
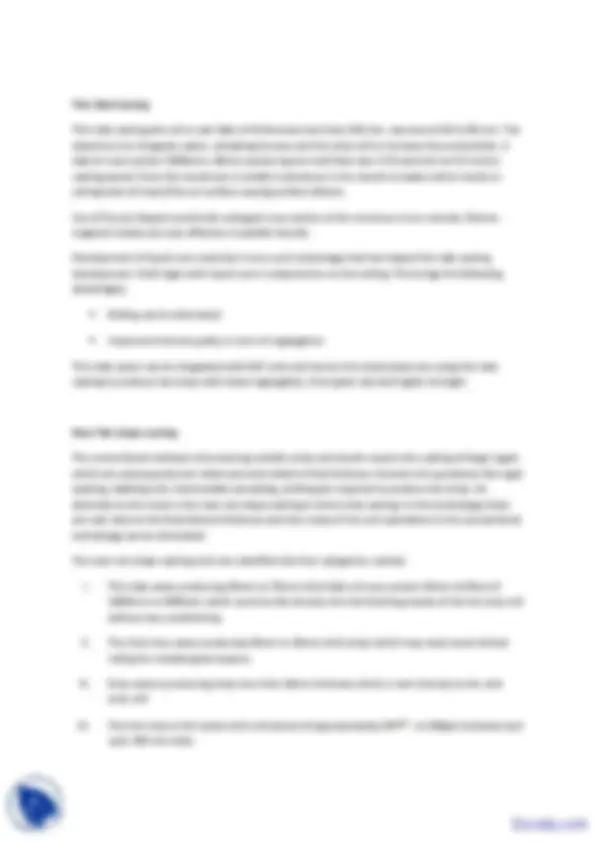
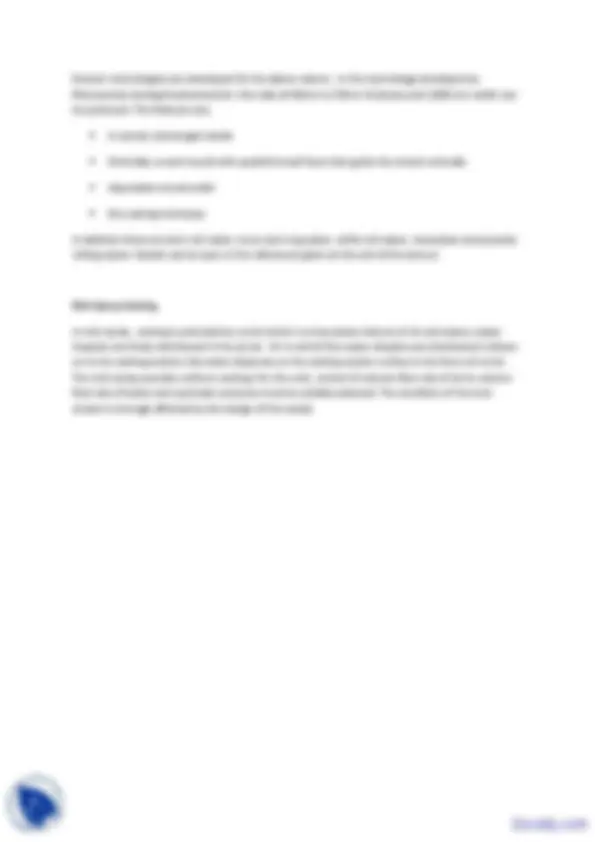
Study with the several resources on Docsity
Earn points by helping other students or get them with a premium plan
Prepare for your exams
Study with the several resources on Docsity
Earn points to download
Earn points by helping other students or get them with a premium plan
Community
Ask the community for help and clear up your study doubts
Discover the best universities in your country according to Docsity users
Free resources
Download our free guides on studying techniques, anxiety management strategies, and thesis advice from Docsity tutors
The major points which I found very informative are:Advances in Continuous Casting of Steel, High Speed Slab Casting, Thin Slab Casting, Strip Casting, Hot Rolling, Direct Charging, Electromagnetic Stirring, Segregation and Porosity, Near Net Shape Casting
Typology: Study notes
1 / 4
This page cannot be seen from the preview
Don't miss anything!
