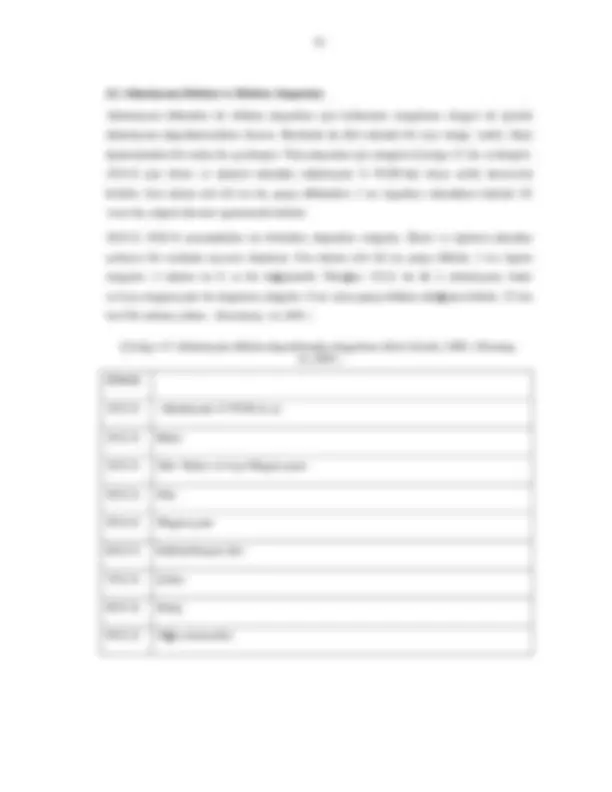
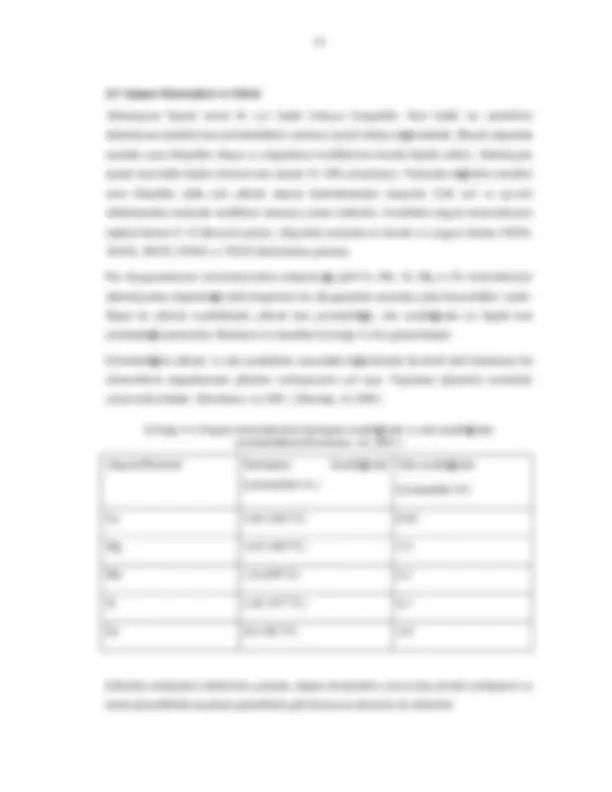
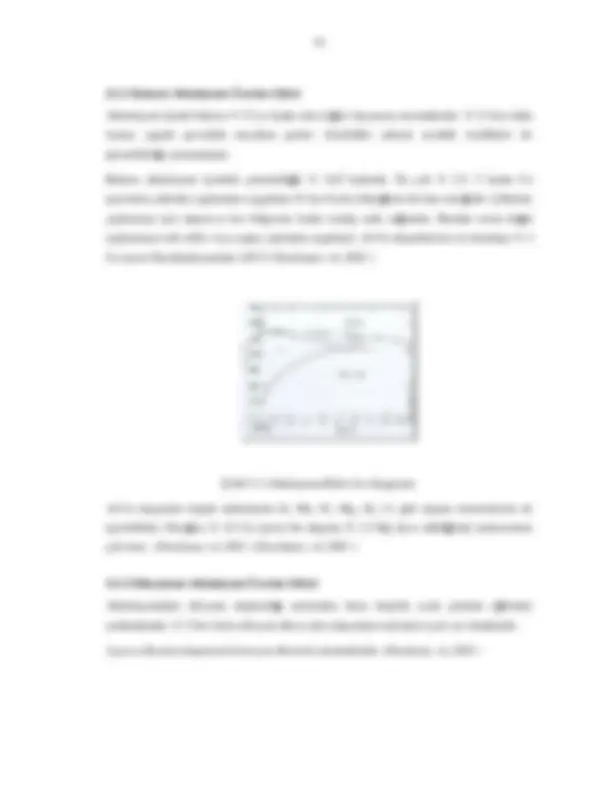
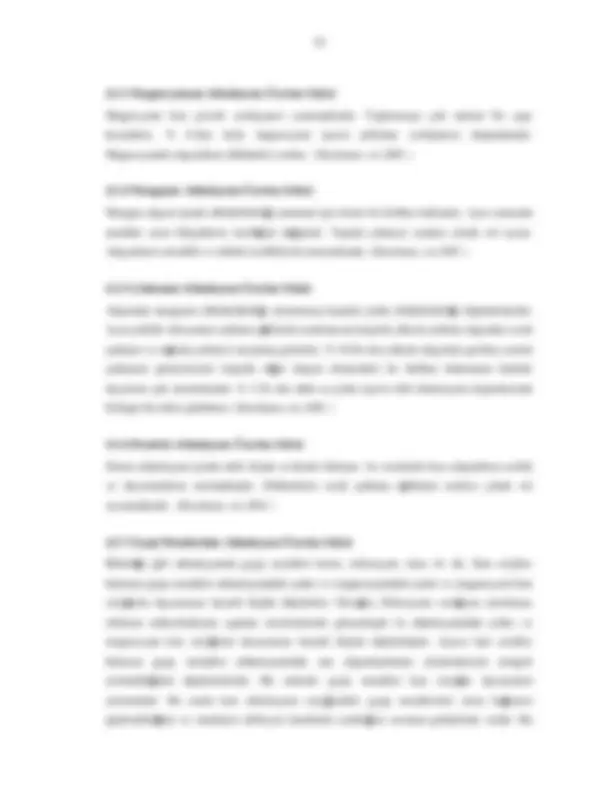
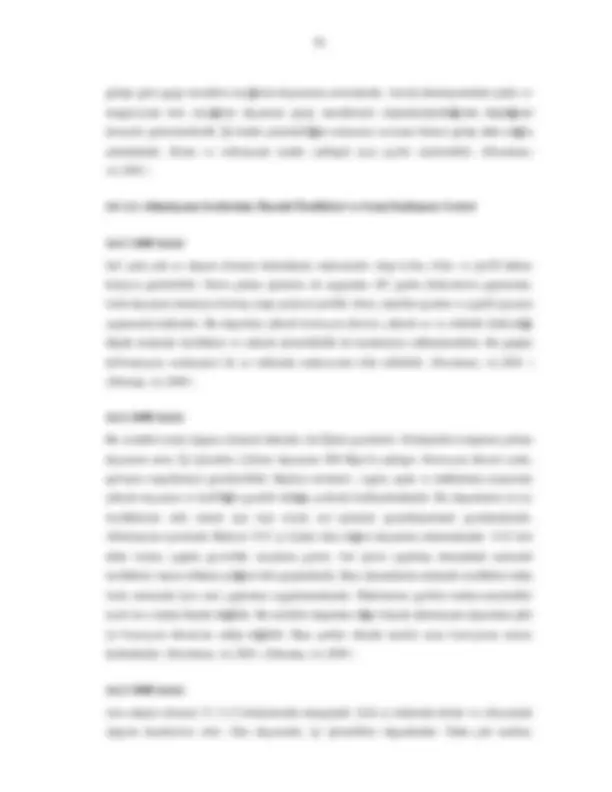
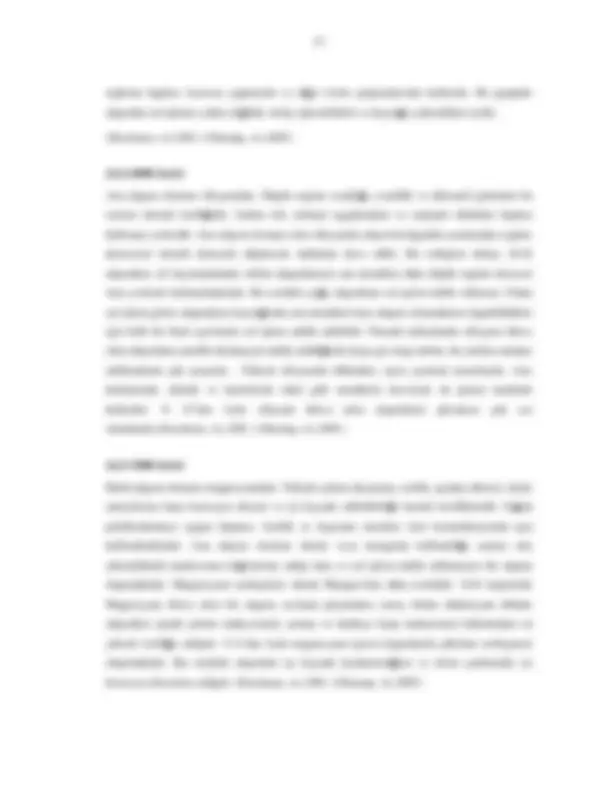
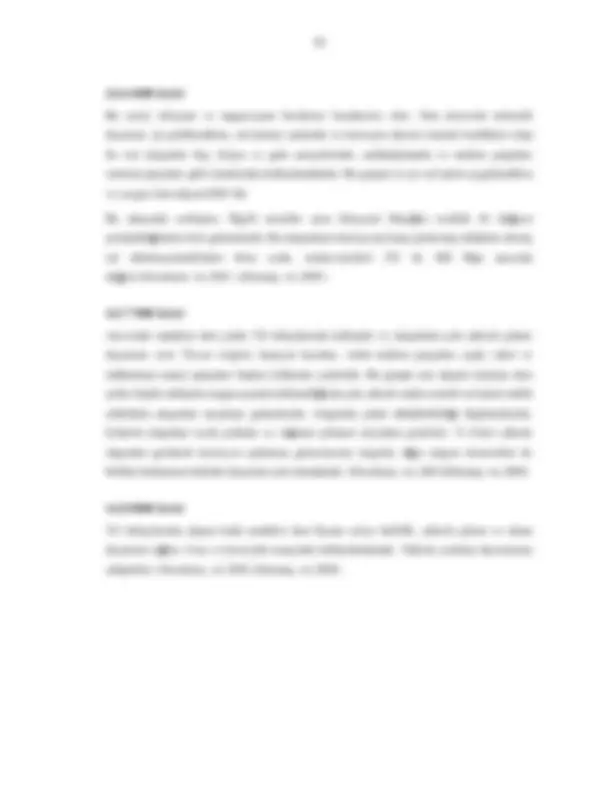
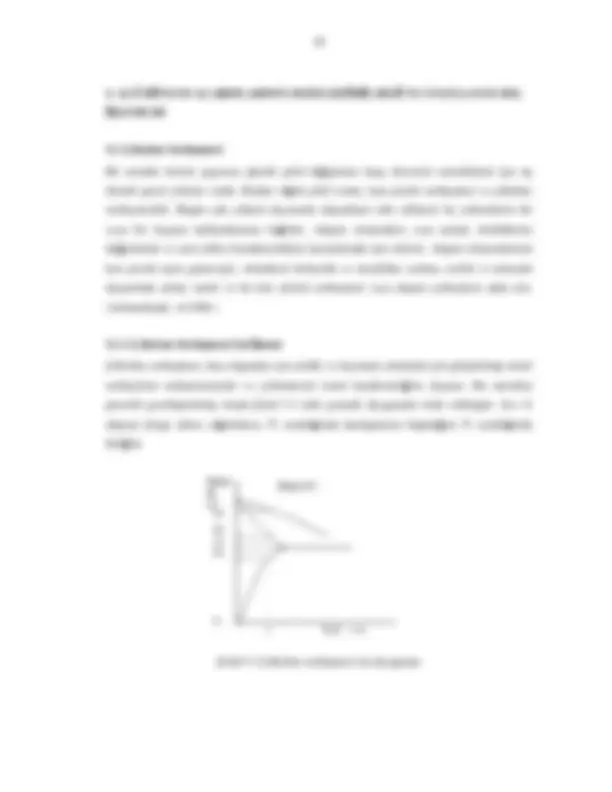
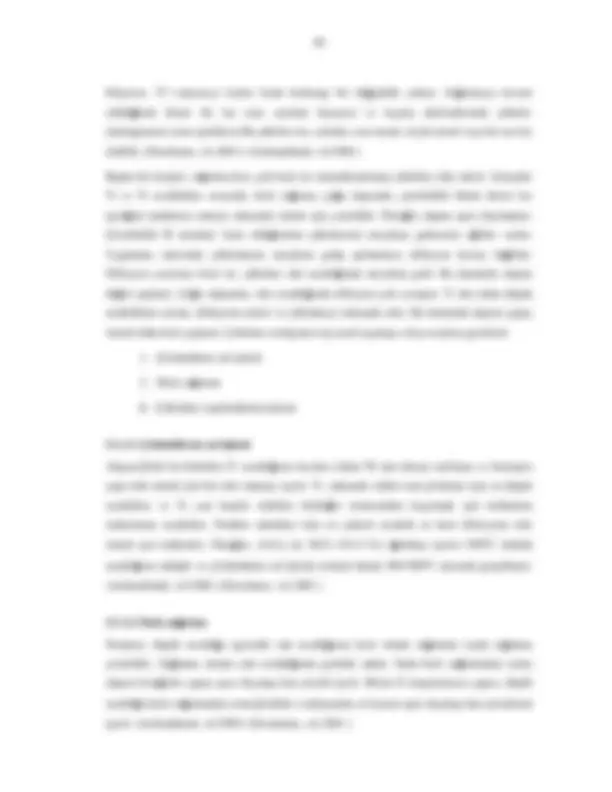
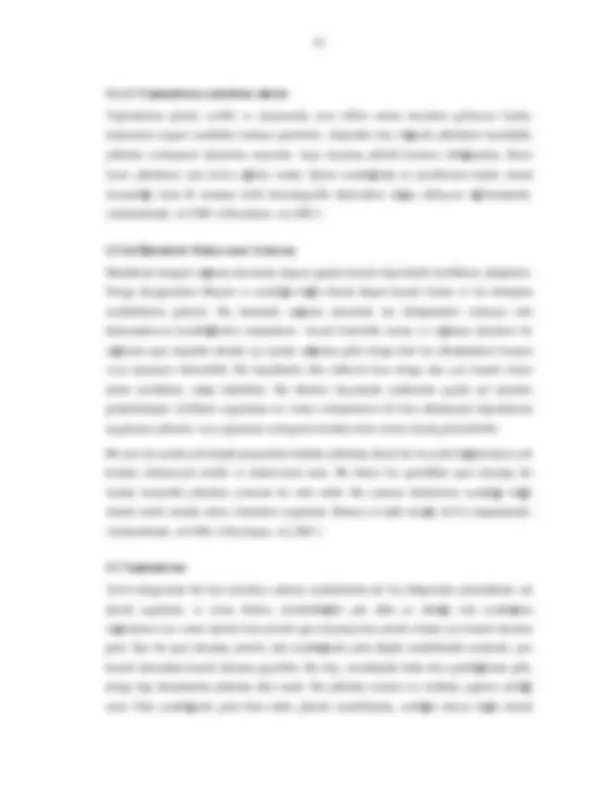
