
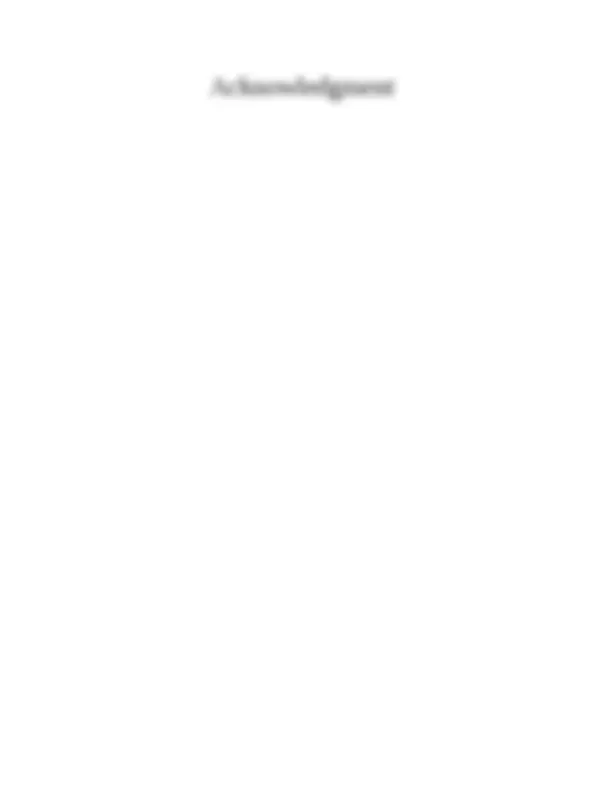
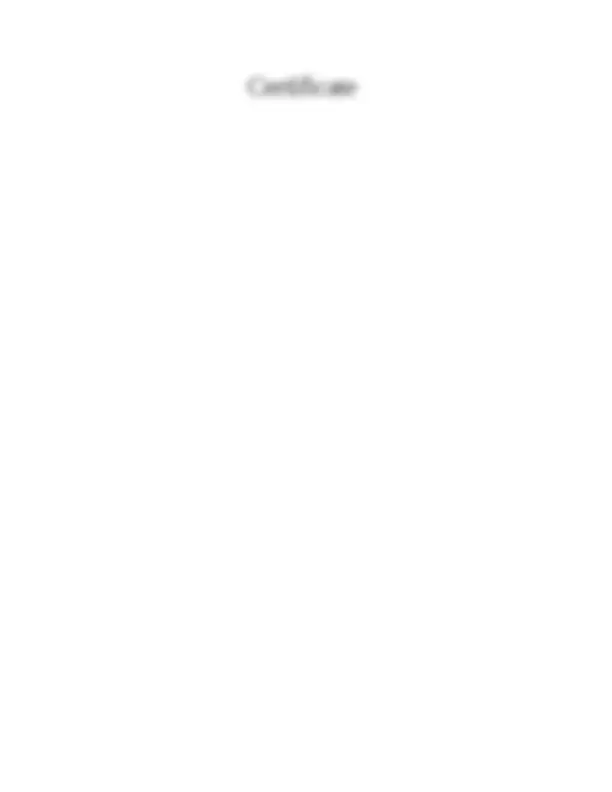
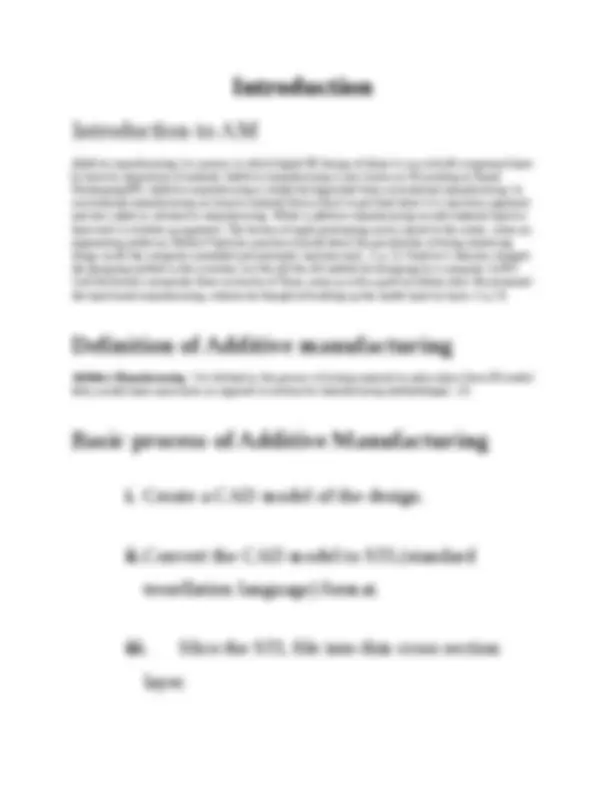
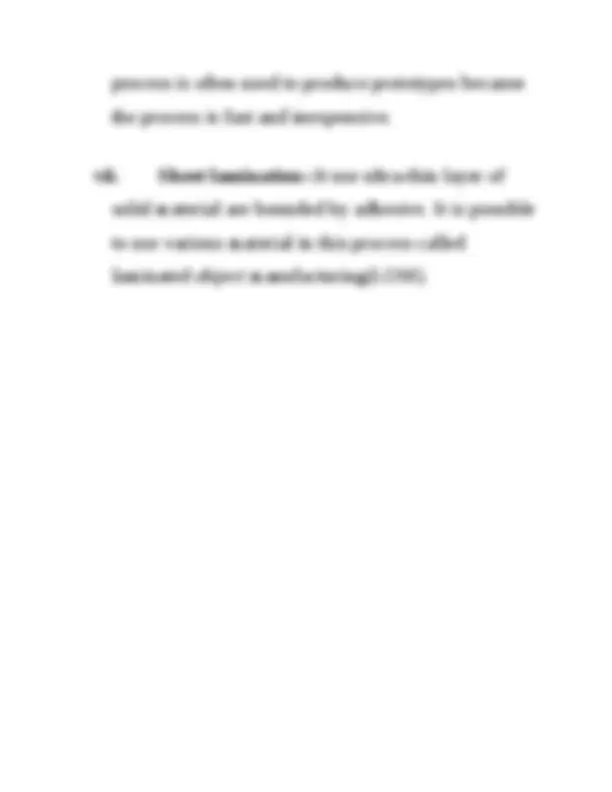
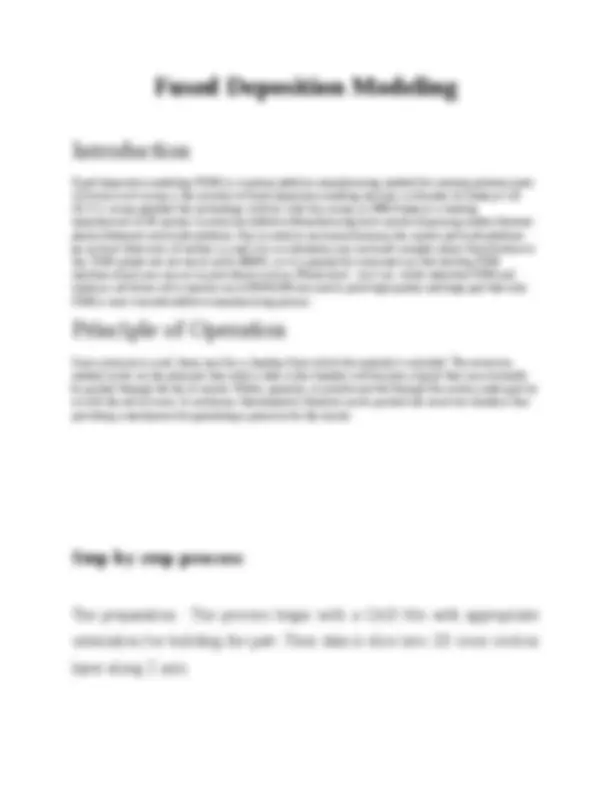
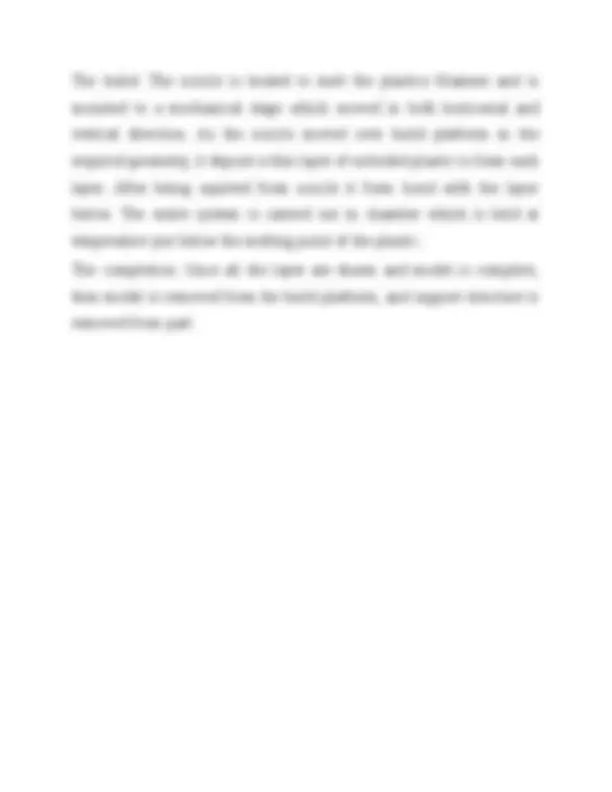
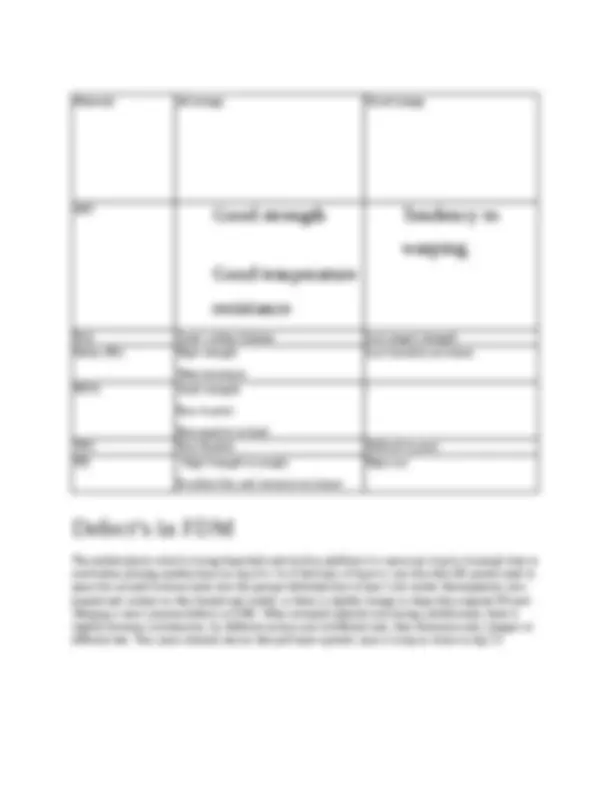
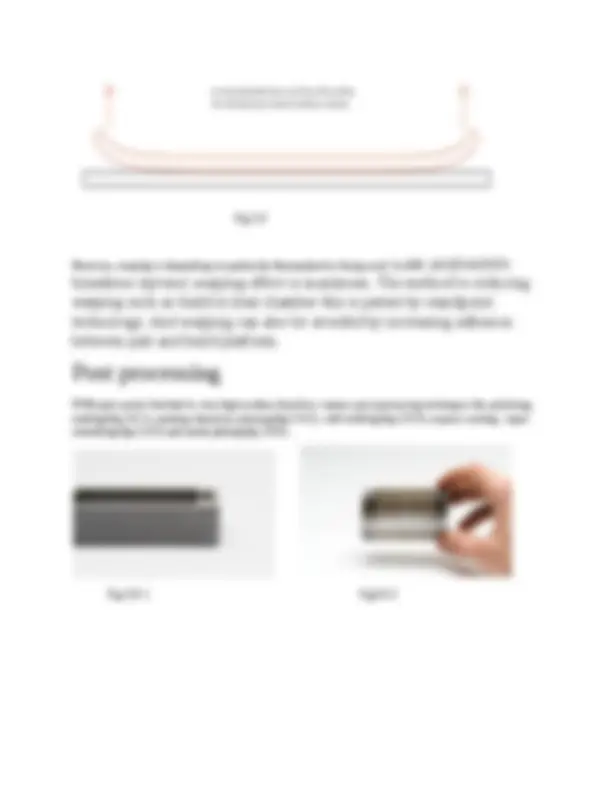
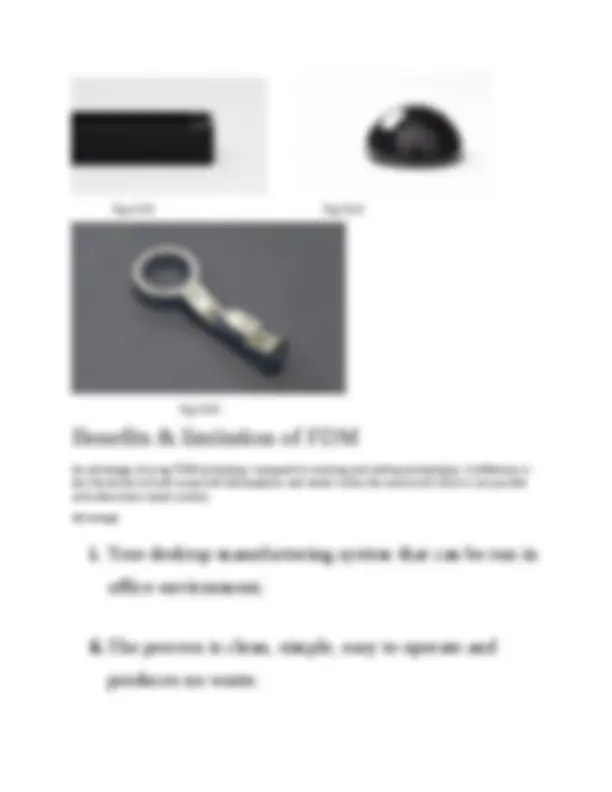
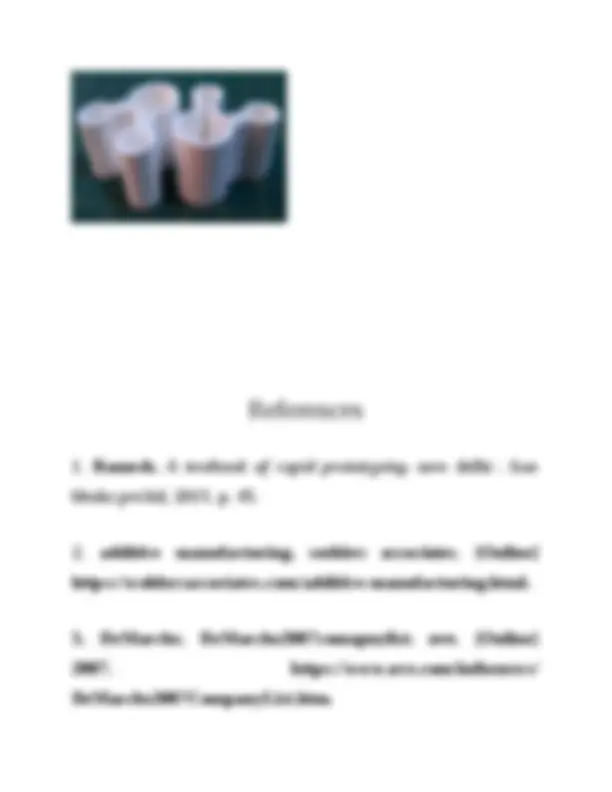
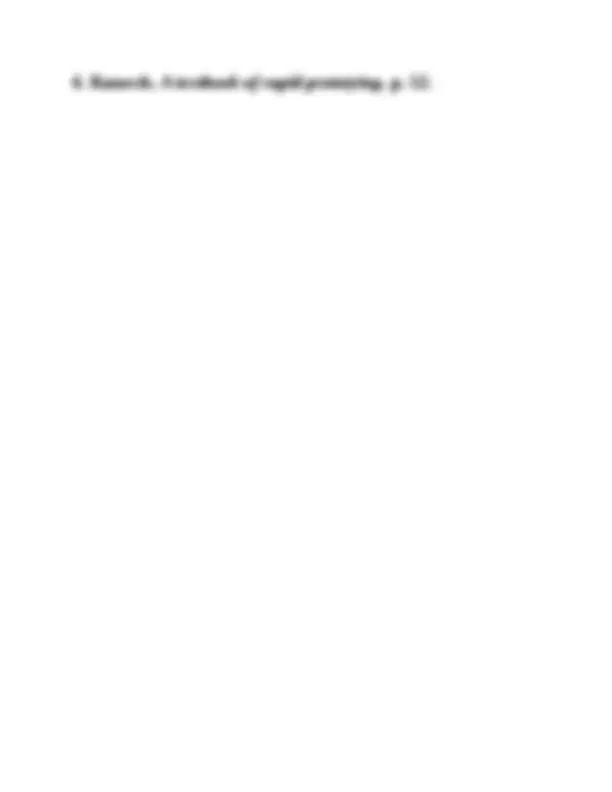
Study with the several resources on Docsity
Earn points by helping other students or get them with a premium plan
Prepare for your exams
Study with the several resources on Docsity
Earn points to download
Earn points by helping other students or get them with a premium plan
Community
Ask the community for help and clear up your study doubts
Discover the best universities in your country according to Docsity users