Lecture 34 Advances in Continuous Casting of Steel Contents Introduction High speed slab casting Thin slab casting Key words: Thin slab casting, strip casting, Hot rolling, direct charging Introduction Continuous casting is one of the most significant developments in the technology of steelmaking. A ladle containing 300 tons of molten steel at 1600 can be cast into approximately 60 minutes in a semi-finished product like bloom, billet and slab. It reduces energy consumption, material handling and as a result lead to increase in plant productivity. In addition continuous casting offers the possibility to integrate the hot strip or blooming mill by direct hot charging. In recent years considerable developments have taken place both in conventional continuous casting to improve the product quality and to develop new technology to produce nearly finished products. Some of the developments are briefly described. Electromagnetic Stirring(EMS) EMS is an electric method of inducing motion in liquid steel without using any mechanical device. In continuous casting EMS can be applied in mold and secondary cooling zone to Decrease segregation and porosity Improve steel cleanliness by forcing inclusions to float on the surface where they can be absorbed by a slag Improve the steel quality in terms of reducing the defects Stirring induced by EMS modifies the flow pattern of molten steel of the solidifying strand. Improved stirring reduces segregation. Because of the imposed stirring, the superheat of the melt can be quickly dissipated which results in modification of structure of the solidifying strand from columnar to equiaxed and then to globular structure. EMS allows to increase the casting speed which increases productivity of the caster. An inductive electromagnetic stirrer is the stator of an asynchronomous motor, the rotor of which is the liquid core of the solidifying strand. This stator produces either a rotating or travelling magnetic field B, which induces eddy current J, perpendicular to B and its velocity vector. B and J combine together to create an electromagnetic force which causes stirring in the bath. The mains frequency is usually used for stirring billets or small blooms beneath the mold. In secondary cooling zone low
frequency (1 to 20Hz0 is required to electromagnetically stir the liquid steel of the solidifying strand because the thick solid steel shell shields the magnetic flux. High speed Casting High speed casting of slab increases the productivity. Average casting speed in the conventional slab casters is on average 2 m/min. Now if want to increase the casting speed we have to consider design and operational features of tundish, mold and secondary cooling zone. This is illustrated by the following example; Consider a conventional 2 strand caster casting slab of cross section 280mm x 1950mm at 2 m/min casting speed. Molten steel is fed from a tundish of 70 tons capacity by submerged entry nozzles in both the molds of the continuous casting machine. Volume of slab /minute = 1.092 m^3 /minute. Assuming density of liquid steel as 7 tons/m^3 steel flow rate is 7.6 tons/minute/strand. Now if we increase casting speed to 3 m/min., the required steel flow rate would be 11. ton/min/strand, and which will increase to 15.2 tons/min/strand for 4 m/min casting speed. Now let us calculate the average residence time of molten steel flowing in the tundish assuming 70 tons tundish will be used even for high speed casting Steel flow rate (tons/min/strand Residence time (minutes) 7.6 4. 11.4 3. 15.2 2. We note that the average residence time of steel melt in the tundish decreases with the increase in the casting speed. Thus, chances of inclusion floatation will be very low at higher casting speeds. Thus, the following modifications may be considered; In one modification tundish capacity needs to be increased, if tundish is to be used to remove inclusions during the process of continuous casting. Thus, a change in tundish design would be required. In other modification we improve the upstream steelmaking facility so that inclusion content in steel are within the tolerance limit. One may consider other alternatives depending on the available resources. We have to consider further as to what will happen in the mold? Increase in steel flow rate will increase the steel velocity in the mould since the mold length is not being changed. One requires to consider the cross section of the submerged entry nozzle too. The higher steel flow rate in the mold would require intense cooling in the mold. The steel flow in the mold will be more turbulent. Also the mold powder consumption may increase. We would be requiring mold flux whose melting rate is relatively higher to keep pace with the casting speed. Similarly water spray in the secondary cooling zone has to be modified in view of the increase in the casting speed. Uniform cooling of the strand is the prerequisite for the success of the caster.
Several technologies are developed for the above casters. In the technology developed by Mannesman demag Huettentechnik thin slab of 40mm to 70mm thickness and 1200 mm width can be produced. The features are;