
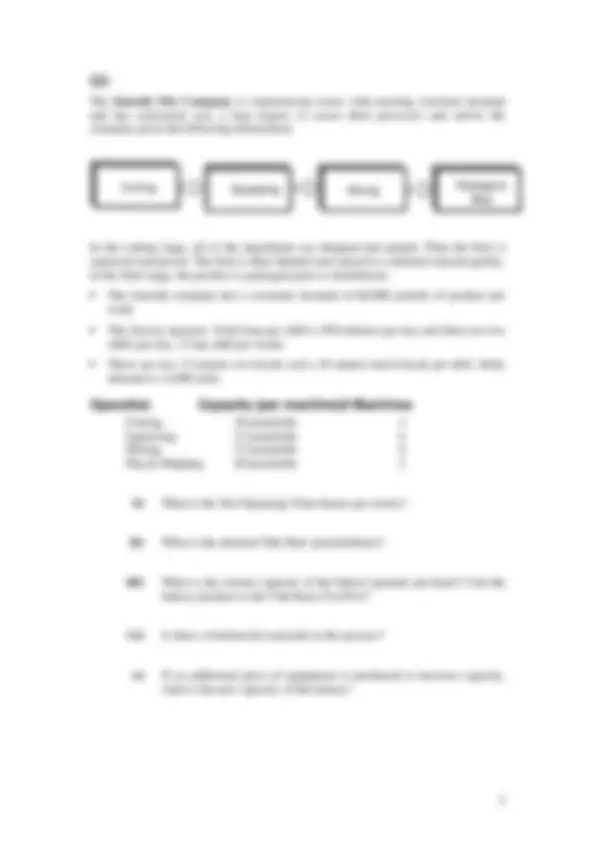
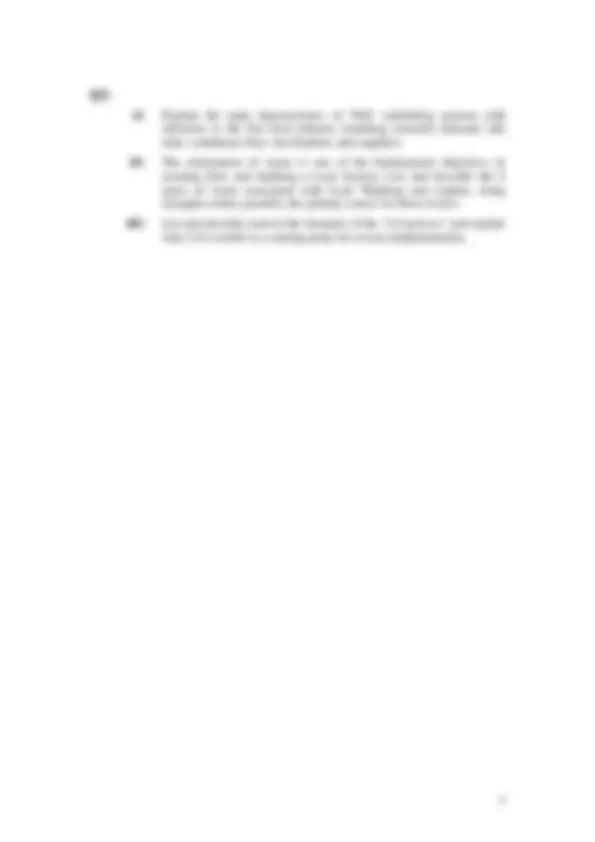
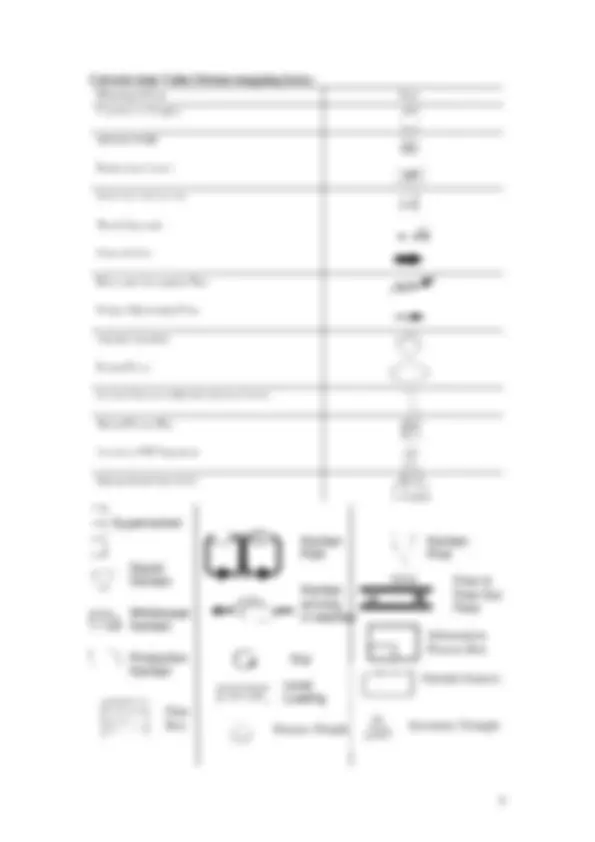
Study with the several resources on Docsity
Earn points by helping other students or get them with a premium plan
Prepare for your exams
Study with the several resources on Docsity
Earn points to download
Earn points by helping other students or get them with a premium plan
Community
Ask the community for help and clear up your study doubts
Discover the best universities in your country according to Docsity users
Free resources
Download our free guides on studying techniques, anxiety management strategies, and thesis advice from Docsity tutors
Main points of this past exam are: 5-S Process, Current State Map, Euro Disney France, Departure Terminal, Luggage Collection, State Value Stream, Suggest Lean Improvements, Smooth Mix Company, Net Operating Time, Demand Takt Rate
Typology: Exams
1 / 5
This page cannot be seen from the preview
Don't miss anything!