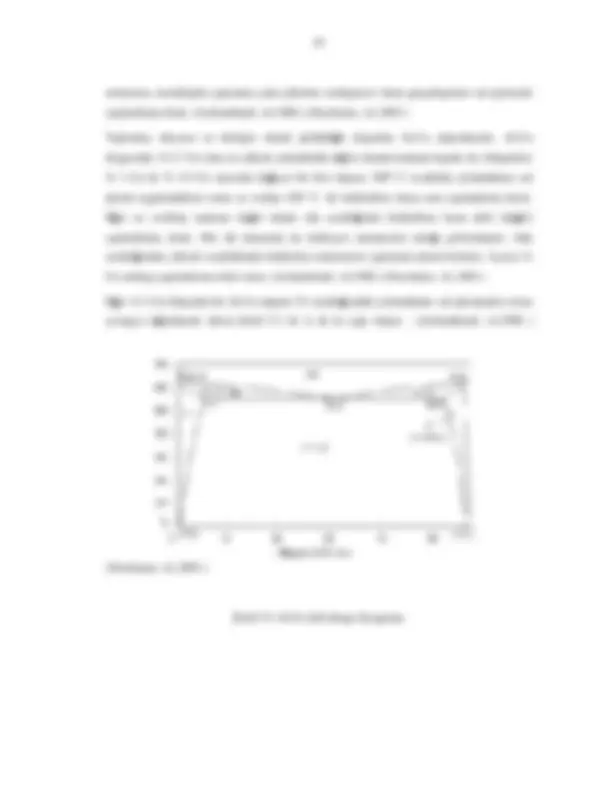
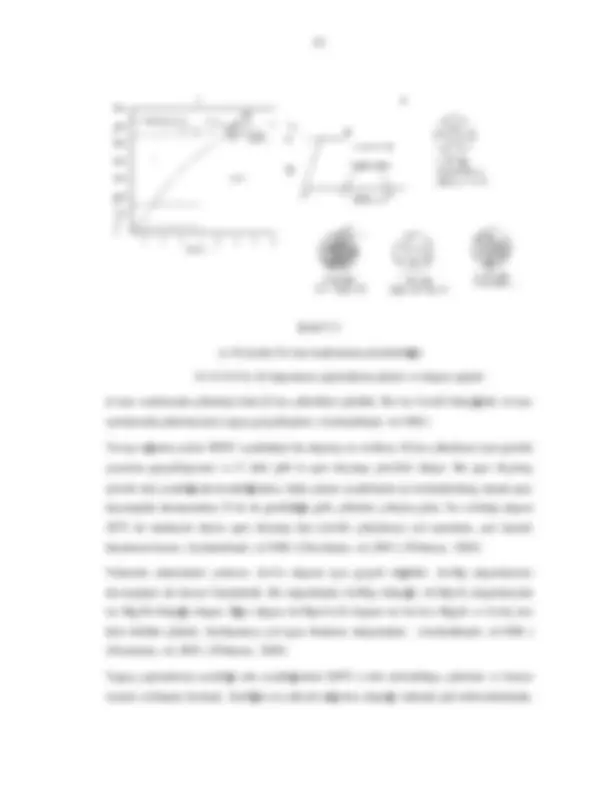
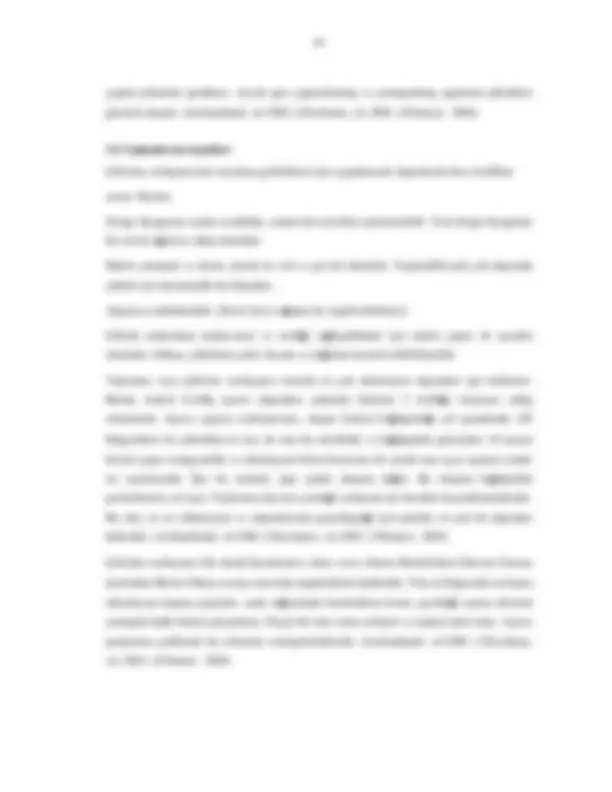
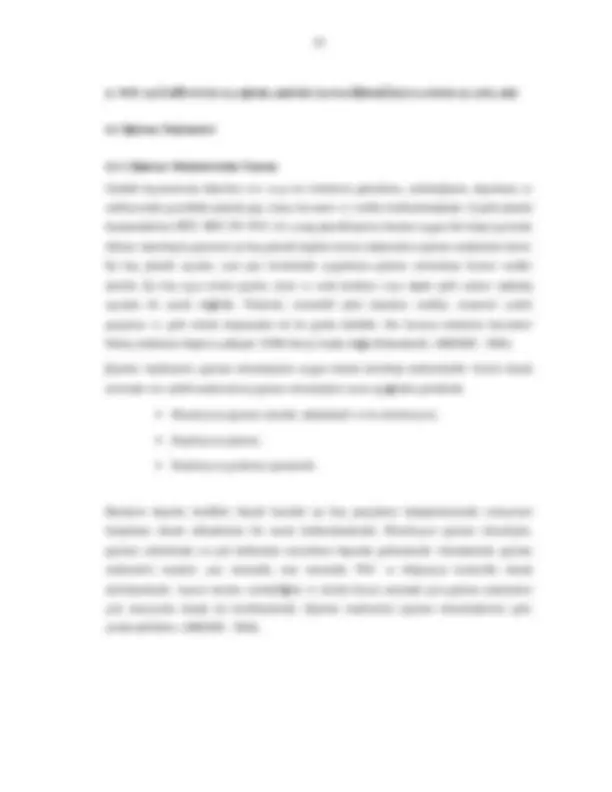
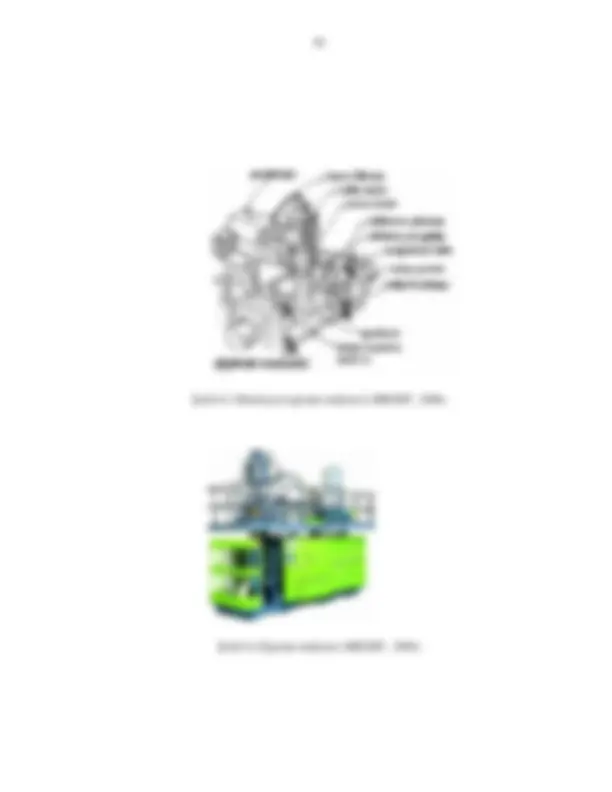
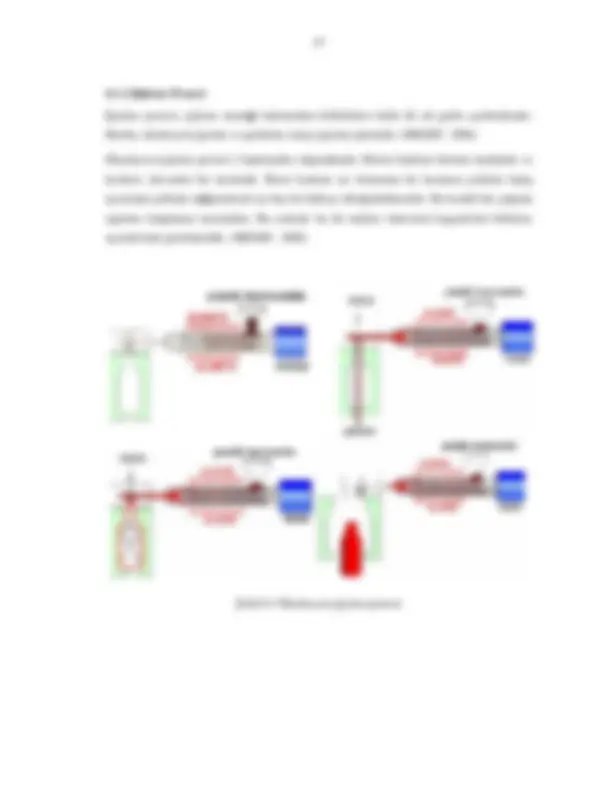
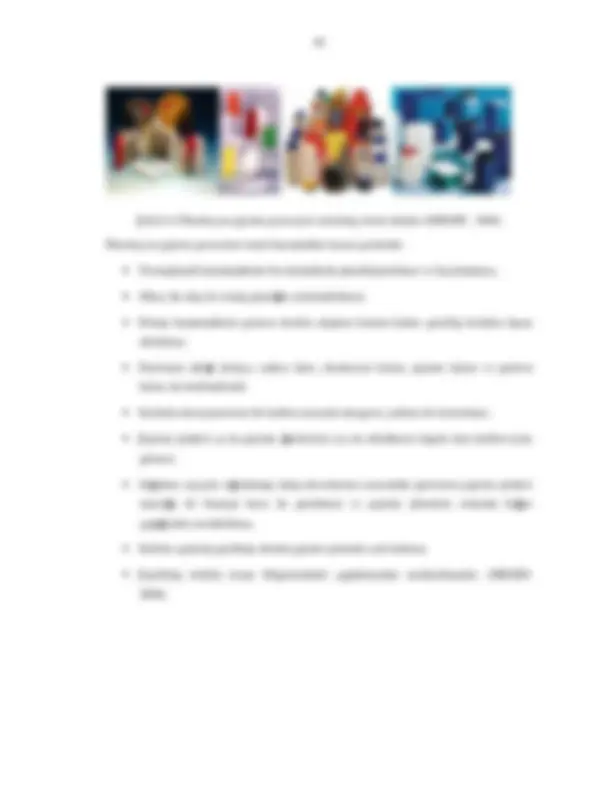
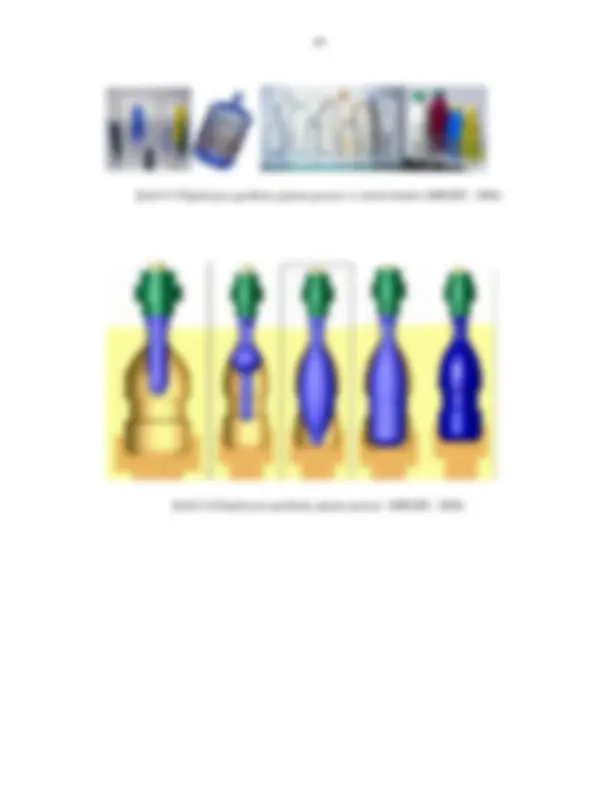
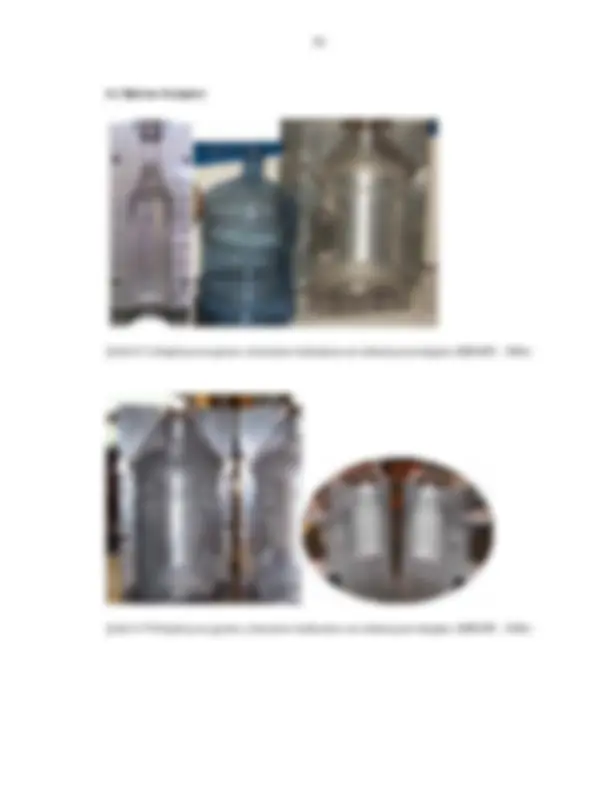
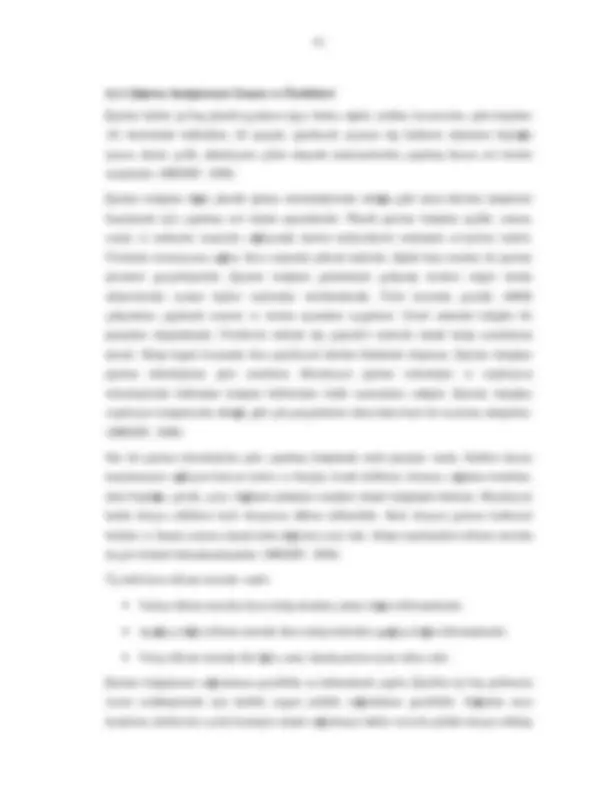