Free resources
Download our free guides on studying techniques, anxiety management strategies, and thesis advice from Docsity tutors
fused depostion molding selective laser sintering or melting sterolethography
Typology: Study Guides, Projects, Research
1 / 19
This page cannot be seen from the preview
Don't miss anything!
Additive manufacturing it is process in which digital 3D design of object is use to build component layer by layer by deposition of material. Additive manufacturing is also known as 3D printing or Rapid Prototyping(RP). Additive manufacturing is totally distinguished from conventional manufacturing. In conventional manufacturing we remove material from a block to get final object it is top down approach and also called as subtractive manufacturing. While in additive manufacturing we add material layer by layer and it is bottom up approach. The history of rapid prototyping can be traced to the sixties, when an engineering professor, Herbert Voelcker, question himself about the possibilities of doing interesting things worth the computer controlled and automatic machine tools. (1 p. 2). Voelcker’s theories changed the designing method in the seventies, but the old the old method for designing by a computer. In 80’s Carl Deckward a researcher from university of Texas came up with a good revelatory idea. He pioneered the layer based manufacturing, wherein he thought of building up the model layer by layer. (1 p. 3)
Additive Manufacturing : It is defined as the process of joining material to make object from 3D model data, usually layer upon layer, as opposed to subtractive manufacturing methodologies. (2)
Materials Advantage Disadvantage
PLA Good surface finishes Low impact strength Nylon (PA) High strength