Exam Code(s) 4BI1, 1APE1, 1APE2, 1EM Exam(s) 4 th^ Industrial Engineering M.Applied Science (Enterprise Systems) Erasmus
Module Code(s) IE Module(s) Lean Systems
Paper No. 1 Repeat Paper
External Examiner(s) Prof J Antony Internal Examiner(s) *Ms. Mary Dempsey Prof. P McHugh
All questions will be marked equally.
Duration (^) 2 Hours
No. of Pages Cover + 4 pages College/Discipline College of Engineering & Informatics Course Co-ordinator(s) Mary Dempsey
Requirements : None
[Note: A list of all icons required to produce the current state map is provided on page 4]
It was an ordinary Low cost flight, just a trip to Euro Disney France for three days. Breakfast was rushed but we managed to leave home at 6.15am. Returned a few minutes later, forgot the passports, managed to find them and finally left home (again) by 06.30. Arrived at the Airport at 07.00, dropped Aoibhín off with the bags at the departure terminal and went to the long term car park. Eventually found a parking space after ten minutes.
Waited eight minutes for the courtesy bus. Following a six minute journey back to the terminal we were queuing at the bag drop off counter by 07.24. Following a twenty minute queue we arrived at the counter, however it took an additional eight minutes to answer all the security questions about our bags. Went through passport control and waited in the queue for the main security check for ten minutes. Security decided I looked suspicious and proceeded to search my carry on bag for three minutes.
Arrived in the departure terminal at 08.05. Spent one hour and five minutes reading and looking at plastic souvenirs. Flight called to a gate at 09.10, took two minutes to walk to the gate and a further five minutes to queue at the gate. Through the gate walking out on to the airport ground and up the steps of the plane takes four minutes and eventually in seat at 09.21. Wait fourteen minutes for plane to fill up with other passengers. Plane starts to taxi to runway at 09.35. Plane queues to take off for ten minutes. Plane takes off at 09.45. Smooth flight to Paris 55 minutes. Circle for ten minutes then touch down at Paris at 10.50. Taxi to terminal and wait fifteen minutes to disembark.
Disembark at 11.05 and walk to luggage collection, (calling to lavatory on way), arrive at luggage collection at 11.15. Wait for luggage eight minutes. Through customs and arrived at the taxi rank at 11.26. Wait for taxi four minutes. In the taxi by 11.30 and 30 minutes later arrived at the hotel at 12.00.
ii) Produce a current state Value Stream map from this data, depicting both the material/human and information flows. Include a timeline at the bottom of your map, showing the total lead-time from departure from home to arrival at hotel destination.
iii) Identify the value added time and the throughput time for this logistical process between the hours of 6.15 and 12.00 i.e. 5 hours 45 minutes.
iiii) Suggest Lean improvements for this process. Identify and describe some of the improvement opportunities that can be applied to the current state processes. Describe your ambitions for a future value stream map and a future future value stream map.
ivi) Eliminating the queuing quickens the time it takes to flow through a system. What are the disadvantages of removing those parts?
ii) Explain the main characteristics of ‘Pull’ scheduling systems with reference to the fast food industry including customer demand, takt time, continuous flow, fast Kanban, and suppliers. iii) The elimination of waste is one of the fundamental objectives in creating flow and building a Lean System. List and describe the 8 types of waste associated with Lean Thinking and explain, using examples where possible, the primary causes for these wastes. iiii) List and describe each of the elements of the ‘5-S process’ and explain why 5-S is useful as a starting point for a Lean implementation.
Current state Value Stream mapping icons:
FIFO
Supermarket Kanban
Signal Kanban
Withdrawal Kanban
Production Kanban Level Loading
Pull
Kanban arriving in batches
Path
Kanban Post
First-In First-Out Flow
Outside Sources
Person / People^ Inventory Triangle
Information Process Box
Data Box