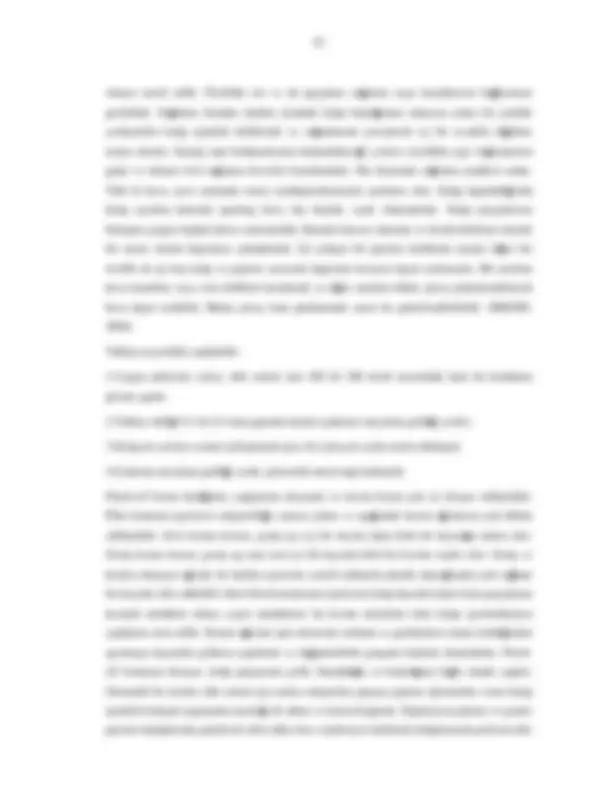
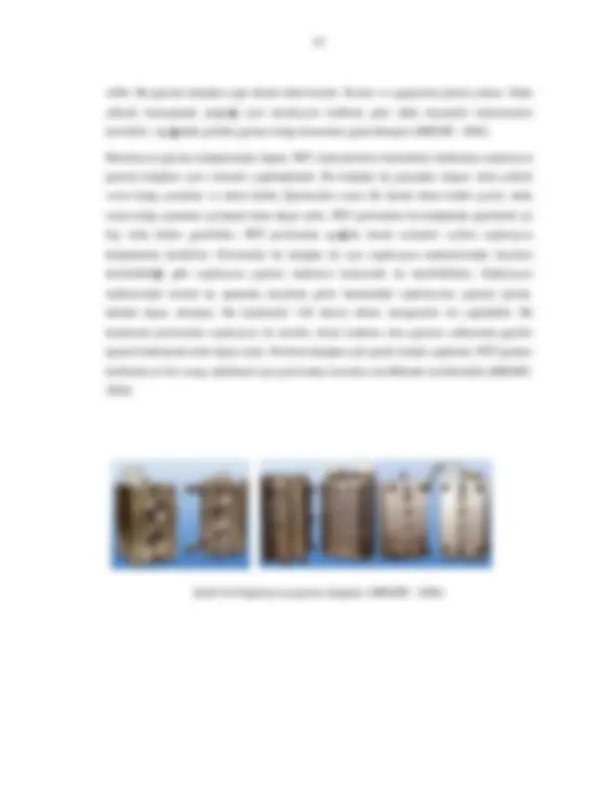
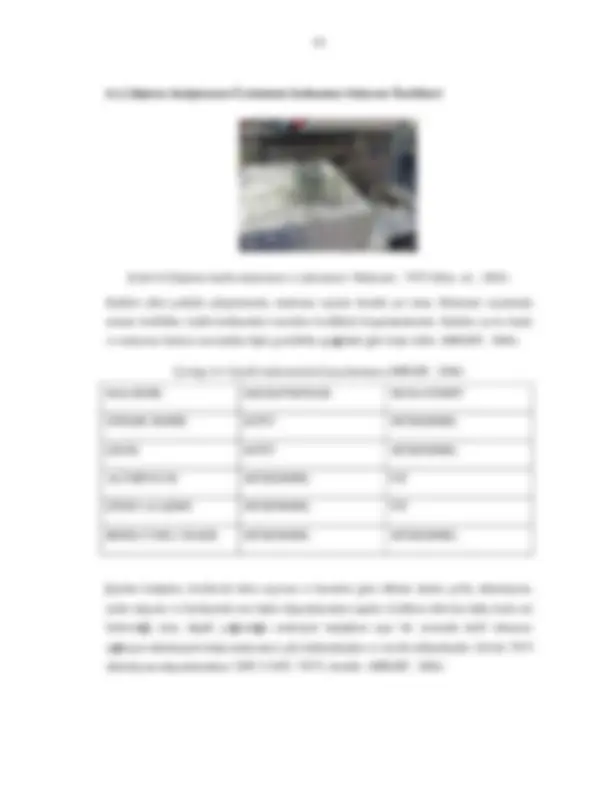
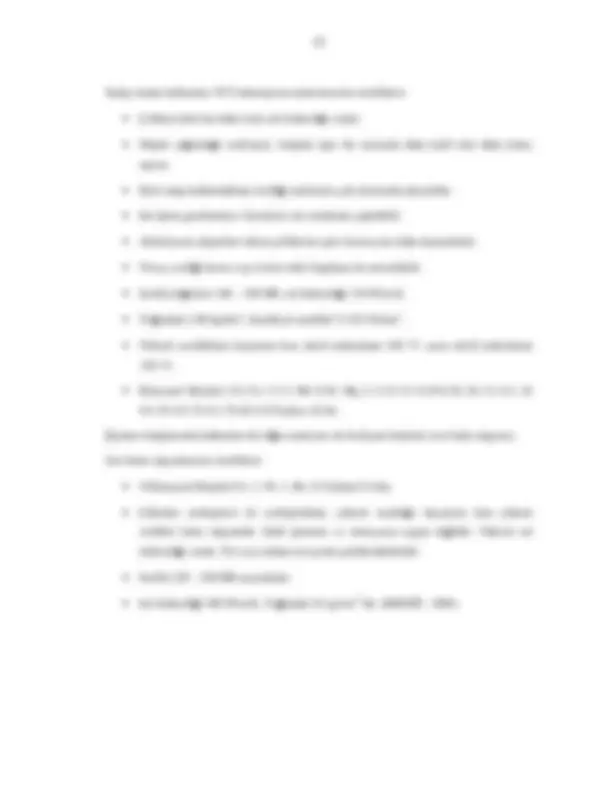
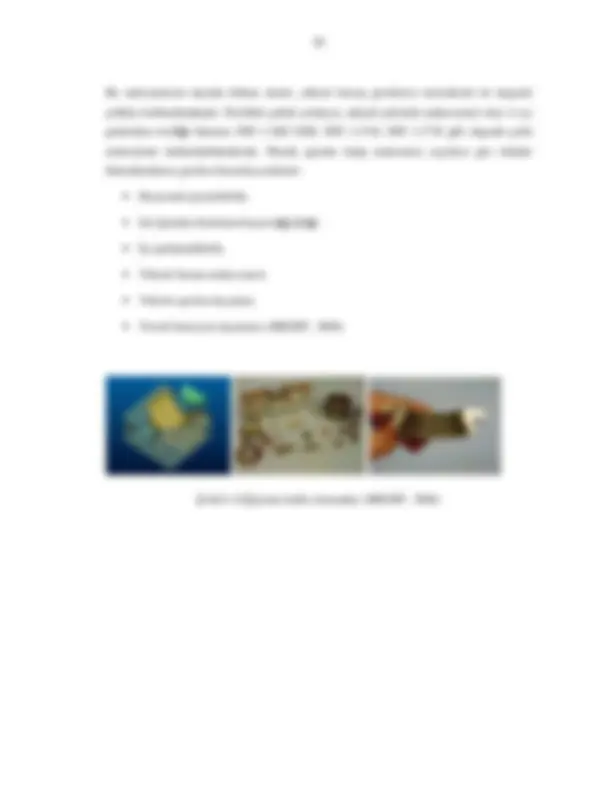
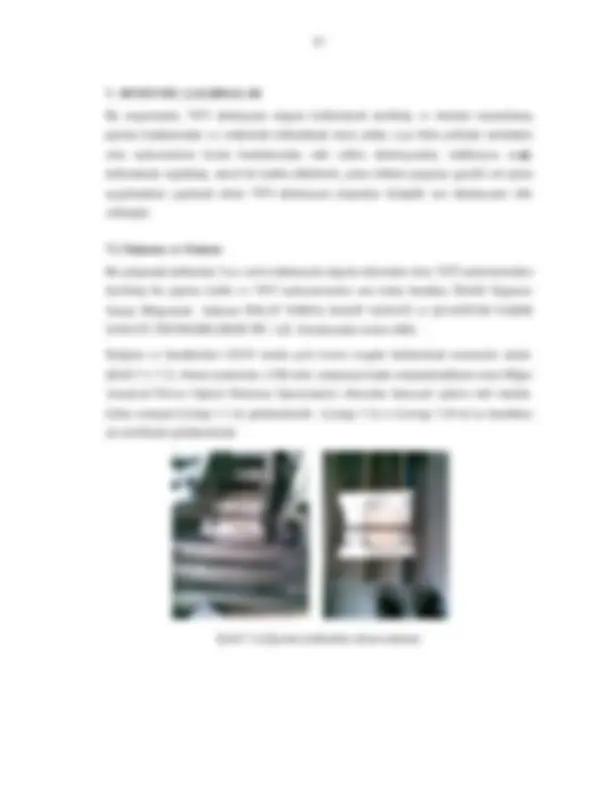
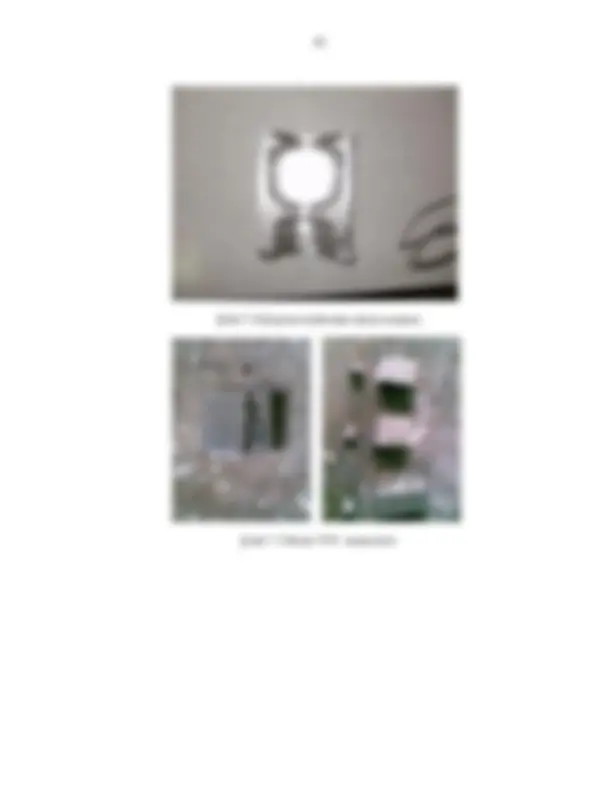
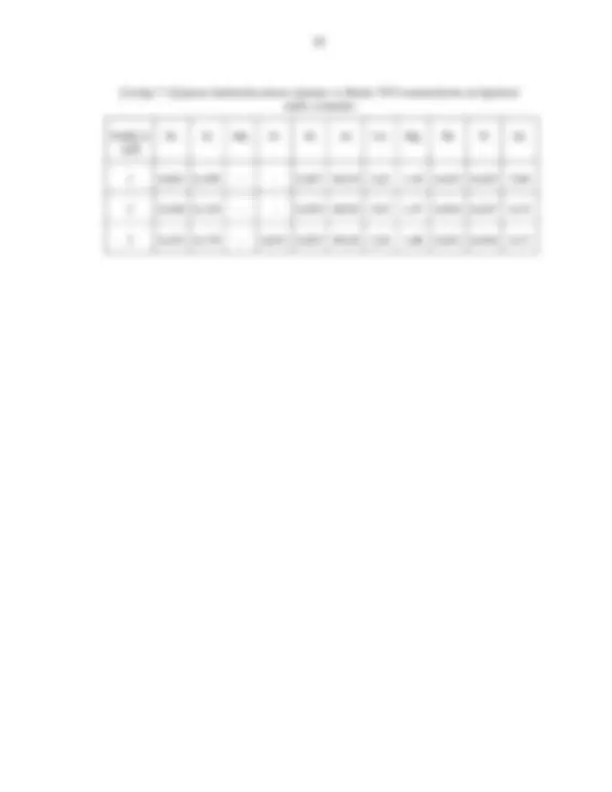
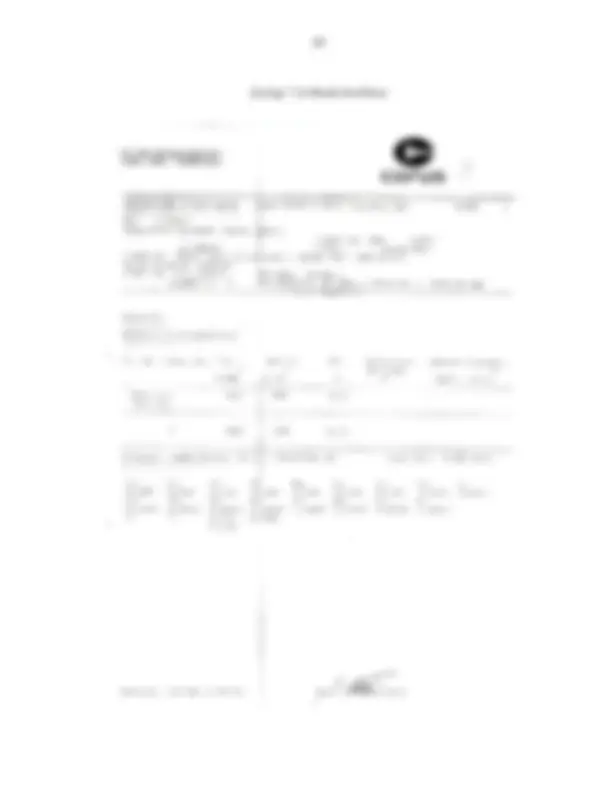
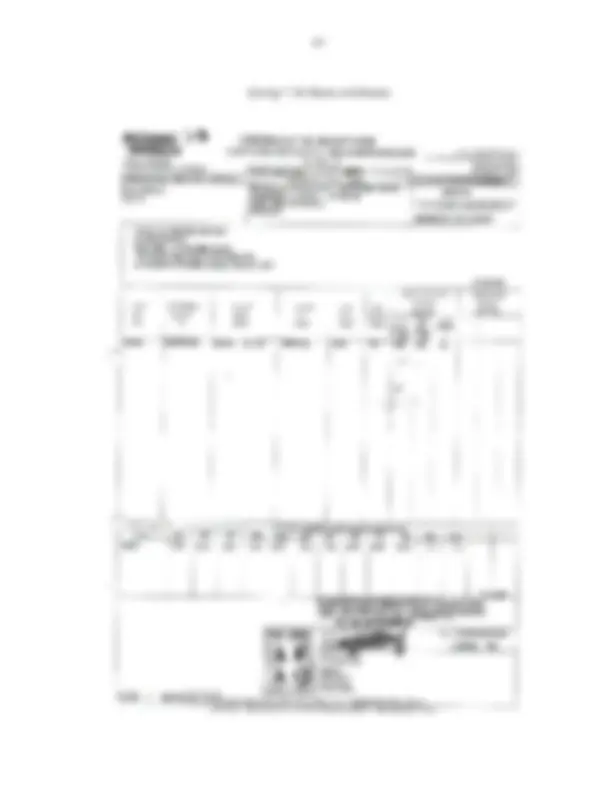