Wear resistance
Low humidity resistance
PETG Good strength
Easy to print
Non-reactive to food
TPU Very flexible Difficult to print PEI High Strength to weight
Excellent fire and chemical resistance
High cost
The melted plastic which is being deposited onto built-in platform it is necessary to give it enough time to cool before printing another layer on top of it. So if thickness of layer is very thin then 3D printer need to pause for seconds between layer else the part get deformed due to heat. Like metals thermoplastics also expand and contract as they heated and cooled, so there is slightly change in shape then original 3D part. Warping is most common defects in FDM. When extruded material cool during solidification, there is slightly decrease in dimension. As different section cool at different rate, their dimension also changes at different rate. This cause internal stresses that pull layer upward, cause it wrap as shown in fig 2.
FDM part can be finished to very high surface finish by various post processing technique like polishing, sanding(fig-2.6.1), panting chemical, priming(fig-2.6.2), cold welding(fig-2.6.3), expoxy coating, vapor smoothing(fig-2.6.4) and metal plating(fig-2.6.5).
Fig-2.6. 1 Fig2.6.
Limitation
Fit, Form and Function Testing. Determine function and performance of specific part and help to evaluate your model.
Due to wide range of FDM material available, any application can approach.
Precise, Detailed parts
FDM produce durable models, even they can still produce small intricate parts as show in figure.
High Heat Application
FDM part can withstand high heat tolerances. So FDM part can be used in application which subjected to high heat
4. Ramesh. A textbook of rapid prototying. p. 52.