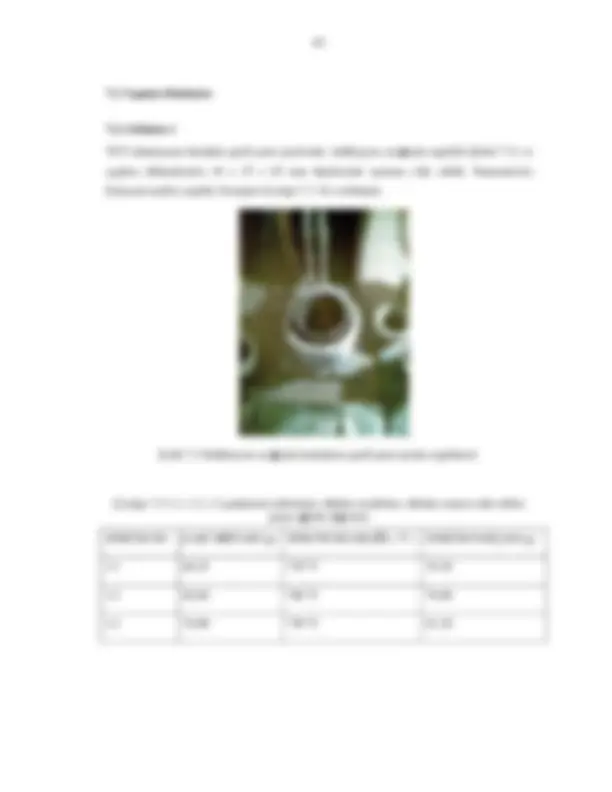
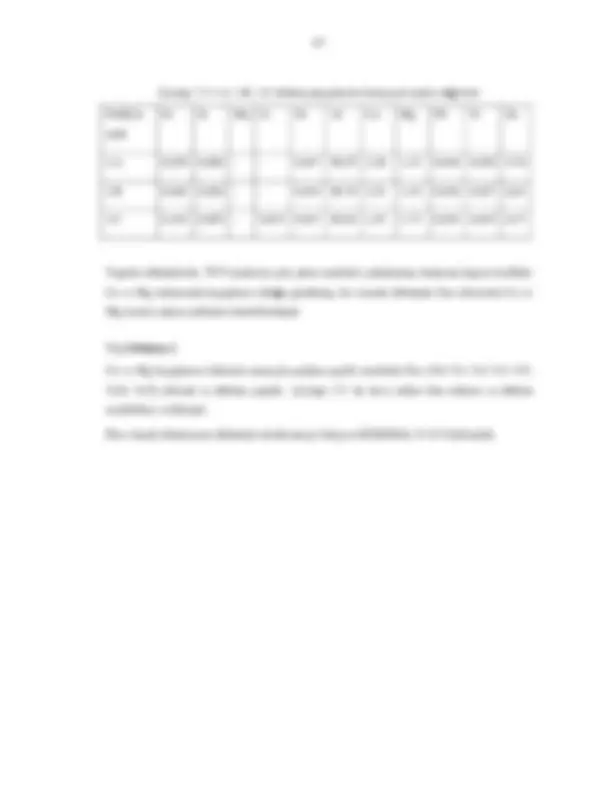
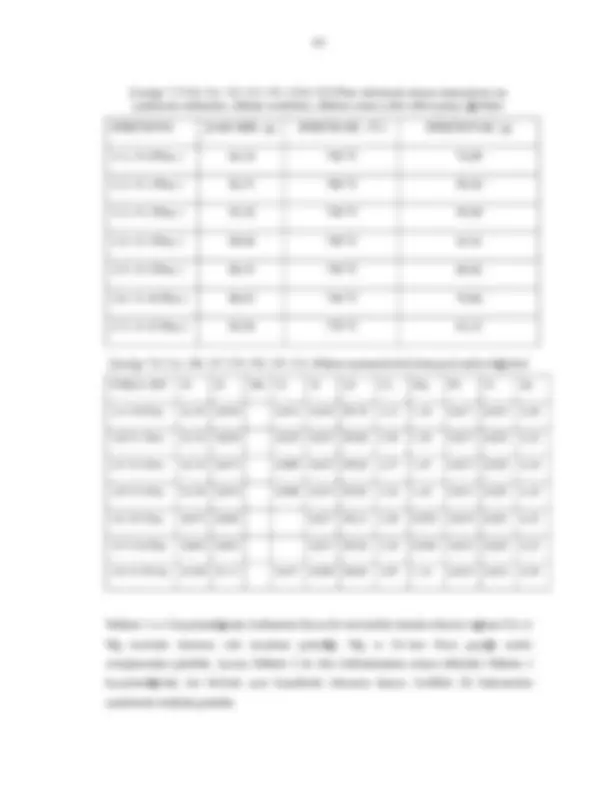
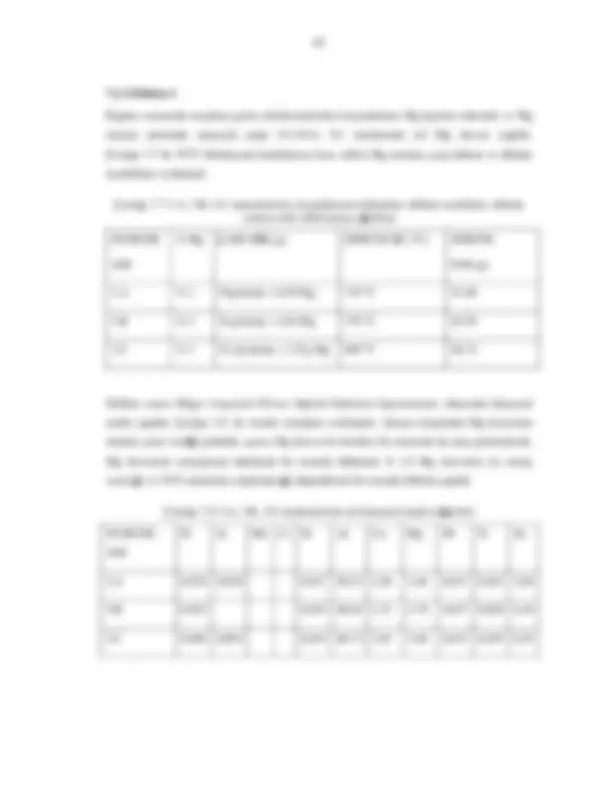
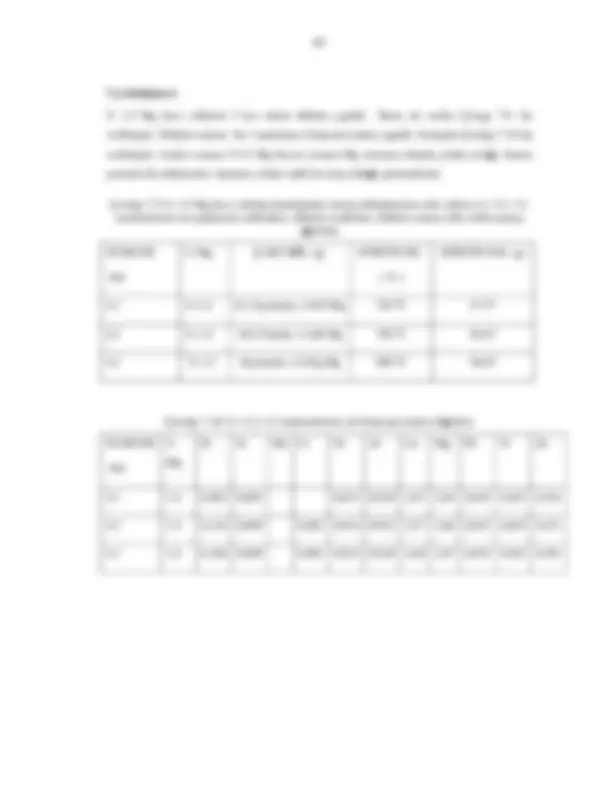
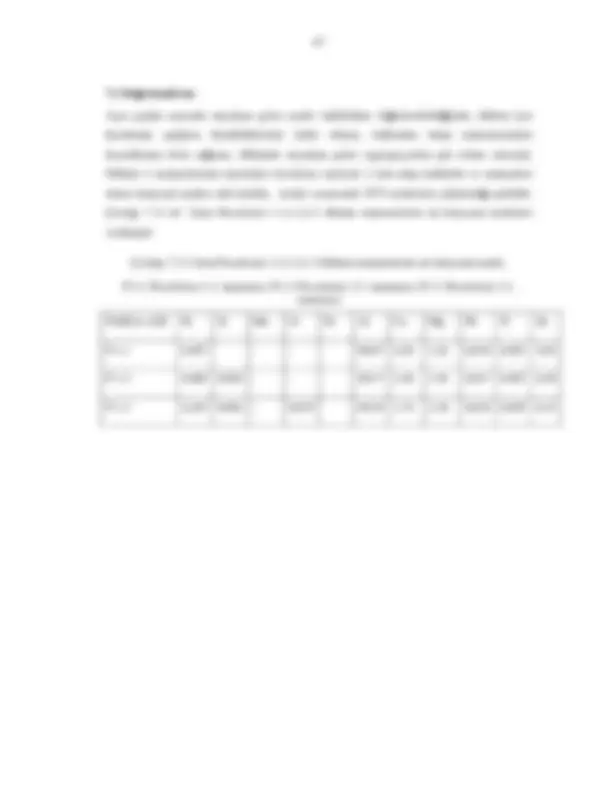
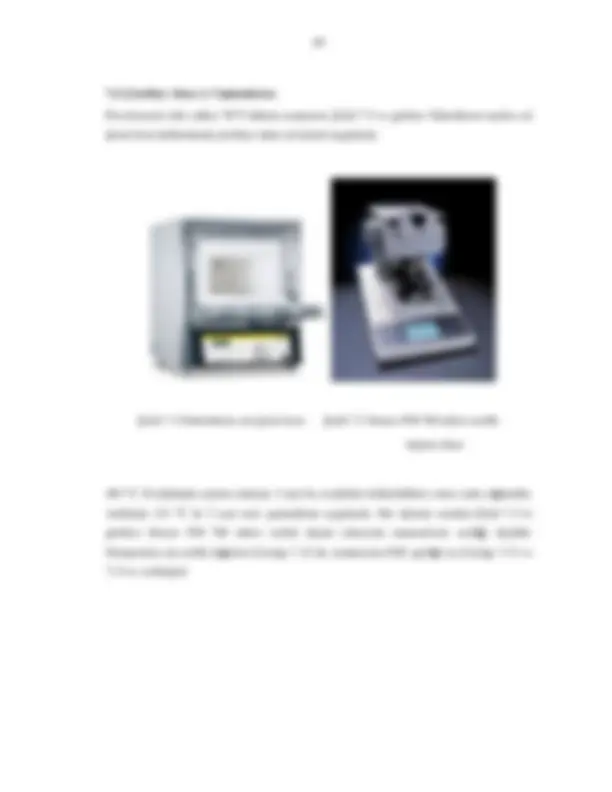
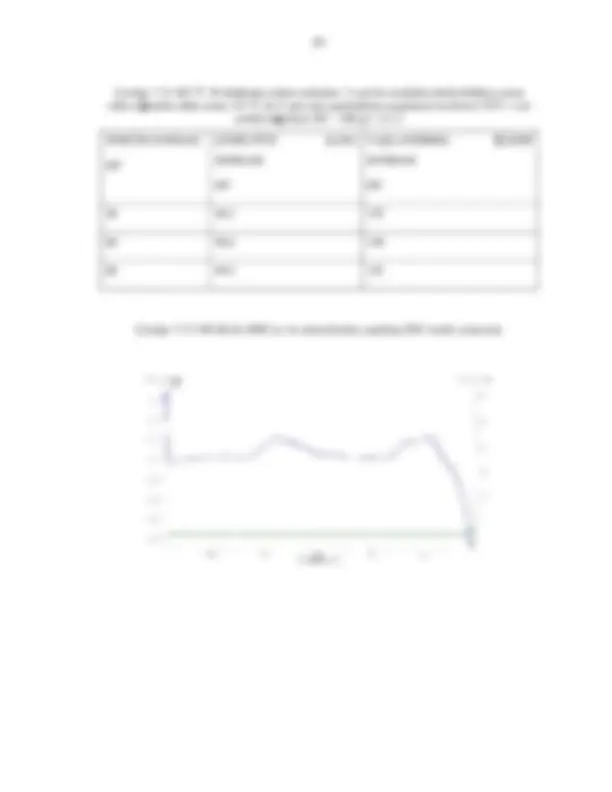
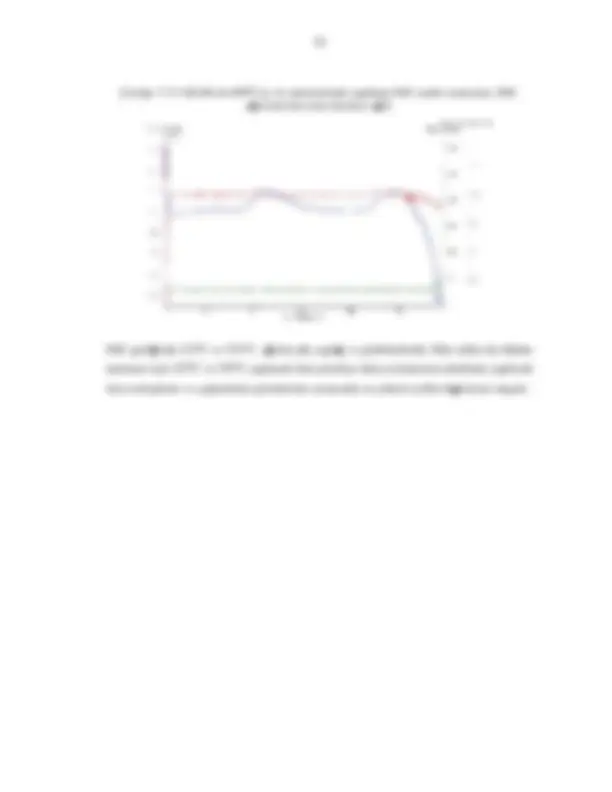
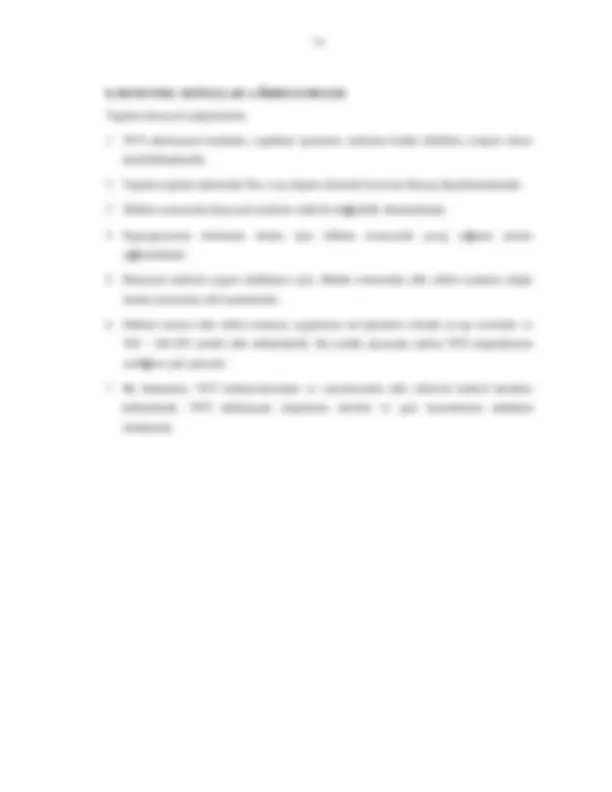
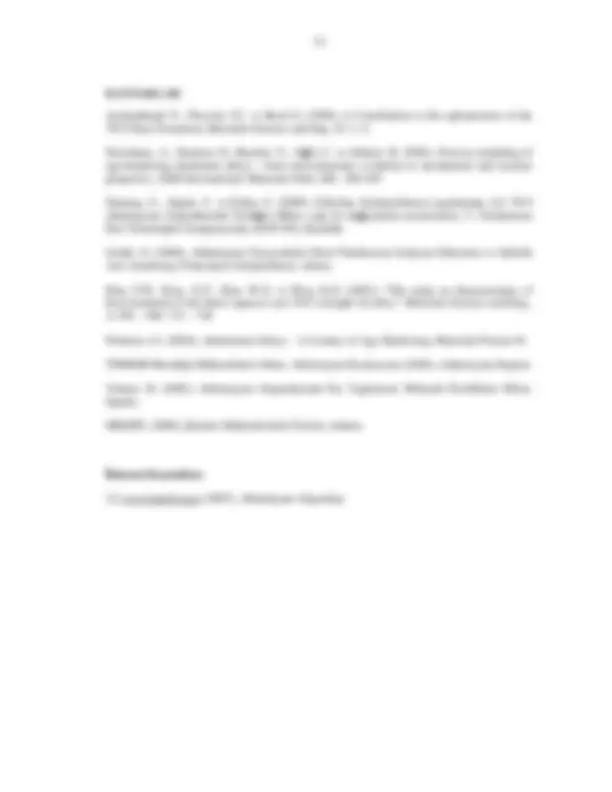
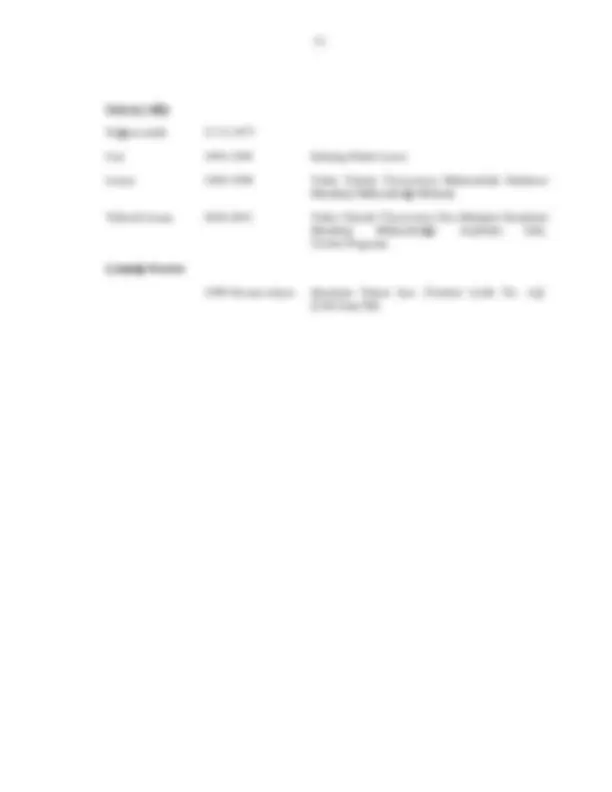
Study with the several resources on Docsity
Earn points by helping other students or get them with a premium plan
Prepare for your exams
Study with the several resources on Docsity
Earn points to download
Earn points by helping other students or get them with a premium plan
Community
Ask the community for help and clear up your study doubts
Discover the best universities in your country according to Docsity users
Free resources
Download our free guides on studying techniques, anxiety management strategies, and thesis advice from Docsity tutors
alüminyum ve kullanımı şişirme kalıpları güzel bir çalışma
Typology: Lecture notes
1 / 84
This page cannot be seen from the preview
Don't miss anything!
Metalürji Mühendisi Sarp BURGUCU
F.B.E. Metalürji Mühendisliği Anabilim Dalı Programında Hazırlanan
Tez Danışmanı: Prof. Dr. Müzeyyen MARŞOĞLU (YTÜ)
ii
Sayfa
SĐMGE LĐSTESĐ........................................................................................................................... v
KISALTMA LĐSTESĐ……………………………………………………………..................... vi
ŞEKĐL LĐSTESĐ………………………………………………………………………............... vii
ÇĐZELGE LĐSTESĐ………………………………………………………………..................... viii
ÖNSÖZ………………………………………………………………………………………..... x
ÖZET……………………………………………………………………………………............. xi
ABSTRACT…………………………………………………………………………….............. xii
2 ALÜMĐNYUM ve GENEL ÖZELLĐKLERĐ………………………………................ 4
3.1 Birincil Alüminyum Üretimi…………………………………………………............. 7 3.1.1 Boksit…………………………………………………………………………............ 7 3.1.2 Alümina…………………………………………………............................................. 10 3.1.3 Alüminyum…………………………………………………....................................... 11 3.2 Đkincil Alüminyum…………………………………………………............................ 14 3.3 Alüminyum Tüketimi…………………………………………………........................ 17 3.4 Dünyadaki Alüminyum Üreticileri…………………………………………………... 18 3.4.1 Alcoa…………………………………………………................................................. 18 3.4.2 Alcan…………………………………………………................................................. 19 3.4.3 Hydro…………………………………………………................................................ 20 3.4.4 Pechiney…………………………………………………............................................ 21 3.4.5 Rusal………………………………………………….................................................. 22 3.4.6 Sual………………………………………………….................................................... 22 3.4.7 Önemli Lokal Orta Ölçekli Firmalar …………............................................................ 23 3.5 Ülkemizde Alüminyum………………………………………………………............. 24
4 ALÜMĐNYUM VE ALAŞIMLARI……………………………………………..…... 28
4.1 Đşlenik Alüminyum Alaşımları ve Simgelenme Dizisi…………………………..…... 28 4.2 Alüminyum Döküm ve Döküm Alaşımları………………………………………… 32 4.3 Alaşım Elementleri ve Etkisi…………………………………………………............ 33 4.3.1 Bakırın Alüminyum Üzerine Etkisi………………………………………..………… 34 4.3.2 Silisyumun Alüminyum Üzerine Etkisi……………………………..………………. 34 4.3.3 Magnezyumun Alüminyum Üzerine Etkisi ……………………………………..….. 35 4.3.4 Manganın Alüminyum Üzerine Etkisi……………………………………………….. 35 4.3.5 Çinkonun Alüminyum Üzerine Etkisi………………………………………………... 35
v
Å Angstron, milimetrenin on binde biri (1/10.000 mm) ºC Derece santigrad μ Mikron, milimetrenin binde biri (1/1000 mm) Al Alüminyum Cu Bakır Fe Demir Zn Çinko Mg Magnezyum Si Silisyum Cr Krom Ti Titanyum Co Kobalt Be Berilyum Tö Ötektik Sıcaklığı T Sıcaklık Mpa Megapascal
vi
PET Polietilen Tereftalat PBT Polibutilen Tereftalat PP Poli Propilen PVC Polivinilklorür PLC Programmable Logic Controller (Programlanabilir Mantıksal Denetleyici) ASA Amerikan Standartlar Birliği ESR Electro Slag Remelting (Cüruf Altı Ergitme)
viii
Sayfa
Çizelge1.1 Yeryüzünde en çok bulunan on elementin kimyasal sembolleri ve bulunma sıklıkları………………………….................................................. 1 Çizelge 2.1 Katı metalin 20 ºC. deki yoğunluğu için örnek verilen değerler.................. 4 Çizelge 2.2 Alüminyumun bazı özelliklerinin diğer metallerle karşılaştırılması............. 6 Çizelge 3.1 En büyük 10 boksit üreticisi……………………………………................. 7 Çizelge 3.2 Türkiye Boksitleri 2002 yılı genel rezervleri………………….................... 8 Çizelge 3.3 Seydişehir-Akseki bölgesi 2002 yılı boksit rezerv dağılımı ….................... 9 Çizelge 3.4 Bazı ülkelerdeki boksit maliyetleri………………………........................... 10 Çizelge 3.5 Bölgelere göre dünya metalurjik alümina üretimi ve planlanan kapasite artışları ( X 1000 TON )…………………………………………………… 11 Çizelge 3.6 Bölgelere göre birincil alüminyum üretimi ve planlanan kapasite artışları (x100 ton)………………………………………………………….............. 13 Çizelge 3.7a Çizelge 3.7b
Avrupa dam alüminyum kutu kullanımı ve geri dönüşümü (2001)……….. Avrupa dam alüminyum kutu kullanımı ve geri dönüşümü (2001)………..
Çizelge 3.8 Başlıca Ekstrüzyon üreticilerimiz……………………………..................... 25 Çizelge 3.9 Başlıca yassı ürün üreticilerimiz………………………………................... 26 Çizelge 3.10 Başlıca alüminyum iletken üreticilerimiz……………………..................... 26 Çizelge 3.11 Başlıca parça döküm üreticilerimiz……………………….......................... 26 Çizelge 4.1 Alüminyum işlem alaşımlarında simgeleme dizisi……………................... 28 Çizelge 4.2 Temel işlemleri gösteren simgeler…………………………….................... 29 Çizelge 4.3 Alüminyum döküm alaşımlarında simgeleme dizisi………….................... 32 Çizelge 4.4 Alaşım elementlerinin katılaşma sıcaklığında ve oda sıcaklığında çözünürlükleri……………………………………...................................... 33 Çizelge 6.1 Çeşitli malzemelerin kıyaslanması……………………………................... 54
Çizelge 7.1 Şişirme kalıbından alınan numune ve Hurda 7075 numunelerine ait Spektral analiz sonuçları ……………………………………......................
Çizelge 7.2a Hurda sertifikaları……………………………………………..................... 60 Çizelge 7.2b Hurda sertifikaları………………………………………………................. 61 Çizelge 7.3 1.1, 1.2, 1.3 şarjlarının miktarları, döküm sıcaklıları, döküm sonucu elde edilen parça ağırlık değerleri………………………………………………. 62 Çizelge 7.4 1.A, 1.B, 1.C döküm parçalarının kimyasal analiz değerleri….................... 63 Çizelge 7.5 %0, %1, %2, %3, %5, %10, %15 Flux eklenerek alınan numunlere ait, şarjlarının miktarları, döküm sıcaklıları, döküm sonucu elde edilen parça ağırlıları…………………………….............................................................
Çizelge 7.6 2.A, 2.B, 2.C 2.D, 2.E, 2.F,2.G döküm numunelerinin kimyasal analiz….. 64 Çizelge 7.7 3.A, 3.B, 3.C numunelerine ait şarjlarının miktarları, döküm sıcaklıları, döküm sonucu elde edilen parça ağırlıları………….................................... 65 Çizelge 7.8 3.A, 3.B, 3.C numunelerine ait kimyasal analiz değerleri…….................... 65 Çizelge 7.9 % 1,5 Mg ilave edilmiş hurdalardan alınan dökümlerden elde edilen 4.1, 4.2, 4.3 numunelerine ait şarjlarının miktarları, döküm sıcaklıları, döküm sonucu elde edilen parça ağırlıkları………………………………………... 66 Çizelge 7.10 4.1, 4.2, 4.3 numunelerine ait kimyasal analiz değerleri….......................... 66 Çizelge 7.11 2mm Frezelenen 1.1,1.2,1.3 döküm numunelerine ait kimyasal analiz F1.1: Frezelenen 1.1. numunesi, F1.2: Frezelenen 1.2. numunesi, F1.3: Frezelenen 1.3. numunesi………………................................................... 67
ix
Çizelge 7.12 465 oC 30 dakikada ısıtılan ardından 2 saat bu sıcaklıkta bekletildikten sonra suda soğutulan daha sonra 121 oC de 2 saat suni yaşlandırma uygulanan fezelenen 7075 ‘e ait sertlik değerleri(HV – 500 gf / 12 s)……. 69 Çizelge 7.13 10C/dk ile 600C'ye Ar atmosferinde yapılmış DSC analiz sonucunu…….. 69 Çizelge 7.14 10C/dk ile 600C'ye Ar atmosferinde yapılmış DSC analiz sonucunu, DSC eğrisinin türevinin (kırmızı eğri)…………………………………………... 70
xi
Günümüzde, havacılık sektöründen otomotiv sektörüne, medikal malzemelerden mutfak eşyalarına, makine parçalarından kalıp yapımına kadar imalat sektörünün hemen hemen her basamağında sahip olduğu özelliklerinden dolayı alüminyum ve alaşımları kullanılmaktadır.
Sektörden sektöre kullanım şekli ve şartları değişmekle beraber, bu çalışmada da üzerinde durulan 7xxx ( Al Zn Mg Cu Alaşımları ) serisi alüminyum alaşımları, plastik enjeksiyon ve şişirme kalıplarının imalatında kullanılmaktadır.
Genel olarak 7075 T6 ( AlZnMgCu1,5 - % Al: 87,1 – 94,1 Cr: 0,18 – 0,28 Cu: 1,2 – 2 Fe: Max. 0,5 Mg: 2,1 – 2,9 Mn: Max. 0,3 Si: Max. 0,4 Ti: Max 0,2 Zn: 5,1 – 6,1 ) alüminyum alaşımları endüstride kalıplık sert alüminyum olarak bilinmektedir. Yerli üretim yapılmakla beraber Eti Alüminyum A.Ş.’nin üretim programında da bulunan 7075 T6, en büyük lama ölçüsü olarak 20 mm x 120 mm ölçülerinde üretilebilmektedir. Şişirme ve enjeksiyon kalıplarında kullanılan 7075 T6 malzemesinin ölçüleri bakımından kıyaslandığında yerli üretim olan malzeme ebatsal olarak küçük gelmektedir. Boyutsal nedenlerden dolayı 7075 T alüminyum alaşımlarının daha büyük ebatlarda çeşitli üreticilerden ithal edilmektedir.
Diğer yandan, 7xxx serisi hurdalar, diğer alüminyum hurdaları ile beraber toplanılmakta ve geri kazanımı yapılmaktadır. Fakat kendi serisine dönüştürülmemekte ve daha alt serilerdeki alüminyum alaşımları elde edilmektedir. Kıymetli olan bir hurda ne yazık ki hak ettiği şekilde geri kazanılamamaktadır.
Bu araştırmada, 7075 alüminyum alaşımı kullanılarak üretilmiş ve ömrünü tamamlamış şişirme kalıpları ve endüstride kullanılmak üzere plaka veya blok şeklinde satılmakta olan malzemelerin kesim hurdaları, indüksiyon ocağı kullanılarak ergitilmiş, metal bir kalıba dökülerek, çıkan döküm parçaları gerekli ısıl işlem uygulamaları yapılarak tekrar 7075 alüminyum alaşımları ( kalıplık sert alüminyum ) elde edilmiştir.
Anahtar Kelimeler : 7xxx serisi alüminyum alaşımları, 7075 T6, geri kazanım
xii
Today’s industrial production including aviation, the automotive sector, medical pharmaceuticals, kitchen ware, machinery parts till tooling works makes use of aluminium and it’s alloys due to their metallurgical properties.
The application of aluminium and it’s alloys changes according to purpose and conditions of use; in this present investigation the materials in question are the aluminium alloys according to 7xxx (Al Zn Mg Cu alloys) being also used for plastic injection and blow molding tools.
In general the grade 7075 T6 ( AlZnMgCu1,5 - % Al: 87,1 – 94,1 Cr: 0,18 – 0,28 Cu: 1,2 – 2 Fe: Max. 0,5 Mg: 2,1 – 2,9 Mn: Max. 0,3 Si: Max. 0,4 Ti: Max 0,2 Zn: 5,1 – 6,1 ) is known as hardened tooling aluminium for industrial applications. The local production of ETĐ ALÜMĐNYUM A.Ş. does cover the grade 7075 T6, however, the maximum producable flat dimension runs to 20 x120 mm only. Therefore the dimensional range of local production is too narrow for blow molding and plastic injection applications; thus 7075 T6 aluminium alloys in larger dimension are presently made available from various producers outside Turkey only on import basis.
On the other point of view 7xxx grades of scrap are collected with other scrap of aluminium alloys in one turn and are recycled all together as well. As the regain of these alloys is not done according to isolated grades the final recycled ingots result in lower grades. High value aluminium scrap is regrettably not recovered as it should or could be.
The 7075 aluminium alloys this investigation is dealing with originate from discharged blow molding tools and rest piece cuttings of blocks and plates; the material was induction furnace remelted into small ingots and hardened according to 7075 aluminium alloy parameters ( hardening tooling aluminium ).
Keywords : 7xxx series of aluminium alloys, 7075 T6, recycling
Bir alüminyum minerali olan alum Yunanlılar ve Romalılar tarafından biliniyor ve harç
olarak kullanılıyordu. 1746 yılında J.H.Pott alumdan alüminayı (Al 2 O 3 ) ayırdı. O zamanlar
içerisinde A.L. Laosier’inde olduğu birkaç bilim adamı alüminanın bilinmeyen bir metalin
oksidi olduğuna inanıyorlardı. Alüminyumun oksijene olan ilgisi o kadar fazlaydı ki, ne
karbon ne de bilinen indirgeyiciler onun oksidini redüklemede etkili olamıyordu.
1807 yılında H. Davy, alüminyumu oksit halindeki bileşiğinden ilk ayıran ve kısmi olarak
elde eden kişi oldu. Elektrotermik ve elektrokimyasal yöntemle küçük miktarda Al-Fe
alaşımını ayırmayı başararak, bunu alüminyum olarak adlandırdı.
H.C.Oersted, 1825’de bir çeşit civalı bileşik olan potasyum amalgamının alüminyum klorüre
etkisi sonucu açığa çıkan üründen civayı ayırarak alüminyumu elde etti. Fakat bu yeni metalin
özelliklerini belirleyemedi. Sadece rengini ve çinkonun parlaklığına sahip olduğunu tespit etti.
Đki yıl sonra F.Wöhler, metalik potasyumla alüminyum klorürü ısıtıp karıştırarak küçük
miktarda alüminyumu gri toz şeklinde üretti.
Ancak elde edilen bu küçük miktardaki metalik alüminyumun özellikleri belirlenemedi.
Wöhler, 1845 yılında alüminyumun bilinmeyenlerine yeniden döndü. Bu kez, buhar halindeki
AlCl 3 ’ü ergimiş potasyum üzerinden geçirerek her biri 10-15 mg olan alüminyum
küreciklerini elde etti. Üretilen alüminyumun ergime noktası, yoğunluğu, dövülebilme ve
çekme özellikleri belirlendi. Wöhler’in bu başarılı çalışmalarıyla alüminyumun elde
edilmesinin ve özelliklerinin belirlenmesinin birinci dönemi kapandı.
Đkinci dönem teknik alüminyum üretim dönemidir. 1854 yılında H.St.Claire Deville adlı
Fransız okul öğretmeni tarafından başlatılmıştır. Deville, alüminyumu sodyum
tetrakloralüminattan ısıl indirgeme yoluyla üretti. Böylece sodyum çok pahalı potasyum
yerine indirgen olarak ortaya çıktı. Bu proses alüminyum üretimi için çok pahalı idi. Deville
3.Napolyon Hükümeti’nden para yardımı aldı. Alüminyum metali örnekleri Paris’te
sergilendi. Alüminyumun hafifliği onun üzerindeki ilgiyi arttırdı. Đlk üretilen alüminyumda
saflık % 92 civarında idi ve ana safsızlıklar demir ve silisyumdu.
1854 yılından sonra alüminyum üretim teknolojisi sürekli iyileştirilerek kalite ve üretimi
arttırma, üretim maliyetini düşürme çalışmaları yapıldı. Çünkü o tarihlerde son derece yüksek
üretim maliyeti nedeniyle, altın ve gümüş gibi kıymetli metaller arasında sınıflandırılıyordu.
Fransa’da ilk kurulan tesiste günde 2 kg alüminyum üretilirken, 1857’de bu miktar
50kg/gün'e, saflığı da % 96-97’ye erişti. Tüm kimyasal yöntemlere rağmen, ikinci dönemde
alüminyum üretim istenilen düzeylere erişemedi.
Üçüncü dönem, bugünkü endüstriyel alüminyum üretiminin temeli olan proses için 23 Nisan
1986’da P.L.T. Heroult ve aynı yılın 9 Temmuz’unda Amerika’da C.M. Hall tarafından,
birbirlerinden habersiz olarak, ergimiş kriyolit içerisinde çözünen alüminadan elektroliz
yoluyla alüminyum üretimi için patent istemeleri ile başladı. Bu nedenle Hall-Heroult olarak
adlandırılan bu prosesin endüstriye uygulanmasıyla alüminyum üretimi ani olarak artış
göstermeye başladı.
Bu yöntem günümüzde birincil alüminyum üretiminde halen kullanılmaktadır. Bu sebeple
1886 yılı alüminyum endüstrisinin başlangıç yılı olarak kabul edilir. 1886 yılında Werner Von
Siemens’in dinamoyu keşfi ve 1892 yılında K.J. Bayer’in, boksitten alümina eldesini sağlayan
Bayer prosesini bulması ile alüminyumun endüstriyel çapta üretimi kolaylaşmış ve kullanımı
yaygınlaşmıştır. Bu sayede alüminyum, demir çelikten sonra dünyada en çok kullanılan ikinci
metal olmuştur. 1980 yılından sonra alüminyum üretiminde büyük bir artış olmamıştır.
(Gedik, 2009 )
kullanılmasına yol açar. Ayrıca ısı iletkenliği artan safiyet derecesi ile büyür. Bu %99,489 alüminyumlu bir metal için 200 ºC de 0,5 cal/cm s°C ve % 99,
alüminyumlu bir metal için 0,531 cal/cm s ºC dir.
direncidir. Kimya ve besin sanayinden inşaat sanayine ve ev eşyalarına dek çok geniş
bir alanda kullanılmasının başlıca nedeni alüminyumun bu özelliğidir. Korozyona karşı mukavim oluşunun nedeni, alüminyum havada ince fakat çok sıkı bir alüminyum oksit kabuğu ile kaplanır. Elektron mikroskobu ile yapılan araştırmalar bu örtünün sık
ve gözeneksiz olduğunu göstermektedir. Bu, metali oksitlenmenin devam etmesine karşı korur ve ona yüksek bir mukavemet sağlar. Metalik parlak alüminyumun
yüzeyindeki koruyucu alüminyum oksit takriben 0,2 μ kalınlığındadır.
çeliğin esneklik katsayısının 1/3. ne eşit olduğundan, çelik yerine alüminyum
kullanılmaya karar verildiğinde, esnemenin çeliğe göre üç kat daha fazla olacağı göz önüne alınmalıdır.
kadar çıkabilir. Çekme dayanımı ise 9 MPa değerinden, bazı yaşlanabilir alaşımlarda
65 MPa değerinin üstüne çıkabilir. Alüminyumun bazı özellikleri diğer metallerle karşılaştırmalı olarak Çizelge 2.2 de verilmiştir. (Deschams, vd., 2001 )
Çizelge 2.2 Alüminyumun bazı özelliklerinin diğer metallerle karşılaştırılması (Deschams, vd., 2001 )
ÖZELLĐK Al Cu Fe Zn Mg
Özgül Ağırlık (g/cm^3 ) 2,70 8,94 7,87 4,1 1,
Elektrik Direnci (Ohm.mm^2 /2).10^2 2,66 1,68 9,8 6,00 4,
Isı Đletkenliği (cal/cm^2 /cmoC) 0,52 0,92 0,19 0,27 0,
Isıl Genleşme Kat. (mm/mmoC). 10- 6^24 16,7 11,9 33 25,
Ergime Sıcaklığı oC 660 1083 1535 420 651
Yanma Isısı (kcal/kg) 6970 - 1600 1270 6000
Uzama (%) 43 50 48 - -
Sertlik (BHN) 19 25 70 - -
Yukarıda belirtilen özelliklerinden olayı sanayi ve üretimde alüminyum birçok uygulama ve
kullanım alanı bulmaktadır.
Ülkemiz ise %95’i Toros kuşağı içinde yer alan 422 milyon tonluk rezerv potansiyeline
(dünya boksit potansiyelinin %1’i) sahip olmakla birlikte bunun 57.3 milyon tonu görünür
rezerv durumundadır. Đşletilebilir boksit potansiyeli ise %0,2 kadardır. Dünya boksit
üretimindeki ülke payımız ise %0,5 düzeyindedir. Boksit yataklarımızın %88 i diasporitik,
demirli diasporitik ve lateritik tip boksitlerden oluşmakta ve bunların tümü Toros kuşağı
içinde yer almaktadır. Türkiye’nin en zengin metalurjik boksit yatakları Seydişehir-Akseki
bölgesi rezervleri olup, işletilebilir rezerv yaklaşık 36 milyon tondur. (Çizelge 3.2 ve Çizelge
3.3)
Çizelge 3.2 Türkiye Boksitleri 2002 yılı genel rezervleri (TMMOB, 2004)
BÖLGELER REZERV ( X1000 TON ) TĐPĐ
Seydişehir-Akseki 35,251 1,253 36,504 31,000 Böhmitik
Zonguldak-Kökaksu 5,900 3,400 9,300 5,000 Böhmitik
Yalvaç-
Şarkikaraağaç
Diasporitik
Payas-Islahiye - 215,500 215,500 - Demirli-
Diasporitik
Tufanbeyli- Saimbeyli
5,500 6,000 11,500 9,800 Diasporitik
Muğla-Milas- Yatağan
9,400 11,200 20,600 17,500 Diasporitik
Bolkardağı - 3,900 3900 - Diasporitik
Alanya 1,300 7,700 900 - Diasporitik
Toplam 57,351 364,553 421,904 63,
Çizelge 3.3 Seydişehir-Akseki bölgesi 2002 yılı boksit rezerv dağılımı(TMMOB, 2004)
YATAK ADI REZERVLER
( X 1000 TON )
TOP. Al 2 O 3 SiO 2 Fe 2 O 3 Diğe r
Mortaş 4,222 - 4,222 3,300 56,98 8,89 17,5 3,
Doğankuzu (G) 6,835 - 6,835 6,000 57,81 7,13 17,7 3,
Doğankuzu (K) 4,088 - 4,088 3,700 58,26 6,30 17,8 3,
Doğankuzu
(GD)
Ağaçyolu 300 - 300 200 57,20 5,40 17,8 3,
Değirmenlik 11,
0
Çatmakaya 833 - 833 700 58,55 5,21 18,1 3,
Morçukur 6,336 - 6,336 5,500 52,91 11,
4
Erikligediği 280 - 280 200 55,15 5,15 19,0 3,
Yarpuz 218 - 218 200 57,14 5,50 18,5 3,
Gömene 296 20 316 200 52,34 10,
0